Series/parallel connections
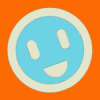
W3ABC
Registered Users Posts: 19 ✭

I've got four 12v batteries that I want to use to power small electronic devices. I'd like to wire the batteries up in a series/parallel configuration, as seen above, to save on wiring costs from the solar panels (30ft one direction).
What's the best way to wire up 12v electronics in this configuration? Is it as simple as adding another wire or will I have to convert 24v back down to 12v?
Comments
-
Re: Series/parallel connections
You have two choices: use a DC to DC converter to shift the 24 Volts to 12 or re-wire the batteries when you want to power 12 Volt devices.
Beware of pulling 12 Volts off "half" the 24 Volt bank; it will unbalance the batteries. -
Re: Series/parallel connectionsWhat's the best way to wire up 12v electronics in this configuration? Is it as simple as adding another wire or will I have to convert 24v back down to 12v?
You would need some sort of 24V to 12V DC to DC converter.
If the sole purpose of the batteries is to feed 12V electronics, it may be better to connect all batteries in parallel (or use one bigger 12V battery) and build a 12V system. -
Re: Series/parallel connections
If I wire the batteries in series for a total of 48v 150ah, then convert it back to 12v for my electronics, will I have 600ah (150 x 4) to work with on my 12v devices? -
Re: Series/parallel connectionsIf I wire the batteries in series for a total of 48v 150ah, then convert it back to 12v for my electronics, will I have 600ah (150 x 4) to work with on my 12v devices?
That is so: four 150 Amp hours @ 12 Volts in series is 150 Amp hours @ 48 Volts. In parallel it's 600 Amp hours @ 12 Volts.
Not much sense in re-wiring the bank between charging and running because you need the same amount of power to charge either way too. -
Re: Series/parallel connectionsCariboocoot wrote: »That is so: four 150 Amp hours @ 12 Volts in series is 150 Amp hours @ 48 Volts. In parallel it's 600 Amp hours @ 12 Volts.
Not much sense in re-wiring the bank between charging and running because you need the same amount of power to charge either way too. -
Re: Series/parallel connectionsI wouldn't be rewiring between charging and running. What I meant to ask was if I charged the batteries at 48v from the solar panels, then used a DC-DC converter to go from 48v to 12v, will I have 600ah or 150ah to work with after it's been converted to 12v?
The reason why Watts were invented.
150 Amp hours @ 48 Volts = 7200 Watt hours
300 Amp hours @ 24 Volts = 7200 Watt hours
600 Amp hours @ 12 Volts = 7200 Watt hours
The difference here is that there is some loss of power when run through a converter.
However, finding a 48 Volt to 12 Volt converter is more difficult than a 24 to 12. -
Re: Series/parallel connections
If you had two 250w solar panels (24v nominal @ 8.15a each), would you wire them in series or parallel?
The end result will always be powering 12v electronics, but I can't put five 100w 12v panels in parallel because I would need like 00 AWG wire to carry the current. How would you build the system if you had four 12v 150ah batteries that powered 12v electronics (assume 1800wh load per day)? -
Re: Series/parallel connectionsIf you had two 250w solar panels (24v nominal @ 8.15a each), would you wire them in series or parallel?
The end result will always be powering 12v electronics, but I can't put five 100w 12v panels in parallel because I would need like 00 AWG wire to carry the current. How would you build the system if you had four 12v 150ah batteries that powered 12v electronics (assume 1800wh load per day)?
A true 24 Volt nominal panel will have a Vmp of 35. Some "24 Volt" panels have a Vmp of 30 or so. You need to check that Voltage spec. In any case if used with a PWM type controller you will get the current @ battery Voltage, not the full power of the panel. So on a 250 Watt panel you'd have 7 Amps @ 35 Volts but at the battery you'd have up to 14.8 (charging Voltage) @ 7 Amps or only 105 Watts - less than half the panels capacity.
The solution to this is an MPPT type charge controller, which can down convert the higher panel Voltage and turn it into greater charging current. In that case the one panel would deliver approximately 16 Amps maximum. Two would be up to 32 Amps.
As to whether to put them in series or parallel ... On PWM controller all you get for current is the Imp of the panels. The Voltage would be pulled down to system (battery) Voltage and V-drop calculations would be based on that. With an MPPT controller you would be running 'true array Voltage' down to the controller and V-drop calculations would be based on that. On the whole it is better not to have nominal array Voltage more than 2X system Voltage, so you would use the 24 Volt panels in parallel and be running a maximum of 35 Volts @ 14 Amps to the controller. The controller will make the change to the lower Voltage and higher current.
