Maintenance and runaway test for bypass diodes
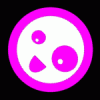
josealjim
Solar Expert Posts: 33 ✭
Dear all,
I need tour help once again. We are about to install 144 polycrystalline modules in front of the office. There will be shadow 3 months a year after noon.
- How can I check the bypass diodes before installation? multimeter?
- How can I check/avoid the runaway fault? We got a thermographic camera.
Diodes specs:
Attachment not found.
Thanks in advance
I need tour help once again. We are about to install 144 polycrystalline modules in front of the office. There will be shadow 3 months a year after noon.
- How can I check the bypass diodes before installation? multimeter?
- How can I check/avoid the runaway fault? We got a thermographic camera.
Diodes specs:
Attachment not found.
Thanks in advance
Comments
-
Re: Maintenance and runaway test for bypass diodes
In my opinion you're worrying about nothing.
They're new; assume they're good. The only time they will be doing anything is if the panel is under partial shade. When shading is even it knocks out power evenly and the bypass diodes do nothing. Their purpose is to divert power from unshaded cells around shaded ones.
Really it's not a concern. -
Re: Maintenance and runaway test for bypass diodes
If you have heavy shading--Perhaps you might want to look at Micro Inverters (assuming Grid Tied system). That will reduce the amount of time the bypass diodes are subjected to current due to shading of portions of the array/panels.
-BillNear San Francisco California: 3.5kWatt Grid Tied Solar power system+small backup genset -
Re: Maintenance and runaway test for bypass diodes
The forward voltage drop of 0.6v is pretty high. Look into "Schottky" diodes which have much less forward voltage drop. -
Re: Maintenance and runaway test for bypass diodes
I think I'm confused.
He's not building 144 panels surely? So if you buy panels the bypass diodes are built-in. You wouldn't be putting any in yourself, would you? -
Re: Maintenance and runaway test for bypass diodesPNjunction wrote: »The forward voltage drop of 0.6v is pretty high. Look into "Schottky" diodes which have much less forward voltage drop.
A forward voltage drop of .6V is not all that high for a Schottky diode which is carrying close to its full rated load current. There is still internal resistance.
To get the full benefit of the ~.2V minimum forward drop you need to oversize the diode significantly with respect to load current. And commercial manufacturers are just not going to do that....SMA SB 3000, old BP panels. -
Re: Maintenance and runaway test for bypass diodes
Thanks guys for your reply,
We bought the modules from JA Solar, they come with 3 Schottkys diodes. They will be under shading conditions (0 to 100%) 3 months a year. Some installers and friends with experience in Thailand told me that diodes may fail after certain cycles withing shading conditions. That is what i want to know, when exactly they fail in order to proceed with replacements.
Im not an expert on this so please correct me if im wrong:
-When a bypass diode fails under shading conditions, power will be dissipated on shaded cells and it will make the current falls bellow values that are normal when diodes are working well. Voltage will also drop (according to the number of cells shaded) but being the modules in series, i guess that the key to detect a diode fault is the current of the string.
- Im also doing the automation of biogas production and biogas upgrade plants, so i do want to monitor the voltage and current of each string.
- In order enter a fault detection code into the micro-controller or plc (i have no idea how the inverters check strings faults ) i was thinking to create an alarm when the current of one string drops under certain value and the surrounded ones are ok. Which values of current should I set for this alarm? (if it is only the current the parameter i should look at)
- Any ideas to set the diode fault alarms?
I really appreciate ideas about how to write the code, which parameters should i look at? which values?
BR and thanks a lot -
Re: Maintenance and runaway test for bypass diodesThanks guys for your reply,
We bought the modules from JA Solar, they come with 3 Schottkys diodes. They will be under shading conditions (0 to 100%) 3 months a year. Some installers and friends with experience in Thailand told me that diodes may fail after certain cycles withing shading conditions. That is what i want to know, when exactly they fail in order to proceed with replacements.
