Adding Grid Tie System to Subpanel on XW System
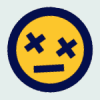
krsmichael
Registered Users Posts: 19 ✭
I have talked to Xantrex about this. They said yes, I can do it. I would like to get a few opinions here. I have a 9k XW System and it drives a 200 amp sub panel. The Xantrex provides a max of 60 amps to the panel. I would like to add a small grid tie system to that sub panel, ~15 amps. Xantrex says yes, and that the grid tie would continue to provide power on the sub panel in the even of a grid down.
Any insight on this setup?
Any insight on this setup?
Comments
-
Mini Grid and AC coupling search will yield all kinds of Information.
https://www.google.com/url?sa=t&rct=j&q=&esrc=s&source=web&cd=4&ved=0CDkQFjAD&url=https%3A%2F%2Fwww.altestore.com%2Fmmsolar%2Fothers%2FXW_AC_Coupling_of_Inverters.pdf&ei=yuKKVYb2I8P7sAWwpbyoBQ&usg=AFQjCNE8vxb_8bmpCEc5ZB57x_tJwUuQUA&bvm=bv.96339352,d.b2w&cad=rja -
You need to know the conductor size of the sub panel.
Most sub panels in homes are under rated to the actual sub panel.
(I.E) hypothetically if you have a 100 or 125amp sub panel, but if the conductor run to that sub panel is6awg cu THHN 90*c you will run I to problems if it's a 60amp inverter.
The conductor has to be 120% greater than the supplied breaker at main panel in order to back feed solar through it.
(I.E) I have a 125amp sub panel at one of my projects. The conductor however is only 75amp maximum. The breaker at main is 50amp, so I am only allowed 10amps of back feed according to the back feed of the breaker/conductor.
I am also confused as to what you are suggesting. Are you back feeding 60amps, or 15amps of solar?
Also if it's a 60 amp inverter you are already exceeding the 120% back feed rule, maximum allowable is 40amp on a 200amp main, unless you derate the 200amp main service breaker to 175, which you probably won't find, because eaton, Siemens, square d home line don't make a 175amp for BR style stabbings. -
The one potential problem is how the particular GTI you get will interact with the Xantrex. If, during a grid outage, your total load should drop below the 15A the GTI is providing, the Xantrex will have to either order it to throttle down (for which there is no standard) or cause it to shut down completely by raising the Xantrex' own output frequency beyond the acceptable tolerance of the GTI.
SMA SB 3000, old BP panels. -
The one potential problem is how the particular GTI you get will interact with the Xantrex. If, during a grid outage, your total load should drop below the 15A the GTI is providing, the Xantrex will have to either order it to throttle down (for which there is no standard) or cause it to shut down completely by raising the Xantrex' own output frequency beyond the acceptable tolerance of the GTI.
If it's an XW-NA hybrid inverter, it shouldn't be a problem. The OP hasn't disclosed if it is hybrid or just standard XW.
I agree with what you stated. I am however also concerned with un regulated voltage rise. When 2 inverter types are working simultaneously. Both inverters are always trying to sync up to the other sine wave. It works Duplication of that frequency. Each inverter will function to step up voltage, just like voltage rise occurs with GTI accept this type of voltage rise is more accelerated.
It can actually void warranties with some inverter manufacturers if the voltage exceeds 255~261V. -
Blackcherry04 wrote: »Mini Grid and AC coupling search will yield all kinds of Information.
https://www.google.com/url?sa=t&rct=j&q=&esrc=s&source=web&cd=4&ved=0CDkQFjAD&url=https%3A%2F%2Fwww.altestore.com%2Fmmsolar%2Fothers%2FXW_AC_Coupling_of_Inverters.pdf&ei=yuKKVYb2I8P7sAWwpbyoBQ&usg=AFQjCNE8vxb_8bmpCEc5ZB57x_tJwUuQUA&bvm=bv.96339352,d.b2w&cad=rja
Thank you for that most excellent link. I will read that tomorrow. -
SolarPowered wrote: »I am however also concerned with un regulated voltage rise. When 2 inverter types are working simultaneously. Both inverters are always trying to sync up to the other sine wave. It works Duplication of that frequency. Each inverter will function to step up voltage, just like voltage rise occurs with GTI accept this type of voltage rise is more accelerated.
It can actually void warranties with some inverter manufacturers if the voltage exceeds 255~261V.
