Wind Charge Controller // Battery Selection
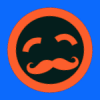
usernamemous
Registered Users Posts: 16 ✭✭
Hey guys,
I recently got a 2kW 48V 3 Phase axial flux wind turbine along with a 48V charge controller from china. The manufacturer says that the rated output of the charge controller is 42A and it is variable. I am buying a Li-Ion battery for it and the charging current is 7A and the manufacturer says that the charging current of the battery does not matter and only the battery voltage matters. Is this true? If so, how does this work? can anyone please explain? Thanks!
Ps. I am doing a DIY project with no prior experience in batteries and charge controllers.
I recently got a 2kW 48V 3 Phase axial flux wind turbine along with a 48V charge controller from china. The manufacturer says that the rated output of the charge controller is 42A and it is variable. I am buying a Li-Ion battery for it and the charging current is 7A and the manufacturer says that the charging current of the battery does not matter and only the battery voltage matters. Is this true? If so, how does this work? can anyone please explain? Thanks!
Ps. I am doing a DIY project with no prior experience in batteries and charge controllers.
Comments
-
First, get as much information as you can about your specific Li-Ion battery... Does it have a BMS (battery management system)? What type of BMS does it have (passive, active, fault shutdown).
Li-Ion batteries, in general, do not like high charging voltages or low discharging voltages (out of specification range). And depending on the specific chemistry, it can range from very short battery life (LiFePO4 for example) to (worst case) a fire.
Flooded Cell Lead Acid batteries are much more forgiving--They "gas" (and eventually can overheat) when overcharged (of course, everything has its limits). A lithium BMS can set an alarm (you shutdown the system if there is a issue) to self correcting (equalizing cells), to fault protection (disconnect bank from charger/loads).
The second question is how does the charge controller "interact" with the battery bank and BMS (if any)... I would start with understanding the Li-Ion side of the issues first--Then figure out how the wind charger would be affected by the Li-Ion requirements.
Also note--If this is a Horizontal Axis Wind Turbine (HAWT), they need an electrical load 100% of the time (like a battery bank), and/or some sort of overspeed control/shutdown system (typically, short the alternator on the HAWT to stall the blades, and a second system like a mechanical brake and/or furling system to point "way from the wind"). HAWTs, if unloaded and on a windy day can easily overspeed and self destruct.
-BillNear San Francisco California: 3.5kWatt Grid Tied Solar power system+small backup genset -
BB. said:First, get as much information as you can about your specific Li-Ion battery... Does it have a BMS (battery management system)? What type of BMS does it have (passive, active, fault shutdown).
Li-Ion batteries, in general, do not like high charging voltages or low discharging voltages (out of specification range). And depending on the specific chemistry, it can range from very short battery life (LiFePO4 for example) to (worst case) a fire.
Flooded Cell Lead Acid batteries are much more forgiving--They "gas" (and eventually can overheat) when overcharged (of course, everything has its limits). A lithium BMS can set an alarm (you shutdown the system if there is a issue) to self correcting (equalizing cells), to fault protection (disconnect bank from charger/loads).
The second question is how does the charge controller "interact" with the battery bank and BMS (if any)... I would start with understanding the Li-Ion side of the issues first--Then figure out how the wind charger would be affected by the Li-Ion requirements.
Also note--If this is a Horizontal Axis Wind Turbine (HAWT), they need an electrical load 100% of the time (like a battery bank), and/or some sort of overspeed control/shutdown system (typically, short the alternator on the HAWT to stall the blades, and a second system like a mechanical brake and/or furling system to point "way from the wind"). HAWTs, if unloaded and on a windy day can easily overspeed and self destruct.
-Bill
at 120 rated RPM the charge controller produces 48V & 42A which is 2000W. Does the charge controller (has a break function) automatically apply break to the wind turbine to match the 7A of the battery? -
It really depends on the wind charge controller, but I would guess it does not have the ability to reduce/control charging current.Most are "dump" type controllers... Basically the controller turns on a relay that connects a resistor dump load, or possibly just stops the turbine when the battery is full.I'd your battery back going to be a 12 volt or 48 volt battery bank?Do you have a link to the turbine and charger controller system?7 amps is a small battery bank for a 42 amp charging system... Would expect closer to 420 amphour battery bank at 48 volts. Which would usually charge/discharge at 42-84 amps.7 amps at 58 volts charging is only 406 Watts. A 2,000 watt wind turbine seems to be way oversized.Do you have other charging sources available... Utility power, solar, gender?Bill
Near San Francisco California: 3.5kWatt Grid Tied Solar power system+small backup genset -
BB. said:It really depends on the wind charge controller, but I would guess it does not have the ability to reduce/control charging current.Most are "dump" type controllers... Basically the controller turns on a relay that connects a resistor dump load, or possibly just stops the turbine when the battery is full.I'd your battery back going to be a 12 volt or 48 volt battery bank?Do you have a link to the turbine and charger controller system?7 amps is a small battery bank for a 42 amp charging system... Would expect closer to 420 amphour battery bank at 48 volts. Which would usually charge/discharge at 42-84 amps.7 amps at 58 volts charging is only 406 Watts. A 2,000 watt wind turbine seems to be way oversized.Do you have other charging sources available... Utility power, solar, gender?Bill
The spec sheets are attached to this post and the link to the battery is: https://www.lithiumion-batteries.com/products/12-volt-lithium-batteries/12v-7ah-lithium-ion-battery-2.php
I understand 7Ah is a small battery bank but it serves my purpose. At 48V the capacity is 336Wh.
