Help With A Rigged Windmill Setup
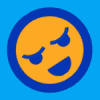
Grendergon
Registered Users Posts: 6 ✭✭
Hello All & Thank in advance for the help.
I rigged up a windmill cylinder that I resurrected from an old well on our land, using an old pump jack and other equipment I had laying around. I purchased a TEFC Leeson 24V 39 amp 1750 rpm electric motor to power the pump, and I am hoping to use the system to supply water to a garden about 1,100 horizontal feet away from a pond water source.
I have pretty minimal water requirements. There is a 1200 gallon tank at the garden, and water requirements are probably less than 200 gallons a day. With an average of 6 hours of light a day, this pump should be able to move 1,800 gallons a day.
I have hooked up 300ft of 1" diameter black poly pipe and successfully pumped water at ~5 gpm using the pump motor. However, two 12V car batteries (just for testing purposes) hooked in series (24V) went from fully charged to dead in less than 30 minutes of pumping.
My question is, what would be the best solar setup to help run this pump effectively. We can easily run it manually, (when water gets low, someone goes and turns the pump on). My thinking was two 300 watt, 24 v panels hooked up in parallel would be most effective? What about a pump controller? Any help appreciated...
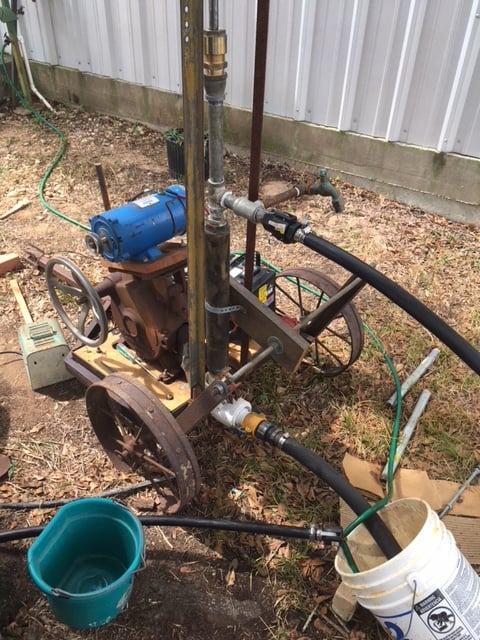
Comments
-
I would suggest that you get a DC Current Clamp DMM (really AC&DC Current Clamp Digital Multimeter)... Here is a "mid range" meter:
https://www.amazon.com/gp/product/B019CY4FB4
You need to know what the DC current to the motor is (and DC (and AC) current clamp meters make debugging power systems much easier).
A car battery is around 60-80 AH (at 20 hour rate)... And running dead in 1/2 an hour, would probably suggest a 30-60 amp DC current @ 24 volts (high discharge rates for FLA batteries, they have less than "rated" output current--And old batteries have less AH capacity too).
IF your motor needs 40 Amps @ 24 volts, then the minimum solar array (Vmp~30 volt panels):- 40 Amps Imp * 30 volts Vmp = 1,200 Watts of 60 cell solar panels
The issue is that solar panels are really "terrible" solar batteries. Their output voltage varies by almost a factor of 2x (from Vmp-hot days low voltage to Voc-cold high voltage on freezing days).
Normally, for a 24 VDC motor, a person would use a LCB (linear current booster) to limit high voltage to the motor, and in less than perfect sun, provide more current at lower DC bus voltage (current~torque, voltage~RPM). But LCBs are not common and, for the most part, are expensive (for DC pumping applications).
It is possible to use a DC to DC down converter to produce lower voltage/higher current for the motor (set output voltage to 20 VDC to run at slower RPM) but the converter will supply higher current to start/keep the motor turning.- Power = 20 volts * 40 amps = 800 Watts = 60 Vmp-array * 13.33 Amps-array
https://www.solar-electric.com/residential/solar-water-pumping/pump-controllers-current-boosters.html
https://www.ebay.com/sch/i.html?_from=R40&_trksid=p2540003.m570.l1312.R1.TR11.TRC2.A0.H0.Xd.TRS1&_nkw=dc+buck+converter&_sacat=0
"Slow pumping" is very common for off grid solar power systems... Changing the pulley diameter to reduce power on the motor...