There may still be some interaction between the output of the battery inverter and the output of the GTI inverter, but it will be minimal if the wires are large enough and the battery inverter has a low output impedance.
SMA SB 3000, old BP panels. -
One of the inverters in the mix MUST be operating in stand-alone mode, controlling its own output voltage and frequency.
Micro inverters aren't standalone and they tend to have the issue of Voltage rise. Which requires longer length conductors/trunk cable to regulate the rise between micro inverters, both ABB and Enphase call this out in the trunk cable installations.
Voltage rise is one of those phenomenons that happens with GTI's. Voltage rise happens when you engineer to max out inverters for conditions of winter months.
(I.E) If I use LG 300 panel that produces 279 watts, enphase inverter which makes 240V @ 1 amp = 240 watt continuous, but inverter can produce 250. At peak it will deliver 250V, not 240V, as an instance of voltage rise.
Hypotheticlly If I use a 3000watt string inverter, and I install 3300watts DC panels, and DC string amps are at maximum allowable, a string inverter will produce up to 262V because voltage can no longer be down converter.
Now if you have 2 inverters "islanding" one GTI, and one OGI, the phenomenon occurrs where the voltage you can measure at point of inverters can be lower, then at the point of the distribution panel because the event allows for voltage concentration.
-
SolarPowered wrote: »
Micro inverters aren't standalone and they tend to have the issue of Voltage rise. Which requires longer length conductors/trunk cable to regulate the rise between micro inverters, both ABB and Enphase call this out in the trunk cable installations.
Voltage rise is one of those phenomenons that happens with GTI's. Voltage rise happens when you engineer to max out inverters for conditions of winter months.
(I.E) If I use LG 300 panel that produces 279 watts, enphase inverter which makes 240V @ 1 amp = 240 watt continuous, but inverter can produce 250. At peak it will deliver 250V, not 240V, as an instance of voltage rise.
Hypotheticlly If I use a 3000watt string inverter, and I install 3300watts DC panels, and DC string amps are at maximum allowable, a string inverter will produce up to 262V because voltage can no longer be down converter.
Now if you have 2 inverters "islanding" one GTI, and one OGI, the phenomenon occurrs where the voltage you can measure at point of inverters can be lower, then at the point of the distribution panel because the event allows for voltage concentration.
Sorry, but voltage rise with multiple microinverters is just the ordinary voltage drop across the trunk cable and the additional wiring that connects to the grid.
You would get exactly the same effect from one 1000W string inverter as you would from five 200W microinverters.
You have to size the wire to carry the amount of current that the inverter(s) will generate no matter what kind of inverters you use or how many.
It has nothing to do with each inverter trying to outdo the rest (or any such explanation.)
As for this:Now if you have 2 inverters "islanding" one GTI, and one OGI, the phenomenon occurrs where the voltage you can measure at point of inverters can be lower, then at the point of the distribution panel because the event allows for voltage concentration.
SMA SB 3000, old BP panels. -
Sorry, but voltage rise with multiple microinverters is just the ordinary voltage drop across the trunk cable and the additional wiring that connects to the grid.
You would get exactly the same effect from one 1000W string inverter as you would from five 200W microinverters.
You have to size the wire to carry the amount of current that the inverter(s) will generate no matter what kind of inverters you use or how many.
It has nothing to do with each inverter trying to outdo the rest (or any such explanation.)
This is incorrect. The first inverter in the trunk cable accepts the initial voltage drop from length of conductor from the distribution panel to the trunk cable array, but once all inverters are in sync per their 8 cycle algorithm voltage drop along the trunk cable means almost nothing. The length run between micro inverters is moot, the voltage drop is less than .0047% per 3.5' between inverters. AC sine wave is non linear, not linear as DC currents are. This means voltage travels both directions along the trunk cable. Because ac current flows both directions and causes voltage concentration through out the cable. CEC rated efficiency allows for a 2% voltage rise with an 8 cycle algorithm per second, in order to maintain efficiency. This is also because the amp "limit" is 1amp for (1) M250 micro inverter. Once the amperage maxes at 1amp at 240watt continous, the inverter in order to meet 250watt the voltage increases per cycle upto 250V, unless the grid voltage is higher than 250 "hypothetical" 255V, then the 8 cycle algorithm will shift more volts and reduce amps to compensate, for the grid voltage.
