Absorb Time for LiFePO4
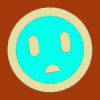
Dave
Registered Users Posts: 59 ✭✭
I've read snippets here and there but nothing conclusive about absorb settings. If this has been discussed elsewhere on the blog, please point me and I'll see if I can get this deleted.
Anyway, up and running with 800Ah bank and learning about balancing/charging etc.
Originally tried charging up to 3.45V but discovered that at my slow charge rates (<0.05C) the knee at 3.4V is incredibly critical and that if the bank starts edging beyond that knee, the balancers cannot keep up and some super cells just start running away.
With absorb at 3.395V, the charge current fell from mid 30s to about 12A over 3 hours. Difference between high and low cell was less than 25mV throughout the time.
They were pretty well balanced at what the graphs show to be over 95% SOC.
If they are nearly fully charged, why does the current continue to fall as they sit at absorb for 3 hours? I was expecting to see the current stabilize and from that I could decide on a reasonable absorb time but it was still falling after 3 hours.
How can I determine how long to leave them at absorb?
My other conclusion is that a float of 3.35 V seems too low. Unlike my FLA batteries, which fell to float voltage over a very short time, these batteries have such great capacity, that they greatly resisted falling to float. For two hours at the end of the day, some power was coming out of the batteries rather than all from the sun. It seemed like a waste that any was coming out of the batteries during the day when sun was available, just to drop the batteries to float.
I'm thinking of a float around 3.375 might lessen this effect.
Is there a downside to setting the float up this high?
12 * 300 W (10 fixed rooftop, 2 movable pole mount), Morningstar Tristar MPPT 60, Magnum 4448 PAE, 64 200Ah CALB in 4p16s arrangement with 16 LED Balancers and a Choice BMS300 (It is lousy and I don't recommend but it provides high and low voltage cutoff)
Tagged:
Comments
-
The thing to remember is that the charge controller was primarily designed to work with lead acid batteries, LFP don't need a long absorption so the controller needs to be programmed to minimize the absorption stage to a few minutes simply to satisfy the controller's 3 stage algorithm.
The float voltage 3.375 VPC is good, it is just before the knee.1500W, 6× Schutten 250W Poly panels , Schneider MPPT 60 150 CC, Schneider SW 2524 inverter, 400Ah LFP 24V nominal battery with Battery Bodyguard BMS
Second system 1890W 3 × 300W No name brand poly, 3×330 Sunsolar Poly panels, Morningstar TS 60 PWM controller, no name 2000W inverter 400Ah LFP 24V nominal battery with Daly BMS, used for water pumping and day time air conditioning.
5Kw Yanmar clone single cylinder air cooled diesel generator for rare emergency charging and welding. -
thanks @mcgivor, i went ahead and reduced the absorb time. the thing that puzzles me is that if the battery is charged when it hits 3.4 (or whatever V), why does the charge current gradually decrease over hours if it is left charging at that V? if the battery were full, i'd expect the current to fall off very rapidly to near zero.even a controller that's designed for FLA, should be able to sense how much current is needed to hold a certain Voltage and only direct that much current into the battery. what am i thinking wrong?
12 * 300 W (10 fixed rooftop, 2 movable pole mount), Morningstar Tristar MPPT 60, Magnum 4448 PAE, 64 200Ah CALB in 4p16s arrangement with 16 LED Balancers and a Choice BMS300 (It is lousy and I don't recommend but it provides high and low voltage cutoff) -
FLA batteries tend to hit the "absorb" setpoint at ~80-90% state of charge (depends on charging current vs AH capacity ratio--Higher charging current, closer to 80% SoC). But there is still chemical reactants available to continue storing energy. So, there is an advantage to hold the voltage setpoint for 2-6 hours (deeper discharge, longer absorb time). And the acceptance current slowly drops through the absorb cycle.
With Li Ion (rechargeable) batteries, they don't need to be "held at absorb" to continue the electrochemical reactions to store more energy (and the Li Ion current does not ramp down when held at absorb, it should drop very quickly to near zero amps).
-BillNear San Francisco California: 3.5kWatt Grid Tied Solar power system+small backup genset -
BB. said:
With Li Ion (rechargeable) batteries, they don't need to be "held at absorb" to continue the electrochemical reactions to store more energy (and the Li Ion current does not ramp down when held at absorb, it should drop very quickly to near zero amps).
