Victron Smart Solar MPPT 100/50 and Proper awg
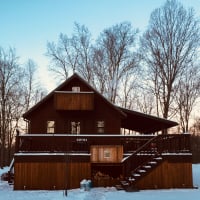
Say you have a 480 Watt PV Array connected to a Victron MPPT 100/50 with the following specs:
PV Array-
53.7 vmp max
60.69 voc max
8.96 imp max
9.36 isc max
Connected to MPPT 100/50 with MC4 4mm^2 wiring
MPPT CC-
Nominal PV 700W
Max PV voc 100V
Max PV isc 60A
Rated Charge Current: 50A
12V Battery Bank
Regarding the wiring coming from CC to the battery bank, is it safe to assume that the CC is never going to be putting out 50A of charge current since the max potential output of the array is only 60V and under 10 amps?
I'm trying to size the output wires from CC to battery appropriately to ensure they can handle the potential amperage.
Thanks for your time

Comments
-
Solar power is "variable"... Many times you have less than full rated array power (i.e., I usually use a 77% derating on the "marketing" numbers for solar panels). Vmp-panel and Vmp-array is temperature sensitive (higher panel/cell temperature, lower Vmp voltage).
HOWEVER, it is possible for you to get more energy... Freezing winter weather, "edge of cloud focusing of sunlight", reflections from snow/sand/water) and such can give you 100% (or even more) of panel power rating.
Remember for MPPT (maximum power point tracking) solar charge controllers, their output power is Power=Voltage*Current... So if you have higher voltage (cold weather) or higher current (more sun on panels), you can get more power into the controller, and output to the batteries.
The NEC basically suggests that use 1.25x safety factor for solar power to account for these variations. For example if your panels are rated for 9.36 Amps Isc, then the wiring should be 1.25x higher rated or >11.7 amps... If you look at the spec sheet for your panels, you should see a "series fuse rating" (for paralleling 3 or more strings of panels)... Probably 15 amps in this case (and you should use wiring rated for 15 amps or greater for the array wiring).
For DC output to a battery bank... the two major types of charge controllers have different behaviors... PWM type (pulse wave modulation) simply pass the current from the array to the battery bank (Imp at that moment). A PWM controller has no ability to limit its output current--What comes from the panels is passed to the battery bank (PWM is "on/off/on/off..." control).
MPPT type controllers do have the ability to "control/limit" their output current to the rating of the controller... A 50 Amp controller should never output more than 50 Amps to the battery bank. Even if your array is capable of more power...
In North America, our NEC wiring and breakers (and fuses) are rated for 100% current, but really only for surges (such as motor starting). The breakers are rated to "never trip" at 80% or less of rating. And will trip at 100% or more of rated current (may take minutes or hours at 100% of rated current).
For battery charging, it is very possible if your battery bank is discharged (50% of capacity or less) to charge at "full current" for hours at a time... So I suggest to use the NEC derating for "continuous current circuits" (such as gym lights that are on for 12+ hours per day)... For your 50 Amp controller that would be:- 50 amps * 1.25 NEC derating = 62.5 amps minimum branch circuit wiring and breaker/fuse rating
That will help prevent "false trips" during cool/clear/sunny days with a discharged battery bank... Because MPPT controllers operate differently than PWM, their output current and power drawn from solar array is also dependent on battery voltage... Comparing a battery charging at 14.75 volts (80% charged, no loads) vs a discharged battery bank with loads at 11.5 volts:- 50 amps * 14.75 volt battery charging = 737.5 Watts from array
- 50 amps * 11.50 volt battery charging = 575 Watts from array
- 480 Watts / 11.5 volts charging = 41.7 amps
- 41.7 amps * 1.25 NEC solar/continuous derrating = 52 amps rated wring/breaker/branch circuit for 480 Watt array
So it is "safe" to assume for a 50 amp MPPT controller its output is limited to 50 amps--But I would suggest wiring for 1.25x more current for long term reliability and avoiding "false trips" down the road (or if you ever add more panels)....
Using the NEC ampacity chart for solar wiring is relaively conservative (marine wiring charts are a bit more "optimistic"):
https://lugsdirect.com/WireCurrentAmpacitiesNEC-Table-301-16.htm
-BillNear San Francisco California: 3.5kWatt Grid Tied Solar power system+small backup genset -
Thank you Bill for the great information as always. Exactly what I was looking for.
