3rd time the charm? final plan for cabin power

minisolar
Solar Expert Posts: 158 ✭✭
Hey all,
I have twice in the past worked hard on getting my cabin off my honda generator but life takes me other places. This time I started a new business that fortunately really took off and required my full attention.
Therefore, I wish to come up with a simpler plan than the one I had so I can really make this happen.
I measured my power consumption when I was last planning and my largest was 1.86KWh for the day.
So my thinking is to get 2x 12v 100ah lifepo4 batteries (they have ones with heating element so it protect the battery in cold weather charging) then charge it at night with generator, use it in the day so at max I will discharge them to 80% (2x12v 100ah = 2.4kwh. 1.9kwh/2.4kwh = 80% right?). I have an all in one battery charger, mppt, invertor that I bought before and will use.
I adjust my previous diagram. I think my battery wiring are now too large since my bank is smaller and I also think I am missing a breaker between batteries and all-in-one.
If anyone can chime in on those and any other thing that seems off?
btw - batteries I will get - amazon.com/dp/B08N56CYS5/
I have twice in the past worked hard on getting my cabin off my honda generator but life takes me other places. This time I started a new business that fortunately really took off and required my full attention.
Therefore, I wish to come up with a simpler plan than the one I had so I can really make this happen.
I measured my power consumption when I was last planning and my largest was 1.86KWh for the day.
So my thinking is to get 2x 12v 100ah lifepo4 batteries (they have ones with heating element so it protect the battery in cold weather charging) then charge it at night with generator, use it in the day so at max I will discharge them to 80% (2x12v 100ah = 2.4kwh. 1.9kwh/2.4kwh = 80% right?). I have an all in one battery charger, mppt, invertor that I bought before and will use.
I adjust my previous diagram. I think my battery wiring are now too large since my bank is smaller and I also think I am missing a breaker between batteries and all-in-one.
If anyone can chime in on those and any other thing that seems off?
btw - batteries I will get - amazon.com/dp/B08N56CYS5/
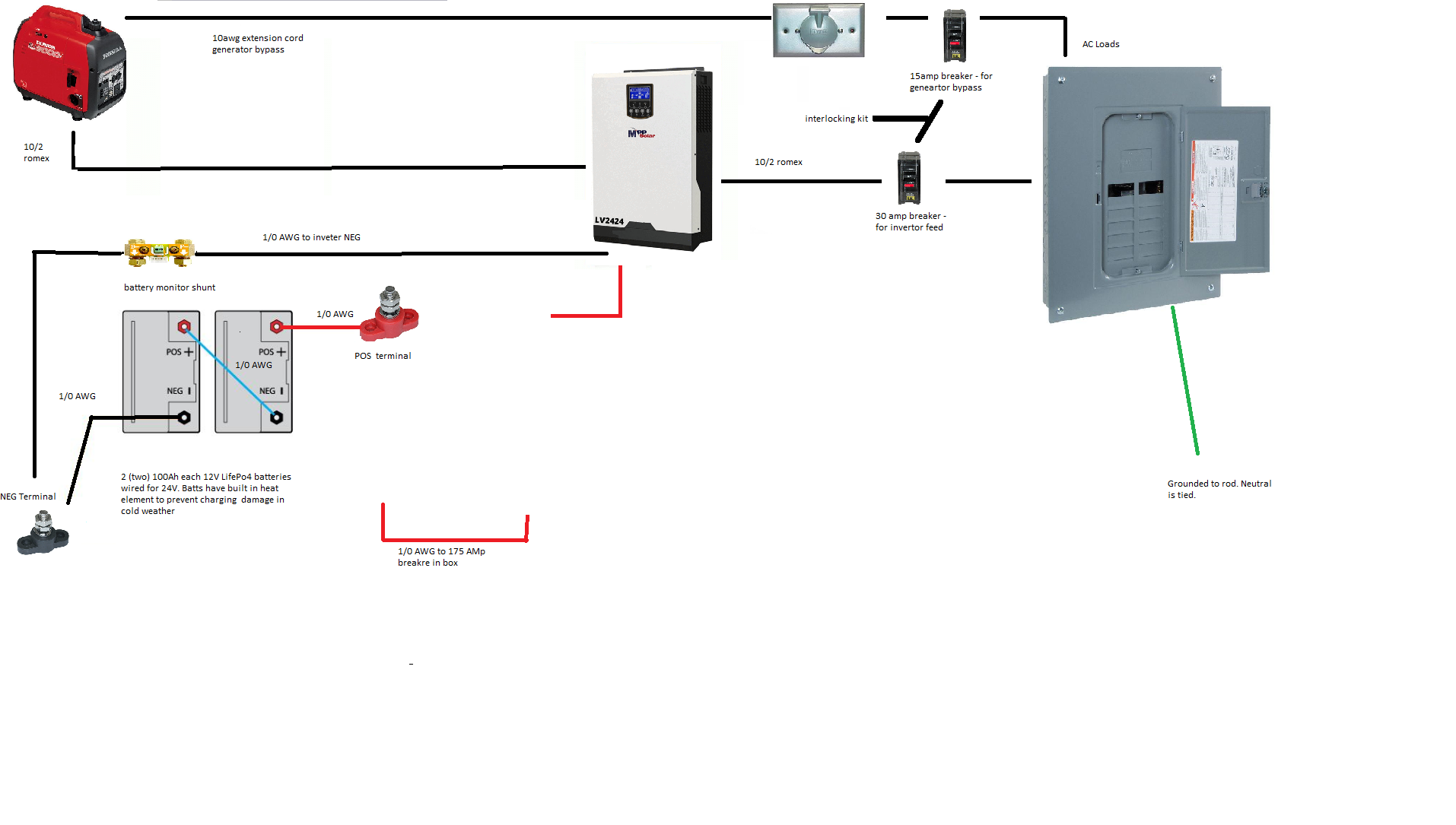
Comments
-
Mini…hoping this works out for you this time:)
I’m an amateur. One of the experts will likely chime in soon.I believe that you will need a breaker on the positive wire.Make sure that the POS and NEG cables from batt to electronics are the same length.If you already have the 1/0 wire, go ahead and use it. Otherwise BB or one of the other experts will walk you through the math to get you to the right size wire.Best of luck with your project and congrats on the new business.Off-Grid in Terlingua, TX
5,000 watt array - 14 CS 370 watt modules. HZLA horizontal tracker. Schneider: XW6048NA+, Mini PDP, MPPT 80-600, SCP. 390ah LiFeP04 battery bank - 3 Discover AES 42-48-6650 48 volt 130ah LiFePO4 batteries -
Yup exactly. breaker and wire size are perhaps the things missing. Then I need to just confirm if I am doing anything for different for grounding than what I currently have. I am in NY so no fires but still.
