How can I correctly feed a 60 amp Renogy Controller Charger with eight 12 v 175 watt solar panels?
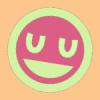
TellGRBill
Registered Users Posts: 111 ✭✭
Hello,
I hope that you have had a joyful holiday. 

I would like to have two trailers, each mounted with four 12 volt 175 watt Renogy solar panels and 100' of 10awg cable leading to my 60 amp Rover Renogy controller from each trailer.
Can I arrange and connect the panels to provide an acceptable total of 700watts for the one 60 amp controller to charge the 12 volt battery bank ?
The controller charger can accept: up to 140 volts, 800 maximum input watts, rated charge current 60 amps.
1Each 12volt 175 watt Renogy panel provides an optimum operating current of 9.73 amps,
If each trailer/solar array has a separate cable leading to the controller charger, the current/amperage of 9.73 amps from both arrays combined is 2(9.73amps), and the 12 volts from the arrays remains 12 volts. What is the wattage of the combined cables from the two (four panel 175 watt 700watt arrays, when connected to the controller charger?
Note: Our Renogy 3000watt inverter only accepts 12 volts.
Comments
-
I am a bit confused... You have a long, detailed discussion that pretty much answered these questions:
https://forum.solar-electric.com/discussion/357595/need-help-setting-up-solar-electric-system-on-our-converted-bus-motor-home#latest
--As far as I can tell... Simply 4 panels in series (each trailer) x 2 trailers in parallel to an (over paneled) 60 amp MPPT controller charging at 12 volt battery bank.
You have other options (buying a second MPPT controller, etc)... But to keep costs down, this is the "optimum for you needs at this time".
The MPPT controller itself will limit its output to 60 Amps when charging your battery bank... And if the controller has "issues" (such as running hot during warm weather/poor ventilation), it will reduce the output current to prevent overheating.
The controller also has "limited output" based on the amount of solar energy from your array... If your array is producing 300 Watts because of clouds/poor sun angle in morning or evening, etc., it cannot produce more output power than the array is capable of providing. The controller will only output 300 Watts (300 watts/14.4 volts charging = 20.8 amps).
There is the issue of over paneling an MPPT controller... Having an array that produces more wattage than the MPPT controller can output.
Typically the math would be:- 60 amps * 14.4 volts charging * 1/0.77 solar array deraring+controller losses = 1,122 Watt "optimum" array typical "best case derated" harvest in warm weather (the 0.77 array+controller derating factor)
A good quality MPPT controller will allow over paneling (larger than XXX Watt array) because it has the capability of adjusting its output current to the battery bank based on its ratings and actual conditions. With your 2x700 Watt trailers (1,400 Watt total), there will be times that array will be capable of producing more than 60 Amps of charging current into your 12 volt battery bank. The MPPT controller will simply not take more Array Wattage than needed to charge the battery bank, up to its 60 amp max output rating.
There are limits to all things... Yes, a well designed 60 amp MPPT controller can be connected to a 100,000 Watt array--It is just that the wiring itself inside the controller could "catch fire" if the controller fails (all things eventually fail).
In this case, the MPPT controller is also designed to charge a 48 volt battery bank--Meaning that it can output 4x more Power (Watts) or (57.6 Volts charging * 60 amps = 3,456 Watts into battery bank) a much larger array and still be "safe" (MPPT controller solar array input rating). As long as you respect the other limits (such as maximum 140 VDC input rating).
-BillNear San Francisco California: 3.5kWatt Grid Tied Solar power system+small backup genset -
Oh Bill, You're wonderful !I thought that maybe you got sick of my long confused questions :-(I was afraid that I lost you as a mentor.Does it help things to use a separate 10awg lead wire for each trailer array, or can I link the trailers together?If you have made progress with your converted van camper plans, please put our farm campground on your travel stops.Struggling Bill
-
Bill, the forum is a "hobby", not a job... I do have a life (whatever that is) too so it may take a day or two for me to reply.
