Ideal Grid Support Voltage to extend the life of the Flooded Batteries
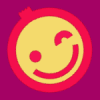
ChuckKautz
Registered Users Posts: 10 ✭✭
I have a grid tied system that allows net metering. I have an 8100 W array with 2 Schneider Electric XW6048 inverters, 4 charge controllers,and battery for backup. The battery is flooded 875 Ah and 48V. I want to maximize the life of the battery. I understand that each month I should exercise the battery down to 48V, top off the distilled water and then equalize the batteries. Three questions:
1. How do I exercise the battery down to 48V? Set Grid support to 48V for a day a month?
2. What grid support Voltage should I set the inverter to so that the batteries will have as long a life as possible?
3. Anything else that I need to do to extend the battery life?
TIA
Comments
-
Welcome to the forum ChuckKautz,
You have a remote battery temperature sensor on the bank and configured for use? "Hot" Lead Acid batteries need reduced charging voltage as they get hot (for every 1C over 25C, the voltage is reduced by -0.005 volts per cell per C, or 0.12 volts per C for a 24 cell/48 volt battery bank).
What brand/model of batteries do you have? Always a good place to start it with the Battery Mfg. specifications.
It sounds like you are floating the batteries mostly, with "rare" power outages (during hurricanes, ice storms, etc.?). So, make sure you bank is at float charging voltage unless you have recently (a few hours ago) have discharged your bank.
Use a good digital voltmeter to check both the bank voltage (at proper float and absorb voltages) is correct. And check/log the voltage across each battery in your string(s). Investigate any battery that is higher or lower than any of its neighbors. You are looking for differences. Measure both resting/float voltage... And when you are cycling the bank, double check when significant charging/discharging current is flowing. A weak battery may read high voltage (when charging an open/weak cell can raise apparent battery voltage) or read load (a shorted cell can make a 6 volt battery look like a 4 volt battery).
Use a hydrometer to check/log the temperature corrected SG for each cell once a month (you could use the voltage per battery to find any 'outliers' and then use that to initiate SG readings. SG (specific gravity readings) are the gold standard for checking the health/state of charge for FLA batteries.
When charging or EQ (equalize) charging, check electrolyte levels and make sure all plates are covered--Do not "fill" the cells until the batteries are fully charged and bubbling... If you fill when cold, then charging/EQ charging can force your electrolyte levels out the caps (big mess, and issues of lost electrolyte/battery acid).
Monitor your water levels... If you must refill every month or less--You should crank down on the charging voltage. If you are refilling every 6 months or longer, you may need to raise charging voltage a bit.
Most FLA/Lead Acid batteries die from under charging. But excessive charging (excessive EQ, higher voltage, etc.) can be hard on lead acid batteries too (EQ charging erodes plates, Oxygen is formed and can corrode plate grids, high temperatures cause faster aging of batteries).
The typical recommendation is to EQ the batteries once a month. 5% to 2.5% rate of charge for EQ current (875AH*0.05=43.75amps suggested maximum), watch bank temperature (stop EQ if bank is overheating). Tall cased batteries need EQ more than short cased batteries (to mix the electrolyte and prevent stratification). Also, EQ is suggested if the SG between high and low cells is greater than 0.015-0.030+ SG units). Check sg every hour of all cells--When SG does not rise since last reading, then cells are fully charged--Log temperature corrected SG for all cells--And this is the 'new' 100% SoC for each cell.
Overall, keep your bank cool... The standard engineering rule of thumb is for every 10C/18F over room temperature (25C/75F), the batteries will age twice as fast (93F battery will last 1/2 as long vs 75F battery--aging wise). Guessing you are somewhere around Lakeside TX (warm/hot climate?).
Batteries are mostly killed by undercharging. Other things like using other than distilled/deionized water, exposing plates, overheating batteries, over discharging, or letting batteries sit at low charge (roughly under 75% State of charge) for day/weeks/months will cause to sulfate to harden into black crystals (sulfating is non-reversible, and is a permanent loss of battery capacity).
It is suggested that you take your battery bank down to ~75% state of charge once per month to exercise the bank (deep cycle batteries like to be exercised) and bring back >90% SoC... Do not try for 100% SoC every day--That is hard on lead acid batteries (excessive gassing/heat). The engineer in me says to cut the AC power to your XW system and let it run (while you monitor battery voltages)--That is the only way to guarantee the system actually is running/working correctly in a power out situation. Of course, you could lose power if there is a failure--Make sure computers are backed up/on local UPS/or shutdown during transfer (if you have critical data--Laptops should be find with their own internal batteries).