In general, diodes will fail in two ways... One is shorted and the second is open. One general assumption is that diodes fail open (like a fuse) for high current events (and high temperature?) and shorted in low to medium current applications--Although some number of open failures are caused by diodes failing shorted and then shunting too much current. But--In general, you should assume that they can fail either way.-When a bypass diode fails under shading conditions, power will be dissipated on shaded cells and it will make the current falls bellow values that are normal when diodes are working well. Voltage will also drop (according to the number of cells shaded) but being the modules in series, i guess that the key to detect a diode fault is the current of the string.
Not worrying what causes the failure (my two cents--High working temperature--hot sun--And current when shunting because of power from I*V or something like 2-8 watts in a plastic box, mounted in hot sunlight, with no heat sinks), A shorted diode will shunt the current around a string of 18 to 24 cells or so (depending on solar panels design). Since each cell is ~0.5 volts, that would be a short circuit of ~9-12 volts of panel voltage (Vmp-panel minus ~9-12 volts). Current production will probably not be affected.
If a diode fails open... And the panel (string) is in full sun--Not detectable. Diodes do not conduct under normal operation anyway.
If there is partial shading, the solar cells go "high resistance" and stop conducting. Panel/string current will drop to near zero Amps. If the string voltage is high enough (probably over 12-24 volts), the Solar Cells (which are just "giant diodes") are reversed biased by too much voltage and will suffer breakdown--and probably fail. You will then see a mix of lower string output current and/or voltage.- Im also doing the automation of biogas production and biogas upgrade plants, so i do want to monitor the voltage and current of each string.
More or less--The easy/ideal way to check operation... Two ways. One is that Vmp-array (if using GT inverter and/or MPPT charge controllers with operate at Vmp-array voltage). If you see a dramatic drop, then there is a problem. Note that Array Voltage is both temperature and load sensitive. As solar cell temperature rises, Vmp-array (and Voc-array) fall. Also Array Voltage is current sensitive. At zero current the array is as Voc-array. At Imp the array is at Vmp or roughly Voc*0.8 and as temperature rises more, Vmp-can fall a bit more. In sub freezing weather, Vmp-array can exceed Vmp-STC (standard Test Conditions). Very roughly, Voc cold (sub zero) to Vmp-hot can be almost a 2:1 voltage range.
With a MPPT GT Inverter, you can even estimate the solar cell temperature based on current Vmp-array operating point.
Current is proportional to sunlight (in a MPPT controller operating at maximum harvest). Pretty linear to ~5% of sunlight (2x more sun, approximately 2x more current). Imp-array does rise very slightly with temperature--But is, for the most part, OK to ignore (~1/5th or less of the voltage sensitivity to temperature).
Monitor the over all Array Voltage (minimum Vmp-array should track array temperature and outside air temperature with an offset--Wind can affect too). You should not see Vmp-array fall much below Vmp-array@temperature if all is well (and panel is in direct sunlight).
If you have two or more parallel strings--Simply monitor the current for each string (DC current monitoring is an issue--AC is much easier/cheaper). If the two strings are within 10-20% of each other--The world is fine. If the two strings are 50% or more different, something has failed or other problem.
This, of course, means that strings have identical installations... Otherwise, you may have to do your "test" at high noon (no panels in shade).
Also, remember current is dependent on the amount of sunlight--Very dark/cloudy/rainy days can give you 5% of rated/sunny output pretty easily. So you have to make sure your controller can account for a week of bad weather too.- In order enter a fault detection code into the micro-controller or plc (i have no idea how the inverters check strings faults ) i was thinking to create an alarm when the current of one string drops under certain value and the surrounded ones are ok. Which values of current should I set for this alarm? (if it is only the current the parameter i should look at)
I would guess that the matched string values would become less accurate (with simple shunt or some sort of Hall Effect sensor) at less than 25% of or rated/expected current (poor instrument accuracy, poor sun giving mixed results). Perhaps you would only want to do the test at (for example) 4 hours after sunrise (few seconds of average current measurement).
