48VDC generator head
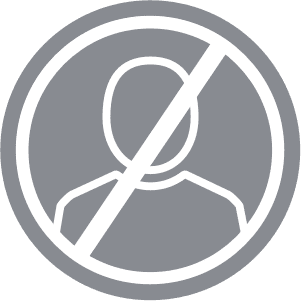
ChrisOlson
Banned Posts: 1,807 ✭✭
I want to build a small 48VDC generator to keep our bank up during peak load times in the evening in the winter time when the wind isn't blowing. We had a gas charger for years with a Techumseh 6 horse on it, and I miss that thing because it worked really good.
I have a little Hatz 1B20 diesel that was given to me because it didn't run. I fixed the injection pump and got it running. I'm looking for a suitable small 2 kW or so 48VDC generator head to drive with it to build a charger again. I could build a generator for it from scratch, but I'm looking for something commercially made so I can get the unit built and get it working. Does anybody know where I might find such a thing?
Thanks!
--
Chris
I have a little Hatz 1B20 diesel that was given to me because it didn't run. I fixed the injection pump and got it running. I'm looking for a suitable small 2 kW or so 48VDC generator head to drive with it to build a charger again. I could build a generator for it from scratch, but I'm looking for something commercially made so I can get the unit built and get it working. Does anybody know where I might find such a thing?
Thanks!
--
Chris
Comments
-
Re: 48VDC generator head
You might try Alpha Technolgy or Polar and see if they will sell you just eh gen head.
http://www.polardcmarine.com/polarpower/
http://www.alpha.ca/web2/products/generators/item/alphagen-portable?category_id=28
Tony -
Re: 48VDC generator head
What are you asking us for? You're the generator guy
How about a permanent magnet DC generator? Not too expensive on ebay, there's currently a 4.8kW 48V one available for $400. -
Re: 48VDC generator head
I'd prefer a wound field generator so it can be externally excited and regulated to precisely match shaft power at variable engine speed.
--
Chris -
Re: 48VDC generator head
If you can DIY, Leece Neville makes a few 48v alternators. The MDA5909 is rated at 1920W. (52vdc @ 40a). Has a .875 OD shaft and utilizes the common J180 3-point Mount. No idea what shaft speed produces their specs. There's also a decent selection of milsup units available. -
Re: 48VDC generator head
You may want to look at Electric Vehicle DIY component shops. Series-wound motors rule for high performance EVs: tons of low-end torque! My first hybrid vehicle used 12" Advanced DC series-wound in parallel with a Kohler two-banger. It was a real hot-rod. Although most series-wound motors for EVs are too big for your application, smaller units may be available. Advanced DC has been around for a long time and series-wound DC motors is their specialty.
As noted in other posts, I have also been investigating a DIY 48VDC generator. When I laid out the draft mechanization drawing, I used a motor from a DIY EV shop as the concept design. It was 6kW, a bit larger and more expensive than your plans. -
Re: 48VDC generator headYou might try Alpha Technolgy or Polar and see if they will sell you just eh gen head.
http://www.polardcmarine.com/polarpower/
http://www.alpha.ca/web2/products/generators/item/alphagen-portable?category_id=28
Tony
http://www.ebay.com/itm/HONDA-ALPHAGEN-CABLE-TV-TELECOMMUNICATIONS-DCX3000-36V-48V-DC-GENERATOR-NEW-/261130685229?pt=BI_Generators&hash=item3ccc9a0b2d -
Re: 48VDC generator head
I can't find a suitable, economical 48 volt generator anywhere. I've decided what I'm going to do is build a 8 pole permanent magnet three-phase generator and rectify it to DC. If I build it for 80 open DC volts at 2,200 rpm idle and 131 open DC volts at 3,600 rpm I can run the high voltage DC thru a Classic 150 controller that will handle the bulk/absorb on the bank.