No, the wind turbine that spins intermittently is the only source.
-
Thank you for posting the specifications... I do not see any capability to limit charging current to 7 Amps... There is a micro charging current option for the controller, but that is only "useful" when the battery hits the voltage setpoint (continue some charging current once setpoint is reached, vs shutting down or turning on the dump load). And "absorb charging current/micro current" function is only useful for Lead Acid batteries, not usually needed for Lithium Ion type.
This has a PWM "stepless" dump load... It is possible that this would hold the charging voltage of 5x.x volts--But it does not seem to be setup to limit absolute charging current to 7 amps.
And, if you are using a 7 AH battery bank, 7 amps of charging is a C/1 rate of charge or 100%. That is a very high charge rate (100%)--For various lead acid batteries, 10-20% rate of charge is pretty much standard.
I think this turbine is simply way oversized for your needs... You could look at some other type of switching power supply that takes a wide range of input voltage, and outputs 7 Amps in constant current mode until 5x.x volts is reached, then it holds 5x.x volts. This still leaves an issue with how the turbine in managed (shutdown/what happens with ~400 Watt load or less (once battery bank is full, loading is reduced to pretty much zero amps + whatever your loads maybe). Then you would need to work on some sort of loading/braking system for the turbine.
Almost anything is possible--But are you pushing the envelope at the moment (I think).
Another question--Is the BMS for the Lithium Bank capable of running @48 volts nominal? That is higher than the typical 4/12/24 volt range that many BMS are designed for.
-BillNear San Francisco California: 3.5kWatt Grid Tied Solar power system+small backup genset -
BB. said:Thank you for posting the specifications... I do not see any capability to limit charging current to 7 Amps... There is a micro charging current option for the controller, but that is only "useful" when the battery hits the voltage setpoint (continue some charging current once setpoint is reached, vs shutting down or turning on the dump load). And "absorb charging current/micro current" function is only useful for Lead Acid batteries, not usually needed for Lithium Ion type.
This has a PWM "stepless" dump load... It is possible that this would hold the charging voltage of 5x.x volts--But it does not seem to be setup to limit absolute charging current to 7 amps.
And, if you are using a 7 AH battery bank, 7 amps of charging is a C/1 rate of charge or 100%. That is a very high charge rate (100%)--For various lead acid batteries, 10-20% rate of charge is pretty much standard.
I think this turbine is simply way oversized for your needs... You could look at some other type of switching power supply that takes a wide range of input voltage, and outputs 7 Amps in constant current mode until 5x.x volts is reached, then it holds 5x.x volts. This still leaves an issue with how the turbine in managed (shutdown/what happens with ~400 Watt load or less (once battery bank is full, loading is reduced to pretty much zero amps + whatever your loads maybe). Then you would need to work on some sort of loading/braking system for the turbine.
Almost anything is possible--But are you pushing the envelope at the moment (I think).
Another question--Is the BMS for the Lithium Bank capable of running @48 volts nominal? That is higher than the typical 4/12/24 volt range that many BMS are designed for.
-Bill
I understand the turbine is over sized, but there is going to be only intermittent wind and the battery size even though being small, it serves the purpose of "testing". I like the idea of switching power supply and I assume it goes between the charge controller and the battery, is that right? What is the key terms I should use to search for this part?
Once the battery bank is full, the charge controller will automatically start the break function to slow down the turbine speed - This function is built into the charge controller.
For the battery bank, I confirmed with the manufacturer that they can be connected in series to get 48V and can be charged using a single 48V charger. -
Note: I am not a fan of small wind turbines... Few seem to work well, and few last without lots of maintenance. This is one product that the DIY turbines seem to work better than off the shelf units.
The chance that your turbine will output >7 amps @ 5x.x volts is rare in most conditions--Other than when you have wind storms. And wind storms are always a big concern with turbines.
If you are just testing--And you do not have high winds forecast--Shut down the turbine until the storm blows by.
You could do other things, like set up a current shunt and a small microcontroller... And simply shut down the turbine when >7 amps is being passed (pause 5 minutes, then restart, etc.), or turns on a dump load (possibly several dump loads in steps), shuts down turbine and requires a manual reset, figure out RPM needed for 7 amps charging, setup microcontroller to load/short turbine (PWM) when turbine >max rpm/current, etc...
And there is always the other turbine issues... Mounting in "clean/non-turbulent air"--Usually a 30 foot or taller tower (above ground) and another 10+ feet above nearby obstructions, don't mount on a living structure (home/office building), away from people (homes, play fields, etc.--Blades can fly off, ice can be thrown, yaw bearings fail and drop the whole nacelle).
