Advice on grid design for sunsaver mppt 15 w/ multiple panels
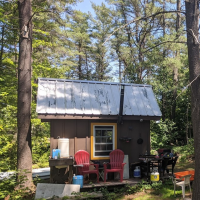
Comments
-
Welcome to the forum Northwoods,
Lots of questions here. I will attempt to help.
First, if you need a portable refrigerator, the unit you have is fine... However, if you need one to hold more food at the cabin, I suggest you also look through the full size DC refrigerators. For example Homedepot.ca:
https://www.homedepot.ca/search?q=dc%20refrigerator#!q=dc%20refrigerator
A 10 cft refrigerator/freezer does not use that much more energy than the small 2.x cft portable fridge--524 vs 396 WH per day (I will say "in theory" for the energy numbers--In practice, how you use the fridge does affect energy usage... Freezing a bunch of ice every day, placing warm food in, then cooling, high ambient temperatures can all increase energy usage):
https://www.homedepot.ca/search?q=dc%20refrigerator#!q=dc%20refrigeratorStarting with the hours of sun per day you can harvest:- Super efficient construction features 3.5 in. (9 cm) of insulation in the freezer and 1.9 in. (5 cm) in the fridge
- Total Watt stable running (24V DC): 524 W/24hrs
- Danfoss/Secop compressor the world's leading DC compressor
- Features an inline fuse for protection
- Features adjustable heavy-duty glass shelves, a bottom crisper and an interior light
- Fridge Temp. Range: -2°C to 10°C (28.4°F - 50 °F) and Freezer Temp. Range: up to -25°C (-13 °F)
http://www.solarelectricityhandbook.com/solar-irradiance.htmlHamilton
Measured in kWh/m2/day onto a solar panel set at a 62° angle from vertical:
Average Solar Insolation figures
(Optimal summer settings)
You could, for example, place 1/2 of the panels facing southwest and the other 1/2 facing south east... That will give you more hours of harvest per day--Which is great for lead acid batteries (they are always happier with more time on charge)--And you will lose something like 10% of your harvest efficiency in summer with non-south facing array.Jan Feb Mar Apr May Jun 2.38
3.22
3.94
4.64
5.09
5.59
Jul Aug Sep Oct Nov Dec 5.68
5.22
4.54
3.46
2.23
2.03
If you want to see hour by hour how much shading will cost you, the PVWatts program lets you download a 365 day hour by hour spread sheet:
https://pvwatts.nrel.gov/pvwatts.php
The bad news is that ANY SHADING on a solar electric panel will pretty much "kill" its output. 50% to 100% loss of charging current is pretty standard. So if you have "moving" dappled sunlight on a forest floor--Solar is not going to do good for you. However, if you have some spots with AM sun, and others with PM sun, installing arrays in both locations with SW/SE facing arrays can give you pretty good results.
Of course, we are about at the point where the sun is highest in the sky--You have to look at March through September (or whatever are you peak seasons) and see what happens to your sun.
You may be able to find a Solar App for your smart phone that can give you an idea of how the shading vs sun position in the sky will affect your harvest.
Next--Battery Bank. I like to call the battery bank the "heart" of your system. Your loads define the battery bank, and the loads and battery bank size determine the size of the solar array (location, shading, tilt, shading also matter too).