The nice thing about using high voltage DC from the generator is that I can use much smaller wire. At full power and 131 open volts with a wind turbine power curve programmed into the controller to "clamp" it to 127 volts with a .15 ohm stator I can send 27 amps @ 128 volts, or ~3.4 kW to a Classic without using 4 gauge cables to get from the gen to the utility room. The Classic is about 92% efficient so I calculate it will put out about 3.1kW to the bank for charging at full throttle.
That little Hatz diesel has about 4.2 kW shaft power at our elevation here. And I can build a 8 pole three phase generator that will run over 90% efficiency @ 3.4 kW - I've built dozens of 'em for wind turbines. There's a little loss with a 1.4V forward drop in the rectifier and some transmission loss in the wiring to the utility room @ 27 amps in 8 gauge wire. But not much. I think it will be a pretty close match to shaft power.
It will probably be after the first of the year before I get to building my little DC genset. I'm working on a 20 pole 150 volt wind turbine generator that I have to get done first. I got a coil group wound for one phase, but when I ordered magnets for this thing the other day I didn't order enough extra to build another generator right away
Attachment not found.
--
Chris -
Re: 48VDC generator head
I'm not familiar with the voltages you guys use so this might not be practical, but if normal 110V 3 phase alternators are easy to find, then you could use one of those instead of a PMA, then onto 3 110V-60V transformers and a bridge rectifier. This way you can draw 110V AC from it too.
Using a midnite classic as a transformer seems an expensive option. In all cases it would be really neat if you could link the output voltage to the RPMs, so could effectively build a fuel efficient battery charger that slows down for absorb.
Or would it be possible to use 2 x 24V truck alternators in series? -
Re: 48VDC generator headChrisOlson wrote: »I can't find a suitable, economical 48 volt generator anywhere. I've decided what I'm going to do is build a 8 pole permanent magnet three-phase generator and rectify it to DC. If I build it for 80 open DC volts at 2,200 rpm idle and 131 open DC volts at 3,600 rpm I can run the high voltage DC thru a Classic 150 controller that will handle the bulk/absorb on the bank.
The nice thing about using high voltage DC from the generator is that I can use much smaller wire. At full power and 131 open volts with a wind turbine power curve programmed into the controller to "clamp" it to 127 volts with a .15 ohm stator I can send 27 amps @ 128 volts, or ~3.4 kW to a Classic without using 4 gauge cables to get from the gen to the utility room. The Classic is about 92% efficient so I calculate it will put out about 3.1kW to the bank for charging at full throttle.
That little Hatz diesel has about 4.2 kW shaft power at our elevation here. And I can build a 8 pole three phase generator that will run over 90% efficiency @ 3.4 kW - I've built dozens of 'em for wind turbines. There's a little loss with a 1.4V forward drop in the rectifier and some transmission loss in the wiring to the utility room @ 27 amps in 8 gauge wire. But not much. I think it will be a pretty close match to shaft power.
It will probably be after the first of the year before I get to building my little DC genset. I'm working on a 20 pole 150 volt wind turbine generator that I have to get done first. I got a coil group wound for one phase, but when I ordered magnets for this thing the other day I didn't order enough extra to build another generator right away
--
Chris -
Re: 48VDC generator headUsing a midnite classic as a transformer seems an expensive option. In all cases it would be really neat if you could link the output voltage to the RPMs, so could effectively build a fuel efficient battery charger that slows down for absorb.
I already got four Classic 150's. The reason I'd be running the little generator is probably to maintain the bank during continuous heavy draw times like winter evenings when it's really cold and the wind isn't blowing. So all I have to do is put another breaker in the solar combiner to hook the little generator up to, go to the Mode menu on the Classic and select a different input source, start the little generator and voila! Diesel Powered Solar Panels! 8)Hatz rates that engine at 3.5kW @ 3600 (I assume at sea level), so how did you arrive 4.2kW? Just curious.
