How many LiFePo4s in a string for 48V system?
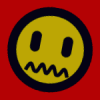
mattg
Registered Users Posts: 17 ✭✭
Hi, I'm about to
purchase an LiFePo4 bank for my 48V off grid setup, and as I've not worked with LFP
before, I'd really appreciate advice on how I should size it to work with my existing setup.
My
budget is around 8-10k, so I'm looking at one string of CALB CA400
cells. I know there is some advice out there to skip top balancing, but I'm going
to err on the side of caution and also purchase some form of BMS in the
unlikely case a cell goes bad - I need to get many years out of this purchase so I don't mind paying a little extra for insurance...
My
2 Outback inverters (parallel slave config) can take up to 68V DC input each, according to the
specs. So I figure it makes sense to get as many CA400s in the
string as I can, without allowing the charge controllers (3x Midnite
Classic 150s) or inverter charging outputs to get too close to 68V. So lets say I
set the CCs to stop charging at 65V, allowing a few volts for margin.
Standard
procedure seems to be to charge each CALB LFP cell no higher than 3.6V,
and the BMSs I've been looking at (Clean Power Auto and EV Power) seem
to have the threshold of each module fixed at that level without the ability to adjust.
So
18 cells x 3.6V max balance voltage = 64.8V, and if I set my charge
controllers to stop charging at 64V, cells should ideally get a charge
of about 3.55V each, and the BMS may never kick in - but it would be there as a backup in case something were to go wrong during charging.
But,
seeing as the usable wattage of CALB LFP cells seems to be when they
are between 3V and 3.35V: assuming there is a BMS that would let me set my own voltages, I'm wondering if I should look at adding an
extra cell.
If I could find a setup that would let me set a balance voltage of 3.4V for example: 19 cells x 3.4V balance = 64.6V, and again I would stop charging at 64V.
If I could find a setup that would let me set a balance voltage of 3.4V for example: 19 cells x 3.4V balance = 64.6V, and again I would stop charging at 64V.
As
well as getting more kWh I wouldn't be pushing the cells as hard during
the charge cycle, which I'd hope would translate to an increase in the
number of discharge cycles...
Not sure I'd need a configurable high voltage cutoff output for backup relays to isolate the charge
controllers and inverter charger outputs, in case the voltage seen by the
bank went over 66V for example, as a "backup backup", but would be good to know if a unit has this as well. Or, I'd be open to the idea of just monitoring each cell instead of having balancing circuitry for each, and using a high voltage cutoff if any cell went over a threshold.
As
I've not used LFP before I may be missing something obvious, so I'd
appreciate any correction, and/or feedback along the lines of whether or
not using 19 cells is feasible etc. (I recall reading of others using 17 CA400 cells for a "48V" setup like mine, not sure why they didn't go 18 or 19).
And if feasible/worthwhile, if anyone can recommend a BMS system that would be suitable (and relays if not included in the system). Doesn't look like I could configure any of these kind of settings with either of the BMS systems mentioned above.
And if feasible/worthwhile, if anyone can recommend a BMS system that would be suitable (and relays if not included in the system). Doesn't look like I could configure any of these kind of settings with either of the BMS systems mentioned above.
Comments
-
If you want my 2c, for your first lithium system i would keep it simple. Std 16cell configuration, top balance, routine charges to a bit less than 100%, no bms. Lithium or no lithium, solar systems work best when kept simple. They spend most of their time in the upper SOC ranges, so limiting overcharge is the key to happiness there. External LVD, automatic cell balancers, and the like all bring with it a whole range of complications, that you just dont need. Yeah i know you know that theres a range of views on this, but you asked and thats mine.
If peice of mind is what you are after then why not just add a cell level monitoring system, with a loud hooter. We can point you to some ideas there.
How are you going to import them? Slipping them in with your personal effects?! Might be good to check up on any restrictions on the container contents!
1.8kWp CSUN, 10kWh AGM, Midnite Classic 150, Outback VFX3024E,
http://zoneblue.org/cms/page.php?view=off-grid-solar -
Thanks zoneblue! Appreciate the advice, and I will end up going with fewer cells if it turns out there are no BMS systems that can support what I'm trying to do. (Checked with the shipping company by the way and they are fine with LFP cells being in the container).