The 2 or more strings would work much of the time--Overall logging of energy harvested per day would tell you if everything is adiquate (with eye on weather in area).
One string failure out of two is pretty easy to see from a gross WH per day (50% drop in harvest). However when you have 3 or more parallel strings--"Seeing" a single string failure is probably difficult to pick out from bad weather/seasonal shading.
You can set up a single small cell (or panel) with a current shunt and monitor the current (voltage drop across the shunt) of the "pilot" cell. If all is well, the other string/system array currents should track pretty closely. Also, can alarm if there is sun detected and gross power levels are way low (compensate for local weather/solar conditions).- Any ideas to set the diode fault alarms?
So--If I was doing this--I would keep very simple. Usually the easiest is to monitor power readings from controllers (is this Grid Tied Solar, or Battery based system with battery chargers?). If you see something falling 50% below seasonal or "twin" installation in same plant--I would alarm as definitely failed/problem.
If I was monitoring solar panel strings, I would be monitoring 2 or more parallel strings--Or a single string with a "pilot cell". Only sample at ~solar noon (+/- an hour or two--to save code/clocks/etc. by 4 hour after sun rise or something similar) once per day (only monitor continuously if you really need the data for off-line trend analysis/billing/etc.).
If you are monitoring strings, I would think about a "pilot" or reference cell to make up for the "missing" string data.
I would not "worry" about bypass diode failures. Such failures will, eventually, affect overall harvest numbers. There is no "reasonable" method (that I can see) for you to diagnose/fault specifically on bypass diode failures (open failures are not easily detectable, shorted failures will affect array voltage/current output if parallel strings/overall harvest).
And you have to look at the cost of monitoring and cost of failure... If the cost of failure is high--You should look at N+1 redundancy. Two or more redundant systems where you can compare outputs over time and if there is a failure, give yourself time to go out and service (during normal inspection/group multiple sites for service, etc.).
And such monitoring will alter you to catastrophic failures (two random failures overlap, somebody with rocks or a 22 rifle, etc.).
Have not talked about batteries yet... Probably more likely to fail than N or N+1 solar array power system.
Your thoughts?
-BillNear San Francisco California: 3.5kWatt Grid Tied Solar power system+small backup genset -
Re: Maintenance and runaway test for bypass diodes
Thanks for your answer.
Im working inn a Energy Research institute so we do have several plcs and microcontrollers already working on pilots plants and energy optimization systems (it would not require too much extra investment)
What about this method?:
Single strings tracking (Id do also the array strings harvesting tracking)
- from 7-10 am (no shadow along the year):
* Voltage comparison between strings ---> voltage drop higher than 12v (20 cells per diode config) --> malfunction on the string (open cell, shorted diode)---> check string with thermographic camera
* Current comparison between strings ---> current drop ---> hot cell ----> check with themographic camera
- With shadow with the same pattern on different strings:
* Current comparison between strings ---> current drop ----> bad diode/s ----> check with thermographic camera
Thanks -
Re: Maintenance and runaway test for bypass diodesThanks for your answer.
Im working in an Energy Research institute so we do have several plcs and microcontrollers already working on pilots plants and energy optimization systems (it would not require too much extra investment)
What exactly is the power system configuration? On grid/Off grid/ ABC AH at XY Volt Battery Bank/off the shelf MPPT or PWM controllers/etc.?
Are you going to design your own charge controllers/GT power management/GT inverter system?What about this method?:
Single strings tracking (Id do also the array strings harvesting tracking)
Why single strings? Two strings would give you better reliability and could give you N+1 redundancy.
Is this a pure research on panel failure or are you actually trying to build systems to put into the field with as much self diagnosis/monitoring as possible/practicable? Are you going to sell systems--Or is this part of a "installation and service" contract?