However if it is a particularly long run from the array the MPPT controller can take both panels in series and still make the conversion at the output. The PWM controller would not do this at all, but would simply pass the equivalent of one panel's current; the other panel would be completely wasted.
You do have to use a good MPPT controller; there are those that do not handle different or high input Voltages. Avoid the Blue Sky controllers for that reason. -
Re: Series/parallel connections
Usually, your best option is to use a MPPT charge controller.
"24 volt" panels are usually Vmp~30 volts, which is not high enough voltage to charge a 24 volt battery bank (really need around 35 to 38 volts). And if you charge a 12 volt bank, you get only about 60% of the rated power from a panel using a PWM controller.
So--Your typical configuration would be to use a MPPT type charge controller with 1-3 panels in series (typically, depends on specific MPPT charge controller) and use the MPPT controller to down convert to 12 volts. Or 2-3 panels in series for a 24 volt battery bank, or 3 panels in series for a 48 Volt battery bank. And then you would add more strings in parallel for higher current/power solar arrays.
MPPT charge controllers are more expensive, normally running in the $300 to $600+ range. With the higher cost controllers having more options and some various voltage/current configuration options (higher Vmp-array support, etc.). Higher voltage arrays allow you to have a longer distance from array to charge controller/battery bank and use reasonable gauge copper wire. Note the controllers support ~12-48+ volt battery banks... But with higher voltage battery banks, the controllers will manage larger Wattage solar arrays (i.e., 60 amps * 14.5 volts = 870 watt array; at 58 volts charging * 60 amps = 3,480 watt array with same charge controller).
-BillNear San Francisco California: 3.5kWatt Grid Tied Solar power system+small backup genset -
Re: Series/parallel connections
Which MPPT controller would you recommend? I was looking at the Morningstar Sunsaver MPPT 15, but wouldn't the output current be exceeded after the 24v was converted to 12v? -
Re: Series/parallel connectionsWhich MPPT controller would you recommend? I was looking at the Morningstar Sunsaver MPPT 15, but wouldn't the output current be exceeded after the 24v was converted to 12v?
Yes, it would. At which point you'd only have 15 Amps. One of those panels would be the limit for that controller.
Rogue has a new 30 Amp controller coming soon, and MidNite may have one as well. However there is the possibility that your 500 Watts of panel could exceed the output capacity of either, so you'd could 'clip' a couple of Amps now and then or go with a Morningstar 45 MPPT http://www.solar-electric.com/motr45ampmps.html
At this point you have to look at two things; how big is the battery bank and what are the prospects for future expansion?
An Outback FM60 is $515 (a better deal than MS TriStar 60 @ $524) and the MidNite Classic Lite 150 is $500 (no display). -
Re: Series/parallel connections
The MS Sunsaver is a very nice controller... It has lower maximum input voltage so you can probably only use 1x "24 volt" panel in series and then add parallel panels. And it only has 15 amp maximum output current. So, my suggested maximum "cost effective" array would be around:- 15 amps * 14.5 volts * 1/0.77 panel+controller derating = 282 watt array
You can put more panels (in parallel) on the MPPT Controller--It just will (safely) limit the output current to 15 Amps in the middle of the day even if more sun/current is available.
If you put it on a 24 volt battery bank, it will output 2x the wattage--But, with the typical GT panels and Vmp~30 volts, will mean that Voc-cold is very close to exceeding the maximum input voltage to this smaller controller (75 volt maximum input voltage would mean the maximum Vmp-array supported would be ~50 volts--too low for two panels in series).
At this point, the next step in controller would be the MS TS MPPT 45 amp controller. And the money piles up... Adding LCD display + remote battery sensor not being cheap.
-BillNear San Francisco California: 3.5kWatt Grid Tied Solar power system+small backup genset -
Re: Series/parallel connectionsCariboocoot wrote: »At this point you have to look at two things; how big is the battery bank and what are the prospects for future expansion?
12V x 600Ah = 7200Wh
7200Wh x 0.5 (50% discharge) = 3600Wh
3600Wh / 0.8 (inefficiencies) = 4500Wh
4500Wh / 5 (sun hours) = 900Wh
So in order to replenish a 50% discharge in one day, I need about 900W. This gives me about 12.5Ah to work with, which is more than enough to power my electronics. I guess my goal is to be able to charge 50% of my battery bank over 4-5 hours of sun. Also, I can get batteries at extremely low cost, so doubling my current bank would be rather easy.
So, if I discharge my bank to 50% I would need an Outback FM60/80? Or would it make more sense to wire a 24V battery bank and use 24V-12V converter to power my electronics? -
Re: Series/parallel connections
Well to charge 600 Amp hours @ 12 Volts you'd would indeed want about 935 Watt array. That is definitely "MPPT territory".