In your original discussion, I did go through the math for 1x vs 2x runs of 10 AWG cable... You will have less losses due to resistance with two 10 AWG runs back to the bus.If you run 1x pair of 10 AWG @19.44 amps (two trailers in parallel on 1x 10 AWG cable run):Now voltage drop calculations.. Say 10 AWG, 100 Feet, 9.72 amps:You will lose ~3.21% of your energy from the array using 10 AWG cable... Not bad
https://www.calculator.net/voltage-drop-calculator.html?necmaterial=copper&necwiresize=2&necconduit=pvc&necpf=0.99&material=copper&wiresize=0.4066&resistance=1.2&resistanceunit=okm&voltage=72&phase=dc&noofconductor=1&distance=100&distanceunit=feet&eres=9.72&x=57&y=20&ctype=necResult
Voltage drop: 2.31
Voltage drop percentage: 3.21%
Voltage at the end: 69.69- 175 Watt panels * 4 series * 0.77 panel+controller = 539 Watts max (cool clear day) per trailer array
- 175 Watt panels * 4 series * 0.77 panel+controller * 0.0321 losses = 17 Watt loss per "trailer"
https://www.calculator.net/voltage-drop-calculator.html?necmaterial=copper&necwiresize=2&necconduit=pvc&necpf=0.99&material=copper&wiresize=0.4066&resistance=1.2&resistanceunit=okm&voltage=72&phase=dc&noofconductor=1&distance=100&distanceunit=feet&eres=19.44&x=0&y=0&ctype=necResult
Voltage drop: 4.62
Will a single run work? You will have 2x the losses because 1/2 the amount of copper... or ~34 Watts per trailer at "high noon" and full current/power draw... Or 64 Watts loss, or as a "solar panel"
Voltage drop percentage: 6.42%
Voltage at the end: 67.38- 64 Watts loss * 1/0.77 panel+controller losses = 83 Watts of solar panel "losses"
If you paid a $1 per Watt for your panels, then you are "losing" ~$41.50 "worth" of solar panel power vs $xx.xx worth of 200 feet of 10 AWG cable...
A huge loss--No. The system will still be functional. Just less harvest...
With solar, we try for efficiency because these losses happen every (sunny) day. But for most people, running 4/0 cable 100 feet (for near zero voltage drop losses) while much lower losses--Just does not make financial sense.
3% cable losses... Pretty much "lost in the noise". You would be hard pressed to even "see" these losses in a day to day system. Over 10% losses. Can start to impact a system's performance.
What is it "worth" to you (more $$$ copper or more $$$ panels, or more $$$ genset fuel, or simply using 6% (or whatever) less power that day).
With off grid solar power--A system is always "over designed" to produce more power than "needed"... You are simply looking at a system that will produce "enough energy" during an average winter week, may produce 4x that amount of energy on a bright/clear/beautiful" summer's day. Vs a design that will work fine during summer, and leave you with dead batteries (or fuel costs for genset) during the winter.
Whether more panels for more generation, or more copper for less losses, or using less energy, or using more fuel for genset during winter weather-These are the trade-offs that only you can make.
-BillNear San Francisco California: 3.5kWatt Grid Tied Solar power system+small backup genset - 175 Watt panels * 4 series * 0.77 panel+controller = 539 Watts max (cool clear day) per trailer array
-
Thank you.1. I guess if I'm already "over paneling" the charge controller. then maybe a little more loss may be an advantage I guess.How would you suggest that I link the two arrays? What type of physical connection?2. I may have up to ten 12 volt 100AH deep cycle batteries in parallel, Can I run leads from several positive battery posts to the main positive battery buss connection? and the same for the negative battery posts?I don't know if I told you before, but a local battery distributor who I have done years of business with, has offered to sell me several used, tested, less than 1 year old, 100 AH, deep cycle batteries for $50 each with 4 month warranty to be sure that they are good batteries.BillNote: I just got your response above by email. That's the first email reply I have ever gotten from Forum Solar-electric !Very helpful !!
-
Bill,
In theory, all you have to do is wire nut (or use bus connectors, etc.) to simply connect the trailer's + connections together, and the - connections together... If you had thee or more trailers, you would use a Combiner box (circuit breakers or fuses) in the + leads to protect against short circuits (when three or more strings of panels are paralleled, the "series protection fuse" (probably something like 15 amps in your case--But always check the solar panel documentation for series protection fuse value) to protect one shorted panel from being fed power from the other parallel strings and starting a fire.
In practice, you might want to use a pair of switches (or circuit breakers in the + or + and - leads. The issue is that if you connect one trailer, the leads to the other trailer are now "hot" and can shock/electrocute some body. Say you use a 15-20 amp "plug and socket" to connect each trailer. Normally the "socket" is the "hot" (protected from human touch) and the plug "blades" are un-powered. However, when connecting the second trailer, both the wiring from the trailer is powered, and potentially the power from the charger is powered by the first trailer. Having a pair of switches at the "combiner point" lets you keep the "2nd connection" "dead" until you connect (if using standard plugs and sockets at the trailer).
The SmartGauge website talks about how to "optimally" connect batteries so they "share charging/discharging current" when you have paralleled battery banks:
http://www.smartgauge.co.uk/batt_con.html
To be honest, your setup with separate "battery pods" makes it difficult to wire optimally... So in your case, you are just using (relatively) heavy wire between batteries to keep voltage drop between pods low.
I guess, which ever is your largest "AmpHour Pod", wire per the SmartGauge link... Wire each other "pod" like per the link... And simply run the + and - connections between each pod... There is nothing else you can do to make "and optimal" distributed battery bank wiring scheme.
I am not a fan of running multiple parallel sets of wiring (such as wiring banks in parallel then running, for example, charger connections to each pod too--Those "charger connections" now become more parallel connections). The "extra parallel wiring" are more possible shorts and poor connections waiting to happen (and more $$ copper). But then you have this parallel cabling. Say 8 AWG (just example numbers to type about) from charger and 4/0 for battery main connections. If you have a poor 4/0 connection, it would now force your 3,000 Watt inverter to draw its current through the remaining 8 AWG connections and could overheat those remaining "good" small AWG cables. This is why paralleling current connections (i.e., 2x 1/0 in parallel vs 1x 4/0 is usually not allowed or a good idea).