Basic tools would include:
https://www.solar-electric.com/search/?q=hydrometer
glass thermometer / IR thermometer
A DC Current Clamp DMM (digital multimeter) (really and AC+DC clamp meter) is really nice to debug and monitor parallel battery strings--Are all string sharing charging/discharging current well--As an example):
https://www.amazon.com/UNI-T-Digital-Multimeter-Current-Capacitance/dp/B078PDNS27 ("good enough" meter--check prices/availability--They are all over the place right now)
https://www.amazon.com/gp/product/B019CY4FB4 (mid priced meter)
Other maintenance includes checking cable connections for corrosion/dirt/ensure bolts are tight.
If you have parallel battery strings--Make sure they are wired "optimally" to share current (charging/discharging):
http://www.smartgauge.co.uk/batt_con.html
And read through the battery manual... Or look at Rolls or Trojan manuals for reference:
https://rollsbattery.com/public/docs/user_manual/Rolls_Battery_Manual.pdf (downloading very slow for me today)
http://www.trojanbattery.com/pdf/TrojanBattery_UsersGuide.pdf
For programming your system... I am not the person to ask. Read the manuals and start with their suggested settings. Test your system (do you have a backup genset too?). Gensets can be setup to run once a week or once a month--Or you can "pickle" the genset for storage (put staring battery on float charger if needed) and only start when needed (I have done this for my small Hondas--And they have always started/ran nicely once filled with new fuel--Even after years or a decade+).
If you really need backup power--The old saw that 1 is none, 2 is one, and 3 is 2 (regarding backups)--I.e., two gensets--I use one small one (fuel efficient) and a second cheap bigger noisy genset if the first does not run, or I need more power for some reason).
Fuel storage--Gasoline and Diesel need preservatives, gasoline should be recycled every 6-12 months even with preservative. Diesel needs to be in airtight/low humidity tank to prevent algae growth. Propane is a very nice fuel for storage--Especially if you already have propane for your home. Other issues can include cold weather/smaller tanks "freezing" when running genset (if using propane vapor for genset).
I will stop here... I am sure others can add their suggestions (I am Grid Tied, and use backup genset--I do not have a battery backed system). Other than very recently--Power outages are very rare and not more than an hour or two for me--Other than the latest wild fire warnings and required utility shutdown... Perhaps that is over with now (and the old earthquake prep'ing here).
-BillNear San Francisco California: 3.5kWatt Grid Tied Solar power system+small backup genset -
Thank you BillYes, I have a remote battery temp sensor.The battery is Earls Refurbished Solar BatteryIt is my understanding that you can not sell back to the grid if it is in float mode. The grid support voltage sells back to the grid when the battery is over this set voltage. I currently have it set at 55 V and was wondering if it is healthier for the battery to be kept at a higher voltage?Great advise on checking each cell with a voltmeter and checking outliers with the hydrometer. I just bought the
MidNite Solar Hydrovolt Battery Hydrometer
from this website.So it seems that each month I should go off grid in the evening to pull my battery down to 75% SoC (what V does that correspond to for me?), then equalize the battery, then top it off with distilled water, then check with voltmeter, and then check outlying cells with hydrometer.Also, I have two inverters. Do I set each at 43.75 Amps maximum charge rate or divide that by two?Chuck -
Do you know the brand/model of battery that has been reconditioned? Some require higher voltages to charge/EQ vs others.
Sounds like you may have a forklift/traction battery (require a bit higher charging voltage--Watch electrolyte levels. Some of these types of batteries do not have a large electrolyte reservoir and tend to need watering more often--You do not want to ever let the plates get exposed to air. And don't fill to the very top--especially when "cool". Just make sure plates are covered then charge. At end of charging cycle you can then fill the cells most of the rest of the way--Otherwise a cold/filled battery can push out electrolyte through the caps as the cells get hot and gassing. Big mess).
I am not the expert here--Starting with the settings recommended by Schneider is a good start for the "float voltage".
For an 875 AH battery bank--Normally around 10%-13% rate of charge is ideal for longer battery life (875 AH * 10% = 87.5 Amp nominal charging rate). An 8,100 Watt array will output a typical maximum charging current (cool/clear day, around solar noon, battery bank less than ~80% state of charge):- 8,100 Watt array * 0.77 panel+controller deratings * 59 volts charging = 105.7 Amps typical max
- 105.7/875 AH = 0.12 = 12% rate of charge
For State of Charge under ~80%, the batteries can take a lot of current (or even "excessive" amounts of current)--However, FLA batteries are very efficient below ~80% SoC, so they tend not to heat or gas much (if at all).
When the FLA batteries are over ~80% or so SoC, then the start to gas--But at that point, they should be at the setpoint of the charge controller(s)--And the the FLA bank will naturally start to current limit itself--So having a higher current charging source does not change much as long as the Absorb (and float) voltages are set correctly.
