Do two separate arrays requie two controllers?
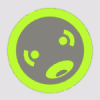
petefink
Registered Users Posts: 6 ✭
Just starting out for off-grid cabin design. I plan to have one 4 panel array on an adjustable frame from 0 to 75 deg from horiz and one 2 panel array fixed at 15 deg from horiz. (on a pump house roof). Arrays are about 30 feet from each other. All six panels are identical 100w "12V" panels and will face about 25 deg from true south. Do I need two charge controllers? Also need advice on best way to arrange panels and battery bank - three 1X2 arrays (24v output)?, or what's is best and why? Output will be 110v ac if that matters. Thank you. Peter
Comments
-
It depends on whether or not you want to use an MPPT charge controller or a PWM controller. With the wire run distances you are talking about I'd have suggested MPPT so that you can run the array at a higher voltage. To run it at a higher voltage you want to have 2 parallel strings of 3x100w panels. It doesn't matter if the strings are at different angles to each other as long as each individual string is facing the same direction. The basic rule is series panels should face the same direction and parallel panels can face different directions if needs be. If you have a PWM charge controller you should make 3 strings of 2x100w panels because a PWM can't transform a higher voltage array to a lower battery voltage while increasing current. With PWM the maximum current you get is what the panels give. You will however need very thick conductors. Same story applies with strings and direction. Each of the 3 strings should face the same direction for those in series.
But to answer your first question you don't need 2 charge controllers provided you wire the array cleverly. The charge controller should just be rated at 1.5x the array power. 2 charge controllers would be necessary if you need 2 separated power sources at different voltages.
In larger systems multiple charge controllers are used simply because they don't make charge controllers big enough to handle more than about 80amps. -
I would try it and see. I do things that you are 'Not Supposed' to do in solar. What could possibly go wrong??? If you can get an idea of using 1 string with the controller and then adding the other and see the difference in a day or three of testing to compare the production. It may make less with only one controller, but with the cost of controllers it may be worth waiting until another is purchased. An additional unit would also function as a backup. Very handy to have in my experience.
Good luck and let us know how it works out.12K asst panels charging through Midnite Classic 150's, powering Exeltechs and Outback VFX-3648 inverter at 12 and 48 volts. 2080 AH @ 48 VDC of Panasonic Stationary batteries (2 strings of 1040 AH each) purchased for slightly over scrap, installed August 2013. Outback PSX-240X for 220 volt duties. No genny usage since 2014. -
Morningstar released this last week: Parallel Charging Using Multiple Controllers With Separate PV Arrays.
Morningstar manufactures solar controllers for charging battery banks with nominal voltages of 12 to 48 Vdc and a range of maximum charging currents from 4 to 60 Amps. The TriStar and TriStar MPPT controllers have the highest charging current ratings with 30A, 45A or 60A maximum charging. Larger battery banks often require greater charging than a single controller can provide. Generally, there is no problem with charging battery banks with several charging sources. The TriStar MPPT manual states the following. “Multiple TriStars can be installed in parallel on the same battery bank to achieve higher charging current. Additional parallel controllers can also be added in the future.”
Here are a few considerations for the use of parallel solar controllers:
● Each solar controller must have its own separate solar array and each array is configured and sized in accordance with the solar controller specifications.
● The batteries need to be designed to handle the combined charging currents. Contact the battery manufacturer if there is any question as to recommended max. charging current.
● The charging sources and controllers are set up properly (explained below).
....
Morningstar’s TriStar and TriStar MPPT controllers have been designed to coordinate parallel charging control effectively without the need for intercommunication between products. While it is always possible to have one controller handle most of the charging regulation alone, as in cases when using 3rd party charging sources, the TriStar and TriStar MPPT controllers’ voltage regulation is accurate enough to synchronize and coordinate the charging regulation for parallel operation.
http://www.morningstarcorp.com/wp-content/uploads/2015/03/ParallelTSandTS-MPPT-030112015.pdf
5kVA Victron Multiplus II, 5.2kW array, 14kWh DIYLifepo4 bank, all grid-tied. -
First, thanks to all of you. I have no controller picked out but if I want to try the single MPPT controller and do 2 parallel strings of 3x 100w panels for the higher voltage (36V?), will it matter that one of the panels in the string (the one on the roof) will almost always be at a different angle from the horizon than the other two (the two on the frame) in the string? thank again.
