Calculation Verification
Options
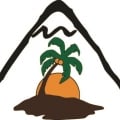
hemmjo
Solar Expert Posts: 90 ✭✭
I have been visiting this site for a while trying to get a handle on planning solar systems for a mission I work with in the Dominican Republic. We have a small complex miles from any grid connection
I think I have a pretty good idea now. Here are results I get from my understanding so far.
I have a 120v 200 watt load that needs to run about 13 hours.
Running the numbers I get the following.
AC load
volts=120, amps=1.7, watts=204, hours/day= 13, watthour/day=2652
DC storage needed
battery volts= 12, Amp Hr/Day = 221, discharge= 50%, battery capacit =442
A common battery available in the DR is 6 volt 225 Amp Hour. 4 of these would give me 2- 12 volt 225 amp strings for 450 ah.
Next I need to size the panels in order to properly maintain the batteries.
panel capacity
AH of Battery=450 charging volts=14.5 derating=1.3
rate of charge
=2% panel watts=170 Float charge
=5% panel watts=424 minimum charge rate
=10% panel watts= 848 good nominal charge rate
=13% panel watts=1102 cost effective maximum, no point in having more.
If I get 3-250 watt panels for 750 watts. In our location useful sun is 4.6(dec) to 5.8(july) hours @ 750 watts gives 3450 to 4350 watt hours @ 12 volts = 287 to 362 amphours.
So, this should be able run the load, keep the batteries charged to optimum levels, and maybe run a bit of extra load, perhaps a few LED lights at night.
Does this sound correct?
As always thanks for your input,
John
I think I have a pretty good idea now. Here are results I get from my understanding so far.
I have a 120v 200 watt load that needs to run about 13 hours.
Running the numbers I get the following.
AC load
volts=120, amps=1.7, watts=204, hours/day= 13, watthour/day=2652
DC storage needed
battery volts= 12, Amp Hr/Day = 221, discharge= 50%, battery capacit =442
A common battery available in the DR is 6 volt 225 Amp Hour. 4 of these would give me 2- 12 volt 225 amp strings for 450 ah.
Next I need to size the panels in order to properly maintain the batteries.
panel capacity
AH of Battery=450 charging volts=14.5 derating=1.3
rate of charge
=2% panel watts=170 Float charge
=5% panel watts=424 minimum charge rate
=10% panel watts= 848 good nominal charge rate
=13% panel watts=1102 cost effective maximum, no point in having more.
If I get 3-250 watt panels for 750 watts. In our location useful sun is 4.6(dec) to 5.8(july) hours @ 750 watts gives 3450 to 4350 watt hours @ 12 volts = 287 to 362 amphours.
So, this should be able run the load, keep the batteries charged to optimum levels, and maybe run a bit of extra load, perhaps a few LED lights at night.
Does this sound correct?
As always thanks for your input,
John
Two systems in the Dominican Republic http://villagemountainmission.org/
installed Feb 2014 at 19.796189° -70.893594°, Classic 150 + WBJR, KISAE SW1210, MN Battery Monitor, IOTA DLS 55/IQ4, 4- Solar World 275w, 4-6v x 225ah Trace Batteries
installed Feb 2015 at 19.795733° -70.893372°, same components as above
Honda PowerMate PC0497000, 7000/8750w generator - powers the well and chargers maybe once a week
installed Feb 2014 at 19.796189° -70.893594°, Classic 150 + WBJR, KISAE SW1210, MN Battery Monitor, IOTA DLS 55/IQ4, 4- Solar World 275w, 4-6v x 225ah Trace Batteries
installed Feb 2015 at 19.795733° -70.893372°, same components as above
Honda PowerMate PC0497000, 7000/8750w generator - powers the well and chargers maybe once a week
Comments
-
Re: Calculation Verification
Let's see, a 200 Watt load for 13 hours is 2600 Watt hours.
Inverter efficiency of 90% = 2889 Watt hours.
Inverter consumption over 13 hours = additional 260 Watt hours.
Total 3149 Watt hours.
On 12 Volts that's approximately 263 Amp hours consumed. Limiting battery to 25% DOD = 1052 Amp hour battery bank. You really do not want a target of 50% DOD because it gives you effectively no reserve.
At this point I'd suggest going up to a 24 Volt system. It will cut the Amp hours in half, improve efficiency, and make it possible to charge from a single controller.
The panels are there to recharge the batteries, not to run things. Don't try and count on the 'surplus' power that would otherwise go unharvested once the batteries are full, but have a plan to make use of it if it is available. Basically you're looking at 105 Amps @ 12 Volts or 1636 Watts of panel. This would be about the same size array on 24 Volts, but could be handled by a single controller (50 Amps @ 24 Volts).
Caveats:
1). Round power consumption figure up or if possible down.