Batteries keep cool are happier (for every 10C/18F over 25C/77F, batteries age 2x faster). Monitoring specific gravity (logging sg readings for all cell into a lab book is a good idea). And typically EQ once a month (around 5% to 2.5% charging current to EQ--After batteries are first fully charged normally). EQ is typically stopped when all the individual cells stop rising in SG (that is the "new" fully charged SG level fr each cell). Or stop when batteries start to get too hot (typically over ~45C/113F). If EQ is still needed, start again the next day. Typically cells should be not more than 0.015 to 0.030 sg units from high to low cell--When over that spread, EQ is typically performed. Note that cells will have a maximum SG reading--Once reached (cell no longer rises SG between readings), that cell will not ever go any higher with SG.
Traction/forklift batteries tend to require more EQ than other types... And it can take a few days of EQ cycle to get everything in balance, and sometimes a series of charge/discharge/charge cycles to get to maximum SG readings (condition the plates). So just keep an eye on everything.
FLA batteries do use water... Typically if you have to fill "low electrolyte cells" every month or less, perhaps crank down the charging setpoint a bit. If the cells go 6 months between fills, then crank up the setpoint a bit.
Remember--If you cycle once a month--Recharging normally first (hold absorb voltage for 2-4 hours or so), then EQ... Do not try to EQ a partially charged battery--You do not want too much current, or to get the cells into a "rolling boil". Charging to >90% state of charge is fine... Do not try for 100% state of charge every day... Gassing uses water, and is sort of hard on FLA batteries (plate erosion, plate corrosion, higher battery temperatures).
Taking with your battery source--They may have some good information too about keeping your battery happy.
The gold standard for state of charge is to use your hydrometer... Using voltage is a bit hit and miss... Lead Acid batteries have variable voltage due to state of charge, current levels, temperature, and even age:
http://www.scubaengineer.com/documents/lead_acid_battery_charging_graphs.pdf
Just using a bit of math and the numbers (WH or AH) from your XW, you can estimate 25% battery usage:- 875 AH * 48 volt nominal bus voltage * 0.25 of capacity = 10,500 Watt*Hours of bank usage
- 875 AH * 0.25 = 219 AH of bank usage
https://forum.solar-electric.com/discussion/4426/working-thread-for-solar-beginner-post-faq/p1
-Bill
Near San Francisco California: 3.5kWatt Grid Tied Solar power system+small backup genset -
I do not have the brand/model.Lots of good information. How do I know what my 100% SoC is?
-
You won't like this but I don't recommend grid selling or supplimenting from a battery based hybrid inverter..
With PV charge controller DC charging batteries and single phase inverter pulling from batteries to push power to AC you are subjecting batteries to constant high ripple current. If you push 4kW to AC from inverter you will have over 120 amps peak to peak ripple current going through batteries even with net zero average current through batteries.
The DC PV charge controller delivers a near constant (PV illumination based variance) DC current to batteries. The DC input current profile for single phase sinewave inverter is sine squared profile at 120 Hz with peak to peak current of 1.57 times the average DC current. The batteries are acting like a large filter capacitor with the associated push-pull ripple current.
The absolute worse mistake made is having a large PV array with too low AH batteries. For lead-acid the peak ripple current should not exceed 25% of the AH size in amps of battery array or there will be significantly more battery longevity degradation.
Your associated extra battery replacement costs over time may eat up grid power savings. Put the money into a GT inverter and use AC coupling to cover you when grid goes down. This prevents high ripple current on batteries for PV AC power push. You will also get greater PV to grid power conversion efficiency then conversion efficiency of charge controller times the conversion efficiency of hybrid inverter.
I could almost agree to grid selling from a hybrid inverter with LFP batteries held at 50-70% state of charge float voltage.
Categories
- All Categories
- 228 Forum & Website
- 136 Solar Forum News and Announcements
- 1.4K Solar News, Reviews, & Product Announcements
- 199 Solar Information links & sources, event announcements
- 898 Solar Product Reviews & Opinions
- 256 Solar Skeptics, Hype, & Scams Corner
- 22.5K Solar Electric Power, Wind Power & Balance of System
- 3.5K General Solar Power Topics
- 6.7K Solar Beginners Corner
- 1K PV Installers Forum - NEC, Wiring, Installation
- 2.1K Advanced Solar Electric Technical Forum
- 5.6K Off Grid Solar & Battery Systems
- 428 Caravan, Recreational Vehicle, and Marine Power Systems
- 1.1K Grid Tie and Grid Interactive Systems
- 654 Solar Water Pumping
- 816 Wind Power Generation
- 624 Energy Use & Conservation
- 619 Discussion Forums/Café
- 312 In the Weeds--Member's Choice
- 75 Construction
- 124 New Battery Technologies
- 108 Old Battery Tech Discussions
- 3.8K Solar News - Automatic Feed
- 3.8K Solar Energy News RSS Feed