Sizing the battery bank... Typically we use 1-3 days of storage, and 50% maximum discharge. AGM batteries have lower self discharge/are more efficient than flooded cell. And you have a large supply of cheap/free AGMs. So, this may not be a limiting factor for you. But lets guess that 1,500 WH per day is your energy usage (fill in your own numbers as needed). A 2 day storage, 50% max discharge 12 volt battery bank would look like:- 1,500 WH per day * 1/0.69 AGM DC off grid system end to end efficiency * 1/12 volts * 2 days storage * 1/0.50 max discharge = 725 AH @ 12 volt battery bank
- 1,500 WH per day * 1/0.69 AGM DC off grid system end to end efficiency * 1/24 volts * 2 days storage * 1/0.50 max discharge = 326 AH @ 24 volt battery bank
- 725 AH * 0.10 rate of charge = 72.5 Amps
Anyway, a suggested solar array for a 10% rate of charge for either voltage battery bank battery bank would be:- 725 AH * 14.4 volts charging * 1/0.77 panel and controller deratings * 0.10 rate of charge = 1,356 Watt array nominal
The other question is hours of sun per day... Assuming you get 4.0 hours of day minimum sun per day (clear of shading):- 1,500 WH per day * 1/0.69 DC AGM system eff * 1/4.0 hours of sun per day = 543 Watt array minimum
You can series/parallel your batteries into one big battery bank just fine. I suggest that 1-3 parallel strings is optimum--If you have lots of "no cost" batteries, you can put more strings in parallel--But it can become a pain to wire and maintain. In theory, with lots of parallel battery strings, each string should have its own fuse/circuit breaker to reduce the chances of a shorted battery string causing a fire.
Wiring wise, this web page does a good job of explaining the better wiring configurations/options:
http://www.smartgauge.co.uk/batt_con.html
Regarding multiple arrays and charge controllers--You can connect them all to one battery bank/battery bus just fine. The individual controllers should be programmed the same (same charging voltage set point). And each controller will go into float based on what each "sees" on the battery bus. They will not go into float at the identical times, but that really does not matter for the big picture.
Charge controllers should be close to the battery bank with short/heavy wire runs--You want low voltage drop from controller to battery bus... Typically 0.05 to 0.10 volts for 12 volts, and 0.1 to 0.2 volts for 24 volt systems.
The "longer" wire runs should be from the array(s) to the charge controller(s). Each MPPT controller should be connected to its own array (do not electrically share one array with multiple MPPT controllers--They do not work well connected that way). You want to solar array wire drops to be in the ~1-3% voltage drop range. For longer distances, higher Vmp-array voltage lets you use smaller AWG wiring from array to controller--And saves you money on copper.
I personally suggest one battery bank... Having separate battery banks is more to monitor, and does not allow you to share harvest and loads between separate systems. Paralleled charge controllers to one bank is fine.
(
Mixing older batteries into a single battery bank is always suspect. "Free" batteries are hard to ignore. Ideally, you want to "match" batteries in a series string (i.e., two 100 AH capacity batteries in one string gives you 100 AH at 2x the voltage--If you mix a 50 AH and 100 AH battery in one string, the string now has 50 AH "usable" capacity).
If your "free" batteries are relatively large AH capacity (100 AH or larger)--Then it is probably worth trying them and "chucking" the bad/poor performing batteries. You will probably get something like 2-5 seasons out of them.
If they are 20 AH or smaller batteries--I would chuck them (recycle) and get new batteries. For a start, "Golf Cart" batteries are inexpensive and relatively rugged/forgiving (many people "murder" their first battery bank to two--Expensive batteries can really hurt your wallet). A typical "golf cart" battery is 6 volts @ 200 AH (and something like ~USD $100 each in USA). 2x 6 volts in series gives a 12 volt bank. 3x 200 AH strings in parallel gives 600 AH.
I suggest that you get a couple of tools. A hydrometer (if you use flooded cell, not useful for sealed/AGM batteries):
https://www.solar-electric.com/search/?q=hydrometer (solar-electric.com is our host for the forum)
And I recommend an AC+DC Current Clamp DMM:
https://www.amazon.com/UT210E-Handheld-Digital-Resistance-Capacitance/dp/B06XSMDMYV (low cost meter)
https://www.amazon.com/gp/product/B019CY4FB4 (mid-cost meter)
Just some suggested starting links to research... Note there are AC only current clamp meters too--They are perfectly good meters, but we need AC+DC clamp meters for debugging the DC section of the solar power systems. Clamp meters are very safe and easy to use (no cutting of wires to measure current).
There are still other things to discuss... The Vmp-array vs charge controller vs battery bank voltage for example. 2x "12 volt" solar panels (Vmp~17.5 volts per panel typically) is fine for a 12 volt battery bank and MPPT charge controller... But if you use 24 volts 3x panels in series with 2x parallel strings is probably a better fit. And note, at 24 volts, your charge controller can manage 2x more solar panels.