And each small AWG parallel connection back to the charge controller should have its own fuse/breaker (protect the 8 AWG cable against short circuits)... More cost and complexity and more to go wrong.
You have a relatively "complex" wiring scheme for your bus... You have to be very careful that you don't setup trip points (such as "live connections" at the "2nd trailer" or multiple parallel connections without fuses/breakers.
Glad to hear your email notifications are working... You can go to your profile and edit what kinds of notifications you want to receive here:
https://forum.solar-electric.com/profile/preferences/
Take care,
-BillNear San Francisco California: 3.5kWatt Grid Tied Solar power system+small backup genset -
That battery wiring link is very helpful.Now..help me see ( how / if ) I can apply 3# example to where I can potentially locate batteries.
-
If the "left of drawing" 3+5 batteries are next to each other (4" apart between the two groups?)... I would wire them up as #2 in the SmartGauge drawing. Very simple wiring is my goal. #2 gives you simple point to point cables that are the "right length" and one (or two) long cables to connect to the "battery common buses".
#3 is good, but I fear that you will end up with a large clump of 4' cables (long enough cables to reach the farthest batteries, and clumped with tangled cables that are "too long" to reach the nearby batteries leaving you with a rats nest (the idea being that all battery cable sets are the same length, same resistance, balanced current flow).
The two batteries in the next to the charger--Wire them how you like and combine their +/- buses to the cable running to the 3+5 bank.
I could tell you to add fuses/breakers at various points (like on the 3+5 bus + bus bar and another breaker on the 2 battery bus bar--But I am not sure what that buys you for safety...
The plan is for every + cable that "leaves" the + battery bus should have its own breaker/fuse to protect that cable from over current (if shorted). If you use breakers, that also gives you a handy on/off switch to isolate battery banks for service...
-BillNear San Francisco California: 3.5kWatt Grid Tied Solar power system+small backup genset -
Mentor Professor Bill
That's the kind of advice that I was hoping for. The two groups of batteries are in compartments that are about 4" apart. The compartment with the three battey group was designed and used for the bus vehicle start and operational batteries. The compartment designated for the five battery group was designed as an equipment/tool storage compartment. The two battery group is being used now as the "house" 12volt supply in a compartment along with a 7000 watt motorhome gasoline generator.
I plan to place fuses near power sources and heavy duty switches wherever I think will help with maintenance.
Student Bill -
Hi Bill,
Just to be clear--That is 4 Feet apart (4')... 4" is 4 inches...
Even 4 feet apart--I would probably still go with #2 wiring diagram. Trying to do #3 in a tight battery box(es) is probably not worth trying to jam everything into a cramped space. Whether you treat the 3+5 groups as one bank or as two separate banks connected together--That is up to you. Wiring them up as one bank (via #2) is "better" especially if all your loads/charging sources are connected to the one 3+5 bus.
If you have distributed major loads/charger connections are mixed (some in 3 battery areas and others are in 5 bank area, then I would keep the wiring "simple" and not run "extra" load/charging wiring trying to make a single bus location. (if that makes sense).
The last 2 battery set--So far away that it is practicable to add it via #2 diagram.
Just monitor your battery bank voltages (during charging/discharging) and make sure you don't have large voltage drops/differences during charging and discharging.
Regarding the 7,000 Watt genset...You might want to look at a second smaller 2,000 Watt or so inverter-generator... Especially if you keep your loads "smaller", especially during winter/poor sun. 7 kWatt gensets with light loading (i.e., genset loads closer to 1,000-2,000 Watts) are usually horrible inefficient. You do not get "fuel" efficient with standard type gensets until you are at or over 50% of rated load (around 3,500 Watts for your genset).
Inverter-generators tend to be relatively fuel efficient down to 25% of rated power (i.e., even down towards 500 Watts of loading).
A 2 kWatt ivnerter generator will run on 1 gallon of fuel for something like 4-9 hours.
A 7kWatt Onan:
https://norwall.com/products/cummins-onan-qg-7-0-gasoline-rv-generator-7.0hgjab-900
Runs at 0.7 gallons per hour (if I read the spec's correctly) or ( 1/0.7gph= ) ~1.4 hours per gallon @50% load...
Or something like (8 hours / 1.4 hours) = 5.7 times more fuel for the larger genset... IF you are running smaller load (i.e., ~1,750 Watts genset loads).
If, on average, you have larger loads (i.e. >=3,500 Watts), then you need the larger genset.