2). Round battery capacity up to nearest available size.
3). Round array size up to nearest available size.
Not quite the minimalist system you were hoping for, but much more likely to prove serviceable in the long term.
Although you have long daylight hours working for you there, you have high temperatures working against you. -
Re: Calculation Verification
Thank you for your response. I was pulled away from this project by life, you know stuff happens. I am back to it now and have to make some decisions this week.
The 200 watt for 13 hours figure per day, was a rounded up figure. I used it to test my understanding of the calculations. The most demanding load we have is a refrigerator with a tag that says it is 60 watts. It runs about 1/2 the time during the day. The only other AC loads we have are a tiny washing machine that just agitates the clothes and has a spin mode, it does not even have a pump to remove the water, you just lower the hose to drain it. Occasionally a computer power supply/charger, and a printer plugged in only when needed. We will also have a a couple of LED lights.
I understand the value of going to 24volts or even higher. Especially for the panels as it is harder to shorten that wire run. As I read about charge controllers, am I understanding correctly that an Outback FlexMax 60 or 80 MPPT controller can be set to work with panels from 12, 24, 36, 48 or 60 volts? In addition that battery bank voltage does not have to match the panels? So if I start with 3 - 24 volt 255 watt panels, I could use the Flex controller in 24 volt mode. But if I got 4 -24 volt panels, I could wire each pair in series and use the controller in 48 volt mode?
In addition the controller can be set to charge a battery bank that is different than the panel array? I would love to use a 24 volt bank, but we have had a 12 volt 1000 watt pure sine wave inverter donated, as well as some 12 volt LED lighting that we can use while bypassing the inverter.
If you have an understanding of my situation, I would appreciate your thoughts.
Thanks,
JohnTwo systems in the Dominican Republic http://villagemountainmission.org/
installed Feb 2014 at 19.796189° -70.893594°, Classic 150 + WBJR, KISAE SW1210, MN Battery Monitor, IOTA DLS 55/IQ4, 4- Solar World 275w, 4-6v x 225ah Trace Batteries
installed Feb 2015 at 19.795733° -70.893372°, same components as above
Honda PowerMate PC0497000, 7000/8750w generator - powers the well and chargers maybe once a week -
Re: Calculation VerificationThank you for your response. I was pulled away from this project by life, you know stuff happens. I am back to it now and have to make some decisions this week.
Life is what happens while we are making plans.The 200 watt for 13 hours figure per day, was a rounded up figure. I used it to test my understanding of the calculations. The most demanding load we have is a refrigerator with a tag that says it is 60 watts. It runs about 1/2 the time during the day. The only other AC loads we have are a tiny washing machine that just agitates the clothes and has a spin mode, it does not even have a pump to remove the water, you just lower the hose to drain it. Occasionally a computer power supply/charger, and a printer plugged in only when needed. We will also have a a couple of LED lights.
Surge power is also important... Induction motors can have a surge current of 5x rated load... That 60 watt refrigerator may surge to 300 VA or more. A modern "standard" refrigerator will run ~120 watts and surge to 600 watts (plus various defrost/anti-sweat heaters, etc.). A 120 Watt pump will usually barely reliably start on a "good" (whatever that is--notice "fuzzing" up of the statement is on purpose) 1,000 watt AC inverter--1,200 to 1,500 watt inverter is recommended (who knows the surge capabilities of the 100's of inverters out there--A "good one" with appropriate battery bank and DC wiring should surge around 2x rated output power).I understand the value of going to 24volts or even higher. Especially for the panels as it is harder to shorten that wire run. As I read about charge controllers, am I understanding correctly that an Outback FlexMax 60 or 80 MPPT controller can be set to work with panels from 12, 24, 36, 48 or 60 volts? In addition that battery bank voltage does not have to match the panels? So if I start with 3 - 24 volt 255 watt panels, I could use the Flex controller in 24 volt mode. But if I got 4 -24 volt panels, I could wire each pair in series and use the controller in 48 volt mode?
The "typical" ideal voltage for a MPPT charge controller is around 2x the battery voltage. A 29 volt charging battery (24 volt battery bank) would like (around) 58 volt Vmp array).
For a 140-150 volt maximum input MPPT charge controller, a Vmp~100 volt maximum array is about the highest voltage the controller can handle (a 100 Vmp array should have Voc-cold approaching 140 VDC in a very cold climate). Always check the Voc-cold of your panels against your weather conditions/controller ratings to be sure. This is complex and the controllers are expensive to fry (and controllers frequently log the maximum input voltage for warranty claims).In addition the controller can be set to charge a battery bank that is different than the panel array? I would love to use a 24 volt bank, but we have had a 12 volt 1000 watt pure sine wave inverter donated, as well as some 12 volt LED lighting that we can use while bypassing the inverter.