-BillNear San Francisco California: 3.5kWatt Grid Tied Solar power system+small backup genset -
BB. said:Note: I am not a fan of small wind turbines... Few seem to work well, and few last without lots of maintenance. This is one product that the DIY turbines seem to work better than off the shelf units.
The chance that your turbine will output >7 amps @ 5x.x volts is rare in most conditions--Other than when you have wind storms. And wind storms are always a big concern with turbines.
If you are just testing--And you do not have high winds forecast--Shut down the turbine until the storm blows by.
You could do other things, like set up a current shunt and a small microcontroller... And simply shut down the turbine when >7 amps is being passed (pause 5 minutes, then restart, etc.), or turns on a dump load (possibly several dump loads in steps), shuts down turbine and requires a manual reset, figure out RPM needed for 7 amps charging, setup microcontroller to load/short turbine (PWM) when turbine >max rpm/current, etc...
And there is always the other turbine issues... Mounting in "clean/non-turbulent air"--Usually a 30 foot or taller tower (above ground) and another 10+ feet above nearby obstructions, don't mount on a living structure (home/office building), away from people (homes, play fields, etc.--Blades can fly off, ice can be thrown, yaw bearings fail and drop the whole nacelle).
-Bill -
Most charge controller do not have a regulated output voltage.And most systems the battery bank is the voltage regulator. It sinks current if the bus voltage is high (charging) and sources current if the bus voltage is low k discharging).Lithium batteries cannot safely/reliably sink current if 100% full (over charging lithium batteries can quick ruin them). And over discharging can ruin them too. That is why BMS controllers can have battery bank disconnect if things go south on the battery bus.Think of the wind turbine that can output 0-75+ VDC. And 0 to 35 amps. The battery would be expected to take 0-75 amps (short term at least) and keep the bus voltage between 42 and 60 VDC or so.Long term, the charge controller is expected to reduce charging current (pulse width modulation) by switching on/off multiple times a second. Or idea a dump controller (typically for wind turbines) and pwm between zero and 35 amps load (in your case).Because the turbine can exceed 7amps, by a lot, the battery cannot regulate the short current spikes without over voltage/damage or tripping the over current or over voltage BMS protection circuit.There other issue to review is which lithium ion chemistry you have. Around here, LiFePO4 is the the usual type as it fails safely, more or less.Other lithium chemistries can fail with smoke and fire and other issues.This is not a trivial set of issues.BillNear San Francisco California: 3.5kWatt Grid Tied Solar power system+small backup genset
-
BB. said:Most charge controller do not have a regulated output voltage.And most systems the battery bank is the voltage regulator. It sinks current if the bus voltage is high (charging) and sources current if the bus voltage is low k discharging).Lithium batteries cannot safely/reliably sink current if 100% full (over charging lithium batteries can quick ruin them). And over discharging can ruin them too. That is why BMS controllers can have battery bank disconnect if things go south on the battery bus.Think of the wind turbine that can output 0-75+ VDC. And 0 to 35 amps. The battery would be expected to take 0-75 amps (short term at least) and keep the bus voltage between 42 and 60 VDC or so.Long term, the charge controller is expected to reduce charging current (pulse width modulation) by switching on/off multiple times a second. Or idea a dump controller (typically for wind turbines) and pwm between zero and 35 amps load (in your case).Because the turbine can exceed 7amps, by a lot, the battery cannot regulate the short current spikes without over voltage/damage or tripping the over current or over voltage BMS protection circuit.There other issue to review is which lithium ion chemistry you have. Around here, LiFePO4 is the the usual type as it fails safely, more or less.Other lithium chemistries can fail with smoke and fire and other issues.This is not a trivial set of issues.Bill
Also, for a 48V LiFePo4 battery, what will be the voltage at 0%? should I ask this to the manufacturer? what is the usual case here? Thanks! -
Many of these wind charge controllers are "PWM" type. More or less a simple on/off switch (transistor). They are either on or off.
For dump controllers the switch connects the battery bank to the load bank (a bunch of power resistors). Depending on the design, they will cycle on/off a few times to 10's of times a second. There is no current regulation--It is either on or off--And it may cycle many times per second.
For a turbine shunt controller, I guess it simply shorts out the alternator on the wind turbine, stopping current to the battery bank, and loading/slowing down the wind turbine... Purely a guess on my part on how it may work.
But notice that the current flow is defined by the amount the turbine can output (RPM based), and what the battery can accept. If the turbine can output way more current than the battery can accept--Generally that is not very good for the battery bank, and not very uniform battery bus voltage (lots of voltage peaks). Exceeding rated current/voltage for cells is not a good thing (almost any rechargeable battery type). The battery is supposed to "clamp" the voltage range of the battery bank (charging/discharging). If you exceed the current limits of the cell/battery, then your bus voltage will go outside the nominal voltage range. How your loads (and your cells react) could be an expensive experiment.
The manufacturer should provide you the operational voltage range of the battery bank (discharging and charging). The single cell voltage range is probably around 2.50 to 3.65 volts from discharged to 100% charged (per cell).