Anyway--When you ask lots of questions, you can get long replies. Note that the array/current/etc. recommendations are estimates. In solar power anything that is within 10% of "the number" is pretty much dead on accurate. I use more digits so you can follow the math easier (and not get more rounding errors).
Your thoughts/questions/corrections?
-BillNear San Francisco California: 3.5kWatt Grid Tied Solar power system+small backup genset -
This is really great information thanks - and especially your point about targeting the panel direction based on places where I can get clear skies at any given time of day. Considering my location, there are some brighter sunny areas that are not on the cabin roof, so maybe I should built a little shed and have all of the solar happening there - then run cable to the cabin from the shed. Would it be better to have the longer cable run be panels->controllers (and have the batteries and controllers at the cabin site) or between batteries->load?I could see having a 4 panel grid facing to midmorning sun and a 4 panel grid facing mid afternoon sun and have these two controllers feeding the same bank. I thought that some shade would be OK but knowing that it's possibly cutting charge rate to zero means I'll work harder at finding clear sky.Of course your detailed reply creates more questions but that is part of the fun. The batteries are all 100AH agm. So I guess what I should do is put a load on each one separately and try to figure out the discharge rate and capacity. Or get a tool that can tell me these things... then I can decide which are worth using.Luckily, this is just "for fun" and anything I do will be better than carrying batteries back home twice a summer to charge them. THe worst case scenario is melted ice and no patio lanterns :-)
-
OK I did a little spreadsheet for load. Due to space restrictions I want to stick to a smaller chest style fridge, specd at <400Wh/day. I also think they are less wasteful when you open and close them. I made two columns, one for unoccupied time in case I want to leave the freezer on while I am away, and another for occupied time (days that we are there and using other things and also opening and closing the freezer). I set the number of days to 3 as we are most commonly visiting for 3 day weekends, and only do one or two extended stays a year. it looks like 4 matched 100Ah batteries would be a decent bank size and unless we get no sun for 3 straight days, our visits will be covered well.
Daily Demand Wh Occupied Unoccupied Freezer 500 400 Interior LED 25 0 Exterior LED 25 10 music, usb chargers, etc 50 0 total 600 410 Bank Size Ah 435 297 Since there are days of low (or zero) load in between visits, I feel like the charge rate can be lower, right? If it takes a few days for the solar charging to "recover" from a discharged state that occurs during our visits, it's not a big deal since we aren't there for a week or two in between weekends.The question remains - what is the best way to deploy 8 panels and up to 4 charge controllers? I could in theory have any of the following:- 2 panels into each controller, either series or parallel, and then 4 controllers feeding the one 12v bank
- 3 panels in series to one controller (for two 36 volt strings) and 2 panels to a third controller (@24 volt input) and those 3 controllers feeding the one 12v bank
- the 2x2 series/parallel (24 volts from 4 panels) in to two controllers I mentioned in my first post, but connected to one bank instead of separate banks.
If I am understanding your previous message correctly, it means I can connect the output of multiple charge controllers to the same battery bank, therefore it makes more configurations possible than I previously thought. The controller specs are:Charge Rating 15 amps Max. PV Open Circuit Voltage (Voc) 60 volts Nominal Battery Voltage 12V or 24V Nominal max. Operating Power* 200W/12V, 400W/24W Peak efficiency 97.5% Battery Voltage Range 7-36V Voltage Accuracy 1.0% Operating Temperature Range -40 C to +60C Warranty 5 Years I guess what I don't understand is how to best enable the sunsaver controllers to get the most charging out of the panels under my conditions (limited times of full sun). From what I am reading, it is beneficial to have a much higher input voltage than charge voltage, so feeding 36v strings in could be better, even though intuition tells me that having 3 panels in parallel would give better charge because the amperage is higher.
Or I can just use candles and an acoustic guitar :-)
-
I miss-remembered Vpanel-max for the SunSaver MPPT controller... 60 volts max--3x panels is too much. 2x is about it for (Voc~21 volts) "12 volt" panels.
