Knowledge
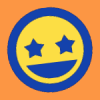
Donny31
Registered Users Posts: 9 ✭✭
Hello I just bought a wind turbine to help keep my 🔋 charged at night and help with charging wile I run my fridge exit. I have it about 20=30 feet off my back porch it gets wind at time the break has even engaged one or twice but I noticed that the charging wires that come from the controller are small compared to my solar. The question is how do I know if my turbine is really 400 wats like it says and the amps
Comments
-
You would need to put an ammeter in series with the output wires to measure the current as well as a voltmeter to see what voltage the windmill is developing. Practically, you would want it hooked up to a battery to prevent overspeeding. But I can almost guarantee you that you are unlikely to see anything near 400 watts if the windmill is not on a tower and you aren't experiencing REALLY strong winds.
Volts x amps = wattsIsland cottage solar system with appriximately 2500 watts of panels, 1kw facing southeast 1.3kw facing southwest 170watt ancient Arco's facing due south. All panels in parallel for a 24 volt system. Trace DR1524 MSW inverter which has performed flawlessly since 1994. Outback Flexmax 80 MPPT charge controller four 467A-h AGM batteries. Insignia 11.5 cubic foot electric fridge 1/4hp GSW piston pump. My 31st year. -
It is and its on like two 10 foot steel polls the winds are crazy
-
Tried to upload an video of the turbine won't let me but it spins has been since I put it up that's what has me scratching my head my solar charged my bank up with no problem
-
Donny,
I have updated your status--I am not sure the fact you are a new user (with less than 5-6 posts) limited your posting of videos--But you an try again.
I am not quite I understand what is happening with your turbine...- Your turbine needs to be mounted on a tall tower/pole clear of obstructions--Typically 30 feet tall, and at least 10 feet above any near by obstructions. Turbines need to be in "clean air" (non-turbulent air). If the turbine blades are spinning then slow down or even reverse, the nacelle "hunts" (keeps yawing left/right by 90 degrees or more), etc... Then the air flow is probably turbulent--No turbine can harvest much energy in turbulent air flow.
- Is this a "12 volt" DC battery bank?
- How far do the cables run from the turbine to the battery bank?
- Do you have a controller near the battery connected to the turbine (in-line)? Or do you have a "dump controller" (a charge controller that connects to the battery bank and "turns on" when the battery bank is full and dumps current to a resistor bank to prevent over charging?
- Can you measure the voltage at the battery bank when the turbine is running (prefer at night, or with the solar array turned off)?
- Do you have a current meter (shunt resistor+meter) to measure charging current from turbine? If not, you can get some pretty inexpensive current meters from Amazon/etc... Or you can get an AC+DC Current Clamp DMM to measure the current. Some examples for your research:
https://www.amazon.com/s?k=UNI-T+UT210E+True+RMS+Mini+Digital+Clamp+Meter&i=tools&ref=nb_sb_noss (inexpensive DC Clamp meter)
https://www.amazon.com/gp/product/B019CY4FB4 (nicer mid-range AC+DC current clamp DMM)
It sounds like you have some sort of wind turbine controller which can shutdown the turbine in high wind? There are just a bunch of different types of systems out there. You are welcome to post a link to the turbine brand/model you have installed.
Wind turbine issues are difficult to debug--Especially across the Internet. There are just so many issues (mounting, wind, turbulence, different controllers, etc.) and many that just do not work (even in "perfect" conditions they do not produce much energy).
-BillNear San Francisco California: 3.5kWatt Grid Tied Solar power system+small backup genset -
YaeMarine Wind Turbine Generator, Windmill Generator, 400W 24V Wind Turbine Businesses 5 Blade Wind Controller Turbine Generator kit for Home/Camping
-
Ok the turbine is maybe 10 feet from the 🔋 bank and yes 12 but no dump load I use an fan and have my fridge running so the bank gets to 100 and I turn the fan on fir load and not 30 feet maybe 20 feet
-
-
Donny,
First, the turbine is too close to the home/roof. Depending on direction of wind, you may have better airflow (winds come from left of picture). And very poor air to turbine with wind from rear, right, front.
