Ready with the c0omponents, but need some reality from the gathered, TIA
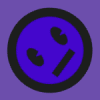
solartrout
Registered Users Posts: 11 ✭✭
OK, I've got all system components acqured. HQST 100W 12v panel,
Epever Tracer 4210AN controller and (finally) a 12v 50AH Lifepo4
battery. No need for an inverter as I have no need for shore power.
I
have one 10AWG extension wire for the panel, to go into the shell, from
the roof of the shell, and I'll use it for moving the panel from the
roof to a ground mount for positioning for maximum harvest.
What
I need is a recommendation for wire going from the controller to the
battery. What size wire (8awg enough? VERY short run) and where can I
get wire with a bare end and ring terminals for the other end, to attach
to the battery?
At my age (68) This is the only solar
system I'll ever build, and I can't justify blowing $50-100 for a
crimping tool to create two wire connections. So where can I get a
two-three-foot cable as described above, so I can get the show on the
road? Can anyone help me?
Comments
-
You want to keep voltage drops to a suggested maximum of:
- 12 volt drop from charger (solar, AC, etc.) to 0.05 to 0.10 VDC max (for fast/accurate battery charging)
- 12 volt drop from battery to loads a maximum of 0.5 volts
- Solar Array wiring drop... Typically suggest 3% max drop (0.03*12v=0.36 volt drop)
https://www.calculator.net/voltage-drop-calculator.html
Say 10 amps from controller to battery... 5 feet with 10 AWG cable:
https://www.calculator.net/voltage-drop-calculator.html?necmaterial=copper&necwiresize=2&necconduit=pvc&necpf=0.99&material=copper&wiresize=0.4066&resistance=1.2&resistanceunit=okm&voltage=12&phase=dc&noofconductor=1&distance=5&distanceunit=feet&eres=10&x=58&y=12&ctype=necResult
Voltage drop: 0.12
So even 5 feet from controller to battery with 10 AWG cable and 10 amps is on the "high side" for voltage drop.
Voltage drop percentage: 0.99%
Voltage at the end: 11.88
You have an MPPT type charge controller... Ideally, the Vmp-array should be around 2x battery charging voltage (14.4*2=28.8 volts "optimum").
You can be higher, and you can be lower... But sending Vmp-array=18 volts to this controller is less than optimum. Ideally, if you had 2* 100 Watt 12 volt panels and wired them in series it would be "better". And then you could remote mount the two panels (in series) remotely and use a much smaller AWG cable (save cable costs and storage space).
Crimping is much more reliable vs soldering (for example). Solder "wicks up the cable" and makes a "fulcrum" where any bending focuses stresses at the fulcrum and quickly will work harden/fracture the copper strands.
-BillNear San Francisco California: 3.5kWatt Grid Tied Solar power system+small backup genset -
Would you suggest using a heavier gauge wire (heavier than 10awg) for charger to battery? What inline fuses (breakers) and battery cutoff do you suggest?
-
I was just using a "random example" of how to use the calculator aound how Amperage, Wire AWG, and distance interact to give you "voltage drop". If the distance in the above example was assembled with 2 feet of cable from controller to battery bank--Then the numbers would be fine (and 10 AWG is "good" for upwards of 30 Amps using NEC ampacity tables).
In practice--You should really go through the full "paper design" process first... Size the battery bank, solar array, AC inverter (if needed) to support your loads. You can also design for future upgrades (say more solar panels as your savings account allows)...
For example, some rough numbers:- 100 Watt solar panel, typically 18 volts Imp
- P=I*V; I = P/V
- Battery charging current = 100 Watts * 1/10.5 volts charging (of "dead battery") * 9.77 solar panel+controller deratings * 1.25 NEC safety factor = 9.2 Amps Minimum suggested Battery Charging Branch Circuit design.
https://lugsdirect.com/WireCurrentAmpacitiesNEC-Table-301-16.htm
From the table, 14 AWG would work (15 Amp max current rating)... 12 and 10 AWG are "common" solar wiring sizes. 10 AWG cable costs a bit over 2x more per foot vs 14 AWG cable.
You could pick 14 AWG with 10-15 Amp fuse or circuit breaker (1.25 NEC safety factor is 9.2--Round up to 10 amps--Conservative numbers). Say you want to be "cheap" (OK to be cheap with good design practices)... Using the Drop Calculator use 9.2 amps with 0.10 max VDC drop and 14 AWG cable. Play with voltage drop calculator by changing distance (this is "one way wire run distance for this calculator) and see what max length is:
https://www.calculator.net/voltage-drop-calculator.html?necmaterial=copper&necwiresize=0&necconduit=pvc&necpf=0.85&material=copper&wiresize=0.4066&resistance=1.2&resistanceunit=okm&voltage=12&phase=dc&noofconductor=1&distance=1.8&distanceunit=feet&eres=9.2&x=0&y=0&ctype=necResult for 9.2 amps, 0.10 VDC max drop, 14 AWG cable, DC current, with 1.8 foot run from controller to battery bank. Note use 10-15 amp fuse/breaker near battery (source of high current to pop fuse if short circuit).