According to the specs of an enphase micro inverter M250 if it were to use a solar panel greater than 285wp, because of voltage rise, would void the warranty of the XW inverter. The M250 produces 1 volt greater than the XW at 264V, the XW maximum allowable is 263V. The voltage specs have to match identically if you want to max out the grid tied inverter(s) to the XW. If not the panel size is limited for micro inverters, for string inverters the array size is limited. Attachment not found.
Attachment not found.As for this: , I really do not understand what you are trying to say. The voltage can only be lower if there are loads connected along the way. Voltage difference between ends of a wire is IxR. Period.
I believe you misunder stood what I said, if so I apoligize.
Lets take a hypothetical situation.
If the grid tied system meters 255V, and the XW systems meters 254V, lets say conductor runs to distribution are 80' (equal distance to distribution) sized to the appropriate conductor size for minimal voltage drop. The distribution panel should meter 254.4V. -
SolarPowered wrote: »
I believe you misunder stood what I said, if so I apoligize.
Lets take a hypothetical situation.
If the grid tied system meters 255V, and the XW systems meters 254V, lets say conductor runs to distribution are 80' (equal distance to distribution) sized to the appropriate conductor size for minimal voltage drop. The distribution panel should meter 254.4V.
And as for the Enphase trunk cable, the IR drop along the cable will be whatever it is based on the current flowing at each point along the cable. The output of each microinverter will be exactly what is present at its terminals with that current flowing. The only reason for the micro to actively try to increase or decrease the voltage would be if the inverter nearest to the distribution end of the trunk measures the voltage and tells the other micros on the trunk cable what their output should be, and they then correct that to be able to deliver full power. A normal GTI, or a set of micros running a normal GTI output stage, will just deliver the current needed and not care about the voltage as long as it is within limits.
My impression is that you either do not understand how this all works or are doing a very poor job of explaining it.SMA SB 3000, old BP panels. -
And just why should the XW meter 254 while the GTI meters 255? The only reason for that to happen would be that power is flowing from the distribution panel to the XW rather than the opposite. That means that the XW would be in charge mode rather than sell mode.
In order for GTI's to maintain the efficiency thresh hold above 95%, unlike the XW at 93%. Voltage has to rise per 8 cycles of algorithm in order to maintain conversion efficiciency. There is no throttle back on GTI's, in the case of micro inverters if you use a panel that exceeds 285wp for an M250 micro inverter, and its at peak insolation, in order to achieve its optimal rated efficiency the voltage has to go up. The only throttle back is max watts out, but that doesn't mean that the conversion ratio between volts/amps can't change.
Prior to installing solar systems on homes. I take 3 metered tests. one at 9am, one at 12noon, one at 5pm. Grid voltage seems consistent with no significant rise. After I install solar I've noticed with larger panels with micro, or higher voltage larger arrays for string, at peak insulation voltage rises anywhere from 5 to 10 volts, at maximum watts out.
Then there ar einstances where a niehbor has grid tied and both are sharing the same transformer, then volts really go up, no different than if it was an XW tied into a subpanel.
I am misunderstandng your question between chrge and sell mode.
Sell mode is allowable up to 260V +/-3. If its in sell mode which I would assume it would be, sellng at peak hours, then the thresh hold can't exceed 263. Using GTI with XW is to sell more at peak.
My impression is that you either do not understand how this all works or are doing a very poor job of explaining it.
Very poor job explaining it. -
SolarPowered wrote: »
In order for GTI's to maintain the efficiency thresh hold above 95%, unlike the XW at 93%. Voltage has to rise per 8 cycles of algorithm in order to maintain conversion efficiciency. There is no throttle back on GTI's, in the case of micro inverters if you use a panel that exceeds 285wp for an M250 micro inverter, and its at peak insolation, in order to achieve its optimal rated efficiency the voltage has to go up. The only throttle back is max watts out, but that doesn't mean that the conversion ratio between volts/amps can't change.
Prior to installing solar systems on homes. I take 3 metered tests. one at 9am, one at 12noon, one at 5pm. Grid voltage seems consistent with no significant rise. After I install solar I've noticed with larger panels with micro, or higher voltage larger arrays for string, at peak insulation voltage rises anywhere from 5 to 10 volts, at maximum watts out.
Then there ar einstances where a niehbor has grid tied and both are sharing the same transformer, then volts really go up, no different than if it was an XW tied into a subpanel.
I am misunderstandng your question between chrge and sell mode.