If you have a "48 volt battery", that may be:- 48 volts / 3.2 volts nominal (for LiFePO4) = 15 cells in series
- 3.2 volts nominal * 4 cells per battery * 4 batteries (everything in series) = 51.2 volt nominal
- 2.50 volts "dead" * 16 series cells = 40 volts minimum
- 3.65 volts "100% charged" * 16 cells = 58.4 volts maximum
- 3.60 * 16 cells = 57.6 volts charge set point
And that is one of the functions of (many) Battery Management Systems. To make sure that no cell runs out of voltage range (alarm, shut down battery pack, shut down charging/loads, equalize high and low voltage cells, etc.).
LI Ion batteries cannot be "equalized" like Flooded Cell Lead Acid batteries can be. Lead Acid batteries are "over charged" a bit, so that the 100% charged cells let current through to bring up the 95% charged cells.
The above are rough guesses... Yes, you do need the information from the cell/battery manufacturer as to what their specific values are (there are variations in chemistry, construction, BMS setpoints/functions/capabilities, etc.).
-BillNear San Francisco California: 3.5kWatt Grid Tied Solar power system+small backup genset -
BB. said:Many of these wind charge controllers are "PWM" type. More or less a simple on/off switch (transistor). They are either on or off.
For dump controllers the switch connects the battery bank to the load bank (a bunch of power resistors). Depending on the design, they will cycle on/off a few times to 10's of times a second. There is no current regulation--It is either on or off--And it may cycle many times per second.
For a turbine shunt controller, I guess it simply shorts out the alternator on the wind turbine, stopping current to the battery bank, and loading/slowing down the wind turbine... Purely a guess on my part on how it may work.
But notice that the current flow is defined by the amount the turbine can output (RPM based), and what the battery can accept. If the turbine can output way more current than the battery can accept--Generally that is not very good for the battery bank, and not very uniform battery bus voltage (lots of voltage peaks). Exceeding rated current/voltage for cells is not a good thing (almost any rechargeable battery type). The battery is supposed to "clamp" the voltage range of the battery bank (charging/discharging). If you exceed the current limits of the cell/battery, then your bus voltage will go outside the nominal voltage range. How your loads (and your cells react) could be an expensive experiment.
The manufacturer should provide you the operational voltage range of the battery bank (discharging and charging). The single cell voltage range is probably around 2.50 to 3.65 volts from discharged to 100% charged (per cell).
If you have a "48 volt battery", that may be:- 48 volts / 3.2 volts nominal (for LiFePO4) = 15 cells in series
- 3.2 volts nominal * 4 cells per battery * 4 batteries (everything in series) = 51.2 volt nominal
- 2.50 volts "dead" * 16 series cells = 40 volts minimum
- 3.65 volts "100% charged" * 16 cells = 58.4 volts maximum
- 3.60 * 16 cells = 57.6 volts charge set point
And that is one of the functions of (many) Battery Management Systems. To make sure that no cell runs out of voltage range (alarm, shut down battery pack, shut down charging/loads, equalize high and low voltage cells, etc.).
LI Ion batteries cannot be "equalized" like Flooded Cell Lead Acid batteries can be. Lead Acid batteries are "over charged" a bit, so that the 100% charged cells let current through to bring up the 95% charged cells.
The above are rough guesses... Yes, you do need the information from the cell/battery manufacturer as to what their specific values are (there are variations in chemistry, construction, BMS setpoints/functions/capabilities, etc.).
-Bill -
As an example, the turbine outputs 0-48 volts from 0-48 RPM. There is "no" energy harvest--Just a breeze blowing the turbine, overcoming bearing friction, and magnetic "drag" (pole pieces, a little circulating current in the steel/iron poles, etc.).
You are correct, if the battery bank is 48 VDC, and the turbine is 48 VDC, then there is no current flow.
Depending on the design of the charger/rectifier system, you may have 1-2 volts drop (across rectifying, blocking diodes) to change AC into DC, and prevent the battery from discharging backwards into the charge controller electronics, etc.
When the turbine is at 80 to 120 RPM, it will try to output from 48 volts to ~75 volts (or whatever). And it will have available current of 0.0 to 42 amps (or whatever--Specifics do not matter too much for the explanation to work).
Now, you have a source curve (RPM, current, voltage) available from the turbine/charger system. And you have a "load" curve, which is your battery bank. More or less, assuming you do not feed "too much current" to the battery bank, Li Ion batteries have very little voltage drop (or rise) vs current. In other words, if you feed 0-7 amps at >48 volts to the Li Ion battery, it will hold a voltage that represents its "present" state of charge (say 51.2 volts nominal means 50%--I don't know, did not look it up, just an example)... As the charger feeds 7 amps to the battery, the battery voltage will rise from 51.2 volts (50% SoC) to 58.4 volts. Since your battery was at 50% capacity, and its capacity was 7 AH and 50% full, you needed 3.5 AH to fill the battery to 100%. Or in this imaginary example, you needed 1/2 an hour (30 minutes) to feed 7 amps constant current to the bank to bring it to ~58.4 VDC "full" (100% capacity, all cells balanced, etc.).
Now, lets say you feed 42 Amps to the battery (turbine at full speed, under 58.4 volt battery bus), you now have a contention between the generator source, which can supply 42 amps from 0 to 75 VDC, and a battery trying to hold 51.2 volts (50% SoC).