However I'm the engineer/nerd/tinkerer type, a bit of complexity appeals to me, and, I'm not going to go without some degree of an automated failsafe mechanism to prevent over- and under-voltage situations - something like a warning buzzer wouldn't be an option for me, as I need the system to be able to take care of things while I'm not present.
If anyone has had experience with any BMS systems that would allow me to achieve that level of piece of mind, while at the same time wringing the most potential out of a single string of 400AH LFP cells with a 65V limit, would very much like to hear your ideas. I'm not looking for a BMS system for balancing, as much as for monitoring individual cells and shutting the system down if one of them gets out of order - or if the bank gets over/under my customized threshold. -
Hi mattg,
Sounds like you are approahing things the right way, here is my two cents for what it is worth.
One point about running at the higher end of the inverter's voltage range is how does this affect the efficiency and life of the inverter and the charge controllers?
I don't think you need to charge above 3.45 volts/cell. I usually charge to 3.4 volts/cell and once a week to 3.45 volts/cell to reset my SOC counter. 3.4 volts/cell should give you a long life and if you set the end current to C/50 will get more than a 90% full battery.
Other points to maximise the life of the battery are as a guide to keep the charge current to less than C/4 and discharge current to less than C/2.
May I ask what your maximum output load, maximum charge current and dialy power requirments is likely to be.
I agree with Zoneblue about the Battery Monitoring/Management, but if you are away from the system more automation is called for.
I have designed and developed a flexible BMS system for my LFP battery, details can be found here https://github.com/simat/BatteryMonitor. I have recently added the facility of monitoring the battery remotely via a web browser which is not yet in the documentation. There is also a crowd in Australia that make a BMS which a number of folk use but I cant find the details.
Simon
Off-Grid with LFP (LiFePO4) battery, battery Installed April 2013
32x90Ah Winston cells 2p16s (48V), MPP Solar PIP5048MS 5kW Inverter/80A MPPT controller/60A charger, 1900W of Solar Panels
modified BMS based on TI bq769x0 cell monitors.
Homemade overall system monitoring and power management https://github.com/simat/BatteryMonitor
-
Thanks Simon, appreciate your comments.
A higher voltage of 65V regularly seen by the Outback inverters potentially affecting efficiency / lifespan also crossed my mind. I will bounce that off outback sometime over the next day or two and report the answer here.
I'll be sure to check out your battery monitor code at GitHub. Thanks!
I can feed up to 6kW of inverter with the battery bank (2x VFX3048E). I expect to sometimes use close to all of that capacity but typically less than half. Max charge- whatever 3x Classic 150 CCs can provide (on phone so not easy to double check right now). Daily usage: 10 to 15kWh. More capacity would be nice to cover bad weather days, but the budget is what it is.
Was the Australian company you mention these guys? http://www.ev-power.com.au
They are one of the two companies I mentioned above, and I've directed them towards this post, as I'd like to know it they can recommend any modifications to their off the shelf system that might work for me. -
If you will be running without a BMS, but with a dependable CC that will limit the string voltage, I would definitely recommend that you bottom balance rather than top balance. As long as you do not try to charge the string to higher than 80% SOC (somewhere around 3.2-3.3V ? ) there is no need to top balance.
Trying to charge the cells to 100% SOC is just not a good idea as it is easy to go to far and damage the battery AND because resting at 100% SOC will cause the battery to degrade over time much faster than resting it at 80%SOC maximum. This is totally unlike the management strategy for lead acid batteries.
The flat portion of the discharge curve where most of the energy will be delivered at least stress on the battery will be close to 3.2 VPC.
So a 16 cell bank would have an operating voltage (open circuit) of about 51.2V.
SMA SB 3000, old BP panels. -
mattg said:I recall reading of others using 17 CA400 cells for a "48V" setup like mine, not sure why they didn't go 18 or 19.