I will plan for either 4awg or 6awg from controller to batteries. I would also plan for a MRBF Terminal Fuse Block with a 60A fuse on the positive (+) battery post. (or appropriate fuse size depending on which awg)
Couple more questions if you don't mind:
1.) Would you say I'm still good with the 4mm^2 (12awg) wires from the PV array to the CC? These are the same gauge wires that connect the panels together in their Series-Parallel config. They should be good for 20Amps depending on some other factors, correct?
9.36 isc (A) * 1.25 NEC solar/continuous deratings = 11.7 A
8.96 imp(A) * 1.25 NEC solar/continuous deratings = 11.2 A
2.) How do you feel about doubling up wires to achieve a larger gauge and amp capacity (ie two 8awg wires = effective gauge: 5awg). Is this a good idea or would you avoid this for any particular reason/reasons? Specifically on the runs between the batteries and CC. (I'll also add: this is considering you already have multiple quantities of smaller awg, so not looking at it from a cost perspective)
3.) How do you feel about using Aluminum/copper clad conductors for connections between battery and CC and/or between batteries and inverter? I see there are separate ratings on the NEC chart for copper clad which looks to be slightly less amperage capacities than their equivalent AWG in copper. Pros/Cons?
Thanks again
-
Remember that current is one limiting factor regarding wire AWG (and different temperature ratings, conduit fill, ambient temperatures, etc.)... Another is voltage drop... Ideally, suggest around 0.05 to 0.10 volt drop from charge controller to a 12 volt battery bank for fastest/most accurate battery charging.
You generally want a short run from charge controller to battery bank. You can use a voltage drop calculator to do some quick calculations.
Just for example, say you 6 AWG, 50 amps, 7 foot wire run:
https://www.calculator.net/voltage-drop-calculator.html?necmaterial=copper&necwiresize=4&necconduit=pvc&necpf=0.99&material=copper&wiresize=0.4066&resistance=1.2&resistanceunit=okm&voltage=14.75&phase=dc&noofconductor=1&distance=7&distanceunit=feet&eres=50&x=43&y=16&ctype=necResult
Voltage drop: 0.34
You can see that even with heavy cable, adding distance makes voltage drop pretty high... You need 1/3rd the length or 3x heavier cable to get down into the 0.10 volt drop range.
Voltage drop percentage: 2.33%
Voltage at the end: 14.41
Voltage drop is a real pain for 12 volt systems when you are taking about higher current/power levels. And why for larger systems, suggest 24 or 48 volt battery buses.
Same issue with solar array wiring... Having the correct wire AWG and UV resistant insulation is one part... Voltage drop is another question.
You have a 12 volt battery bus and a 54 Volt Vmp-array-std... From a functional point of view, as long as your voltage to the MPPT controller is, at least, ~2x the battery charging voltage (15 volts * 2 = 30 volt minimum "optimal" array Vmp voltage)--That is fine.
The other is simply losses due to voltage drop... Suggest that use 1% to 3% as a good aim point (less than 1% is simply a lot of money spent on copper)... And over 3% is getting to be more losses...
Say 20 amps Imp-array, 12 AWG cable, and 50 feet of wire run (this calculator uses "one way" cable run distance), 54 volt Vmp.
https://www.calculator.net/voltage-drop-calculator.html?necmaterial=copper&necwiresize=1&necconduit=pvc&necpf=0.99&material=copper&wiresize=0.4066&resistance=1.2&resistanceunit=okm&voltage=54&phase=dc&noofconductor=1&distance=50&distanceunit=feet&eres=20&x=0&y=0&ctype=necResult
Voltage drop: 4.02
In this example, the MPPT controller will run fine with 7.45% loss (~49.98 volts at MPPT input)... Only you can decide if 7.45% (vs 1-3% suggested losses) is a "killer" for you or not...
Voltage drop percentage: 7.45%
Voltage at the end: 49.98- 4.02 volts * 20 amps = 80 Watts of array wiring losses (in this example)
Regarding doubling (paralleling) cable runs... NEC code only "allows" for larger AWG cables (I forget what, but possible 4 AWG paralleled?).