Sell mode is allowable up to 260V +/-3. If its in sell mode which I would assume it would be, sellng at peak hours, then the thresh hold can't exceed 263. Using GTI with XW is to sell more at peak.
Very poor job explaining it.
The microinverter has no choice at all what voltage it is going to run its output at, regardless of what might be the most efficient voltage. The basic laws of electricity tell us that it must have an output voltage which is equal to the grid voltage at the service transformer secondary offset by the IR drop (gain in this case) which corresponds to the resistance, R, of the wire in between and the current, I, which corresponds to the power output of the inverter.
The micro cannot just decide to raise its voltage.
Your observation that the terminal voltage goes up as the number of inverters is increased is quite reasonable, but it is happening because the resistance, R, of the service, feed and branch wiring is too high and the current from three inverters is three times the current from one inverter. Each micro has no idea what the "actual" grid voltage would be if the micro were not feeding power into it. It can only measure its own terminal voltage.
It would be theoretically possible for an inverter to shut down, measure the voltage, and then decide what voltage to set its output to based on that. But I do not know of any GTI circuit that actually works that way.SMA SB 3000, old BP panels. -
SolarPowered wrote: »Voltage rise is one of those phenomenons that happens with GTI's. Voltage rise happens when you engineer to max out inverters for conditions of winter months.
(I.E) If I use LG 300 panel that produces 279 watts, enphase inverter which makes 240V @ 1 amp = 240 watt continuous, but inverter can produce 250. At peak it will deliver 250V, not 240V, as an instance of voltage rise.
Hypotheticlly If I use a 3000watt string inverter, and I install 3300watts DC panels, and DC string amps are at maximum allowable, a string inverter will produce up to 262V because voltage can no longer be down converter.SolarPowered wrote: »and causes voltage concentration through out the cable. CEC rated efficiency allows for a 2% voltage rise with an 8 cycle algorithm per second, in order to maintain efficiency.SolarPowered wrote: »In order for GTI's to maintain the efficiency thresh hold above 95%, unlike the XW at 93%. Voltage has to rise per 8 cycles of algorithm in order to maintain conversion efficiciency. There is no throttle back on GTI's, in the case of micro inverters if you use a panel that exceeds 285wp for an M250 micro inverter, and its at peak insolation, in order to achieve its optimal rated efficiency the voltage has to go up. The only throttle back is max watts out, but that doesn't mean that the conversion ratio between volts/amps can't change.
I am really at a loss to make any sense of these statements. Honestly, it sounds like jibberish to me.
-
Ethan Brush wrote: »I am really at a loss to make any sense of these statements. Honestly, it sounds like jibberish to me.
Sounds like you have a hard time with monitoring systems. I wouldn't recommend you do so without a minimum of 2 years of O&M training. J/K I know you are one of the brilliant ones here, no pun intended.
Based off this monitoring diagnostic if we were to install a GT with a hybrid on sell mode, at about 11:30 insolation, both inverters (hybrid and GT) would sample both frequency and voltage to reach a max peak in voltage. The micro inverter will do so as long as the 1amp maximum isn't reached.
Even after peak insolation drops the inverter still achieves 255volts, from peak insolation voltage rise. This is a constant value even as amps drop.
Attachment not found.
Attachment not found.
Categories
- All Categories
- 228 Forum & Website
- 136 Solar Forum News and Announcements
- 1.4K Solar News, Reviews, & Product Announcements
- 199 Solar Information links & sources, event announcements
- 898 Solar Product Reviews & Opinions
- 256 Solar Skeptics, Hype, & Scams Corner
- 22.5K Solar Electric Power, Wind Power & Balance of System
- 3.5K General Solar Power Topics
- 6.7K Solar Beginners Corner
- 1K PV Installers Forum - NEC, Wiring, Installation
- 2.1K Advanced Solar Electric Technical Forum
- 5.6K Off Grid Solar & Battery Systems
- 428 Caravan, Recreational Vehicle, and Marine Power Systems
- 1.1K Grid Tie and Grid Interactive Systems
- 654 Solar Water Pumping
- 816 Wind Power Generation
- 624 Energy Use & Conservation
- 619 Discussion Forums/Café
- 312 In the Weeds--Member's Choice
- 75 Construction
- 124 New Battery Technologies
- 108 Old Battery Tech Discussions
- 3.8K Solar News - Automatic Feed
- 3.8K Solar Energy News RSS Feed