The maximum/optimum array would be:- 15 amps * 14.4 volts charging (AGM) * 1/0.77 panel+controller deratings = 281 Watt array
If you have "extra" panels--might as well use them.
It is a great little controller--But has its limitations.
I am guessing you are staying with a 12 volt battery bank? 600 WH per day? 3 days and 50% max discharge, bank size would be:- 600 WH * 1/12 volt battery bank * 3 days storage * 1/0.50 max discharge = 300 AH @ 12 volt battery bank
- 400 AH * 14.4 Volts charging * 1/0.77 panel+controller derating * 0.05 rate of charge = 377 Watt array minimum
- 400 AH * 14.4 Volts charging * 1/0.77 panel+controller derating * 0.10 rate of charge = 753 Watt array minimum
- 400 AH * 0.05 rate of charge = 20 Amps minimum
If you have 4 days to "recharge", and use 5x600w=3,000 WH for your three day loads. And you have 2x 400 Watt arrays (really 2x 281 = 562 Watt "useful" arrays), then the Hours of Sun you would need would be:- 3,000 WH of load * 1/0.69 DC AGM system efficiency * 1/562 Watt array * 1/4 days to recharge = 1.93 hours of sun average per day
- 3,000 WH of load * 1/0.69 DC AGM system efficiency * 1/562 Watt array * 1/7 days to recharge = 1.11 hours of sun average per day
Sending 12 volts any distance is very difficult. To send any "useful current" at 12 volts with 0.5 volt (or less drop) takes pretty heavy copper cables to do that... Your fridge take 2.7 Amp running. Say 0.5 volt drop. And 10 AWG cable--How far can you run the 12 volt wiring. Using a voltage drop calculator and playing with the distance:
https://www.calculator.net/voltage-drop-calculator.html?material=copper&wiresize=3.277&voltage=12&phase=dc&noofconductor=1&distance=90&distanceunit=feet&eres=2.7&x=0&y=0
That is 90 Feet @ 10 AWG with only 2.7 amps @ 12 volts (~33 Watts):Result
Voltage drop: 0.49
Since your Vmp-array is going to be closer to (2x 17.5 volts Vmp per panel) ~35 volts, you can send the voltage/current longer distances easier.
Voltage drop percentage: 4.05%
Voltage at the end: 11.51
However, you do need to do voltage drop calculations for your >281 Watt array (400 Watts?).- 15 amps output * 14.5 volts charging * 1/35 volts Vmp-array = 6.2 Amps rough maximum Varray current
https://www.calculator.net/voltage-drop-calculator.html?material=copper&wiresize=2.061&voltage=35&phase=dc&noofconductor=1&distance=150&distanceunit=feet&eres=6.2&x=79&y=26
8 AWG cable (one pair per array, so 2x arrays and 2x cable pairs to two charge controllers) minimum gauge suggested:Result
Voltage drop: 1.17
Voltage drop percentage: 3.34%
Voltage at the end: 33.83How much is 150 Feet of 8 AWG cable direct burial cable? Looks like you can get 3 wire + ground (use ground as 4th conductor?) for $1.30 USD per foot... Did not find in Canadian Home Depot...
Anyway--You have lots of decisions to make and I can only guess at what works best for you... But this is a way to figure out your options.
You do have 4x sun savers, and you could put 2x series panels per sun saver. And have 4x arrays out there gathering sunlight... Just depends how far down the rabbit hole you need to go (smaller arrays, either less copper AWG, or longer wire runs into clear field--Which ever works better for your needs).
Anyway--You do have options, and I don't want to get too confusing in my post here.
Please feel free to ask questions. Or pick what works best for you (2,3,4 charge controllers, how far from battery bank to array per controller).
Generally like to suggest batteries and controllers next to cabin... Much easier to do maintenance and keep an eye on everything rather than having to walk a couple hundred feet to check the system out... And as you add more loads, keeping the 12 volt wiring short means less issues.
I will stop here before I make things even more confused (or confuse myself more).
-Bill
Near San Francisco California: 3.5kWatt Grid Tied Solar power system+small backup genset -
Try to arrange your panels so that they all are in the sun at the same time.
