Sprinter buildout schematics and input
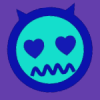
I would greatly appreciate any input on different components or even approaches to dialing this system in.
What I currently have
3 x 280w panels (might use 2 for now)
Magnum MS 2812
Ready to purchase
Midea 8k AC
200amp alternator
IMO PE69-4032 transfer switch
2 x Lifeline 8d 255hr
Midnite The Kid
Midnite MNDC 250plus
Victron phoenix 12/1200
Various breakers and cabling
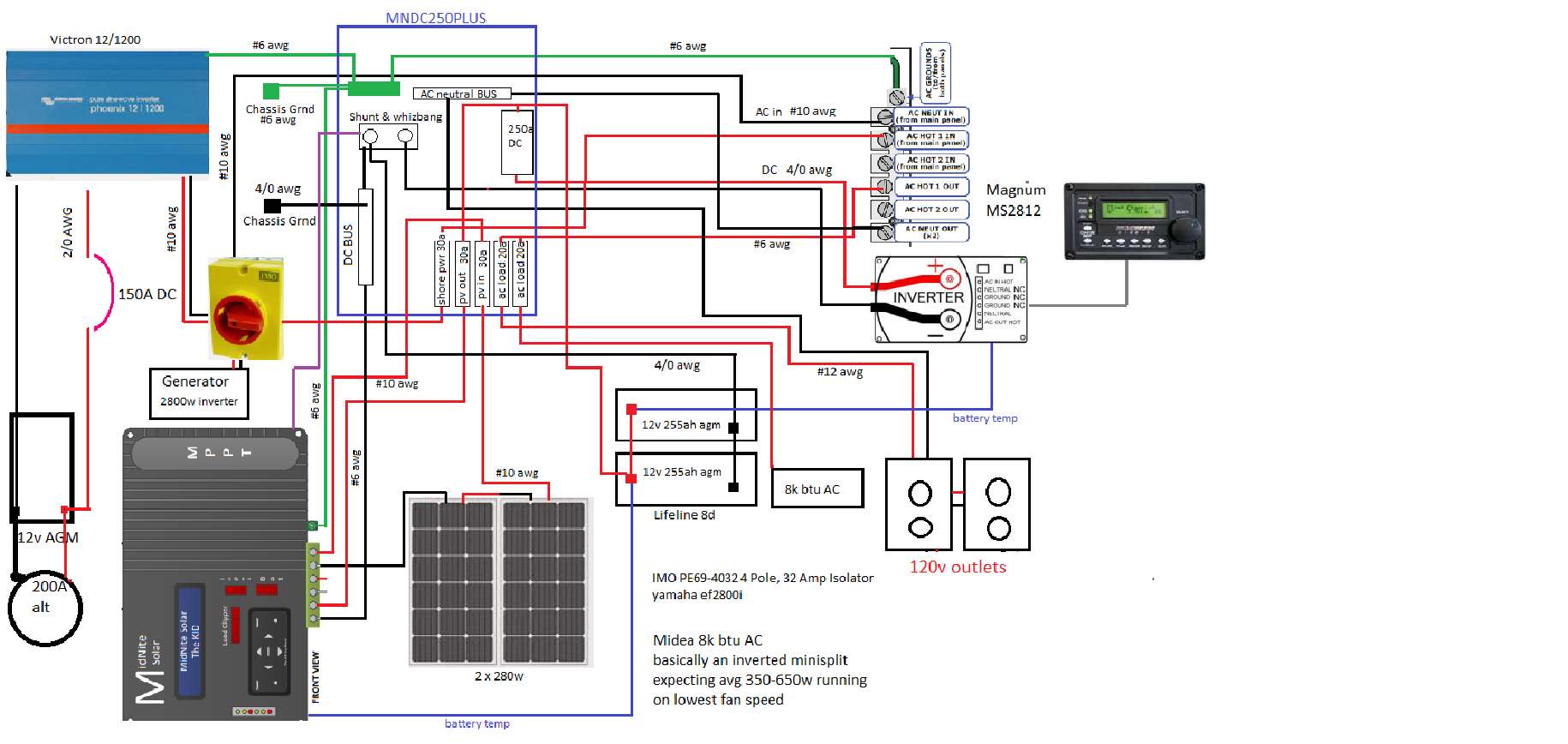
Comments
-
Want to add some more info...
I do not intend to live in the van ever, just extended camping adventure trips where we will be gone the major parts of the day. If I'm not driving an hr per day I have no problem high idling the van or running the genny for 1-2 hr. Sleeping in the ac is the biggest concern. I'm considering a timer on the ac to limit its run time vs constant lowest speed. Need to insulate the van wisely to make that work. According to 1st hand reports, users are averaging a slow ramp up to 600-1000w until the space is cooled to the setpoint, and then settling down to 100-450w on auto. Considering a setpoint of 75 and 80-90 air temp w a 10 hr run time overnight.1000whr /120v = 8.4ah (could be less)
350 x 9/120 = 26.25ah (should be less)
so approx 35ah @120 is 350 ah *1/0.85 is 412ah at 12v MAX?
