Question on shunt
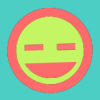
Gregaba
Registered Users Posts: 34 ✭✭
I just received 4 more 100 watt 12V panels. All so got a new renogy shunt.
I have 2 CC's and want to know if I should hook it up to the 40 amp or the 100 amp CC.
The 40 amp will be hooked up in parallel and the 100 amp will be in series.
Thanks
Greg
Comments
-
The Renogy Shunt should have come with its own LCD Display/Controller.
https://www.renogy.com/500a-battery-monitor-with-shunt/
The shunt connects directly to the battery negative (-) terminal... The other side of the shunt is where your charge controller(s), DC loads, DC input to AC inverter, etc. are connected:
You you can see, the Positive Bus Bar and Negative Bus bar are where all of the rest of the DC electrical connections. There is no specific connection between the Shunt+LCD display and either charge controller.
Not sure what you mean with "The 40 amp will be hooked up in parallel and the 100 amp will be in series."
If you are talking about solar panels in series and/or parallel... Need to know exactly what charge controllers, what solar panel Vmp/Imp ratings, and battery bank voltage (12/24/48 volts).
Details do matter here.
-Bill
Near San Francisco California: 3.5kWatt Grid Tied Solar power system+small backup genset -
Thank's BillI don't have any bus bar's yet but they should be in on Thursday. The bad thing about being new to something is you don't really know what you need.The picture you posted is a lot better then the little one they send with the shunt.Some time's I get in a hurry and don't explain my question's right.The 40 amp CC [Renogy] will be connected to the panel's [400 Watt's total] connected in parallel and the 100 amp CC [Epever10115AN] will be connected in series[400 watt's total].The spec's on the panel's areocv-24.3Vscc-5.21A600 VOOV-20.4OC-4.91AI wanted to know if there was any difference in which charge controller I hooked the shunt to since I don't have any bus bars yet or if Ishould just wait until the bus bar's come in?ThanksGreg
-
The "Bus Bars" can be just a long bolt and nut with a bunch of terminal ends bolted together--A flattened copper water pipe with bolt holes, etc... Nothing special about Bus Bars other than a handy single place to connect the wiring (and fuses/circuit breakers to protect + wiring to loads).
The diagrams show that there is no difference how many sources and loads you have for the "shunt" connection. Just connect B- to Battery negative, and P- to All Other Loads/Sources so that the shunt measures all current into/out of the battery. If you were to connect a load/source between B- and Battery-, that current flow would be "invisible" to the shunt. Which then prevents the shunt+display for accurately displaying the battery current flow/state of charge/etc.
I cannot really help you with the panel/array wiring without knowing exactly which solar charge controller(s) you have. PWM controllers (simple, cheap) require Vmp-array to "match" battery bank voltage (i.e., Vmp-array ~ 18 volts charging a 12 volt battery bank or Vmp-array = 2x 18 Vbatt-charge = 36 corrected BB volts Vmp-array-std minimum/optimal).
MPPT controllers (more sophisticated/expensive are much more flexible. More or less, you can connect Vmp-array~18 volts to a Vbatt of 12 volts... But ideally, the Vmp-array should be ~2x the battery bank charging voltage--2x 15 volt battery charging = 30 volts minimum/optimum for Vmp-array...
And for MPPT, there is a Vpanel-max input voltage... These can run from 80 to 100 to 150 to 400+ volts... Although for most MPPT controllers Vmp-array = 2x battery charging voltage is "most efficient" for MPPT controller. There are other reasons to have Vmp-array >> 2x Vbatt-charging. Basically P=V*I, double the voltage, 1/2 the current, and 1/2 the voltage drop... If you have more than 10-20 feet or so between Array and charge controller, then having high Vmp-array lets you use much smaller AWG copper cable--And you can save lots of money by using less copper for the wire run.
Details matter here... Most controller manuals are pretty clear about Array Wiring options.
You also need to worry about cold weather. Voc (voltage open circuit and Vmp voltage maximum power point) rise in cold weather. If you ar in a subfreezing/bitter cold area, a 150 Amp charge controller should be connected to a Vmp-array that 0.7x Vpanel-max (150 Vmax * 0.7 = ~105 Vmp-std array--Pretty much "worst case cold weather design estimate).
You where around Oklahoma (?) so not in bitter cold, but do be careful not to have too high of Voc-array-cold does not over-voltage the charge controller.
Details matter here. Do paper designs... And follow each design/validation step.
-BillNear San Francisco California: 3.5kWatt Grid Tied Solar power system+small backup genset -
Thanks Bill,as usual I will have to read this a few times to get a full understanding.Greg
-
Received my battery monitor-shunt yesterday and installed.I set it for 400AH and decided to see what it did.I ran my 2 led light's [40 watt each] last night [9 hour's]and read the monitor this morning before the sun hit my panels'It read 12.7 volts and showed 100% charge so I guess it is fixed. Looks look's you can't go by the app's that come with these.Thanks for all the help.Greg
Categories
- All Categories
- 229 Forum & Website
- 137 Solar Forum News and Announcements
- 1.4K Solar News, Reviews, & Product Announcements
- 199 Solar Information links & sources, event announcements
- 898 Solar Product Reviews & Opinions
- 256 Solar Skeptics, Hype, & Scams Corner
- 22.5K Solar Electric Power, Wind Power & Balance of System
- 3.5K General Solar Power Topics
- 6.7K Solar Beginners Corner
- 1K PV Installers Forum - NEC, Wiring, Installation
- 2.1K Advanced Solar Electric Technical Forum
- 5.6K Off Grid Solar & Battery Systems
- 428 Caravan, Recreational Vehicle, and Marine Power Systems
- 1.1K Grid Tie and Grid Interactive Systems
- 654 Solar Water Pumping
- 816 Wind Power Generation
- 624 Energy Use & Conservation
- 619 Discussion Forums/Café
- 312 In the Weeds--Member's Choice
- 75 Construction
- 124 New Battery Technologies
- 108 Old Battery Tech Discussions
- 3.8K Solar News - Automatic Feed
- 3.8K Solar Energy News RSS Feed