Then hopefully I am set. I'll order the wires and be all set -
I am not sure how much I can add... The best place to start is with the NEC (National Electric Code for much of the USA) book.
For wiring size, I like to use the NEC charts... Here is a simplified version of the ampacity rating for various wire sizes and insulation types:
https://lugsdirect.com/WireCurrentAmpacitiesNEC-Table-301-16.htm
NEC is relatively conservative (vs marine wiring specs)... And I suggest for continuous current circuits used for battery charging where you can have "hours" of rated current flow) that you derate the wiring using the NEC factor of 80% or (1/0.8= ) 1.25x. Breakers and fuses are typically rated to trip at 100%+ of rated load (minutes to hours of operation) and not trip at 80% or less of rated load... For example, if you have a 60 Amp current (AC side or DC side) for battery charging:- 60 Amp continuous current * 1.25 NEC derating = 75 Amp rated branch circuit ~ round up to 80 Amp breaker+wiring
You can certainly use heavier wire with smaller rated breakers/fuses... Frequently done to reduce voltage drop (big issue in low voltage DC wiring).
For Lithium Ion batteries--They are certainly more sensitive to running outside of specifications (too much current, to high/low of state of charge, out of temperature range, etc.)... Sizing the breaker to max continuous current (vs the AWG max current wire size) is good to protect the battery.
And more than likely the BMS of many of these types of batteries will "protect" against many of these "out of spec" issues...
However, you don't want the BMS/Breaker to be the "primary" limiting devices... BMS turning off battery current (out of spec faults) should be a "last resort"... Cutting battery bus can damage other equipment on the bus--As well as plunge the cabin into unexpected darkness...
Having well designed/controlled chargers/inverters/battery boxes to regulate tempratures/etc. that will not go out of specs during normal operation is primary.
And if you can integrate the BMS with your (typically newer chargers/inverters/etc.) that will gracefully shutdown via BMS feedback--Nice too.
You don't have grounding in the schematic... So the normal AC "green wire" grounding and Neutral+Ground bonding (if appropriate for your inverter and gensets) with ground rod. And DC grounding the negative battery bus to the same AC ground rod--Helpful for safety and lightning safety.
If you have lightning in the area--Also using Surge Protectors would be a very good idea too...
I am not really sure I answered your questions or not... Kind of started out pretty open-ended discussion.
-BillNear San Francisco California: 3.5kWatt Grid Tied Solar power system+small backup genset -
Not sure If I am doing this right but since the inverter is 2400w and my bank will be 24v then 2400/24v = 100amp.
So that is the max current I need to support? Per the chart you gave that is #1 cable for between batteries and inverter? Am I off? I looked up another chart and seems like #5 will support it? which is huge difference. Can you please tell me recommended cable gauge between batteries & between batteries and inverter?
Categories
- All Categories
- 228 Forum & Website
- 136 Solar Forum News and Announcements
- 1.4K Solar News, Reviews, & Product Announcements
- 199 Solar Information links & sources, event announcements
- 898 Solar Product Reviews & Opinions
- 256 Solar Skeptics, Hype, & Scams Corner
- 22.5K Solar Electric Power, Wind Power & Balance of System
- 3.5K General Solar Power Topics
- 6.7K Solar Beginners Corner
- 1K PV Installers Forum - NEC, Wiring, Installation
- 2.1K Advanced Solar Electric Technical Forum
- 5.6K Off Grid Solar & Battery Systems
- 428 Caravan, Recreational Vehicle, and Marine Power Systems
- 1.1K Grid Tie and Grid Interactive Systems
- 654 Solar Water Pumping
- 816 Wind Power Generation
- 624 Energy Use & Conservation
- 619 Discussion Forums/Café
- 312 In the Weeds--Member's Choice
- 75 Construction
- 124 New Battery Technologies
- 108 Old Battery Tech Discussions
- 3.8K Solar News - Automatic Feed
- 3.8K Solar Energy News RSS Feed