But if you looking for longer genset run times... Say 12 hours per day (to keep fridge/freezers cold), then:- 12 hours per day / 8 hours per gallon = 1.5 Gallons per 12 hours per day (small genset, small loads)
- 12 hours per day / 1.4 hours per gallon = 8.6 Gallons per 12 hours per day (big genset, small or larger loads)
For longer term outages (a week or two)--That is a huge difference in the amount of fuel you need to store:- 14 days * 1.5 gpd = 21 gallons of fuel for two week outage (2 kWatt inverter-generator)
- 14 days * 8.6 gpd = 120 gallons of fuel for two week outage (7 kWatt genset)
Propane is a great fuel for storage--And if you already have propane tank(s) at your farm--Then a propane powered genset is a nice mix (get a propane or Propane+Gasoline) capable 3 kWatt inverter-generator (not many propane small inverter-generators available if you want a smaller 2kWatt inverter-genset).
If you are not familiar with inverter-generators... They are a standard generator driving an AC inverter... This allows the generator to throttle back to lower RPM during light loading--Saving lots of fuel. This is "true" for gasoline/propane/natural gas engines.
Or look at smaller diesel gensets--They are much more fuel efficient at lower loads (diesel engines are more fuel efficient themselves). But there is the higher cost of diesel engines (and still issues with long term fuel storage). If you use diesel around the farm anyway--Not a bad option.
Adding more solar panels is always a good place to start--Anything you can do to reduce fuel usage (during outages, winter) is going to be important.
Gensets are frequently a better cost effective solution for random short outages (a couple days every few years)--But the fuel issues are not trivial.
-BillNear San Francisco California: 3.5kWatt Grid Tied Solar power system+small backup genset -
The compartments are Four inches " apart.
-
Battery compartments close together--That is better.
-BillNear San Francisco California: 3.5kWatt Grid Tied Solar power system+small backup genset -
Now I'm wondering about the gauge cable between the battery connections.Student Bill
-
How much current do you plan to draw?
The "issue" with #2 (SmartGauge) laddering of parallel batteries... Say you want to draw 20 amps from each battery max. The first battery in the string will supply 20 amps, the next another 20 amps, and the next (20+20+20...) until you have the last battery connection supplying (for example) 10 batteries * 20 amps each = 200 Amps.
In the ladder scheme, you are drawing current from "kitty cornered" connections. So the current is adding kitty corner too. The The interconnects are adding current so that your increasing current on the positive connectors and increasing AWG is the "opposite" of the decreasing negative connections.
http://www.smartgauge.co.uk/batt_con.html
or:
-Bus common
20 amps 80 amps
40 amps 60 amps
60 amps 40 amps
80 amps 20 amps
+Bus Common
You could size each cable according to its "planned" current loading... Or just size everything the same for the maximum (80 amps in this example)....
Sizing the interconnects for Max Current--Then you would have a fuse/breaker at the final "bus connection" pont. And anywhere there is (possible) short circuit, then all "heavy AWG" cables are protected by the same (100 Amp or whatever) breaker.
Costs a lot of copper (heavy AWG interconnects)--However it is "safe(er)" from that I can see.
In your case, if you plan on using a 3,000 Watt AC inverter at full power, then the minimum wiring/fuse sizing would be:- 3,000 Watts * 1/0.85 AC inverter eff * 1/10.5 volts battery cutoff * 1.25 NEC breaker/wiring derating = 420 Amps Wring+Breaker rating
Using the NEC table (which is sort of conservative)--You would need 500 cmill cable (or a bit less than 3 parallel runs of 4/0 cable) to meet these loads...
Victron, for example, suggests 2x 50 mm^2 or ~1x 4/0 cable minimum (3,000 Watt AC inverter, 12 volts, 0-5 meters, 400 Amp breaker/fuse):
https://www.solar-electric.com/lib/wind-sun/Manual-MultiPlus-3k-120V-(firmware-xxxx4xx).pdf (section 4.2 manual)
https://www.rapidtables.com/calc/wire/awg-to-mm.html (chart AWG to mm^2 conversion)
This is why I originally suggested that you NOT wire the battery bank inside the bus (more or less a fixed "home" at this point) but use a separate "battery shed" and that a 3,000 Watt @ 12 volt inverter is not "saving you money". Going "special/custom/different" gets you into all sorts of questionable issues.
Having the batteries in a separate shed allows you do use larger AH batteries/cells. Install on concrete floor and sheet rock for better fire resistance and keep from "living quarters".
Also, going with 24 or 48 VDC inverters--This allows you to use much smaller diameter cables too.
Does "everyone" use fuses/breakers/"right size AWG" cables for their DIY systems... Probably not. Fires are rare--But they suck (or worse) if they happen to you. Having a fire in a "remote shed" vs a fire in the "basement" of your home or bus--The losses and risk to life are much higher.
Hardware already purchased, low voltage battery bank, high power/current, paralleling/distributing a bunch of batteries in a confined space (bus), etc... They all give you constraints that you may not need (the bus is no longer 'on the road')... And you trying to "future proof" (large 3kW AC inverter but relatively small loads in bus)... It becomes painful.