I thought I had posted this but I don't know where the post went. Anyway - I assumed it was 6 hp. The engine was given to me because it wouldn't start. There's a snap ring on the injection pump that came off so the pump plunger wasn't following the cam. I put the ring back on and it runs fine. So I never actually looked to see how much power it has, and it don't say on it. I see it has 4.8 hp. No matter - I can match whatever with the Classic on it. If I need more power maybe I can put a little turbocharger on it and bump the fuel rate up a bit
--
Chris -
Re: 48VDC generator head
Variable RPM Diesel DC Generator with an MPPT controller (Midnite Classic)--Now that could be a marriage made in heaven for optimum use of fuel. Use some sort of biodiesel fuel (i.e., oils from seeds), and it actually could be very sustainable.
-BillNear San Francisco California: 3.5kWatt Grid Tied Solar power system+small backup genset -
Re: 48VDC generator head
I've got a little lister petter diesel that I was looking to do the same think with. I've been looking into the Axial flux alternators myself and as stated above I think that is a great way to do it.. One problem I'm having is figuring out how to build the axial flux to fit my needs. If you wouldn't mind sharing that part of your project when you get to it that would be awesome
Thanks
Rob -
Re: 48VDC generator head
Rob, while an axial might work OK on a low rpm engine like a Lister, on a high rpm engine like my little Hatz I'm going to build a radial flux generator for it. The problem with axials at high rpm is the centrifugal forces on the magnets and rotors. I've run them successfully up to 1,500 rpm on wind turbines (with gearboxes). But they won't take much more than that, even with the mags pinned, before you get an explosion.
--
Chris -
Re: 48VDC generator headVariable RPM Diesel DC Generator with an MPPT controller (Midnite Classic)--Now that could be a marriage made in heaven for optimum use of fuel. Use some sort of biodiesel fuel (i.e., oils from seeds), and it actually could be very sustainable.
Bill, when I emailed Ryan and boB about this and asked them if they thought it would work (they said it should), I had the theory that I can control the throttle on the little Hatz with a stepper motor using the AUX 2 PWM drive on the Classic with Waste Not.
The Waste Not mode pulses that PWM more and more as the batteries charge up. I've been using it for quite some time to operate my water heating system. I'm pretty sure the PWM output of the Classic can be used to drive a stepper motor to make the engine progressively idle down as the bank gets charged up. I haven't tested that yet, but the pulse width and voltage is about the same as used on most automotive applications for things like fuel injector drive and throttle control for cruise controls.
--
Chris -
Re: 48VDC generator headChrisOlson wrote: »Bill, when I emailed Ryan and boB about this and asked them if they thought it would work (they said it should), I had the theory that I can control the throttle on the little Hatz with a stepper motor using the AUX 2 PWM drive on the Classic with Waste Not.
The Waste Not mode pulses that PWM more and more as the batteries charge up. I've been using it for quite some time to operate my water heating system. I'm pretty sure the PWM output of the Classic can be used to drive a stepper motor to make the engine progressively idle down as the bank gets charged up. I haven't tested that yet, but the pulse width and voltage is about the same as used on most automotive applications for things like fuel injector drive and throttle control for cruise controls.
--
Chris
Only potential problem that jumps out at me is that a PWM output where the duty cycle directly controls the load is not going to be directly compatible with a stepper motor situation where the total count of pulses will control the load. Just what did you have in mind for the action of the stepper motor? If the throttle opening were proportional to motor speed rather than to shaft position you would have something. (Or am I just missing the point somehow?)
If you had a pulse train from the engine speed driving the stepper in one direction and the Classic pulse train drive it in the other direction, you might be able to get the engine speed proportional to the Classic output. But I am not sure that would be stable, since there would be a tendency to overcorrect and hunt.
When the rate of change of velocity (i.e. the acceleration) is inversely proportional to the offset from the set point, you get an oscillator.SMA SB 3000, old BP panels. -
Re: 48VDC generator head
The Classic's PWM does not control the load. It's merely an output based on battery voltage. The PWM CAN be used to control a load like I do with my water heating system where it drives a AC SSR that turns the 2,000 watt AC heater elements on. But I can also be used to control anything that works with PWM.