I am guessing that this is a university study out of Thailand?- from 7-10 am (no shadow along the year):
Why 7-10am? If you have "problems", thermal problems will become more evident at higher temperatures. Power=I2R -- 2x the current, 4x the heat (and higher temperatures for thermal camera).
Another issue--If battery based system--Controllers will draw most current if the batteries are below ~80-90% state of charge... As the battery become more charged and the battery bus rises (above absorb voltage set point for charge controller), the batteries will be accepting less current... So you may have more current at 10am vs 1pm from the solar array due to batteries approaching full charge.
With off grid power systems--This can cause failures to be "hidden". For example, during summer when you have more sun--A good controller may (just an example) fill the battery by 10am, and a controller with a bad string may fill the controller at 3pm. Both will have the same AH/WH generation during they overall daily cycle (both filled the battery bank by end or day with same amount of energy production). But during winter (bad weather), the good system will fill the battery bank by 4pm and the bad system will never fill the battery bank)--So monitoring amount of energy harvest vs time would probably be useful too.* Voltage comparison between strings ---> voltage drop higher than 12v (20 cells per diode config) --> malfunction on the string (open cell, shorted diode)---> check string with thermographic camera
String voltage is a difficult concept to monitor/determine failures. String voltage is (more or less) set by either MPPT controller control (and battery state of charge/load requirements) or by Battery state of charge and other battery conditions (for PWM controller).
If you have two strings in parallel--Both strings will have the same voltage (common solar PV +/- buses).* Current comparison between strings ---> current drop ---> hot cell ----> check with themographic camera
Shorted diodes--I2R heating. Open diodes I=0 (or open solar panel wiring, open solar cell), no current flow, no heating.- With shadow with the same pattern on different strings:
* Current comparison between strings ---> current drop ----> bad diode/s ----> check with thermographic camera
Single string or N+1 strings?
A good diode in a shorted string--You will get heating on the shaded (partially shaded) panel in the Junction Box--You MAY see hot spot at J-Box. If J-Box of panel is in shade, heating above ambient may be more visible. J-Box heating via diode may be less visible/detectable if panel already heated by direct sun.
Also note several things... Glass (and plastic backing/J-Boxes) have very poor thermal transfer characteristics. Your thermal camera will be measuring temperature of glass/j-box, not diodes themselves. May give less than clear results.
Glass is shiny/glossy and sometimes has various surface treatments to reduce reflections and sometimes even IR. May give odd results with camera (especially between brands/models of panels).
Open Diodes=No Current flow=No J-Box heating. And depending on how high of voltage of string and current draw by controller (GT inverter/Charge controller/loads), all you will see is possibly a low grade heating of random solar cells in shaded area as they have effects of reverse voltage break down. You may have a little heating above ambient in shaded area--But you may need a reference source (other solar panel in shade, un-powered solar panel as reference temperature to "know" that shaded area of damaged panel is overheating).
I am still confused--Are you studying solar panel failures (specifically bypass diodes)--Or are your trying to build self monitoring equipment for field use.
IR camera in field would seem to be a bit odd as a way for remote monitoring. More of a research/service tool.
In field--You do not really need to know exactly what failure is (i.e., bypass diode failure, solar cell failure, or internal wiring failure, or even physical damage)--All the service tech needs to know is which string/panel is bad and what parts he should bring for repairs.
However--If you are trying to make more reliable solar panels--I am all for better heat sinking of bypass diodes. I believe the current practice of axial diodes in an plastic box passing Imp of the panel is an unreliable design. Life is cut by 1/2 for every 10C increase in temperature. Run a diode 40C hotter because of poor heat-sinking, You are looking at 1/16 the service life vs a well heat sinked design.
But still not easy. Metal heat-sinks on diodes are electrically connected to cathode--Need insulation between diode and metal J-Box heat-sinking for voltage isolation (panels are generally designed for 600-1,000 VAC of insulation (modern GT solar panels).