If you use a MPPT controller, if one panel in the string is shaded, pretty much count on the entire string shutting down. They are solar panels, not shade panels.
If you use a PWM controller, with all panels in parallel, the shaded panels won't hinder the sunny panels
As batteries sit discharged, they slowly sulfate. If you think you will charge a little bit each day for 5 days and then use it up on the weekend, it's been done before and the batteries don't like it. Just get enough solar to charge them in 2 days of your avaib sun hours.
Powerfab top of pole PV mount | Listeroid 6/1 w/st5 gen head | XW6048 inverter/chgr | Iota 48V/15A charger | Morningstar 60A MPPT | 48V, 800A NiFe Battery (in series)| 15, Evergreen 205w "12V" PV array on pole | Midnight ePanel | Grundfos 10 SO5-9 with 3 wire Franklin Electric motor (1/2hp 240V 1ph ) on a timer for 3 hr noontime run - Runs off PV ||
|| Midnight Classic 200 | 10, Evergreen 200w in a 160VOC array ||
|| VEC1093 12V Charger | Maha C401 aa/aaa Charger | SureSine | Sunsaver MPPT 15A
solar: http://tinyurl.com/LMR-Solar
gen: http://tinyurl.com/LMR-Lister , -
OK this all makes sense, so I will plan to locate two arrays according to clear sky view and feed those to a cabin-based bank and controller. I assume copper is copper and I can use rubber armoured cable that otherwise was intended for household AC use. I was reading about grounding and it seems like I should have a ground rod off the negative take off from the battery bank. Any ideas about how to ground into exposed bedrock? WHat are the repercussions of not tying to actual earth ground? I read the grounding sticky and my head was spinning a bit.By the way, for completeness sake here are my panel specs:Pmax 95WPeak 17.6VPeak 5,40AOpen circuit 21.3short cicuit current 5.82AThanks again, this has been very helpful to see these calculations and considerations as applied directly to my example case!
-
We try.Regarding grounding, do you have lighting in the area?BillNear San Francisco California: 3.5kWatt Grid Tied Solar power system+small backup genset
-
As long as the insulation is rated for voltage and conditions (wet, buried, uv sunlight, as conditions require).There can be an issue with non standard cable.Standard USA equipment is designed for solid or coarse stranded cable.Fine stranded cable will not work under standard binding screws and wire nuts. It squishes and moves out from pressure points... So you may have to put short pig tails to wire to controllers and circuit breakers, or use crimp thimbles to control the strands...Bill
PS: Updated to fix some auto-corrects from my phone posting.Near San Francisco California: 3.5kWatt Grid Tied Solar power system+small backup genset -
Grounding into exposed bedrock has 2 possibilities, and i don't know if they are recognized as valid.
1. Find a crack and drill 10' down, 1 " di. slide the ground rod in and fill the hole up with copper sulfate (tree root killer for plumbers) and water it in, and add more. you want a slurry that will seep into cracks in the rock and make it conductive.
2. Build a 15 foot square concrete form, layer in some half inch rebar and mesh reinforcement. pour a slab over the rock. The concrete has lots of free ions and you may get enough conduction thru the large surface area of the rock to make it worthwhile. And hope it does not become a lightning rod
These are untried pie in the sky thoughts, but thats what I'd start with.
Powerfab top of pole PV mount | Listeroid 6/1 w/st5 gen head | XW6048 inverter/chgr | Iota 48V/15A charger | Morningstar 60A MPPT | 48V, 800A NiFe Battery (in series)| 15, Evergreen 205w "12V" PV array on pole | Midnight ePanel | Grundfos 10 SO5-9 with 3 wire Franklin Electric motor (1/2hp 240V 1ph ) on a timer for 3 hr noontime run - Runs off PV ||
|| Midnight Classic 200 | 10, Evergreen 200w in a 160VOC array ||
|| VEC1093 12V Charger | Maha C401 aa/aaa Charger | SureSine | Sunsaver MPPT 15A
solar: http://tinyurl.com/LMR-Solar
gen: http://tinyurl.com/LMR-Lister , -
10 feet?