Either the battery "wins", and holds ~51.2 volts until full, or the battery "loses control" of the bus voltage, and it rises to a new voltage point somewhere between 51.2 and 75 VDC... And the battery is probably damaged from internal heating, break down in chemistry, or something else.
When the charge controller "sees" >58.4 volts (your set-point), it will (some how) shut down the turbine or turn on a dump load to get the current to 0 volts or even negative current (draw 42 amps from turbine, and possibly extra current from battery bank--Just because this stuff is not set up "laboratory" accuracy (just real round numbers).
At this point, the turbine/charge controller is "shorting out the turbine" (P=V*I) and in theory, there is little heat generated (0 volts = zero power). In practice, you have voltage drop in wiring, rectifier, turbine wiring, etc.--And you can end up with over heating (especially if the wind is >>> rated wind, the turbine will not stall, but will continue to generate >> 42 amps of current in the "short/shunt" system.
If you have a "dump" load, the extra current goes into a resistor load bank, and simply generates "waste heat" (or you have a load, like a water pump, and use the "excess energy" to fill your local cistern/pond).
In some ways, it is not that complex (the alternator generates based on RPM, bus voltage, and bus current). The battery supplies or sinks current according to its capabilities, state of charge (and don't forget the BMS which can do its own thing, like disconnecting the battery from the battery bus).
All of this is a pretty interesting collection of "black boxes" doing their own thing, and together, generating power for your loads and topping off the battery bank (and battery supplying wind with no loads).
My explanation is a "really rough, 50,000 foot view" of how everything works. And because I do not know the details of "each of your black boxes", they may do different things (only turbine short/shunt, only battery dump, both, mechanical brake on turbine, etc.). And understanding the details in important when putting this stuff all together.
HOWEVER, the big warning I want to keep harping on here--You have a 42 amp "capable" wind turbine/alternator/charge controller and a 7 Amp capable Li Ion battery bank. Unless there is something I am missing (which is very possible, I am working with very little information), connecting a 42 amp source to a 7 amp sink is just not safe.
And depending the Lithium Chemistry, and the exact failures, Li Ion batteries (even LiFePO4 types) can fail in very dangerous ways. Besides the simple issue of "fire"--Lithium failures can create/release Hydrofluoric Acid. And, from what I have read, you do not want HF Acid anywhere around people. The stuff is deadly in small concentrations, and fire departments have dumped contaminated equipment (hoses, gear, etc.) because it cannot be decontaminated (at least easily).
More than happy to help understand how turbine/battery power systems work. But I want to make sure that I am not encouraging you to build the system you have proposed (unless the battery bank is in a separate shed/open field, far away from others).
Sorry to be so repetitive...
-BillNear San Francisco California: 3.5kWatt Grid Tied Solar power system+small backup genset -
BB. said:As an example, the turbine outputs 0-48 volts from 0-48 RPM. There is "no" energy harvest--Just a breeze blowing the turbine, overcoming bearing friction, and magnetic "drag" (pole pieces, a little circulating current in the steel/iron poles, etc.).
You are correct, if the battery bank is 48 VDC, and the turbine is 48 VDC, then there is no current flow.
Depending on the design of the charger/rectifier system, you may have 1-2 volts drop (across rectifying, blocking diodes) to change AC into DC, and prevent the battery from discharging backwards into the charge controller electronics, etc.
When the turbine is at 80 to 120 RPM, it will try to output from 48 volts to ~75 volts (or whatever). And it will have available current of 0.0 to 42 amps (or whatever--Specifics do not matter too much for the explanation to work).
Now, you have a source curve (RPM, current, voltage) available from the turbine/charger system. And you have a "load" curve, which is your battery bank. More or less, assuming you do not feed "too much current" to the battery bank, Li Ion batteries have very little voltage drop (or rise) vs current. In other words, if you feed 0-7 amps at >48 volts to the Li Ion battery, it will hold a voltage that represents its "present" state of charge (say 51.2 volts nominal means 50%--I don't know, did not look it up, just an example)... As the charger feeds 7 amps to the battery, the battery voltage will rise from 51.2 volts (50% SoC) to 58.4 volts. Since your battery was at 50% capacity, and its capacity was 7 AH and 50% full, you needed 3.5 AH to fill the battery to 100%. Or in this imaginary example, you needed 1/2 an hour (30 minutes) to feed 7 amps constant current to the bank to bring it to ~58.4 VDC "full" (100% capacity, all cells balanced, etc.).
Now, lets say you feed 42 Amps to the battery (turbine at full speed, under 58.4 volt battery bus), you now have a contention between the generator source, which can supply 42 amps from 0 to 75 VDC, and a battery trying to hold 51.2 volts (50% SoC).
Either the battery "wins", and holds ~51.2 volts until full, or the battery "loses control" of the bus voltage, and it rises to a new voltage point somewhere between 51.2 and 75 VDC... And the battery is probably damaged from internal heating, break down in chemistry, or something else.