-
First, thanks to all of you. I have no controller picked out but if I want to try the single MPPT controller and do 2 parallel strings of 3x 100w panels for the higher voltage (36V?), will it matter that one of the panels in the string (the one on the roof) will almost always be at a different angle from the horizon than the other two (the two on the frame) in the string? thank again.
If you have one panel in a series string facing a different angle (even with an MPPT controller) it may become reverse biased when it's receiving less sunlight than the others. Having 2 parallel strings helps lessen the severity, but there will always be a concern. Modules have diodes to guard against damage by reverse bias, but it's still not good to have shaded modules or cells in a series configuration. But do give it a try, it may work out ok. Watch the modules during the course of the day, keep the system under load to make sure the panels are working @ 100%. When you see a module or a cell or two becoming shaded, check their temperature - if they become too hot to touch that's not good at all... -
I always thought that for the average person, having one MPPT controller for two different facing arrays was usually going to work out OK (meaning something like within 10% of the maximum harvest with two charge controllers).
Basically, the panels generate current when exposed to sun. And when exposed to sun, they get hot. If the panel is not facing the sun, then the panel will not be generating hardly any current, and therefore is a "don't care" as far as the charge controller is concerned.
One other former poster here, who I do respect for his design skills, highly recommended that one MPPT controller be used per panel set/orientation.
For example, the Vmp(t) equation is:- Vmp(t) = Vmp(stc) * [(1-0.0052 per oC * (Cell Temp-STC)]
- Vmp(45oC) = 35 V Vmp(stc) * [(1-0.0052 per oC * (45oC-25oC)] = 31.36 Volts @ 45oC cell temperature
In the end, it won't hurt anything to try once controller on the two strings and see how much power you generate. You can always add a second controller later if needed.
-BillNear San Francisco California: 3.5kWatt Grid Tied Solar power system+small backup genset -
Just to clarify my point on the shading issue - I don't want to cause more alarm than is due. I had my first set of panels located underneath a set of bay windows, where they would become partially shaded at certain times of they day. I noticed that when one cell on a module of 72cells became shaded it would get so hot I couldn't touch it even for a second! This was because the current was flowing "backward" through the shaded cell. The module had 3 mosfets in the junction box acting as diodes that could bypass 24cells at a time if need be, but that still meant that under full load there could be 23cell's worth of power being dissipated in one cell. Now consider a module being 16% efficient at converting sunlight into electricity and you can see the shaded cell getting much hotter than it would if it were just down to plain solar heating. The effect gets worse as the already overheating cell gets illuminated again once the shadow moves away. The effect is much less serious if say 2 or more cells get shaded instead of just one because the ratio of illuminated cells to shaded cells is smaller. Needless to say I moved my array to a place where they can't be partially shaded during the brighter times of day...
-
Again, thank you all. the shading SURE COULD be an issue at the end of a winter day - the roof mounted panels get sunset first. I never thought of that. Only problem with trying 2 - 1x3 strings (36v), is if I DO get issue, I gotta' go back and rewire both 30 foot runs of cable from the 2 panels on the adjustable frame to the 1 panel on the shed roof (4 cables). Maybe best to first try three 1x2 panel arrays - one on shed top and two on adjustable frame. And run all three (at 24 V) into a combiner box then to one controller to see how it works. If it doesnt work "too well", just get another controller for the 1X2 on the shed roof. Maybe also convert the two 1x2 arrays on the frame to 1x4 for more voltage (48v) to make the 30' run to the first controller. Does that make any sense? Looks like I need to do some thinking - good thing I haven't bought anything but the panels yet. Thanks so much. Still don't understand it all (by a LONG shot), but I think I'm getting better and you guys are a great help. (Especially since I know it's hard to visualize the setup given just my limited verbal description.)