-
Regarding lightning, there is some, seasonally, but intermittent. Is the grounding necessary because the panels attract lightning? Or is it to protect against shock hazard for users? I'm surrounded by 60 -80 foot pine trees, my panels will be at most 10 feet off the ground so I don't expect they will change the sunshine if the area during a storm. In a storm I'm more worried about bad luck striking and a tree falling on me than I am about lightning 😂For connections I'll be doing all crimped spades/rings as opposed to screws direct to wire 👍If you haven't seen it before, here is my inspiration for proper wire termination practises. It's a great read if you are into extremely detailed thoroughness!
-
Nice termination guide.
Regarding grounding... There are several reasons for grounding.
The first is to provide a return path for stray current flow. I.e., two wires to an outlet or device, a third safety ground wire that can attach to metal (junction box, three prong cord to metal drill body, etc.). If there is a short, the ground wire will trip the protective fuse/breaker rather than energize the piece of metal/sink/water pipe/gas pipe/etc.
And why the Neutral/Safety ground wire is also bonded in the main breaker panel (north American standard). To trip a fuse/breaker, you need a solid return path the the energy source.
There are variations. The first is a "floating" output. Whether battery or AC transformer output, if neither side is ground referenced, you cannot short one leg to "ground" as there is no return power path. There are other issues with floating power systems... The main one being that they need to be monitored/tested once in a while to verify that they are still floating output. For example, a short circuit to a grounded metal "thing", the system is now "ground referenced" and a second short/touching of the floating leg now would shock/high current flow.
There is a "work around" for 120/240 VAC power systems and not having a third safety ground wire. A GFI (Ground Fault Interrupter) measures the "differential" current flow in the two wires. If the current out = the current in, there is no short to ground. In the USA, if the difference in current is over ~5-10 milliamps, a wiring "fault" is detected and shuts down the outlet/GFI breaker/etc. (in other parts of the world, none as RCDs--Residual Current Devices). AC wiring is very easy to measure differential current flow with a small transformer... Note that all wiring (for residential size systems) are simple "DC and low frequency AC Models" for behavior.
Grounding to a cold water pipe/earth is not a big issue in "safety grounding". The "legal" resistance for Earth to Ground rod is 5-25 Ohms maximum. Not going to carry much more than 5-25 amps @ 120 VAC (typical minimum branch circuit breaker in a home is 15-20 Amps).
Which brings us to lightning... Lighting is a "radio frequency" event... Lightning can have frequency content to upwards of 7,000 Hz (as I recall). So, the wiring/control must be treated as RF current. And the size/type of wire, how the wiring is run (no "square turns") is important (i.e., Impedance--Inductance and Capacitance--Not just "DC Resistance").
I have to head out right now... But here is a post with some links about lightning:
https://forum.solar-electric.com/discussion/comment/84242#Comment_84242
More discussion, if you wish.
-BillNear San Francisco California: 3.5kWatt Grid Tied Solar power system+small backup genset
Categories
- All Categories
- 228 Forum & Website
- 136 Solar Forum News and Announcements
- 1.4K Solar News, Reviews, & Product Announcements
- 199 Solar Information links & sources, event announcements
- 898 Solar Product Reviews & Opinions
- 256 Solar Skeptics, Hype, & Scams Corner
- 22.5K Solar Electric Power, Wind Power & Balance of System
- 3.5K General Solar Power Topics
- 6.7K Solar Beginners Corner
- 1K PV Installers Forum - NEC, Wiring, Installation
- 2.1K Advanced Solar Electric Technical Forum
- 5.6K Off Grid Solar & Battery Systems
- 428 Caravan, Recreational Vehicle, and Marine Power Systems
- 1.1K Grid Tie and Grid Interactive Systems
- 654 Solar Water Pumping
- 816 Wind Power Generation
- 624 Energy Use & Conservation
- 619 Discussion Forums/Café
- 312 In the Weeds--Member's Choice
- 75 Construction
- 124 New Battery Technologies
- 108 Old Battery Tech Discussions
- 3.8K Solar News - Automatic Feed
- 3.8K Solar Energy News RSS Feed