It is almost never cost effective to use 12 volt input AC inverters on a 24 volt battery bank. If you 'unbalance' the batteries (discharge one 12 volt segment more than the other), you will be "equalizing" your batteries all the time--The already full battery will be "overcharged" to get the low battery back up (excessive equalization is very hard on batteries).
You can get "battery balancers" (basically bi-directional isolated DC power supplies) that will charge/discharge between unmatched battery voltages--But is is usually just about as easy to get a 24 volt AC inverter instead (this is sometimes done on "coach conversions" that have 24 volt vehicle system and a 12 volt "house" system).
Good Luck John,
-BillNear San Francisco California: 3.5kWatt Grid Tied Solar power system+small backup genset -
Re: Calculation VerificationAs I read about charge controllers, am I understanding correctly that an Outback FlexMax 60 or 80 MPPT controller can be set to work with panels from 12, 24, 36, 48 or 60 volts? In addition that battery bank voltage does not have to match the panels? So if I start with 3 - 24 volt 255 watt panels, I could use the Flex controller in 24 volt mode. But if I got 4 -24 volt panels, I could wire each pair in series and use the controller in 48 volt mode?
"12, 24, 36, 48 or 60 volts" refers to the nominal voltage of the battery array. The FlexMax can be programmed to work with any battery array with those nominal voltages.
The Vmp (voltage at maximum power point) of a single PV panel or a series string of more than one PV panel should be at least 1.5 times higher than the nominal voltage of the battery array. The open circuit voltage (Voc) of the series string of crystalline PV panels on the coldest day must be lower than the maximum input voltage rating of the charge controller, 150 VDC for either FLEXmax. So, yes, with an MPPT charge controller the Vmp of the PV panels does not have to be 1.5 times the voltage of the battery array like it should be when using a PWM (pulse width modulated) or relay switched charge controller.
If you use a 12 V battery array, the charge controller must be in the 12 V mode which makes the "NEC Recommended Solar Maximum Array STC Nameplate" 750 W for the FM-60 and 1,000 W for the FM-80. These recommendations are conservative allowing you to install 5% or 10% more power. For example, even though the power rating is okay, the FM-80 could not handle 4 Trina Solar TSM-240PA05.08 240 Watt Multicrystalline Solar Modules in series because the Voc would be:
4 * 37.2 V = 148.8 V at 25 C
The voltage would be over 150 V on a cold day. You could only put 3 of these PV panels in series with a FLEXmax charge controller. Your best choice for using 4 of these PV panels with an FM-80 would be 2 PV panels in series and 2 series strings connected in parallel.
I hope this makes it clearer. -
Re: Calculation Verification
Am I understanding correctly that I cannot use a FLexMax 80 with 4 - 255 watt 24 volt panels. These would be wired in series pairs for 2 - 48 volt strings to the charge controller.
I am limited to a 12 volt battery bank (4- 6 volt, 225 amp hour) at this time because of budget issues and a nice donated 12volt, 1000watt pure sine inverter. According to the math, ( 4 panels x 255w = 1020 watts. 1020 watts / 12 volts = 85 amps) it appears that the panels may be a bit too large for the controller. But all of the discussions here point to the fact that panels to not deliver as much as advertized, and seldom are conditions optimum for maximum energy collection.
I am not clear on what SolInvictus means by, "If you use a 12 V battery array, the charge controller must be in the 12 V mode....", does this mean that I cannot use the 48 volt input? Or are you referring to setting the output mode to 12 volt here?
At this time I am locked into the 255 watt panels, the 225 ah batteries, as that is what is available to me in the Dominican Republic. I am also locked into the 12 volt, 1000 watt inverter as we already own it. I could drop off one panel and use only 3 until we can get a 24 volt inverter, but then I cannot use 48 volt input since I will not have 2 pairs of 24 volt panels. (I am assuming the panels are 24 volt, If they are 12 volt I can just put them all in series for 36)
As I read the lists of what many of you have in your signature line the OutBack FlexMax 60 or 80 seems to be a very common choice. Or do you have suggestions for something better.
Thanks again for your input,
JohnTwo systems in the Dominican Republic http://villagemountainmission.org/
installed Feb 2014 at 19.796189° -70.893594°, Classic 150 + WBJR, KISAE SW1210, MN Battery Monitor, IOTA DLS 55/IQ4, 4- Solar World 275w, 4-6v x 225ah Trace Batteries
installed Feb 2015 at 19.795733° -70.893372°, same components as above
Honda PowerMate PC0497000, 7000/8750w generator - powers the well and chargers maybe once a week -
Re: Calculation Verification
The FM80 can use any array Voltage above the minimum required for the system. That means for a 12 Volt system the array needs to be at Vmp 17.5 or above. It will work with an array of 48 Volts nominal, albeit with slightly less conversion efficiency. The system Voltage of 12 is programmed in to the FM80 on start-up (connect battery side first, then the PV array) along with other charging parameters.