In the case of the generator when the voltage gets to the charge stage set point, minus the offset in the AUX 2 setup menu, the PWM starts pulsing. The more power that is applied to the situation, the higher the voltage will try to go, and the more the PWM pulses. So if the generator is charging and the voltage reaches Absorb set point, the PWM is going to start pulsing. The PWM signal can be used to operate a stepper motor to slow the engine down and reduce output. Now, output is reduced so the system voltage drops, the PWM reduces the pulse voltage and makes the engine speed back up, putting out more power.
PWM is very smooth at the high frequency it operates at in the Classic, so it will find a "balance" of how much generator output is required to maintain charging voltage. This I know beyond the shadow of a doubt will work.
The only thing I haven't tested is if the stepper motor I got, which is off a Cummins genset with an electronic throttle, will work with the Classic's PWM drive. The stepper motor says 0-5.5 VDC - 0 volts the plunger is fully extended, 5.5 volts the plunger on it is fully retracted.
--
Chris -
Re: 48VDC generator headChrisOlson wrote: »
The only thing I haven't tested is if the stepper motor I got, which is off a Cummins genset with an electronic throttle, will work with the Classic's PWM drive. The stepper motor says 0-5.5 VDC - 0 volts the plunger is fully extended, 5.5 volts the plunger on it is fully retracted.
--
Chris
Aha! What you are calling a stepper motor is what I would call a linear actuator. If there really is a stepper motor inside your assembly, there is also a control circuit which drives the stepper motor in one direction or the other depending on relation between the applied DC voltage and the current actuator position.
I was thinking about each pulse driving the stepping motor one increment of rotation.SMA SB 3000, old BP panels. -
Re: 48VDC generator head
It could be. Cummins calls it a stepper motor and it runs the throttle lever on an old NT-series genset with electronic frequency control. Like I said, I haven't tested it yet to see what it does with the Classic.
This is for Rob - (Fordguy64) - is your Lister a 900 rpm engine? If it is this generator off my 12G turbines will work on it:
https://picasaweb.google.com/110979388690716770927/12GTurbineBuild#5757339619529501442
It's got pinned mags and I run that same generator at 1,200 rpm on the 350 MPPT turbines. It has 8.54 rpm/DC volt so at 900 rpm it makes 105 open DC volts. The gen rotors are 254mm. The winding resistance in wye is .47 ohm and the windings will handle 36 amps continuous. Your loaded voltage is always less than open. But if you "clamped" the voltage down to like 90 with the Classic, that would give you 32 amps @ 90 volts, or ~ 2.9 kW input to the Classic. I'd have to look up the efficiency curve to see what it is at 32 amps continuous output, but I think it's over 90%, or very close to it, so it will run fairly nice and cool at that power level.
If you don't have facilities to machine rotors, I got a set here with 1" bores (fit on a 1" OD PTO shaft), with the pin holes for the mags already drilled. I quit building generators with neo mags when the price went thru the roof, and designed new ferrite magnet generators instead. So these are a little rusty from laying around in my shop for the last two years, and I never sprayed them after I machined 'em:
Attachment not found.
The stator has 50 turns, 9 coils, 13 AWG windings and I can give you all the pin dimensions for the coil winder if you want to build one for your Lister. If your Lister is a 1,800 rpm engine, just wire the stator delta (or reduce the number of turns in the coils to 25) and it would still work. I have spun these small diameter generators up to 2,000 rpm and they hold up fine. But the bigger ones with 355mm rotors fly apart over 1,500 rpm. And the explosion is really impressive. It puts holes in the shop ceiling and blows the generator right off the test stand.
--
Chris -
Re: 48VDC generator head
There's a sharp gent (in Kansas I believe) that builds custom units based on the high efficient Picher Eagle PMG. Same variable engine RPM idea being discussed here. These PMG's are claimed to be 90% efficient. I'd love to play with one, but are a bit more $ than I can spend right now.