-
After reading through this thread I think I'll drag my old Sunsaver 10 along this summer and see what differences I note with the 120 watt panel mounted to the trailer roof and the the other two panels set up in their normal configuration. Maybe interesting to see what if any differences occur with all three panels through the TS-45 vs treating as two different arrays.
-
A friend asked this question, not sure how to answer.
"I understand the concept of solar panels in parallel, and why that works. I'm a little less sure about charge controllers in parallel. If I understand charge controllers (at least the standard ones), they work with pulse width modulation. That is, they give a blast of charge current into the battery, sense the voltage, and adjust the width of the next pulse to meet the battery needs. I'm not sure whether it senses the voltage during the pulse, or between pulses, but either way, won't two unsynchronized PWM controllers confuse each other?
For the sake of discussion, suppose that the controllers measure battery voltage between pulses. If one controller ends its pulse, and starts to measure battery voltage while pulse from the other controller is still on, won't the first controller
get a wrong voltage, and set its next pulse to be too short? I don't think this will hurt anything, but whenever it happens, the power from the first panel is cut short, and you are not getting the full available power from that panel."
-
First, an "ideal" battery will not change voltage when it receives a current pulse. In practice, there is a "ripple" voltage. And the charge controllers (I believe) measure the "average voltage" of the battery (and wiring voltage drop).
So, the pulses do not have to be synchronize between the parallel charge controllers as they are just measuring an "average" or "filtered" battery voltage.
Each charge controller is making its own decision(s) based on average battery voltage and time (i.e., 2-6 hours of absorb voltage set point). All that matters is that the battery is held at 14.8 volts for 4 hours--That there are two or more charge controllers "holding" that voltage does not matter that much. If one charge controller is really attempting to hold 14.75 volts and the other is holding 14.8 (error between the two controllers) really does not matter. It just means that one controller will be supplying the majority of the current and the other will not. The battery is still at ~14.75 to 14.8 volts and is being charged.
-BillNear San Francisco California: 3.5kWatt Grid Tied Solar power system+small backup genset -
Larger arrays (KW's ) should have their controllers on a network for synchronization. I agree with Bill. Clouds can do some weird things and anyone with sensitive batteries can have an issue if it is excessive.
Clouds/multi angle arrays can also be the reason that someone with KW's of power/loads would go to a second MPPT controller. Most offgrid might not see these effects unless it is being logged on a computer before and after. OK, they might see it if they were really watching, they then buy the second controller...."we go where power lines don't" Sierra Nevada mountain area
htps://offgridsolar1.com/
E-mail offgridsolar@sti.net
Categories
- All Categories
- 228 Forum & Website
- 136 Solar Forum News and Announcements
- 1.4K Solar News, Reviews, & Product Announcements
- 199 Solar Information links & sources, event announcements
- 898 Solar Product Reviews & Opinions
- 256 Solar Skeptics, Hype, & Scams Corner
- 22.5K Solar Electric Power, Wind Power & Balance of System
- 3.5K General Solar Power Topics
- 6.7K Solar Beginners Corner
- 1K PV Installers Forum - NEC, Wiring, Installation
- 2.1K Advanced Solar Electric Technical Forum
- 5.6K Off Grid Solar & Battery Systems
- 428 Caravan, Recreational Vehicle, and Marine Power Systems
- 1.1K Grid Tie and Grid Interactive Systems
- 653 Solar Water Pumping
- 816 Wind Power Generation
- 624 Energy Use & Conservation
- 619 Discussion Forums/Café
- 312 In the Weeds--Member's Choice
- 75 Construction
- 124 New Battery Technologies
- 108 Old Battery Tech Discussions
- 3.8K Solar News - Automatic Feed
- 3.8K Solar Energy News RSS Feed