Second, the tower/pipe is probably way to small of diameter and too tall to support the turbine. I would guess that guy wires would be required to hold the tower upright in high winds.
Third, I cannot see what the base for the tower is... Generally mounted directly in ground with lots of concrete... Mounting to the home, can literally "shake" the home apart (noisy) and blow over at base (torque/twisting from force on turbine down the "lever" of tower to base/home mounting.
Wind turbine towers require a lot of complex engineering--I certainly no expert.
For the size of the wiring... Say the turbine has a 300 Watt output @ 15 volts:- 300 Watts * 1/srt(3) (for 3 phase alternator) * 1/15 volts = 11.5 amps per leg (AC side)
- 14 AWG wire is certainly "good enough" (12-15 amp useful capacity)
https://www.calculator.net/voltage-drop-calculator.html?material=copper&wiresize=8.286&voltage=15&phase=ac3&noofconductor=1&distance=30&distanceunit=feet&eres=11.5&x=51&y=19Result for 14 AWG
Voltage drop: 1.51
That is a lot of drop--And the loss of voltage means a loss of ~1.5 volts from turbine to battery bank... In your case, it may be OK as this is a "24 volt" turbine (more or less, heavier wire from a 24 volt turbine--If it is generating >30 volts, is probably not going to increase the harvest energy with a PWM/direct connect wind controller).
Voltage drop percentage: 10.06%
Voltage at the end: 13.49
But to give you an idea of what a 3% loss looks like:
https://www.calculator.net/voltage-drop-calculator.html?material=copper&wiresize=2.061&voltage=15&phase=ac3&noofconductor=1&distance=30&distanceunit=feet&eres=11.5&x=74&y=22Result for 8 AWG wiring (roughly 4x heavier wiring)
Voltage drop: 0.38
From the wind controller to the battery bank--You don't want a lot of voltage drop. For a 300 Watt turbine on the DC side and 0.1 volt max suggested drop (keep wiring short and heavy):
Voltage drop percentage: 2.50%
Voltage at the end: 14.62- 300 Watts / 15 volts = 20 Amps
- 12 AWG wiring is "close"; 10 AWG would be better
https://www.calculator.net/voltage-drop-calculator.html?material=copper&wiresize=3.277&voltage=15&phase=dc&noofconductor=1&distance=2&distanceunit=feet&eres=20&x=14&y=2Result
Voltage drop: 0.080
Voltage at the end: 14.92:
Voltage drop percentage: 0.53%
The (simplified) NEC table for max current rating of wiring (the real table and rules are much more complex):
https://lugsdirect.com/WireCurrentAmpacitiesNEC-Table-301-16.htm
My humble suggestion (Note: I am not a fan of small wind installations--I think they are costly, require a lot of maintenance, and much of the off the shelf turbines simply do not work as advertised--So take my recommendations with a grain of salt)--Remove the turbine and mount more solar panels and a small backup genset if needed.
Get the solar+battery bank+AC inverter+loads working well--And if you want to install wind someday, start from scratch and look your site--Figure out where you can install a turbine away from the house and on a tower that is tall enough to get "good wind"... And cost the installation out first before you purchase anything. The wind turbine itself is generally the "cheap part" of the project... The engineering+tower+concrete+crane truck/hoist+wiring+controller+yearly maintenance/repairs+etc. is where the money goes.
This is one case where do it yourself turbine designs and builds generally work way better than off the shelf products. But if you are in an area with poor wind (urban area, trees, buildings, etc.)--Then generally a small turbine is not going to work for you.
-BillNear San Francisco California: 3.5kWatt Grid Tied Solar power system+small backup genset -
Thank you for your time to listen and understand what I was trying to explain and the info about the turbine did notice vibration when it was spinning just thought it was normal tho
-
One other questions if you don't mind when I press on the center of the turbine wile its spining the amps go up any idea why?
-
Maybe you take up some end play when you push on the hub causing the clearance between the magnets and the stator to be reduced, thereby increasing the current.