If you want to limit your power usage (say only use 1,200 Watts of 3kWatt AC inverter)--You can do that for now (smaller AWG, smaller breakers/fuses)... May make your life easier for now.
-BillNear San Francisco California: 3.5kWatt Grid Tied Solar power system+small backup genset -
Each compartment for batteries is completely metal and two designed for battery storage and use. Doubt if we ever use more than 1200 watts consistently but might get a surge higher with refrigerator starting, and small water heater that don't always use, and maybe a small air conditioner that was not even used this past summer. We get a natural breeze through the bus.
We have been only using a 20amp 120v circuit to run everything in the converted bus, 2400 watts MAX limit, being careful.
We have never blown a circuit breaker, but sometimes the lights will dim a moment when there is a surge drawn.Looks like using battery power, and the planned limited system, I'll have to be VERY conservative.I have been thinking about the gauge cables between batteries and to the inverter.I think I will use 4/0 wire between batteries and from the inverter to the closest positive buss.I have found a heavy duty copper mechanical cable lug that I believe will help me make the connections that are secure and durable.The lugs are designed for 1/0 wire but I can easily slim down the ends that will fit into the lugs.I think I have fount a good electric connection box for transferring current between array trailers and from trailers to controller. -
I have been looking and searching for a cover/ weather shield for the power cord I am using with inlet and outlet boxes. I finally found them, I think. Many companies are selling the box, but I haven't found anyone selling the weather shield that screws onto it after the plug in inserted until now.The box has threads around the opening where the plug fits into the box. I would like the cover to screw onto the box when the plug is attached to the box to keep the weather out of the plug and box.
-
An update: I asked for advice from Renogy (the company where I bought my solar panels and other solar equipment) about the wire I should use to connect the battery bank to the 3000 watt Renogy Inverter. I was told to use 4/0awg wire. I searched Facebook Marketplace for someone selling a piece that I could use to connect the batteries together and the bank to the 3000watt inverter. WOW...I had never seen 4/0awg wire. I knew it would be heavy but when I got it, I saw that it was more than I needed or could even handle. Even if I slimmed the ends down for a wire lug it was much too heavy. I have used 1/0 welding wire by slimming the ends down for the lugs but 4/0 wire can't be handled by me. Sooo back to Facebook Marketplace and this time to SELL the 4/0 wire to someone wiring an outlet for a heavy duty welder. I'll go back to 1/0awg welding wire to connect the batteries and the battery bank to the inverter. The people monitoring this advice web site surely must chuckle if they read my stumbling. LOL But I'm learning. I appreciate all the help and patience I've experienced on this web site!!
-
That is the problem with Wattage 12 VDC inverters... Need really heavy cable to support high current and low voltage drop for 12 VDC...
Sometimes you can find local shops (battery sellers, possibly welding supply stores) that can help you with cable ends/crimping/etc...
-BillNear San Francisco California: 3.5kWatt Grid Tied Solar power system+small backup genset -
Hello mentorsI have both solar panel trailers assembled and now I'm faced with some wiring uncertainty.1. I understand that to wire panels in series you wire from one panel's positive you wire to the next panel's negative.However, when I think about wiring the two trailer arrays together to the line that goes to the controller I'm afraid that connecting the positive line from one trailer array to the second trailer array negative wire, I'll have two combined lines but neither clearly positive or negative to connect to the controller. Rough drawing attached showing my thought of possibility.2. Also, I want to be able to easily disconnect the trailers from the line to the controller and possibly only use one trailer for the bus/motor home and the other for the farm house. Also, I plan to store the solar array trailers in the barn when not in use. Can I connect, disconnect, and reconnect using M4y connectors, or is there a better way?Thanks for your ongoing patience !
-
We can review your final configuration again (solar panel Imp/Vmp, which solar charger you plan on using)... But from a quick review of an earlier post of mine, you should be wiring up 4 panels in series... Then connecting those two strings (trailers) in paralle.
I suggested that each trailer have its own run of 100 Feet of 10 AWG cable connected in parallel at the MPPT solar charge controller's MPPT input. That was to reduce voltage drop. If you combined the two parallel strings "at the trailers", then you would have a goodly amount of voltage drop on the single run of 10 AWG cable pairs for 100 feet... The system would still work--Just more loses.
Your drawing above has the two trailers connected in effectively a short circuit with each other. Like connecting two 12 volt batteries + to - and - to plus...
What you should be doing is connecting trailer A + to trailer B+, and trailer A - to trailer B- in parallel. Just like connecting two 100 AH 12 volt batteries in parallel for a 200 AH @ 12 volt battery bank.
You could electrically connect the two trailers in parallel for 8 series panels.. But that is too high of voltage for your MPPT controller (Voc-array-cold) and would ruin it.
I may be wrong--You have had a lot of questions... If you wish, let me know which MPPT solar charge controller you want to do for the solar array and what Vmp/Imp solar panel ratings are to conform.
One other thing to remember (if I did not type this warning before)... Always make the +/- connections from MPPT controller to the battery bank first, then make the solar array +/- second.