Voltage drop: 0.10
If you have to mount the controller further away (should "always be near" the battery bank), using 10 AWG would give:
Voltage drop percentage: 0.86%
Voltage at the end: 11.9
https://www.calculator.net/voltage-drop-calculator.html?necmaterial=copper&necwiresize=2&necconduit=pvc&necpf=0.85&material=copper&wiresize=0.4066&resistance=1.2&resistanceunit=okm&voltage=12&phase=dc&noofconductor=1&distance=4.6&distanceunit=feet&eres=9.2&x=0&y=0&ctype=necResultfor 9.2 amps, 0.10 VDC max drop, 10 AWG cable, DC current, with 4.6 foot run from controller to battery bank. Note use 10-15 amp fuse/breaker near battery (source of high current to pop fuse if short circuit).
Voltage drop: 0.10
Voltage drop percentage: 0.84%
Voltage at the end: 11.9Another consideration for fuses/breaker... The rated output of the device--Or charge controller in this case. This controller is 10 Amps output... use NEC safety factor of 1.25x higher current or:
- 10 amp controller * 1.25 NEC safety factor = 12.5 amps or round up to 15 Amps (good for 15 AWG or heavier cable)
- 100 Watt panel / 18 volts Vmp (guess) = 5.56 Amps Imp
- 5.56 Amps Imp * 1.25 (rough Isc short circuit current guess--check panel label) = 6.95 Amps Isc
https://www.calculator.net/voltage-drop-calculator.html?necmaterial=copper&necwiresize=0&necconduit=pvc&necpf=0.99&material=copper&wiresize=0.4066&resistance=1.2&resistanceunit=okm&voltage=18&phase=dc&noofconductor=1&distance=15&distanceunit=feet&eres=5.56&x=0&y=0&ctype=necResult for 14 AWG, 5.56 Amps Imp, 3% max drop, 15 feet
Voltage drop: 0.52
So, if you can (one way wire run) run 15 feet from panel to controller--Then 14 AWG will work... If you need a longer wire run, then going with a heavier cable will work. You do not need any fuse/breaker between solar array (and 1 solar panel) and the solar charge controller.
Voltage drop percentage: 2.88%
Voltage at the end: 17.48
You would then decide the maximum current you need from your 50 AH battery bank (i.e, 50 amps, 5 amps, 2 amps, etc.) and do the same 3% voltage drop @ XX Amps and YY feet calculation. And use a circuit breaker or fuse to protect that DC wiring from Battery bank to Load(s).
This is "backwards" in the design process, but just to pick some numbers... Say this is for home backup power in Redwood City California. Using PV Watts to estimate hours of sun per day with array facing south tilted to 37.5 degrees:
https://pvwatts.nrel.gov/pvwatts.php (ignore the second column--Getting late and don't want to bother editing it out)Month Solar Radiation ( kWh / m2 / day )Ignore 2nd column January 3.77 110 February 4.21 108 March 5.77 163 April 6.64 177 May 6.53 183 June 6.86 185 July 6.97 193 August 7.19 195 September 6.95 182 October 6.16 170 November 4.78 132 December 3.79 111 Annual 5.80
Say we pick February as the break even month for 4.21 hours of sun per day (pretty sunny region)- 100 Watt array * 0.61 off grid DC system eff * 4.21 hours of sun per day = 257 WH per average February day
- 257 WH / 12 volt battery bank = 21.4 Amp*Hours per average Feb Day @ 12 volts
-BillNear San Francisco California: 3.5kWatt Grid Tied Solar power system+small backup genset -
I have cables ordered for charger to battery. Bizarre, the place I found the cables was HOME DEPOT!!! Made by Grape Solar, but no one else had 10AWG with bare wire on one end and ring terminals on the other, and because I'm old and this will be my ONLY solar experience, I don't intend to spend $150 for a crimping tool when I can get cables for $20.
Once I get my cables, I'll set everything up. Looking for a plywood scrap to make a mounting board for the electronics.
Categories
- All Categories
- 228 Forum & Website
- 136 Solar Forum News and Announcements
- 1.4K Solar News, Reviews, & Product Announcements
- 199 Solar Information links & sources, event announcements
- 898 Solar Product Reviews & Opinions
- 256 Solar Skeptics, Hype, & Scams Corner
- 22.5K Solar Electric Power, Wind Power & Balance of System
- 3.5K General Solar Power Topics
- 6.7K Solar Beginners Corner
- 1K PV Installers Forum - NEC, Wiring, Installation
- 2.1K Advanced Solar Electric Technical Forum
- 5.6K Off Grid Solar & Battery Systems
- 428 Caravan, Recreational Vehicle, and Marine Power Systems
- 1.1K Grid Tie and Grid Interactive Systems
- 654 Solar Water Pumping
- 816 Wind Power Generation
- 624 Energy Use & Conservation
- 619 Discussion Forums/Café
- 312 In the Weeds--Member's Choice
- 75 Construction
- 124 New Battery Technologies
- 108 Old Battery Tech Discussions
- 3.8K Solar News - Automatic Feed
- 3.8K Solar Energy News RSS Feed