Do you really need ~960 Watts (over ~1 horsepower) to pump this well (how deep is the well)?
"Solar friendly" solar submersible well pumps are typically in the $800 to $2,500 range (not cheap)...
https://www.solar-electric.com/residential/solar-water-pumping/submersible-and-well-pumps.html?nav_max_gpm=469
Many of these pumps are "solar friendly"--The have the LCB built into the pump (or pump controller on the surface).
I am pretty much out of my depth, but this should give you and idea of the issues with water pumping.
-BillNear San Francisco California: 3.5kWatt Grid Tied Solar power system+small backup genset -
Thanks a lot that was very helpful. The motor is indeed overkill...I couldn’t resist it because it was such a good deal. The dc step down converter seems like a very good solution, but if I understand, what you’re saying this would exchange speed to maintain the torque. Would it not be possible to experiment with the lowest possible amps necessary to run the pump? If I only put 18 amps into the motor and it still turned, how badly would I shorten the life of the motor? in that scenario, I would only need an array totaling 600 watts.
i am going to experiment a bit and see if I can increase the size of the pulley and lower the input of the watts. I have a battery charger where I can set the voltage, and can charge up to 15 amps. I may hook this directly to the motor and see what happens. -
Re pump jack motor: Your motor amp draw is load dependent. Under no load I doubt if it would pull more than an amp or so on a 24 volt battery (24watts) perhaps less. Assuming you have an 1 7/8 cylinder you should pump about a cup or so per stroke. The deeper the surface of the water the more power will be required. Perhaps the drive pulley you’re using is too big. The smaller the sheave the better as long as you have adiquate wrap, and a flexible belt which is not too tight. Gates energy saver belts with notches on the outside work well but flat belts are even more efficient. . A smaller drive pully will pump slower and it will pump with less power. For testing you can put an old fashioned car or tractor 60 amp ammeter in series with the motor lead to observe the current peaks, fluctuations etc. the jack should run about 15 to 25 strokes per minute max. If the leathers are in good order it should work well as long as you don’t let it sit stalled when adiquate power is not available hence the need for a current booster or controller of some kind to get it going first thing in the morning. A fuse or breaker should also be used to protect the motor. Sometimes a spring above the stuffing box or weight on a walking beam can be used to even out the current pulses by storing energy on the down stroke to be reclaimed on the lift. The stuffing box should only be tightened by hand so a small well of water collects in the Box nut to lubricate the polish rod if lifting water above the well head. Permanent magnet motors are quite efficient and once dialed in should only be slightly warm to the touch when running under load. As previous comments say the total water lift will dictate the current requirement. Bear in mind the pump is positive displacement and the water line must never be blocked with ice or a valve that can be shut off or damage may be the result.
-
What Niki says (and with very useful facts on the pump itself).
To slow the pump down, smaller drive pulley on motor and/or larger pulley on pump. Too small of motor pulley, and the belt may slip (not enough contact area) or wear quickly (to much flexing/bending around small pulley).
Knowing a bit more about the DC motor wiring (different field coil connections give different motor performance curves):
https://electrical-engineering-portal.com/4-types-of-dc-motors-and-their-characteristics
-Bill
PS: Keep a eye on the brushes and commutator... Typically they will last something like 5,000 hours of runtime (very rough number). At that point the brushes may need changing and/or the commutator serviced.Near San Francisco California: 3.5kWatt Grid Tied Solar power system+small backup genset -
I have several spare 60 amp ammeters from an old Jeep. That is an excellent idea to gauge the load on the motor, particularly on the startup.
I intuitively did exactly what you suggested with the stuffing box...hand tight.