And disconnect the solar array to the MPPT charge controller first, then the battery bank last.
If you connect the solar array (under sunlight) first, then the battery bank second--You can ruin the solar charge controller, and/or possible "confuse" the charge controller during boot. The controllers are designed to boot from the battery bank first (start the microprocessor) and for the controller to measure battery bank voltage to auto configure for 12/24/48 volt battery bus. If powered by the solar array first, the controller will not boot correctly (no battery bank voltage) and could damage itself with solar power and no battery bank connection.
-BillNear San Francisco California: 3.5kWatt Grid Tied Solar power system+small backup genset -
After getting my confirmation of the "short Circuit I deleted the first drawing and replaced it with what I first thought made more sense.Now I have to see if the watts and volts add right.
-
96 volts would be your "nominal" voltage. Now you need to get the Vmp and Isc. voltages from the data label on the back of one of your panels.
2.1 Kw Suntech 175 mono, Classic 200, Trace SW 4024 ( 15 years old but brand new out of sealed factory box Jan. 2015), Bogart Tri-metric, 460 Ah. 24 volt LiFePo4 battery bank. Plenty of Baja Sea of Cortez sunshine.
-
Thanks.
At least I guess I'm in the "ball park" and I have the right concept.
-
What brand/model of MPPT solar charge controller did you use? Is it only connected to the "trailer" arrays or are you sharing one cotnroller with an existing array?
What is the Voc/Isc/Vmp/Imp of your trailer panels?
I know I can go look up our past posts... But I need to make sure that I know what you are using now--For sure. Also it keeps our discussion "clean" without all of the back and forth on earlier posts.
We need to get this correct. I believe that 8 series panels is too high of voltage for your charge controller's Vpanel input voltage.
And "12 volt" solar panels are not really "12 volts"... They have a Vmp and Voc which are higher voltages.
These not "12 volt panels" for example... They are (guessing) Vmp~18 volts (or 17.5 votls) panels (standard test conditions). And guess that Voc~21.5 volts (Standard test conditions):- 4 * 18 volts Vmp (in series) = 72 Volts Vmp array (for one trailer)....
- 4 * 21.5 volts Vmp (in series) = 86 volts Vmp-array (for one trailer)
That is why we broke the 8 panels into 4 series * 2 parallel cables to both work with your proposed charge controller and the mechanical mounting of 4 panels per trailer.
Also, referring to my post #4 above, if you use a single pair of 10 AWG cables for the 100 foot run from trailers to charge controller, you will lose around:If you run 1x pair of 10 AWG @19.44 amps (two trailers in parallel on 1x 10 AWG cable run):6.42% of your trailer(s) array(s) output power using just one pair of 10 AWG cables... If you use two pair, you would lose 1/2 that amount of power...
https://www.calculator.net/voltage-drop-calculator.html?necmaterial=copper&necwiresize=2&necconduit=pvc&necpf=0.99&material=copper&wiresize=0.4066&resistance=1.2&resistanceunit=okm&voltage=72&phase=dc&noofconductor=1&distance=100&distanceunit=feet&eres=19.44&x=0&y=0&ctype=necResult
Voltage drop: 4.62
Will a single run work? You will have 2x the losses because 1/2 the amount of copper... or ~34 Watts per trailer at "high noon" and full current/power draw... Or 64 Watts loss, or as a "solar panel"
Voltage drop percentage: 6.42%
Voltage at the end: 67.38- 64 Watts loss * 1/0.77 panel+controller losses = 83 Watts of solar panel "losses"
If you paid a $1 per Watt for your panels, then you are "losing" ~$41.50 "worth" of solar panel power vs $xx.xx worth of 200 feet of 10 AWG cable... (note that is 100 feet run of a pair or 2 pair of cables--i.e., 200 feet vs 400 feet of 10 AWG cable in this example).
A huge loss--No. The system will still be functional. Just less harvest...
-BillNear San Francisco California: 3.5kWatt Grid Tied Solar power system+small backup genset -
Please recommend the cable connectors I should use in this wiring diagram.Also, I want to be able to easily disconnect the trailers from the line to the controller and possibly only use one trailer for the bus/motor home and the other for the farm house. Also, I plan to store the solar array trailers in the barn when not in use. Can I connect, disconnect, and reconnect using M4y connectors, or is there a better way?TellGRBill
-
I was afraid you were going to ask how to plug in the trailers to your solar wiring run back to the controller... This is a messy situation. Because you are paralleling two trailers together you have a shock hazard where one trailer plugged in and powers the wiring, and the second trailer now has 80 VDC on both its side of the connection (typically a socket protected against shock) and the typical bladed plug from the wiring back to the controller...
You could use MC4 connectors to attach the solar panels on trailers to your cable run back to the solar charge controller:
https://www.solar-electric.com/learning-center/how-to-use-mc4-connectors-cables.html/
The issue I worry about is that 1) MC4 connectors do not have a high mating life... Something like 50-100x (?) as I recall. They really are designed to be installed "once" with the panels and left connected.