Video: http://www.youtube.com/watch?v=1CvYcCUZqOI
Some details: http://www.microcogen.info/index.php?topic=2860.0 -
Re: 48VDC generator head
Yes, permanent magnet generators are usually more efficient than wound field because the field strength is incredibly powerful compared to wound field. This allows windings with fewer turns of bigger wire which reduces internal resistance of the winding. They are also typically wild AC and run at very high frequencies - usually in the hundreds of hertz on a wind turbine.
The downside to permanent magnet generators is that they are extremely dangerous to work with during assembly, dis-assembly and handling rotors. The attraction force between the two rotors in the above generator that I referenced for a wind turbine is around 1,700 lbs. If anything slips while jacking a rotor down, and you happen to get your fingers in between you will not have any fingers left. When an uncaged rotor is removed from the generator it must be handled with care and packed away where metal objects can't be attracted to it. An uncaged rotor will turn metal objects in the shop into dangerous missiles from incredible distances, and if you happen to be in between a rotor and something it suddenly decides it wants, you're not going to be all that impressed with the situation.
Four years ago me and two other guys were replacing the stator in a Proven 7.5 kW turbine, jacking one rotor down. The jacking screw slipped out of the socket and one of the guys got his whole hand in between the rotor and the stator. It took us about 15 minutes to get the rotor jacked back off the stator to get him out. His hand was not saveable - they amputated it about 4" above his wrist.
--
Chris -
Re: 48VDC generator headVariable RPM Diesel DC Generator with an MPPT controller (Midnite Classic)--Now that could be a marriage made in heaven for optimum use of fuel.
I'm not entirely convinced of this. MPPTs use a closed-loop feedback mechanism to "search" for the global peak power on a Voltage-Current curve. This could be analog or digital. Most MPPTs on the market probably use somewhat advanced algorithms to search for the global peak. I designed MPPTs in the late 1990s. Some of my designs used a PIC microcontroller to "dither" incrementally up and down the V-I curve to search for maxima. A problem occurred if the the V-I curve had bumps. Sometimes it would interpret a bump (a local maxima) as the peak (global maxima). New algorithms are probably more advanced.
The V-I curve of a generator running at fixed conditions may be predictable. But in real life, when the MPPT starts creeping up the current (I), the engine will be loaded, which will change either engine torque or speed output, or both. This will alter the shape of the V-I curve, which will cause the MPPT to continue searching, which will continue change engine loading, which will therefore result in a continually changing V-I curve with the MPPT madly trying to keep up. One of two things will eventually happen: either the MPPT will settle on a local maxima (not necessarily the global maxima), or the system will oscillate as the MPPT constantly searches up and down the V-I curve while loading and unloading the engine.
In other words, it runs the risk of the feedback loop consisting of the MPPT and engine controller going unstable. A real nerd would figure out the time constants and plot the poles and zeros. Even if the engine just has a carb and a throttle, the engine has a time constant and a response characteristic. The rest is up to the algorithm in the MPPT. Maybe some of the advanced algorithms are designed to prevent oscillations, but were they really expecting to be connected to a complex living, breathing entity like an engine?
Another question: is it worth it? Would you really increase system efficiency by putting a switching power supply between the generator and the battery, whereas a straight-feed from a DC gen head into the battery is pretty efficient? I suppose the hope is the engine's energy conversion efficiency could be increased by finding the best torque:speed point on the engine's efficiency (BFSC) map?
My conclusion from this thought-exercise is a MPPT could increase an engine's efficiency by optimizing the engine's torque:speed ratio by changing the output's current:voltage ratio. However, most engines have a similar BFSC (example below). The best efficiency for a given RPM is a bit below the maximum torque, with the best overall efficiency at about 1/3 of the engine's maximum rated RPM. That means operate the engine hard, preferably about 1/3 of the rated maximum RPM. I don't need a MPPT to figure this out.
Attachment not found. -
Re: 48VDC generator headI'm not entirely convinced of this. MPPTs use a closed-loop feedback mechanism to "search" for the global peak power on a Voltage-Current curve.