They start to become practical choices at about 400 Watts.
An FM60 Would handle 600 Amp hours @ 12 Volts at up to 10% peak charge current (60 Amps). It would do the same for 24 Volts, but that's actually double the stored capacity and would require twice as much array. So you could start at 12 Volts, see how it works, and then double up to 24 Volts if need be.
Frankly 3600 Watt hours is a lot of off-grid power. Are you sure you actually need all that? It's about 1kW hour more than I use to run the whole cabin. Looking at your user name I'm going to guess "ham radio equipment". -
Re: Series/parallel connections
I'm pretty sure that you don't want a 600AH 12V battery bank with those batteries. That would be 4 batteries in parallel, which would not be good. -
Re: Series/parallel connectionsI'm pretty sure that you don't want a 600AH 12V battery bank with those batteries. That would be 4 batteries in parallel, which would not be good.
What's wrong with 4 in parallel? -
Re: Series/parallel connectionsCariboocoot wrote: »Frankly 3600 Watt hours is a lot of off-grid power. Are you sure you actually need all that? It's about 1kW hour more than I use to run the whole cabin. Looking at your user name I'm going to guess "ham radio equipment".
You would be correct! And no, I probably won't need near that much. I am realistically looking at < 720W when I have EVERYTHING hooked up (radios, phones, etc). But since I couldn't pass up the deal on the batteries, I now have a 600Ah bank that I want to charge via solar. I was going to plan on a MAXIMUM 50% discharge (3600W), so I was interested in seeing what it would require if I ever decided to approach that limit. -
Re: Series/parallel connections
Batteries are not great at current sharing. They have very low internal resistance (~10 milliohms or less) and if there is any variation in wiring length, resistance between the parallel strings, the wiring can "steer" the current to the low resistance path. (smart gauge wiring suggestions).
Other issues can include variation in batteries (batteries are not "identical"), variation in temperature (hot batteries run slightly lower voltage vs cold batteries), etc...
Also, you should have a fuse/breaker per parallel string to limit the current if there is a short circuit somewhere (cable fails, wrench dropped on battery, etc.) which add costs.
And you have many more cells to check electrolyte levels in. As well as can be a pain to find open/shorted cells in a large parallel bank.
However--Now that there are reasonably priced DC Current Clamp Meters--It makes it much easier to go out several times a month and measure the shared charging/discharging current so you can catch problems before they damage your bank.
Personally, from designing power systems for computer systems, I found that paralleling cables for higher current capacity seems to be a losing game... And I would recommend about 3 parallel strings of batteries unless you have no other option. With cabling, it turns out that the "best/lowest resistance" of the parallel power runs is the most likely to fail first. Remember that heating is (I^2)*R -- So if you have 2x the current, you have 4x the self heating. That takes out the first connection, then the current is shared on N-1, and the next lowest resistance connection fails... Etc.
Not to say that paralleling large numbers of batteries together will not work--There are lots of people who do that and are very happy--It is just that it will require more work and $$$ on your part to keep everything happy and safe.
-BillNear San Francisco California: 3.5kWatt Grid Tied Solar power system+small backup genset -
Re: Series/parallel connectionsWith cabling, it turns out that the "best/lowest resistance" of the parallel power runs is the most likely to fail first. Remember that heating is (I^2)*R -- So if you have 2x the current, you have 4x the self heating** . That takes out the first connection, then the current is shared on N-1, and the next lowest resistance connection fails... Etc.
Perhaps an easier way to see it for some people (since lowering the resistance of the cable will simultaneously decrease the R term and increase the I term), is to look at V2/R instead. For a given voltage drop, the heating in each individual wire will be proportional to 1/R for that wire. And once you lose the first wire, V will suddenly rise, making things progressively worse for the other wires.
If your goal is to minimize (or equalize) voltage drop rather than to get close to the maximum carrying capacity of the wires, then the cascading failure will not be as much of a threat.
** But if you cut the resistance in half, in order to get twice the current, then you have only increased the heating by a factor of two relative to the other wires.SMA SB 3000, old BP panels. -
Re: Series/parallel connections** But if you cut the resistance in half, in order to get twice the current, then you have only increased the heating by a factor of two relative to the other wires.
Except, if you cut the resistance by 1/2 (assuming relatively constant voltage drop from end to end on the cable set), the current flow doubles and the I^2*R heating goes up by 4x.
I saw this happen quite a bit on computers and high end test gear... They have 1/2 dozen wires carrying + current, and another 1/2 dozen carrying the return current (log analyzer, computer with multiple modules, even on back plane pins, etc.).