Another issue--Make sure you have the solar power shut off to (switch breaker before charge controller) or connect/disconnect "at night" (or cover the solar panels with tarps). The MC4 connectors will be damaged if unplugged under load (they will arc and damage the contact surfaces).
The nice thing about MC4 connectors (you are supposed to use tools to unlock the connectors) is that they are relatively shielded against shock--No exposed/energize metal for somebody to touch (roughly 20 volts * 4 panels = 80 VDC which is "dangerous" per code). One could argue that 50 cycle "life" of mating/unmating--That is 50 years of hauling trailers once a year and returning back to shed when done for season... Longer than "I" need to worry about....
You can use simple 120/240 VAC twist lock connectors but you have the choice to install the "socket end" on the solar array (no exposed blades to shock somebody)--But run into the issue that with two trailers in parallel--If you have one trailer connected, then the parallel bladed connector is now energized from the first trailer while the the female side is energized by the second trailer (I hope this all makes sense). It is like making a "suicide" plug for AC power... For example attaching two bladed plugs on an extension cord--Can be used to connect power from from a genset to the home wiring (bladed plug into genset, and bladed plug into home wiring with the main breaker turned off).
An "interesting" solution are Anderson Powerpole connectors. they are available in multiple colors (red/black/green/etc.) and are "stackable"--You can make (for example) a three cable plug (red+black+green) polarized and they are "shrouded connectors" so they don't have exposed "blades".
https://www.andersonpower.com/us/en/shop/wire-to-wire.html?amperage_range=13&color=108,110,107&stackable=57&wire_size=41
Or you could use a pair of Twist (Turn?) Lock connectors from the hardware store... Attach the female sockets to the trailers and the male bladed plugs to the fixed run back to the charge controller/battery shed. Just choose a twist lock that you don't have on your place for 120/240 power cords/tools at your place (twist locks are defined for voltage/current/etc. so they cannot be plugged into to the "wrong" circuit).
What ever you do, installing the plugs/sockets in a weather proof enclosure at the trailers (i.e., buried cable from controller to enclosure(s) next to trailer(s) so you can lockup/protect against weather and anyone (kids, etc.) from unplugging cables and getting shocked. And sockets (vs bladed connectors) at the trailers makes most sense (so trailers don't shock anyone).
Technically, you need to ground the solar panel frames and trailers to protect against lightning strikes (if common for you) and prevent electrocution too (i.e., tie ground to local ground rod, even run a ground wire connection from trailers to solar shed. This stuff is messy (trailers, over 60 Volts of power, etc.)--You need to be careful/safe.I am not there, and all of this gets a bit out of code--So I cannot tell you what to do (there are shielded connectors but they get horribly expensive). Your choices, your installation. I can talk about options, but it is very difficult (nearly impossible) to make your installation "meet code". I (and the forum) are not responsible for your choices/installation. (Yea, the disclaimers).
The question about cable runs from trailers back to the shed... A single pair or 10 AWG cables would work with relatively high losses due to resistance (6.42% losses).
If you run a pair of 10 AWG to each trailer (two pairs from shed), then you would be down to 3.21% losses... and "Y" connect at the the MPPT charge controller.
Or you could run a single pair of 6 AWG from shed to weather resistant box, then "Y" cables to each trailer in 10 AWG) and have less than 3.21% Loss (two pair of 10 AWG cables are the same resistance as one pair of 7 AWG cable--But "odd" size AWG cable is usually custom ordered).
The question of 4 panels in series vs 8 panels in series... For what you want to do, 4 series * 2 parallel for the two trailers is "optimum" for your needs. 8x series panels are too high of voltage for your 150 Volt MPPT solar charge controller.
-BillNear San Francisco California: 3.5kWatt Grid Tied Solar power system+small backup genset -
BillThank you for the link to the MC4 connectors. I'm wondering if the drawing of my trailer system has calculated the output voltage going to the controller at 96 volts when connecting the two trailer arrays in parallel is incorrect and should be 48 volts ?Also, the example of the Anderson connectors in outside use looks like they would not be weather proof.You mentioned having female plugs at the trailer. I plan to use a outlet fixture that has a male connection at the trailer but has a heavy duty flap that closes when disconnected. Then I can use a female connector on the run from the trailers to the controller, so there is never uncovered, energized blades. The connectors are twist lock with a cover on the female end when connected into the socket.I just changed to drawing voltage results. Are to volts, watts, amps closer to correct now ?
-
Regarding 48 volt vs XX volts on drawing: Roughly, the voltage from each trailer 4s * 1p array will range from zero VDC (dark) to 58 VDC (Vmp-array-hot) to 115 VDC (Voc-array-arctic temperatures) (just worst case rules of thumb, can calculate the more exact numbers for your location) based on solar panels.
The voltage for the MPPT controller's Vpanel-input will range from zero VDC (no sun) to 15 VDC (for 12 volt battery bank and 1x of your panels) to 150 VDC (Vpanel-max)...