--vtMaps
4 X 235watt Samsung, Midnite ePanel, Outback VFX3524 FM60 & mate, 4 Interstate L16, trimetric, Honda eu2000i -
mattg said:
I can feed up to 6kW of inverter with the battery bank (2x VFX3048E). I expect to sometimes use close to all of that capacity but typically less than half. Max charge- whatever 3x Classic 150 CCs can provide (on phone so not easy to double check right now). Daily usage: 10 to 15kWh. More capacity would be nice to cover bad weather days, but the budget is what it is.Was the Australian company you mention these guys? http://www.ev-power.com.au
The company I was thinking of is http://www.batrium.com/, looks like you can use any number of cells so might be useful for your proposed setup, My monitor/manager should also work with any number of cells.
Simon
Off-Grid with LFP (LiFePO4) battery, battery Installed April 2013
32x90Ah Winston cells 2p16s (48V), MPP Solar PIP5048MS 5kW Inverter/80A MPPT controller/60A charger, 1900W of Solar Panels
modified BMS based on TI bq769x0 cell monitors.
Homemade overall system monitoring and power management https://github.com/simat/BatteryMonitor
-
inetdog said:Trying to charge the cells to 100% SOC is just not a good idea as it is easy to go to far and damage the battery AND because resting at 100% SOC will cause the battery to degrade over time much faster than resting it at 80%SOC maximum.
From page 5 of this paper http://www.researchgate.net/publication/257224739_Calendar_aging_of_a_graphiteLiFePO4_cell
"This decrease becomes much more substantial for the
cells stored at 60°C for which the capacity fade percentages of the cells (~155 to 188 days of
aging) are about 18.1%, 23.7%, and 26.9% for SOC nom 30%, 65% and 100%, respectively."
Simon
Off-Grid with LFP (LiFePO4) battery, battery Installed April 2013
32x90Ah Winston cells 2p16s (48V), MPP Solar PIP5048MS 5kW Inverter/80A MPPT controller/60A charger, 1900W of Solar Panels
modified BMS based on TI bq769x0 cell monitors.
Homemade overall system monitoring and power management https://github.com/simat/BatteryMonitor
-
inetdog said:If you will be running without a BMS, but with a dependable CC that will limit the string voltage, I would definitely recommend that you bottom balance rather than top balance. As long as you do not try to charge the string to higher than 80% SOC (somewhere around 3.2-3.3V ? ) there is no need to top balance.
Trying to charge the cells to 100% SOC is just not a good idea as it is easy to go to far and damage the battery AND because resting at 100% SOC will cause the battery to degrade over time much faster than resting it at 80%SOC maximum. This is totally unlike the management strategy for lead acid batteries.
The flat portion of the discharge curve where most of the energy will be delivered at least stress on the battery will be close to 3.2 VPC.
So a 16 cell bank would have an operating voltage (open circuit) of about 51.2V.
But but still want a BMS of some description for monitoring purposes to be able to pull the plug if a cell gets out of bounds either high or low, or the overall bank gets too high or low due to an unlikely fault in the CC or charger.
Like Simon I also wonder if there are urban myths associated with the instructions to avoid sitting at 100% SOC that are out there. But as you say, I only need to be concerned about staying in the flat portion of the discharge curve in order to use the majority of the charge in the cells, so I'm planing on using conservative high/low cut off values - I don't see the need to charge to 100% in my setup. Which is why I'm looking at 19 cells - if I always stay in the flat discharge region, I figure I can maximize the overall usable power in a single string bank with this approach.
-
vtmaps said:mattg said:I recall reading of others using 17 CA400 cells for a "48V" setup like mine, not sure why they didn't go 18 or 19.
--vtMaps -
karrak said:
Am I right in thinking that 3 Classic 150s at 64 volts will supply ~240A (~15kW). Is your solar array that size?
-
karrak said:
Was the Australian company you mention these guys? http://www.ev-power.com.au
The company I was thinking of is http://www.batrium.com/, looks like you can use any number of cells so might be useful for your proposed setup, My monitor/manager should also work with any number of cells.
Simon
Had a quick look, and my initial thoughts are that this might be exactly what I'm looking for! I'll read up some more and get in contact with them. Much appreciated Simon.