The problem is with very little resistance ("perfect battery sources" like computer power supplies, usually one or two sets of contacts to make plugging modules easier, and small areas to route power wiring)--These cable bundles were designed to carry 6x one wire's worth of current. Without any "ballast" designed into the DC Harness (such as each segment with a wire of known resistance that was >> all other sources of resistance), I found that, typically, the connection points (contacts, etc.) where the highest resistance). So--Any variable resistance contact (tin lead/gold/moving cables around while servicing, age, etc.).
So, I wondered why I was seeing a series of 6 (for example) contacts where one contact would fail (lots of scorching on housing), or I would see an expanding scorched area, with one contact in the middle showing the most charing). The only way that could explain it was I^2R heating--And if the other contacts were not overheating, it was because they were carrying less current. And the only way was because their circuit path had slighting higher resistance.
In the end, from my circuits, I used the 1+1/n method of derating power cables. And from what I have seen (or not seen), I never had any problems.
1 = 100% of cable rated current
1 + 1/2 = 150% of rated single cable current for two parallel cables
1 + 1/2 + 1/3 = 180% of rated current for three parallel cables
Unless the cable resistance was >> than contact resistance.
Or in the case of batteries, the higher the cable/interconnect resistance, the less the variations in cell "resistance"/voltage/etc. affects sharing of current.
Which is short of the opposite of how we design battery interconnects--Normally, we try for as low as cable resistance as possible to reduce voltage drop and energy loss...
Of course, longer term, battery voltage is also a function of specific gravity... So, lower SG cells will supply less current during discharging and accept more current during charging (from a fixed voltage source). There is some "balancing" going on. But warm batteries also have a lower voltage--So during charging, the "warm cells" could accept more current (as they are at a lower voltage) while cold cells do not--So during charging you can have thermal run-away where the warmer cells become hot and accept even more current.
Anyway--I know that I am doing a bit of hand waving here. But the effects are real. But are they enough to cause significant problems for the "average" smaller off grid system--It is a guess.
I try to be conservative and recommend solutions that reduce the potential problems as the detailed analysis could get us lost in the weeds (too many unknowns, too many variables). Why we keep falling back on rules of thumb to get us pointed in the, hopefully, "best" direction when doing the initial specifications.
Other issues, such as checking dozens of parallel battery cells for electrolyte levels are more human factor issues. Doing every month tends to become a pain for most people.
-BillNear San Francisco California: 3.5kWatt Grid Tied Solar power system+small backup genset -
Re: Series/parallel connectionsExcept, if you cut the resistance by 1/2 (assuming relatively constant voltage drop from end to end on the cable set), the current flow doubles and the I^2*R heating goes up by 4x.
Let me check the numbers on that:
Initial power = I2R.
Now we cut the resistance in half and double the current, just as you specified:
New power = (2I)2(R/2) = 2I2R.
Looks to me like it doubles, not quadruples?
No disagreement with the rest of your post. :-)SMA SB 3000, old BP panels. -
Re: Series/parallel connections
Opps--Yes, you got me... It could also go the other way, the other contacts/connections become dirty (i.e., their resistance goes up)--And then we would see a 4x heating effect on the good connection.
-Bill "waving hands furiously" B.Near San Francisco California: 3.5kWatt Grid Tied Solar power system+small backup genset -
Re: Series/parallel connectionsOpps--Yes, you got me... It could also go the other way, the other contacts/connections become dirty (i.e., their resistance goes up)--And then we would see a 4x heating effect on the good connection.
A definite problem with paralleling anything to get around a hard capacity limit. (Fuses for example!)SMA SB 3000, old BP panels.
Categories
- All Categories
- 228 Forum & Website
- 136 Solar Forum News and Announcements
- 1.4K Solar News, Reviews, & Product Announcements
- 199 Solar Information links & sources, event announcements
- 895 Solar Product Reviews & Opinions
- 256 Solar Skeptics, Hype, & Scams Corner
- 22.5K Solar Electric Power, Wind Power & Balance of System
- 3.5K General Solar Power Topics
- 6.7K Solar Beginners Corner
- 1K PV Installers Forum - NEC, Wiring, Installation
- 2.1K Advanced Solar Electric Technical Forum
- 5.6K Off Grid Solar & Battery Systems
- 428 Caravan, Recreational Vehicle, and Marine Power Systems
- 1.1K Grid Tie and Grid Interactive Systems
- 653 Solar Water Pumping
- 816 Wind Power Generation
- 624 Energy Use & Conservation
- 618 Discussion Forums/Café
- 311 In the Weeds--Member's Choice
- 75 Construction
- 124 New Battery Technologies
- 108 Old Battery Tech Discussions
- 3.8K Solar News - Automatic Feed
- 3.8K Solar Energy News RSS Feed