When the charge controller "sees" >58.4 volts (your set-point), it will (some how) shut down the turbine or turn on a dump load to get the current to 0 volts or even negative current (draw 42 amps from turbine, and possibly extra current from battery bank--Just because this stuff is not set up "laboratory" accuracy (just real round numbers).
At this point, the turbine/charge controller is "shorting out the turbine" (P=V*I) and in theory, there is little heat generated (0 volts = zero power). In practice, you have voltage drop in wiring, rectifier, turbine wiring, etc.--And you can end up with over heating (especially if the wind is >>> rated wind, the turbine will not stall, but will continue to generate >> 42 amps of current in the "short/shunt" system.
If you have a "dump" load, the extra current goes into a resistor load bank, and simply generates "waste heat" (or you have a load, like a water pump, and use the "excess energy" to fill your local cistern/pond).
In some ways, it is not that complex (the alternator generates based on RPM, bus voltage, and bus current). The battery supplies or sinks current according to its capabilities, state of charge (and don't forget the BMS which can do its own thing, like disconnecting the battery from the battery bus).
All of this is a pretty interesting collection of "black boxes" doing their own thing, and together, generating power for your loads and topping off the battery bank (and battery supplying wind with no loads).
My explanation is a "really rough, 50,000 foot view" of how everything works. And because I do not know the details of "each of your black boxes", they may do different things (only turbine short/shunt, only battery dump, both, mechanical brake on turbine, etc.). And understanding the details in important when putting this stuff all together.
HOWEVER, the big warning I want to keep harping on here--You have a 42 amp "capable" wind turbine/alternator/charge controller and a 7 Amp capable Li Ion battery bank. Unless there is something I am missing (which is very possible, I am working with very little information), connecting a 42 amp source to a 7 amp sink is just not safe.
And depending the Lithium Chemistry, and the exact failures, Li Ion batteries (even LiFePO4 types) can fail in very dangerous ways. Besides the simple issue of "fire"--Lithium failures can create/release Hydrofluoric Acid. And, from what I have read, you do not want HF Acid anywhere around people. The stuff is deadly in small concentrations, and fire departments have dumped contaminated equipment (hoses, gear, etc.) because it cannot be decontaminated (at least easily).
More than happy to help understand how turbine/battery power systems work. But I want to make sure that I am not encouraging you to build the system you have proposed (unless the battery bank is in a separate shed/open field, far away from others).
Sorry to be so repetitive...
-Bill -
You still have the issue of "what happens" when the battery is full in high wind conditions... The BMS gives your system ~1 second of overvoltage and will disconnect--That dumps the load on the wind turbine--Giving its controller a very short period of time (seconds?) to shut down the turbine (and many controllers use the battery bus voltage for their "brains"--Cut the battery bus voltage, and the charge controller could shutdown/fail and let the turbine spin uncontrolled--And the blades/turbine could fail). And when the battery "disconnects", your "battery bus" could be hit will full wind turbine output voltage (could easily over 100 VDC pretty easily).
You don't have to install the system in a "remote" location to test the system. You can do the "functional tests" in a lab a lot easier.
Backing up a moment... Are you building the system to test a concept? Such as a remote powered device (anything from radios, remote sensensing, to simply a little power and lights for locals?
Is this a test of a battery bank/power system, a test of a wind turbine in the application, or what?
Wind turbines tend to be highly variable in their harvest (only developing full power in storms, or possibly windy conditions on a hilltop/cliff face/etc.). They also tend to be very seasonal in their harvest.
A 7 AH battery * 48 volts running 24 hours between charges is:- 7 AH * 48 volts = 336 WH (full to dead)
- 336 WH / 24 hour battery load = 14 Watt continuous load over 24 hours (less if 3+ days of energy storage at least)
- 336 WH per day * 1/0.52 off grid system eff * 1/1 hour of sun per day = 646 Watts of solar panel "break even" in deep winter
It would seem to me, if you have the room (and clear of trees/buildings/etc.) to build a 10 meter tall 2 kWatt turbine installation, you should be able to hang a few solar panels there too. Use the solar panels for day to day harvest, and wind turbines for deep winter/stormy weather.
I am sort of "starting in the middle" of a system design... Ideally, I like to understand the loads (24 hours per day, X days of storage, can the loads be shut down during poor harvest, etc.). That defines the battery bank (size, voltage, chemistry, temperature requirements, service requirements, costs, and even safety/failure modes). Then design a charging system that keeps the battery bank "happy".
-BillNear San Francisco California: 3.5kWatt Grid Tied Solar power system+small backup genset -
BB. said:You still have the issue of "what happens" when the battery is full in high wind conditions... The BMS gives your system ~1 second of overvoltage and will disconnect--That dumps the load on the wind turbine--Giving its controller a very short period of time (seconds?) to shut down the turbine (and many controllers use the battery bus voltage for their "brains"--Cut the battery bus voltage, and the charge controller could shutdown/fail and let the turbine spin uncontrolled--And the blades/turbine could fail). And when the battery "disconnects", your "battery bus" could be hit will full wind turbine output voltage (could easily over 100 VDC pretty easily).
You don't have to install the system in a "remote" location to test the system. You can do the "functional tests" in a lab a lot easier.