Even considering max 50% discharge since this won’t be happening on a regular basis, 510Ah w the planned lifelines is most likely not going to get me through 10hrs. Only real world testing will tell. Unfortunately the yamaha is pull start only requiring me to get out of the van to start it up at some point. Makes starting the van up much more attractive.
I can tilt the panels upto 45 deg and I’m seriously considering using 3 since I already own them
panel #'s
Pmax 280W
Voc 44.9V
Isc 8.28A
Vmp 36.0V
Imp 7.77A
The van is 158" long and I'm wary of longer cable runs in the low 12v range. Which is why I think the phoenix 1200 or some equivalent should be mounted under the driver seat w aprox 6-7 ft run of 1/0 or 2/0. Then sending that 10ish amps via 120v aprox 15 ft back to the magnum and power station in the back.I’m aware the magnum is at the extreme end for 12v w its surge to 3900w.
1st I already own this unit, too good a deal to pass up years ago.
2nd I don’t intend to use its full potential but its nice to have more than you need, just in case.
3rd Whats not to love about the variable125a charger!
All other loads will be small, rechargeable led lights, 12v water pump, phone/laptop, and possibly a marine water heater w coolant bypass heater core supplemented w a 12v 400w element to be used in daytime or driving conditions only.
Shurflo 12v 3gpm 7.5maxA
Main concerns/questions…
Is my diagram solid?
Pros/cons and alternatives to the phoenix 1200
What is the most effective way to get max amps from the alternator to the house bank upto 24ft away and should this use a smart charger?
How will the magnum determine how much current to pull from the phoenix or the genny?
Is this something I need to program into the unit w the remote? Will it be 2 different profiles since the genny can input 20.8A and roughly 10A from the phoenix?
What is the most effective way to wake me up when the SoC is reaching 55-60% ?
-
You have really understood the details/requirements for wiring up a full off grid/shore power/van power system...
Just one quick suggestion... the Chassis Ground to battery negative... I suggest placing that on the "Load Side" of the shunt. That way, all current to/from the battery bank will be "logged" by the shunt.
Where it is now, if you have any 12 volt loads that use the chassis for grounding/return power of electrical circuits (examples can include automotive radio, LED lighting, "cigarette lighter outlets", etc... With the Chassis Ground on the "battery side" of the shunt, those types of loads (using chassis for return current) will be "invisible" to the shunt (will not measure/log these types of loads).
I have not gone into deep thought about your loads just yet... However, your calcuations, I highly suggest that you do them in Watts and Watt*Hours--Especially when looking at 12 VDC and 120 VAC "mixed" power (such as battery+inverter) systems.
Watts and Watt*Hours are "complete" units. That is the only number you need to fully describe your power needs. With Amps and Amp*Hours, you always need to know the operating voltage too (100 Amps @ 12 VDC = 1,200 Watts--10 Amps @ 120 VAC = 1,200 Watts).
You only need to convert to Amps when figuring out wiring/fuses/breakers and Amp*Hours (typically) when working on the batteries themselves... Although, more and more people are string to working with Watt*Hours and kWH (1kWH = 1,000 WH) for batteries too...
There is almost never any need to work with Amp*Hours for 120/240 VAC systems... There is no 120 VAC storage "Battery"... For example:1000whr /120v = 8.4ah (could be less)350 x 9/120 = 26.25ah (should be less)so approx 35ah @120 is 350 ah *1/0.85 is 412ah at 12v MAX?
An example (numbers just made up to show math):- 300 Watt average overnight A/C load
- 300 Watts * 8 hours = 2,400 Watt*Hours
- 2,400 WH * 1/0.85 AC inverter eff = 2,824 WH overnight DC load on battery bank
- 2,824 WH / 12 volt nominal battery bank = 235 AH @ 12 volt overnight draw (just for A/C)
- 300 Watt AC load * 8 hours usage * 1/0.85 AC inverter eff * 1/12 volt battery bank = 235 AH @ 12 volt A/C load
Just some other comments... Not saying your design is "right or wrong"--Just some observations.
While you have picked some great suppliers (Victron, Midnite, etc.)... You might want to look at staying in one family so you can have a system monitor with one integrated "monitoring" device. I.e., picking "all Victron" (compatible) hardware and you can have one monitor with cell phone app integration/control too.
Note for AC wiring terminology (North American): 120 VAC circuits have a Hot and a Neutral connection--Not Hot1+Hot2 (or L1 and L2) (for PSW/TSW type inverters). Generally, the Neutral leg is "bonded" to ground (chassis in a van) in one location. And the Hot or Line is the 120 VAC hot leg.
For 120/240 VAC circuits, we have L1 and L2 and Neutral (ground bonded). L1 to N and L2 to N is 120 VAC. L1 to L2 is 240 VAC (you are 120 VAC only for your system)...