-Bill
12 * 300 W (10 fixed rooftop, 2 movable pole mount), Morningstar Tristar MPPT 60, Magnum 4448 PAE, 64 200Ah CALB in 4p16s arrangement with 16 LED Balancers and a Choice BMS300 (It is lousy and I don't recommend but it provides high and low voltage cutoff) -
Is the charge controller holding 14.xxx volts "exactly" during that time?
And it is always possible to pump more energy into batteries, but many times (depending on chemistry, etc.) is not actually storing energy, but causing other reactions (in lead acid batteries, gassing and heat, and over time, damage).
I am not a battery engineer, but the cutoff for Li Ion batteries charging is typically voltage based, and it is because, at that point, there is damage to the cells being done (shorten life, cycle life, and with some specific Li Ion chemistries) the chances of overheating/fire.
There can be "other" issues that affect the apparent charging conditions... If you have a relatively small diameter cable/long cable run from charge controller to battery bank, the resistance of the wire will cause the controller to "see" a higher local voltage vs the battery bus/cell voltage. Another could be if the controller still has the internal temperature sensor/Lead Acid temp compensation enabled (lots of current, controller hot, reduces charging voltage. As charging current falls, the controller increases charging voltage per Lead Acid profile).
And, there is the issue of how the battery BMS (battery management system) works. If there is active cell balancing, you could be seeing the electronics "bypassing" fulls cells to bring up "weak" cells--And just bypassing current for the whole string (pure guessing).
Depending on the current/time profile, you are "charging" another 3-5% of the battery capacity over those three hours--But if the cell voltage limits are being taken to 100% SoC or higher, you are possibly/probably causing damage/reduced battery life (assuming battery bus voltage/cell voltage/BMS is "correct", and not an issue with charge controller issues and slowly creeping higher absorb voltage setting).
More or less, I suggest that if you are within 10% of State of charge or better (in accuracy), that is "close enough" for solar work. Going for that last 5% additional state of charge is not (or at least should not) be make or break for the normal operation of your system (you draw 5% more AH, and your battery bank "goes dead" during normal usage, you are cutting things too close).
And the risk of shortening the life of your battery bank to get that extra 5% SoC--I would suggest is not worth it. You are eating into design/margins of safety (again, assuming a voltmeter on the battery bus is showing that Factory Absorb voltage set point is being obtained and held for those 3 hours).
Measure the battery/cell temperatures and see if they are getting warm. Li Ion charging is weakly "endothermic"--The batteries actually get cooler during charging (and weakly exothermic during discharging, and high(er) exothermic as the cells approach 0% state of charge). If you see the cells/batteries getting warm--That could be heat from battery damage, or from the BMS circuitry.
https://directory.qmed.com/sites/default/files/Electrochem%20Li-ion%20Battery%20Temp%20Trends.pdf
Li Ion cells are very "efficient" and should generate little heat in normal use. If you are seeing heat during operation, something is either wrong (damage) or just part of normal operation (BMS). But heat is a waste product, and if you see it during "absorb", then that energy is not going into charging, but energy lost.