Correction/update... 1/0 AWG Cable is NEC minimum AWG per NEC Code (see post #10 below for details--Updated 2/27/2023. -BB):
https://www.electricallicenserenewal.com/Electrical-Continuing-Education-Courses/NEC-Content.php?sectionID=297.0
Cost wise, copper cable is "mostly" the cost of the copper itself. So that 1x 5 AWG cable cost the same amount as 2x 8 AWG cables in parallel)--Assuming you can find 5 AWG (odd gauge) cable.
The issue is that a failed paralleled connection (loose, dirty, corroded, etc.) is not obvious (a broken single wire connection, current stops).
Paralleling power cables is pretty common in the computer industry--Lots of higher current, lower voltage wiring, and small spaces. I have had to repair quite a few pieces of equipment where paralleling 3-5 or more cables for current to a daughter board because of burned/baked/browned connections...
My theory--Interestingly enough, it is not the "dirty/corroded" connections that "brown/overheat". It is the really good connections that do because they are low resistance and carry most of the current. And remember that electrical heating goes with the "square" of the current:- Power = Current^2 * Resistance
Or, if one wire connection carries 2x more current (because of lower resistance), then it heats 2^2 = 4x more... So the "connectors" tend to "unzip" as they fail (one overheats, then the next lowest resistance connection over currents and overheats and fails, etc.).
From a safety point of view for solar... If you have 1x 12 AWG run with 20 amps... That is safe, but you may have too much voltage drop--So you run 2x 12 AWG (cable on hand) to get from 7% to 3.5% drop and save 40 watts of losses... And that is OK. Even if one connection fails, the remaining cable is still able to carry the full current.
There is another "saving grace" with long wire runs... Remember I said that it was the low resistance path that tended to fail first. In short cable runs, it is usually the connector that is "high or low" resistance. With long cable runs the cable's resistance itself is higher than the connection points. Technically the long cables are the "ballast" which limit current flow (or in this case) help ensure that each parallel cable run carries its share of current. And you don't have (for example) overheating of one or more "low resistance" connections.
Copper Clad Aluminum cable... Good or Bad? Aluminum wiring (from 1965-1972) was a bad idea/implementation:
https://homeinspectioninsider.com/aluminum-wiring/
More or less, Aluminum is softer and oxidizes quickly on its surface. "Standard" bonding screws/etc. used in house wiring did not safely "seal" the electrical connection to aluminum. Add thermal cycling, the aluminum would expand, extrude from under the "screw", cool, shrink, expose more surface to air for corrosion, repeat....
Properly made Aluminum connections are fine (used in larger power systems, drops from pole transformers, etc.) using crimp connections with anti-corrosion grease, etc....
Copper Clad aluminum wiring is supposed to be safer (when used with COALR or CU-AL rated connections). The downside is that aluminum is less flexible and more prone to work hardening/cracking if subjected to bending.
https://inspectapedia.com/aluminum/Copper_Clad_Aluminum_Wire.phpMr. D'Agostino relates that in 1971 as project engineer at UL, he conducted tests evaluating the performance of copper-clad aluminum conductor wiring using a number of types of copper-only receptacles (i.e. binding head screw terminals, back-wired push-in terminals, sid-wired pressure plate screw terminals) and a number of types of AL-CU pressure wire connectors.
That research, conducted under the auspices of U.L., demonstrated that performance of copper-clad wire was:
- similar to that of solid copper-only wiring devices (with binding head screw terminals
- satisfactory for use in AL-CU pressure wire connectors and
- along with copper wire performed poorly, less than adequate in "back-wired push-in" wiring devices.
-BillNear San Francisco California: 3.5kWatt Grid Tied Solar power system+small backup genset -
Bill,
Looking back at your response I see you already answered question #1 about the wiring from panel array to CC so ignore question#1.
Digging deeper in my quest to ensure adequate wiring from CC to Battery Bank I've come across another conundrum....
According to the Victron manual for my CC there is a section that discusses wiring safety precautions and has some specifics about types and diameter of individual strands etc.. (see screenshot below)
Which in turn makes me realize that the wiring I have (specifically 6 awg) I believe was from Home Depot will not meet this requirement laid out in the CC manual. I'm assuming they are referring more to a fine stranded cable similar to welding cables or even the MC4 solar panel cables I've used on the PV end of things? Below are the specs on the stranded 6awg I have.