Note that Neutral+Ground bonding gets "complicated" in an RV. Normally N+G bonding is done in the main AC panel in a home. Larger gensets and AC inverters may come with N+G bonding done internally. And N+G bonding will be done at the Shore Power panel in the RV park... So you need to understand where N+G bonding is done in your system and wire accordingly.
For example, many AC inverters have a 120 VAC input (from generator, shore power, etc.) and they will have an internal transfer switch that connects N+G bond when running from Inverter+genset power, and will "lift" N+G bond when connected to shore power.
Having multiple N+G bonds (i.e., shore power + N+G bond the van) can trip the GFI protection on the shore power outlet).Regarding using an AC inverter to boost from 12 VDC to 120 VAC from Van's 200 Amp alternator is a neat idea--Adding more major components adds cost and complexity (and maintenance) issues. I like to keep things "simple"--I.e., "all in one" AC inverter.
Just an example (from our forum host):
https://www.solar-electric.com/victron-energy-multiplus-ii-inverter-charger-12-3000-120-50-120v.html
https://www.solar-electric.com/lib/wind-sun/Datasheet-MultiPlus-II-3kVA-120V.pdf
There is just a lot to ponder over with an RV power system... My wife and I have been thinking about an RV/Van too in the future for traveling.
If you go to YouTube and look up Van Life videos--You can see a lot about their AC/DC power systems from Van builders and DIY too.
Here is a promo from Grit Overland (Van builder) that talks about their (what seems to be) high end van power system (first minute of video--They also use a 12 VDC A/C system--Unfortunately no details on equipment/build)):
https://www.youtube.com/watch?v=muQKCdHwr1M
-Bill
Near San Francisco California: 3.5kWatt Grid Tied Solar power system+small backup genset -
I already caught that mistake up further review and changed to this
Don't have any DC loads planned so I'll worry about a DC sub panel later if it comes up.
Makes total sense about using Wh, it seems I was trying to simultaneously determine max amps drawn w the 412a figure and total usage.
Again I already own the magnum ms2812 w 125A charger. Don't need to buy another unit.
I'm not sold on any one product BUT I love midnite as I have been running the Classic for 7 yrs on my 48v system. Big thanks to this forum for helping me with the design. I know it works well with the magnum. So even if I went with the victron 1200 or maybe an exeltech 1100, I don't care about linking it to the house system. Its only for "shore power" while running the vans alternator. I'm also considering the sterling 12v 30amp dc-dc charger, just need to figure out wire size with it mounted minimum 16 ft away from starter battery.
Regarding L1 and L2, that is part of the diagrams in the MS2812 manual. Here's an example for wiring 60 amps in, 30 on ea leg and the same way out.
When the inverter is in Standby mode, the full AC continuous pass-thru capacity of the MS Series inverter/charger is 30 amps for each AC leg1 (AC HOT 1 and AC HOT 2). For a 30-amp continuous pass-thru capability, each AC HOT input to the inverter requires a 30-amp continuous duty rated breaker², which corresponds to a minimum cable size of #10 AWG (in conduit). However, the AC HOT 1 and AC HOT 2 may be combined to obtain a 60-amp pass-thru capability² (see Figure 2-10). When tying the AC HOT 1 and HOT 2 together for a 60-amp continuous pass-thru capability, the AC input to the inverter requires a 60-amp continuous duty rated breake
And an excerpt on neutral ground bonding...
The inverter’s NEUT IN and NEUT OUT terminals are electrically isolated from each other while inverting. This is related to the neutral-ground bonding requirement and helps prevent ground-loops (see Section 2.6.5 for more information). If the installation requires the input and output neutrals to be connected together, the inverter’s neutral-to-ground connection must be disconnected
Categories
- All Categories
- 229 Forum & Website
- 137 Solar Forum News and Announcements
- 1.4K Solar News, Reviews, & Product Announcements
- 199 Solar Information links & sources, event announcements
- 898 Solar Product Reviews & Opinions
- 256 Solar Skeptics, Hype, & Scams Corner
- 22.5K Solar Electric Power, Wind Power & Balance of System
- 3.5K General Solar Power Topics
- 6.7K Solar Beginners Corner
- 1K PV Installers Forum - NEC, Wiring, Installation
- 2.1K Advanced Solar Electric Technical Forum
- 5.6K Off Grid Solar & Battery Systems
- 428 Caravan, Recreational Vehicle, and Marine Power Systems
- 1.1K Grid Tie and Grid Interactive Systems
- 654 Solar Water Pumping
- 816 Wind Power Generation
- 624 Energy Use & Conservation
- 619 Discussion Forums/Café
- 312 In the Weeds--Member's Choice
- 75 Construction
- 124 New Battery Technologies
- 108 Old Battery Tech Discussions
- 3.8K Solar News - Automatic Feed
- 3.8K Solar Energy News RSS Feed