solar cells are screen printed?
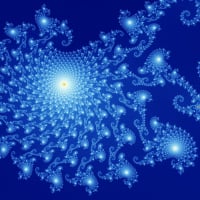
rollandelliott
Solar Expert Posts: 834 ✭✭
just read that solar cells are screen printed!? I never knew that.
http://www.suniva.com/design.php
also what is this ion implantation all about
http://www.pv-tech.org/chip_shots_blog/solar_short_takes_suniva_implements_ion_implantation_first_solar_turns_knob
http://www.suniva.com/design.php
also what is this ion implantation all about
http://www.pv-tech.org/chip_shots_blog/solar_short_takes_suniva_implements_ion_implantation_first_solar_turns_knob
Comments
-
Re: solar cells are screen printed?
The conductive grid on the face of the cell is silver paste that is silk screened on.
This grid captures the electrons migrating from the silicon and flows them onto the bottom of the next cell. The challenge is to make the traces as skinny as possible as they are at the same time shading the silicon below. But, as they get thinner, the resistance goes up. So, that is compensated by have more of them, closer together which is better for capturing more electrons as the recombination distance is shorter. All a game of finding optimum balance of factors. Ion implanting is way more accurate and reliable than screen printed lines of course, but then costs a lot more too. -
Re: solar cells are screen printed?
Most cells have screen printed metalization. Some mono-crystaline cells have metal vapor deposition with copper plating. It is called thin-film deposition since only a very thin layer of metal is vacuum deposited to provide the base for electro-plating of actual conductors.
Metal deposition/plating is superior but more costly to manufacture.
Thick film print metal has higher resistance and the silver in the paste creates a potential migration issue. A passivation layer helps to reduce metal migration.
Other issue with thick film metal printing is adhesion strength and tolerance to heat of soldering connections to it. Many DYI'er have learned this the hard way when soldering on tabbing wire connects. A good panel manufacturer does a sample 'pull tests' on metalization before accepting a lot of wafers. Panels are subjected to a lot of temp cycling in everyday use which puts stress on the tabbing interconnects. Metal adhesion strength is important to avoid an eventual separation of metal attachment due to temperature induced mechanical stresses. Tabbing interconnects should have an "S" shape from top of one cell to bottom of next to help relieve some of the stress on the solder joint.
This is just another reason why DIY panel makers have the deck stacked against them. Most of the "top grade" cells ending up on ebay are rejects for shunt defects or metal adhesion lot sampling.
Categories
- All Categories
- 229 Forum & Website
- 137 Solar Forum News and Announcements
- 1.4K Solar News, Reviews, & Product Announcements
- 199 Solar Information links & sources, event announcements
- 898 Solar Product Reviews & Opinions
- 256 Solar Skeptics, Hype, & Scams Corner
- 22.5K Solar Electric Power, Wind Power & Balance of System
- 3.5K General Solar Power Topics
- 6.7K Solar Beginners Corner
- 1K PV Installers Forum - NEC, Wiring, Installation
- 2.1K Advanced Solar Electric Technical Forum
- 5.6K Off Grid Solar & Battery Systems
- 428 Caravan, Recreational Vehicle, and Marine Power Systems
- 1.1K Grid Tie and Grid Interactive Systems
- 654 Solar Water Pumping
- 816 Wind Power Generation
- 624 Energy Use & Conservation
- 619 Discussion Forums/Café
- 312 In the Weeds--Member's Choice
- 75 Construction
- 124 New Battery Technologies
- 108 Old Battery Tech Discussions
- 3.8K Solar News - Automatic Feed
- 3.8K Solar Energy News RSS Feed