The only thing better than an Outback FM80 is a MidNite Classic, and they cost a bit more. You may not need the additional features they offer either. On the whole the FM60/80 is quite a bargain for a top-end MPPT controller. -
Re: Calculation Verification
What sort of quality is the "nice" 12v inverter. Which brand, where made. We dont recomend using no name "chinese" brands, theres too much to go wrong, and the failure rate is very high on almost all of those cheaper models.
Know that using 12v limits your system for ever. It can never grow. Im learning (slowly) to do things right the first time.
However if youre really stuck at 12v, and/or your system doesnt need to grow and/or you have lots of 12v loads, then 1200W PV is quite doable on a single controller. You can just use the current limit setting to clip any exceptional peaks off. It wont harm them. Know also that midnite classic is rated at 96 amps, so that potentially gives you more harvest. One more upside to the classic is that for $50 the battery monitor addon avoids completely the need to a seperate battery monitor, highly recommended.1.8kWp CSUN, 10kWh AGM, Midnite Classic 150, Outback VFX3024E,
http://zoneblue.org/cms/page.php?view=off-grid-solar -
Re: Calculation Verification
I guess that honestly I do not know the quality of the donated inverter. It is a KISAE, SW1210. It is indeed made in China, I have had it hooked up in my garage to be sure it works, Just using an couple of car batteries.
As for the system growing. I would have liked to have the batteries be 24 volt, but the budget it stretched as it is. So, for now I am going with the 4 - 255 watt panels, in 2 - 48 volt strings, OutBack FLex 80 controller, 4 - 6volt 225 ah batteries, and the KISAE SW1210 controller. If I can make this inverter last a year, and we are able to afford a better controller, I will be able to reconfigure the 4 batteries into a 24 volt string, and add a 24v to 12v converter to run the minimal 12v LED lighting.
Ok so checking the MidNight Classic 150 I see it is 30 more then the OB Flex 80. I see that is comes with the remote battery sensor so that makes it about the same as the OB Flex 80.. I would like to have a battery monitor... but I do not see the battery monitor you mention.
I truly appreciate all of your input..
John
http://villagemountainmission.org/Two systems in the Dominican Republic http://villagemountainmission.org/
installed Feb 2014 at 19.796189° -70.893594°, Classic 150 + WBJR, KISAE SW1210, MN Battery Monitor, IOTA DLS 55/IQ4, 4- Solar World 275w, 4-6v x 225ah Trace Batteries
installed Feb 2015 at 19.795733° -70.893372°, same components as above
Honda PowerMate PC0497000, 7000/8750w generator - powers the well and chargers maybe once a week -
Re: Calculation Verification
the battery monitor is the WBjr, just on the market,... it works with the Classic line and is presently being upgraded (software)
http://www.midnitesolar.com/productPhoto.php?product_ID=519&productCatName=Charge%20Controllers%20-%20Classics&productCat_ID=21&sortOrder=9&act=pc
KID #51B 4s 140W to 24V 900Ah C&D AGM
CL#29032 FW 2126/ 2073/ 2133 175A E-Panel WBjr, 3 x 4s 140W to 24V 900Ah C&D AGM
Cotek ST1500W 24V Inverter,OmniCharge 3024,
2 x Cisco WRT54GL i/c DD-WRT Rtr & Bridge,
Eu3/2/1000i Gens, 1680W & E-Panel/WBjr to come, CL #647 asleep
West Chilcotin, BC, Canada
Categories
- All Categories
- 228 Forum & Website
- 136 Solar Forum News and Announcements
- 1.3K Solar News, Reviews, & Product Announcements
- 198 Solar Information links & sources, event announcements
- 895 Solar Product Reviews & Opinions
- 255 Solar Skeptics, Hype, & Scams Corner
- 22.4K Solar Electric Power, Wind Power & Balance of System
- 3.5K General Solar Power Topics
- 6.7K Solar Beginners Corner
- 1K PV Installers Forum - NEC, Wiring, Installation
- 2.1K Advanced Solar Electric Technical Forum
- 5.5K Off Grid Solar & Battery Systems
- 428 Caravan, Recreational Vehicle, and Marine Power Systems
- 1.1K Grid Tie and Grid Interactive Systems
- 652 Solar Water Pumping
- 815 Wind Power Generation
- 624 Energy Use & Conservation
- 618 Discussion Forums/Café
- 311 In the Weeds--Member's Choice
- 75 Construction
- 124 New Battery Technologies
- 108 Old Battery Tech Discussions
- 3.8K Solar News - Automatic Feed
- 3.8K Solar Energy News RSS Feed