I've seen some affordable cables on places like amazon that "claim" to be 6awg, but not sure if they are to be trusted.
Amazon.com: 6 Gauge 6 AWG 20 Feet Black + 20 Feet Red Welding Battery Pure Copper Flexible Cable Wire - Car, Inverter, RV, Solar : Tools & Home Improvement
Appreciate your thoughts and expertise!
-
Solid vs coarse vs fine stranded cables... Below is just my personal understanding of the issues. I am not an expert in this area. And when dealing with UL/NRTL "Listed" components--There is a whole bunch of paperwork that back this stuff up... Some public, some "private" to the manufacturer/UL (that was frustrating too when trying to get answers for new system designs).
Following the manufacturer's instructions (such as Victron in this case)--Is always the place to start. Where you get into "trouble" is Victron's charge controller may be designed for fire stranded wire--But you need to find hardware on the other end (breakers, fuse holders, bus bars, etc.) that are also designed to mate correctly to the fine wire cables too.
And you cannot try home brew solutions--Such as using solder to make a "solid" pig tail"--As this causes other reliability issues.
Fine stranded cables were originally used for welding cables, locomotive cables, and such places where a high amount of flexing was expected... But, originally, the "welding cables" were not UL/NRTL rated.
The newer cables are MTW Listed (Machine Tool Wire) rated--So have "known UL" properties.
Stranding makes the wire easier to bend (pull through conduit, etc.)--Smaller AWG tend to be solid, and larger AWG tend to be coarse stranded.
And the wire "binding points" for "house" wiring tend to be designed for solid and/or coarse stranded wiring.
Fine stranded wiring has some issues. One is that it is larger in diameter (more "air gaps between strands) vs solid/coarse cable... So if using "crimp" connections, you need to ensure that they will be large enough for fine strand able, and crimp down solidly.
The "house wiring", bus bars, and many devices are not designed for fine stranded able... From what I have seen (no expert), may "house type" devices (breakers, etc.) just use a binding screw directly on the wire. Solid and coarse cables work well. Fine stranded cables tend to "squirm" out from under standard binding screws.
I am guessing that electrical connections designed for "fine cables" have a "shoe" or other arrangement that holds the strands together while force is applied to the cable end.
Example of connections where I would only use solid or coarse stranded cables.
Example of using a ferral to "control/capture" fine stranded cable:
Example of termination rated for fine cables (I would guess because binding screw is the diameter of the wire hole--Vs smaller than example above for non-fine stranded cable):
https://lugsdirect.com/advancementinternational.com/
Example of a "shoe or saddle" that holds the strands captive:
-BillNear San Francisco California: 3.5kWatt Grid Tied Solar power system+small backup genset -
BB and Team.I’ve had excellent results using these NSI sleeves when terminating fine stranded cable. The sleeves hold all of the strands together and they get crushed into a good connection. They are made of tin plated copper.Off-Grid in Terlingua, TX
5,000 watt array - 14 CS 370 watt modules. HZLA horizontal tracker. Schneider: XW6048NA+, Mini PDP, MPPT 80-600, SCP. 390ah LiFeP04 battery bank - 3 Discover AES 42-48-6650 48 volt 130ah LiFePO4 batteries -
Thanks for the great information. I really appreciate it.
-
Hello,
I wanted to see what your thoughts are on my proposed installation of wiring.
Distance from batteries to inverter location is roughly 10ft.(not ideal I know) To keep the voltage loss down I've used 1/0awg cable for the connections between batteries and for the 10 ft length from batteries to inverter location.
85Amps (max) at 12VDC with 1/0AWG at 10ft = 0.20 voltage drop (1.68%)
Additionally, the distance from batteries to CC location is also roughly 10ft. For this I've used #2awg
50Amps (max) at 14.5VDC with 2AWG at 10ft = 0.19 voltage drop (1.30%)
However, the inverter only accepts up to #4awg on the device terminals and the charge controller only accepts up to #6awg on the device terminals.