-BillNear San Francisco California: 3.5kWatt Grid Tied Solar power system+small backup genset -
thanks @BB for that follow up and great questions. you piqued my interest so i have been doing some measurements. first of all, i have a 5' run with 4/0 cable between batteries and controller and i use a sense cable that is supposed to tell the controller exactly what V the bank is at. the reason i settled in on a target V of 3.4V is exactly for the reasons you said, to achieve 95% charge while staying well under the max V of the cells (3.65V). The controller specifies 100mV accuracy at 50V but my measurements indicate it is much much closer than that, within a few mV.Right now, shortly after entering Absorb (set at 54.32 bank/3.396 cell), the V measured at the batteries was 54.29-54.30 whereas the V coming out of the controller was dead on 54.32V measured with a fluke meter, a drop of 2 mVish.I noticed that the controller started displaying "Absorb" a few mV and maybe 30 minutes before the full 54.32V was flowing. So, certainly part of the absorb time is going into bringing the entire set up to the set V. Still, the charge current remained roughly the same (~42-44A) for at least the first half hour after that, until I was dragged away, meter in hand, to go on a walk with wife and dog.If the solar power is removed, the V quickly drops to about 53.3V with minimal loads so I am assuming that is more or less the true charge state of the batteries. If so, I am a long way from the 3.4V I was hoping to achieve. Or, since the curves that @Karrak (simon) posted which are serving as the basis for my approach, are for hitting 95% SOC at 3.4V with a charging rate of 0.05C, then, even with little or no absorb, I should be hitting the target.Can you tell I am confused?BTW, these are LiFePO4 cells, not Lithium Ion per se.12 * 300 W (10 fixed rooftop, 2 movable pole mount), Morningstar Tristar MPPT 60, Magnum 4448 PAE, 64 200Ah CALB in 4p16s arrangement with 16 LED Balancers and a Choice BMS300 (It is lousy and I don't recommend but it provides high and low voltage cutoff)
-
When I first started reading here (a long time ago, and I had just installed a GT Inverter system in my home--Still no battery/inverter system, just a backup eu2000i genset), I was reading about batteries and battery systems... And, from the reading, I could not see how battery (lead acid at the time) ever worked. All the operational rules that can't possibly be fulfilled on an offgrid-solar powered system. But, they do work pretty well.
Years later, as the other Dave says, don't sweat the small stuff. It does work, doing things relatively conservatively, and following some basic rules of thumbs as we use here (more or less, used to get an initial design/system "close enough" to give a reliable/working system, and not waste too much money).
Once you have your system in operation, under load, then monitoring how it functions (under load, under charge) is the next important step. If it is working for you, and is roughly on budget, you have gotten 90% there.
Keeping an eye on the system (voltage, current, SoC behavior, differences between cells/batteries/etc.) and getting ahead of any earl can y failure indications (typically something you have not seen before, a bunch of identical cells/batteries with one or more behaving "differently")--Is what you can do.
In the end, if you enjoy your life, then the system is doing its job.
To a degree--I practiced the "black box" version of engineering design. Understand the "box", follow the rules for the box, implement the box in the rest of the collections of other boxes. And normally that works pretty well.
I do understand your confusion... I am not sure I have ever got over mine.
-BillNear San Francisco California: 3.5kWatt Grid Tied Solar power system+small backup genset -
In case anybody is interested, I thought I'd close this out. I've realized that after a couple weeks of charge cycles up to just shy of 3.4 cell voltage (54.32 bank V), my battery is behaving much more stably as the v goes to 3.4 and beyond. so, I was able to raise target V to like 3.43 today and drop absorb time to 15 minutes. these values seem much more in line with consensus and I think having the higher absorb target and shorter absorb time sidesteps the concerns i had about absorb time length. thanks all for the input.
12 * 300 W (10 fixed rooftop, 2 movable pole mount), Morningstar Tristar MPPT 60, Magnum 4448 PAE, 64 200Ah CALB in 4p16s arrangement with 16 LED Balancers and a Choice BMS300 (It is lousy and I don't recommend but it provides high and low voltage cutoff)
Categories
- All Categories
- 229 Forum & Website
- 137 Solar Forum News and Announcements
- 1.4K Solar News, Reviews, & Product Announcements
- 199 Solar Information links & sources, event announcements
- 898 Solar Product Reviews & Opinions
- 256 Solar Skeptics, Hype, & Scams Corner
- 22.5K Solar Electric Power, Wind Power & Balance of System
- 3.5K General Solar Power Topics
- 6.7K Solar Beginners Corner
- 1K PV Installers Forum - NEC, Wiring, Installation
- 2.1K Advanced Solar Electric Technical Forum
- 5.6K Off Grid Solar & Battery Systems
- 428 Caravan, Recreational Vehicle, and Marine Power Systems
- 1.1K Grid Tie and Grid Interactive Systems
- 654 Solar Water Pumping
- 816 Wind Power Generation
- 624 Energy Use & Conservation
- 619 Discussion Forums/Café
- 312 In the Weeds--Member's Choice
- 75 Construction
- 124 New Battery Technologies
- 108 Old Battery Tech Discussions
- 3.8K Solar News - Automatic Feed
- 3.8K Solar Energy News RSS Feed