Furthermore I am especially interested in what you said about the flat belt. I wanted to keep the original flywheel which was heavy cast iron (weighs fifteen to twenty lbs) but took it off bc the paper pulleys and flat belts were not easy (or cheap) to locate. Do you suppose the weight of the flywheel was designed to help conserve momentum on the stroke as you suggested with the spring? Higher startup costs would then be paid back by longer, more efficient run time...just like a windmill!
as for the other tips tips and advice, I will keep y’all posted. Thanks so much. -
Probably... Windmills do not have a lot of starting torque... The flywheel will help "ride through" any back pressure spikes on the pump.
Also, even out power strokes (stores energy as flywheel speeds up during pump "recovery stroke" and slows the flywheel as the pump loads up on water/back pressure/lift rod weight/etc.).
-BillNear San Francisco California: 3.5kWatt Grid Tied Solar power system+small backup genset -
I assumed perhaps incorrectly that your motor is a permanent magnet type. If it has a shunt field things I said may not be entirely accurate and the field coil should be protected with an inline fuse as overvoltage can damage same. If it is indeed permanent mag you should be able to run it on a small 6 volt battery at 1/4 speed and 1/16 power. Permanant mag motors will reverse direction when the polarity is reversed. A shunt wound motor will run in the same direction even if the battery polarity is reversed.
Your pump jack is designed to run in one direction and usually is indicated by an arrow on the gear box or flywheel. If run backwards the internal oiling system may not work properly. The best oil is zero weight non detergent not gear oil.
A great source for hard to find things like Teflon graphite packing, flat belt material etc is a huge hardware store in Los Angeles. They have just about everything known to man in stock and typically ship within 60 minutes of order. It’s called McMaster-Carr Corp. Their paper catalog is a thing of beauty with over 5000 pages and literally millions of items all in stock.
Your pump jack should put out about 1 1/2 GPM or so with a 1 7/8 cylinder. If you’re getting 5 GPM it’s running way too fast causing unnesessary wear and tear on the gear box, polish rod and other moving parts. Enjoy
-
One more thing re your flywheel. I would use it even if made for a flat belt and you’re using a V belt, it will work fine with all that surface area and won’t slip with a v belt however if you can’t get enough wrap around the small drive pully you may need to increase the distance between the flywheel and the motor or fashion some type of spring loaded idler pully.
-
Amazing, thank you...
-
Actually a 2.5 inch cylinder measuring the inside diameter.
-
*SOLVED*
well, I took the advice of everyone on this forum and the pump is working great. I finally had Time to mess with it this morning.
The 24V perm mag motor is drawing about 4 amps hooked up to a single 12v car battery. That means my power requirements are way less than I thought...on the order of 70-80 watts. At that rate (4 amps) the pump is still running a bit fast (2.5 inch cylinder at 20 strokes a minute) but I have put the smallest pulley I can on and will use a fancy current regulator that my brother has from work to slow it down a bit more.
in conclusion, this satisfies for me that a retrofitted windmill cylinder can be used to pump water very efficiently over distance (12-1300 feet) as long as the head is not too much (the only limiting factor is the stuffing box which can’t take much more than 25 psi)
thanks all
Categories
- All Categories
- 228 Forum & Website
- 136 Solar Forum News and Announcements
- 1.4K Solar News, Reviews, & Product Announcements
- 199 Solar Information links & sources, event announcements
- 898 Solar Product Reviews & Opinions
- 256 Solar Skeptics, Hype, & Scams Corner
- 22.5K Solar Electric Power, Wind Power & Balance of System
- 3.5K General Solar Power Topics
- 6.7K Solar Beginners Corner
- 1K PV Installers Forum - NEC, Wiring, Installation
- 2.1K Advanced Solar Electric Technical Forum
- 5.6K Off Grid Solar & Battery Systems
- 428 Caravan, Recreational Vehicle, and Marine Power Systems
- 1.1K Grid Tie and Grid Interactive Systems
- 654 Solar Water Pumping
- 816 Wind Power Generation
- 624 Energy Use & Conservation
- 619 Discussion Forums/Café
- 312 In the Weeds--Member's Choice
- 75 Construction
- 124 New Battery Technologies
- 108 Old Battery Tech Discussions
- 3.8K Solar News - Automatic Feed
- 3.8K Solar Energy News RSS Feed