Well that's my guess anyway.Island cottage solar system with appriximately 2500 watts of panels, 1kw facing southeast 1.3kw facing southwest 170watt ancient Arco's facing due south. All panels in parallel for a 24 volt system. Trace DR1524 MSW inverter which has performed flawlessly since 1994. Outback Flexmax 80 MPPT charge controller four 467A-h AGM batteries. Insignia 11.5 cubic foot electric fridge 1/4hp GSW piston pump. My 31st year. -
The unit you have is a PMG--Permanent Magnet Generator (Alternator).
A standard car alternator has a spinning rotor with field coils to generate the North/South field(s)--The rotating coils have a pair of slip rings that carry zero to ~4 amps--The current controlled by the alternator's regulator (higher battery voltage, cut back on the current to the slip rings/coils).
A PMG uses high strength magnets and these create a permanent magnetic field. The advantage, the alternator does not need 4 amps of current to generate its own field (saves energy). The downside is that the "voltage regulator" cannot modulate the output voltage/current of the alternator. The controller needs to "dump" excess current to resistors (or other loads), or control the RPM of the turbine--In your case, the controller "short circuits" the 3 phase output which put maximum torque on the rotor--And (more or less) stops the turbine from spinning (or spinning at slow RPM). Feathering blades, furling the blades sideways to the wind, mechanical brake, etc. are also used (high end/reliable commercial turbines usually use several methods to control RPM for redundancy--Horizontal Axis Wind Turbines, HAWT, will overspeed and can self destruct if there is no electrical load/mechanical braking--Shattering blades and even can take down the tower).
So as Jim surmises--There is no electrical reason I can see for alternator output current to increase when pressing on the hub. That leaves mechanical "slop" in the main bearings (moving rotor inside the stator)--Or other electrical possibly are the yaw slip rings (if used) being "jostled" to improve current flow through the yaw slip rings/brushes.
i am not sure how you are pressing on the turbine hub without being turned into sushi (spinning blades and a yawing nacele are very dangerous). You could be seeing small changes in current which are the result of normal variations in turbine RPM/Yaw position, etc.... With solar and wind, "in the wild" (panels under sun, wind turbines on poles)--It is actually pretty difficult to "accurately" measure current/power... If your variations are less than say +/-50%--It is difficult to say that there was really any change due to your pressing on the hub (if you are spinning PMG Alternator on a lath/with an electric drill/etc.), smaller variations may be "real" (i.e., 5 vs 4 amps).
-BillNear San Francisco California: 3.5kWatt Grid Tied Solar power system+small backup genset -
Found the problem i put electric grease in side and it prevented it from charging now I I see almost 6 to 10amps
-
Glad you found the problem... Where was the "excess" grease? Electrical connections/battery posts? On yaw slip rings? etc....There are several types of electric grease... Dielectric grease (insulative type--Stops electrical flow) and conductive grease (helps electric flow).You can use dielectric grease on electrical connections... The connections just need to be tight (squeeze out grease for metal to metal contact) and can use toothed washers to make good electrical connections. And the grease keeps out the moisture.-BillNear San Francisco California: 3.5kWatt Grid Tied Solar power system+small backup genset
Categories
- All Categories
- 228 Forum & Website
- 136 Solar Forum News and Announcements
- 1.4K Solar News, Reviews, & Product Announcements
- 199 Solar Information links & sources, event announcements
- 898 Solar Product Reviews & Opinions
- 256 Solar Skeptics, Hype, & Scams Corner
- 22.5K Solar Electric Power, Wind Power & Balance of System
- 3.5K General Solar Power Topics
- 6.7K Solar Beginners Corner
- 1K PV Installers Forum - NEC, Wiring, Installation
- 2.1K Advanced Solar Electric Technical Forum
- 5.6K Off Grid Solar & Battery Systems
- 428 Caravan, Recreational Vehicle, and Marine Power Systems
- 1.1K Grid Tie and Grid Interactive Systems
- 653 Solar Water Pumping
- 816 Wind Power Generation
- 624 Energy Use & Conservation
- 619 Discussion Forums/Café
- 312 In the Weeds--Member's Choice
- 75 Construction
- 124 New Battery Technologies
- 108 Old Battery Tech Discussions
- 3.8K Solar News - Automatic Feed
- 3.8K Solar Energy News RSS Feed