Backing up a moment... Are you building the system to test a concept? Such as a remote powered device (anything from radios, remote sensensing, to simply a little power and lights for locals?
Is this a test of a battery bank/power system, a test of a wind turbine in the application, or what?
Wind turbines tend to be highly variable in their harvest (only developing full power in storms, or possibly windy conditions on a hilltop/cliff face/etc.). They also tend to be very seasonal in their harvest.
A 7 AH battery * 48 volts running 24 hours between charges is:- 7 AH * 48 volts = 336 WH (full to dead)
- 336 WH / 24 hour battery load = 14 Watt continuous load over 24 hours (less if 3+ days of energy storage at least)
- 336 WH per day * 1/0.52 off grid system eff * 1/1 hour of sun per day = 646 Watts of solar panel "break even" in deep winter
It would seem to me, if you have the room (and clear of trees/buildings/etc.) to build a 10 meter tall 2 kWatt turbine installation, you should be able to hang a few solar panels there too. Use the solar panels for day to day harvest, and wind turbines for deep winter/stormy weather.
I am sort of "starting in the middle" of a system design... Ideally, I like to understand the loads (24 hours per day, X days of storage, can the loads be shut down during poor harvest, etc.). That defines the battery bank (size, voltage, chemistry, temperature requirements, service requirements, costs, and even safety/failure modes). Then design a charging system that keeps the battery bank "happy".
-Bill
I am trying to search for an energy meter that goes at the output of the wind turbine (3 phases), charge controller and battery with data logging functionality. I found a few in amazon like the Eyedro. Can you recommend any? Thanks! -
I cannot recommend any meters for 3 phase--But normally, the turbine output is run right into a rectifier. And (mostly) for a charge controller the Power In from the turbine is pretty much the same as the power out to the battery bank.
Of course, Dump Loads (if present), and when the turbine is shorted (either dead short, or through a low resistance shunt load), is not useful for "harvest" information.
For DC power meters, there are just bunches of them on Amazon (EBay, et.al.)--Depends if you want logging/lab grade accuracy or not--But the "simple" DC Power meters are pretty complex these days:
https://www.amazon.com/s?k=dc+watt+power+meter
For three phase, you could use a current transformer/coil to monitor the current/power on each phase--Or just one phase and assume the other two are symmetrical.
For single phase AC, there are a lot of Consumer Grade meters (don't know how well they work on "wild" AC frequency):
https://www.amazon.com/s?k=ac+watt+power+meter
Of course, there is Fluke--If you happen to have $10,000 laying around:
https://www.fluke.com/en-us/product/electrical-testing/power-quality/438-ii
But how useful that is for you? Not sure you are analysing the design and construction of your Turbine's Alternator...
-BillNear San Francisco California: 3.5kWatt Grid Tied Solar power system+small backup genset -
BB. said:I cannot recommend any meters for 3 phase--But normally, the turbine output is run right into a rectifier. And (mostly) for a charge controller the Power In from the turbine is pretty much the same as the power out to the battery bank.
Of course, Dump Loads (if present), and when the turbine is shorted (either dead short, or through a low resistance shunt load), is not useful for "harvest" information.
For DC power meters, there are just bunches of them on Amazon (EBay, et.al.)--Depends if you want logging/lab grade accuracy or not--But the "simple" DC Power meters are pretty complex these days:
https://www.amazon.com/s?k=dc+watt+power+meter
For three phase, you could use a current transformer/coil to monitor the current/power on each phase--Or just one phase and assume the other two are symmetrical.
For single phase AC, there are a lot of Consumer Grade meters (don't know how well they work on "wild" AC frequency):
https://www.amazon.com/s?k=ac+watt+power+meter
Of course, there is Fluke--If you happen to have $10,000 laying around:
https://www.fluke.com/en-us/product/electrical-testing/power-quality/438-ii
But how useful that is for you? Not sure you are analysing the design and construction of your Turbine's Alternator...
-Bill
- Wind turbine output 3 phase AC (AC current, AC voltage, AC power, DC energy)
- Charge controller (with inbuilt rectifier) output DC (DC current, DC voltage, DC power, DC energy, Battery charge current)
- Battery (Input current, SOC voltage, energy capacity)
I did see all those meters you sent - but I really need a data logging I am researching into it and found a few like Eyedro, Accuenergy and emporia. still looking into it. Fluke is definitely in my list, may be one day -
One of the options with Alternators, is to use an MPPT type charge controller... Basically, Power = Voltage * Current. So, if you draw XX amps (max rated current) at 30 volts to charge your battery bank, with a PWM/Direct connect alternator, you can replace with an MPPT type controller (typically a modified Solar MPPT Charge Controller) and let the RPM of the turbine go higher, and you get 60 or more volts... and with P=V*I, current constant (max rated), but double the voltage, you double the power harvest (MPPT charge controller are typically buck mode down converting switching power supplies with >~95% efficiency (this can double your battery charging current).
But, like everything, it gets complicated. Midnite Solar is one company that has an integrated MPPT/Dump controller system. And like anything complicated, it is not cheap:
https://www.solar-electric.com/search/?q=clipper
https://www.solar-electric.com/midnite-the-kid-mppt-wind-hydro-charge-controller-with-clipper-option.html
http://midnitesolar.com/
I am not the person to talk to about this... Either the engineers at NAWS/Solar-Electric.com, or Midnite Solar directly (at least to get started).