-
Good Luck to you all ! I do mean it. We are here for insurance inspections. Just did one last month."we go where power lines don't" Sierra Nevada mountain area
htps://offgridsolar1.com/
E-mail offgridsolar@sti.net -
Top or bottom probably doesnt matter too much. As far as i can tell Lithium dislikes high and low states of charge about the same, so staying away from either is what you would call a good thing. However in practical day to day life off grid, in milder climates and in systems not having generators, trust me, you will learn to jelously guard your SOCs to the point where higher is ALWAYs better. This is because you dont know when teh next 5 day stretch of bad weather is coming, and thus keeping high "inventory" is just instinctual. Its the one good thing about lead chemistry in that 100% SOC is all round nice.
If you do go down the electronics route, heres the concerns as i see them:
1. the electronics introduces additonal failure points. You dont have to look far on line to find people who have had expensive lessons with LFP, particalarly "balancing" systems that unbalance badly upon failure.
2. difficulty in reliably interupting inverter: your options there;
- expensive vacuum/argon filled relays
- relying on the inverters aux disable sytems
- probably the best option is the carling breakers than have an aux trip. (see midnite website)
3. difficulty interupting the CC. In addition to the above issues, you cant isolate the CC from the battery without isolating the PV from teh CC. So that leaves you with AUX type routes for the HVD.
1.8kWp CSUN, 10kWh AGM, Midnite Classic 150, Outback VFX3024E,
http://zoneblue.org/cms/page.php?view=off-grid-solar -
vtmaps said:mattg said:I recall reading of others using 17 CA400 cells for a "48V" setup like mine, not sure why they didn't go 18 or 19.
--vtMaps
inMichigan42 SP-335's (14.1kw) -> 4 FLEXmax 80's / 5kWh using 17 CA100 CALB cells / FLEXnet DC / MATE3 -> 2 Radian GS8048A and watched over by Vantage Pro 2+ PWS all running since 2015 -
inMichigan said:I went with 17 cells. I would have used 18 (which would have fit nicely on the charging side), but my Outback Radians could only have their low voltage cutoff set as high as 48 Volts. I was nervous at that volt/cell level.inMichigan
-
zoneblue said:Top or bottom probably doesnt matter too much. As far as i can tell Lithium dislikes high and low states of charge about the same, so staying away from either is what you would call a good thing.
-
zoneblue said:If you do go down the electronics route, heres the concerns as i see them:
1. the electronics introduces additonal failure points. You dont have to look far on line to find people who have had expensive lessons with LFP, particalarly "balancing" systems that unbalance badly upon failure.
2. difficulty in reliably interupting inverter: your options there;
- expensive vacuum/argon filled relays
- relying on the inverters aux disable sytems
- probably the best option is the carling breakers than have an aux trip. (see midnite website)
3. difficulty interupting the CC. In addition to the above issues, you cant isolate the CC from the battery without isolating the PV from teh CC. So that leaves you with AUX type routes for the HVD.
2) had a look at the Midnite site, saw a lot of manually operated breakers, but didn't see any kind of breaker that could be triggered by the output from a unit such as the Batrium product.
3) as per above. Their "birdhouse" product seems like it would isolate the PV strings from the CCs - but again only a manually operated device?
Looks like the Batrium unit is going to be the way forward for me here - IF I can find devices that it can control electrically, that will switch out the PV string from the CCs, and the inverter/charger from the battery bank.
Thanks again to all for the advice!
-
The bird house uses the breakers im talking about. Ill try to find the link.
Edit: here:
http://www.midnitesolar.com/productPhoto.php?product_ID=578&productCatName=Breakers&productCat_ID=16&sortOrder=3&act=p
Those things are tough as boots. Worth every penny.
1.8kWp CSUN, 10kWh AGM, Midnite Classic 150, Outback VFX3024E,
http://zoneblue.org/cms/page.php?view=off-grid-solar -
mattg said:Looks like the Batrium unit is going to be the way forward for me here - IF I can find devices that it can control electrically, that will switch out the PV string from the CCs, and the inverter/charger from the battery bank.