My first GT Array failed--My guess because of poor J-Box design. Whether from J-box wiring Current Heating or some sort of bypass diode heating (my array was not shaded), the array had light coffee colored "stains" above J-Box under the glass (had to look pretty closely to see). Panels lost 1/2 their output current due to this failure.
Also--You are paying a lot of attention to array shading. Depending on how system is designed and actual controllers used--ANY Shading on an array will very easily cut upwards of 50-100% of the shaded string's output current. If you have significant shading on an array during the major sun of the day (say between 9am and 3pm), the system becomes either very expensive (more panels than you need to generate required power) or close to useless due to lost output power/energy due to shading.
In the end, if you are studying failure modes of bypass diodes for solar panels--I could think of much easier/better defined methods of configuring test fixtures to give you accelerated test/more useful test results.
-BillNear San Francisco California: 3.5kWatt Grid Tied Solar power system+small backup genset -
Re: Maintenance and runaway test for bypass diodes
Sorry for not giving enough details.
I work for an energy research institute in Thailand. We are allowed to behave as a private company so we develop turnkey projects and consulting. The 37kw on-grid pv system will be installed in front of our building as showcase.
We will use the new Leonics 3phase multistring inverters (2x15kw)
Attachment not found.
We are about to introduce in our portfolio energy optimization and management systems. It comprises many power meters distributed along the building, sending data to a micro-controller by wifi. We want to track and manage energy sources (pv system, grid, biogas generators) and loads.
The microcontroller will be linked (RS485) to the inverter as well, so once we have the system I think it would be a good idea to track the performance of the modules (field sensors plus Perez-Ineichen algorithm ) and also detect any kind of malfunction.
Following your indications, lets see if i can come up with a good solution (excuse my ignorance):
TRACKING. Worst months (November, December, January) from 10:30 to 11:30, the rest of the year from 12:00 to 13:00
-(1) Performance: Pyranometer + temperature sensors + Perez algorithm---> Error>Tolerance ---> ALARM
-(2) Strings current tracking: currents between 10-22% of each other everything OK ----> current difference bigger than 30% ----> ALARM
-(3) Array Wh harvesting: real time data from inverter ----> Array harvesting drop 50% ---> ALARM
Would it be better to track (2) and (3)? or just (3) is enough?
Once we detect a malfunction how do we find the wrong module? Thermographic camera, visual inspection and V/I measurement of each module?
MAINTENANCE:
- Cleaning modules every month
- Visual inspection, connections and corrosion every 6 months?
- Thermographic camera every 6 months or only when we detect a fault?
- Should we check open diodes by generating shadow (current near 0A) for example once a year?
Thanks for your help
Categories
- All Categories
- 229 Forum & Website
- 137 Solar Forum News and Announcements
- 1.4K Solar News, Reviews, & Product Announcements
- 199 Solar Information links & sources, event announcements
- 898 Solar Product Reviews & Opinions
- 256 Solar Skeptics, Hype, & Scams Corner
- 22.5K Solar Electric Power, Wind Power & Balance of System
- 3.5K General Solar Power Topics
- 6.7K Solar Beginners Corner
- 1K PV Installers Forum - NEC, Wiring, Installation
- 2.1K Advanced Solar Electric Technical Forum
- 5.6K Off Grid Solar & Battery Systems
- 428 Caravan, Recreational Vehicle, and Marine Power Systems
- 1.1K Grid Tie and Grid Interactive Systems
- 654 Solar Water Pumping
- 816 Wind Power Generation
- 624 Energy Use & Conservation
- 619 Discussion Forums/Café
- 312 In the Weeds--Member's Choice
- 75 Construction
- 124 New Battery Technologies
- 108 Old Battery Tech Discussions
- 3.8K Solar News - Automatic Feed
- 3.8K Solar Energy News RSS Feed