I first tried some 1/0awg to 4awg reducers commonly used in audio amplifiers, but the terminals were way too close for comfort on the inverter to allow such big reducers and I just didn't like that idea. I messed around with some ferrules as well, but ultimately didn't feel comfortable reducing the gauge so drastically at the terminal connection points.
Is there any cause for concern doing the following?
Bringing the cable runs from the batteries to some positive and negative distribution blocks. Then from the blocks run the shorter distance with the smaller awg to the inverter and the CC.
Also, I would size the fuses to be rated for the smaller awg runs regardless of the larger awg runs ampacity.
This way I can ensure proper ferrule connections at the devices and use adequate terminal lugs at the distribution blocks.
Examples:
1/0awg with 100A fuse between batteries and distribution block (to minimize voltage drop) and 100A fuse on the #4awg short run between distribution block and Inverter.
#2awg with 60A fuse between batteries and distribution block, and a 60A fuse on the #6awg short run between distribution block and inverter.
See simplified schematic below. Note this doesn't show my disconnect switches or any of the fuses. Just for visual purposes.
Thanks for your time.
-
To correct an earlier post of mine regarding paralleling cable and NEC:
https://www.electricallicenserenewal.com/Electrical-Continuing-Education-Courses/NEC-Content.php?sectionID=297.0In the 2017 NEC, parallel conductors inside an auxiliary gutter must be grouped together to prevent current imbalance in the paralleled conductors due to inductive reactance.I don't see any issue with your plans... Other than the battery bank connections. Ideally, you want (for example) top left terminal and top right for both Charge controller and AC Inverter connections. (i.e., connect the inverter to the same terminals as the charge controller in your above drawing).Code Change Summary: A new code section provides requirements for parallel conductors in an auxiliary gutter.
Parallel conductor installations are covered in NEC 310.10(H) and are permitted for each phase, polarity, neutral, or grounded conductor in sizes 1/0 AWG and larger. Joining conductors in parallel is like having two or more smaller conductors connected at each end to make one larger conductor. This is often done to make wire pulling easier.
In order to install conductors in parallel, the paralleled conductors in each phase, polarity, neutral, grounded circuit conductor, equipment grounding conductor, or equipment bonding jumper must comply with all of the following:
(1) Be the same length.
(2) Consist of the same conductor material.
(3) Be the same size in circular mil area.
(4) Have the same insulation type.
(5) Be terminated in the same manner.
The above rules ensure that each set of parallel conductors carries the same ampacity. Where run in separate cables or raceways, the cables or raceways must have the same number of conductors and must have the same “electrical characteristics”.
In your diagram, the AC inverter will be connecting to Zero Volts (the +/- inverter cables are all connected to the "solid" series connection cable between the 4 batteries.
Just to review, "optimum" series connections of batteries:
http://www.smartgauge.co.uk/batt_con.html
-BillNear San Francisco California: 3.5kWatt Grid Tied Solar power system+small backup genset -
Thanks Bill for all of your help. That makes perfect sense. I also mislabeled the schematic and had the inverter and CC swapped in relation to their wire sizes. I'll let you know if I run into any more questions along the way. Thanks again
Categories
- All Categories
- 229 Forum & Website
- 137 Solar Forum News and Announcements
- 1.4K Solar News, Reviews, & Product Announcements
- 199 Solar Information links & sources, event announcements
- 898 Solar Product Reviews & Opinions
- 256 Solar Skeptics, Hype, & Scams Corner
- 22.5K Solar Electric Power, Wind Power & Balance of System
- 3.5K General Solar Power Topics
- 6.7K Solar Beginners Corner
- 1K PV Installers Forum - NEC, Wiring, Installation
- 2.1K Advanced Solar Electric Technical Forum
- 5.6K Off Grid Solar & Battery Systems
- 428 Caravan, Recreational Vehicle, and Marine Power Systems
- 1.1K Grid Tie and Grid Interactive Systems
- 654 Solar Water Pumping
- 816 Wind Power Generation
- 624 Energy Use & Conservation
- 619 Discussion Forums/Café
- 312 In the Weeds--Member's Choice
- 75 Construction
- 124 New Battery Technologies
- 108 Old Battery Tech Discussions
- 3.8K Solar News - Automatic Feed
- 3.8K Solar Energy News RSS Feed