On a system I made for a friend I used a latching relay to disconnect the panels from the CC in the event of a HVD fault . Shutting down the inverter is more of an issue. Not wanting to use a large DC relay I thought about simulating an earth fault on the mains side of the inverter and using the earth leakage breaker to shut down the inverter load, or to shut down the inverter by shutting down the power supply of the control electronics in the inverter as suggested by the inverter manufacture, or maybe stopping the microprocessor controlling the inverter. In the end I decided not to bother on both mine and my friend's system as in our situation someone will be around if the battery is being drained quickly. When I am away from home it is only the fridge, my router and a few other electronic gadgets that are left running which would take over a week to flatten a full battery. If I am away for any period of time I can look at my battery status remotely and if there is a problem phone one of the neighbours and ask them to take action.
Thought I would add the warning about not modifying any circuitry in any inverter unless you really know what you are doing and make sure you comply with any regulations if you do anything on the mains voltage side of the inverter.
Simon
Off-Grid with LFP (LiFePO4) battery, battery Installed April 2013
32x90Ah Winston cells 2p16s (48V), MPP Solar PIP5048MS 5kW Inverter/80A MPPT controller/60A charger, 1900W of Solar Panels
modified BMS based on TI bq769x0 cell monitors.
Homemade overall system monitoring and power management https://github.com/simat/BatteryMonitor
-
His VFX3048E's have a jumper on the connector panel that can be used as a on /off control for the inverters, any relay will control them.
-
mattg said:inMichigan said:I went with 17 cells. I would have used 18 (which would have fit nicely on the charging side), but my Outback Radians could only have their low voltage cutoff set as high as 48 Volts. I was nervous at that volt/cell level.inMichigan
So, if you have
#cells 48V/#
16 3.00 cell would be ok
17 2.82 ok
18 2.66 I know of one guy who bottom balanced near here
19 2.53 Would the cells be damaged/destroyed? Some would say yes.
Of course if you have an additional LVD (sensor, power supply for the contactor, and high current contactor), then, you can protect your cells independent of the Radian's safe-guards.
I bottom balance and have removed by Mini-BMS boards. I currently do not have any additional LVD hardware other than the Radian's own logic. I choose 17 cells thinking that during their life, if 1 should fail, I could drop back to 16 and not get into issues about replacing a single cell. It was mean to be a spare that I kept on the side... and then I got thinking, why not include it in the bank, bumping up the stored energy!.
inMichigan42 SP-335's (14.1kw) -> 4 FLEXmax 80's / 5kWh using 17 CA100 CALB cells / FLEXnet DC / MATE3 -> 2 Radian GS8048A and watched over by Vantage Pro 2+ PWS all running since 2015 -
inMichigan said:If the system ever crashed, draining the batteries towards failure, the Radian will not disconnect until it 36 to 48 V DC. That's the limit of that parameter in the menu.
Categories
- All Categories
- 229 Forum & Website
- 137 Solar Forum News and Announcements
- 1.4K Solar News, Reviews, & Product Announcements
- 199 Solar Information links & sources, event announcements
- 898 Solar Product Reviews & Opinions
- 256 Solar Skeptics, Hype, & Scams Corner
- 22.5K Solar Electric Power, Wind Power & Balance of System
- 3.5K General Solar Power Topics
- 6.7K Solar Beginners Corner
- 1K PV Installers Forum - NEC, Wiring, Installation
- 2.1K Advanced Solar Electric Technical Forum
- 5.6K Off Grid Solar & Battery Systems
- 428 Caravan, Recreational Vehicle, and Marine Power Systems
- 1.1K Grid Tie and Grid Interactive Systems
- 654 Solar Water Pumping
- 816 Wind Power Generation
- 624 Energy Use & Conservation
- 619 Discussion Forums/Café
- 312 In the Weeds--Member's Choice
- 75 Construction
- 124 New Battery Technologies
- 108 Old Battery Tech Discussions
- 3.8K Solar News - Automatic Feed
- 3.8K Solar Energy News RSS Feed