Solar panels are not "batteries" (voltage based source i.e., a 12 volt battery runs from 10.5 VDC Dead to 15-16 VDC charging).
They are current sources (i.e., output ~5 amps from Zero to Vmp in full sun--just to pick random numbers). What meaning do you want the drawing voltage labeling to convey?
Using 48 VDC is a shorthand that does not help "me" as an "engineer" properly design/configure your system. For UL/NRTL/etc... There is a "critical voltage" of 60 Volts--At/above which is considered a hazardous voltage which must be behind "locked" (key or tool) door to prevent unauthorized access.
The confusion also arose because (as I understand your system/requirements) there should be 4s * 2p array(s). If you call these "12 volt panels" then 4x12=48 volt arrays. And they are supposed to be connected in parallel for 48 volts and 2x the per array current.
When you marked 96 volts, that was calling for series connecting your two trailers or 8x "12 volt panels in series (8s * 1p) which would exceed your controllers 150 VDC max panel input voltage (8 panels * 20.6 volts Voc-std = 164 VDC Voc-std --- standard test conditions of 1,000 w/sqmeter sun @ 77F/25C panel/cell temperatures--Remembering that Voc-panel rises as temperatures fall).
If you wanted to call these 48 volt trailers connected IN PARALLEL to a 48 VDC bus back to the charge controller @ 9.72 amps per trailer--That is fine.
If you wanted to call them (4s * 18 volts Vmp) 72 VDC Vmp-array-std cables--That is fine too... Or 15-150 VDC based on charge controller requirements---That also "works".
Again, the "big flag" for me was two "48 volt trailers" connected IN SERIES producing "96 VDC" solar bus to MPPT controller. That was indicating a "wiring error" (or a misunderstanding) on what the Trailer A + Trailer B wiring was supposed to be (parallel as designed, or series which is incorrect).
Lots of words when this is really simple... For example, if you have 2x 12 volt batteries. Connecting in parallel you have a 12 volt bus with 2x the AH rating. If you connect the two batteries in series, you have 2x the voltage or 24 volts @ AH rating. That was my original concern (parallel vs series connections of trailers).
Regarding connectors: Any connections should be inside a weather proof box... Few "plugs" are weather/UV resistant (long term) and you (especially in this case because of the parallel power sources--the two solar trailers) would expose to anyone the ability to unplug and electrocute themselves.
Here is an example of industrial weather resistant connectors:
https://www.leviton.com/en/docs/Temporary_Power_Line_Card_-_Q-741G.pdf
https://www.leviton.com/en/solutions/industries/temporary-power
Vs getting a NEMA outdoor enclosure and housing your plugs inside the secure box(es):
https://www.amazon.com/nema-enclosure/s?k=nema+enclosure
-BillNear San Francisco California: 3.5kWatt Grid Tied Solar power system+small backup genset -
I just edited my system drawing. Are the output figures closer to correct now?
-
Yes, the parallel connection of the drawing is correct.
The other question is how are you going to do the 100 feet of cable... 10 AWG, one pair or two pair, one pair of 6 AWG or what?
-BillNear San Francisco California: 3.5kWatt Grid Tied Solar power system+small backup genset -
That is on my mind alot.I already have one roll of the 100' 10awg cable.And, if I want to use one solar panel trailer at the farm house and the bus at the same time, I'll need another cable, so I guess I should buy another 100' 10awg cable, set them up to be separated easily and be more ready for that eventuality. LOL Thanks Mr. advisor !But now I'll have to rethink my connection points.I did another drawing with two cables going to the controller this time.Making progress.I try to limit all my spending to just what we NEED, and not what we WANT. I know that's UNAMERICAN, but it works for us, and we have something left to share to others.Your Internet friend, and student
Categories
- All Categories
- 229 Forum & Website
- 137 Solar Forum News and Announcements
- 1.4K Solar News, Reviews, & Product Announcements
- 199 Solar Information links & sources, event announcements
- 898 Solar Product Reviews & Opinions
- 256 Solar Skeptics, Hype, & Scams Corner
- 22.5K Solar Electric Power, Wind Power & Balance of System
- 3.5K General Solar Power Topics
- 6.7K Solar Beginners Corner
- 1K PV Installers Forum - NEC, Wiring, Installation
- 2.1K Advanced Solar Electric Technical Forum
- 5.6K Off Grid Solar & Battery Systems
- 428 Caravan, Recreational Vehicle, and Marine Power Systems
- 1.1K Grid Tie and Grid Interactive Systems
- 654 Solar Water Pumping
- 816 Wind Power Generation
- 624 Energy Use & Conservation
- 619 Discussion Forums/Café
- 312 In the Weeds--Member's Choice
- 75 Construction
- 124 New Battery Technologies
- 108 Old Battery Tech Discussions
- 3.8K Solar News - Automatic Feed
- 3.8K Solar Energy News RSS Feed