Still not a fan wind turbines--But if you get (or DIY build) a good quality turbine, they can fill a void in dark weather (farther north, cloudy/raining regions, etc.).
And if this is lab anyway... I would suggest also looking at Flooded Cell Lead Acid batteries (8x 6 volt @ 200 AH "Golf Cart" batteries are cheap (both initial purchase, and if you test to destruction your corner cases--To replace). I would suggest you want a larger battery bank (more stable voltage, ability to take "hours" of charging energy) to gather data and test corner conditions without "wiping out" down stream electronics on the DC battery bus (or loss of RPM control on the turbine).
I would suggest that driving the turbine alternator with a variable speed drive would give you good laboratory conditions (stable output, easily repeatable conditions to test all of the "black boxes".
Testing the turbine itself--A bigger problem. Do you have a reliably windy location to test, tower options (30 feet or higher in non turbulent air, etc.)?
http://hint.fm/wind/
https://eerscmap.usgs.gov/uswtdb/
Not a lot of wind farms in the North East (your location)?
In the olden days, they used to run wind turbines and hang gliders by running on a 1 mile straight road next to the Half Moon Bay airport (south of San Francisco, on the coast).
It sounds like you are planning on doing a lot of qualification testing (not a bad idea, especially with small wind). But it is not going to be a cake walk.
-BillNear San Francisco California: 3.5kWatt Grid Tied Solar power system+small backup genset -
BB. said:One of the options with Alternators, is to use an MPPT type charge controller... Basically, Power = Voltage * Current. So, if you draw XX amps (max rated current) at 30 volts to charge your battery bank, with a PWM/Direct connect alternator, you can replace with an MPPT type controller (typically a modified Solar MPPT Charge Controller) and let the RPM of the turbine go higher, and you get 60 or more volts... and with P=V*I, current constant (max rated), but double the voltage, you double the power harvest (MPPT charge controller are typically buck mode down converting switching power supplies with >~95% efficiency (this can double your battery charging current).
But, like everything, it gets complicated. Midnite Solar is one company that has an integrated MPPT/Dump controller system. And like anything complicated, it is not cheap:
https://www.solar-electric.com/search/?q=clipper
https://www.solar-electric.com/midnite-the-kid-mppt-wind-hydro-charge-controller-with-clipper-option.html
http://midnitesolar.com/
I am not the person to talk to about this... Either the engineers at NAWS/Solar-Electric.com, or Midnite Solar directly (at least to get started).
Still not a fan wind turbines--But if you get (or DIY build) a good quality turbine, they can fill a void in dark weather (farther north, cloudy/raining regions, etc.).
And if this is lab anyway... I would suggest also looking at Flooded Cell Lead Acid batteries (8x 6 volt @ 200 AH "Golf Cart" batteries are cheap (both initial purchase, and if you test to destruction your corner cases--To replace). I would suggest you want a larger battery bank (more stable voltage, ability to take "hours" of charging energy) to gather data and test corner conditions without "wiping out" down stream electronics on the DC battery bus (or loss of RPM control on the turbine).
I would suggest that driving the turbine alternator with a variable speed drive would give you good laboratory conditions (stable output, easily repeatable conditions to test all of the "black boxes".
Testing the turbine itself--A bigger problem. Do you have a reliably windy location to test, tower options (30 feet or higher in non turbulent air, etc.)?
http://hint.fm/wind/
https://eerscmap.usgs.gov/uswtdb/
Not a lot of wind farms in the North East (your location)?
In the olden days, they used to run wind turbines and hang gliders by running on a 1 mile straight road next to the Half Moon Bay airport (south of San Francisco, on the coast).
It sounds like you are planning on doing a lot of qualification testing (not a bad idea, especially with small wind). But it is not going to be a cake walk.
-Bill
Categories
- All Categories
- 229 Forum & Website
- 137 Solar Forum News and Announcements
- 1.4K Solar News, Reviews, & Product Announcements
- 199 Solar Information links & sources, event announcements
- 898 Solar Product Reviews & Opinions
- 256 Solar Skeptics, Hype, & Scams Corner
- 22.5K Solar Electric Power, Wind Power & Balance of System
- 3.5K General Solar Power Topics
- 6.7K Solar Beginners Corner
- 1K PV Installers Forum - NEC, Wiring, Installation
- 2.1K Advanced Solar Electric Technical Forum
- 5.6K Off Grid Solar & Battery Systems
- 428 Caravan, Recreational Vehicle, and Marine Power Systems
- 1.1K Grid Tie and Grid Interactive Systems
- 654 Solar Water Pumping
- 816 Wind Power Generation
- 624 Energy Use & Conservation
- 620 Discussion Forums/Café
- 313 In the Weeds--Member's Choice
- 75 Construction
- 124 New Battery Technologies
- 108 Old Battery Tech Discussions
- 3.8K Solar News - Automatic Feed
- 3.8K Solar Energy News RSS Feed