I use Classics on all my wind turbines. You use the Wind Track mode in the Classic and program a curve for it. A piston engine generator is no different than a wind turbine - just uses a different engine.
The main advantage is not having to use huge cables from a high amperage DC genset to the battery. With the Classic I can transmit power at 120 VDC from the genset to the controller at low amps, and the high amp wiring is short from the Classic to the battery.
--
Chris -
Re: 48VDC generator headChrisOlson wrote: »A piston engine generator is no different than a wind turbine - just uses a different engine.
Not quite. The wind generator has a power:speed map (which relates to its torque:speed map) where you are attempting to find global power maxima. Therefore, a Maximum Power Point Tracker (MPPT) is useful. Since power is a linear relationship of torque and speed, it's relativity easy to find. A piston engine has a specific fuel consumption (BSFC) map, where you are not trying to maximize power. You're trying to minimize fuel consumption, which is a highly nonlinear relationship of the torque:speed relationship. Wind turbine output map below. It is simple to envision how a MPPT finds maximum power by finding the correct turbine speed at a given wind velocity:
Attachment not found.ChrisOlson wrote: »The main advantage is not having to use huge cables from a high amperage DC genset to the battery.
Then you're using the MPPT as a voltage step-down rectifier for high-voltage transmission to low-voltage termination. I understand that reason. It saves you either using big cables, or lowers transmission efficiency losses through smaller cables. Let's put transmission losses aside for a moment while examining a fundamental question: does a MPPT make sense for piston engines?
I charted constant-power curves onto the example BSFC engine map. Every engine has a unique BSFC map. You can find BSFC maps for most reputable engines. I scaled the example map to illustrate a 6kW (peak) engine. Notice the 2.5kW and 3.3kW lines intersect the 36% fuel efficiency region (some maps use grams of fuel per kJ, or some other similar metric). Running the engine at 1.6kW or 4.1kW intersects the 35% region. Even the 820W line intersects the 33% region.
Attachment not found.
Lessons: this is why fixed RPM generators have such poor fuel efficiency at low power and why inverter generators maintain such good efficiencies across variable power loads. This is the fundamental rationale for variable RPM systems!
Continuing the analysis, good efficiency (>33%) is maintained at full torque from 2-3kW. If the engine is operated just a hair below full torque, good efficiency between 33%-36% can be maintained from 1kW to 4.5kW!
Using a MPPT would attempt to maximize power (Maximum Power Point Tracker), which would attempt to draw more power out of the engine by either wanting the generator to spin faster or raise torque, trying like crazy to get to the 6kW peak, although the engine's throttle says differently. The MPPT would be fighting the engine's throttle by always over-spinning or over-loading the engine in attempts to get more power.
To answer the question if a MPPT can optimize a piston engine efficiency, I think the data suggests "no". The engine's throttle position establishes a constant-power curve, and constant-power is incompatible with the goals of a power-maximizing device.
So envision as a thought experiment a fictitious Maximum Fuel Efficiency Tracker (MFET). This device would modulate the generator's Voltage:Current output to move the engine's Torque:Speed behavior to the best fuel efficiency region. This device would need a fuel sensor to monitor and optimize fuel consumption.
Pretend the MFET costs a few percent of efficiency due to switching losses and power electronics. Since the example engine map has already proven that efficiencies could be easily maintained between 33%-36% through the primary operating region without a MFET, adding a MFET would only optimize by (at most) a few percent. Look at the 2.5kW line. There's not much improvement a MFET could make if the engine is already operating near maximum torque. So in this case, the MFET would create a net loss due to its own power electronics efficiency penalty.
To answer the fundamental question if modulating output current and voltage using power electronics to optimize a piston engine's BSFC efficiency, I think the data suggests "no". In the best-case scenario, only a percent or two may be gained.
However, if the MPPT is being used as a voltage step-down device to prevent transmission losses, it may be a net gain. -
Re: 48VDC generator headSo, to answer the fundamental question if a MPPT can optimize a piston engine, I think the data suggests "no".
The idea is not to optimize a piston engine. I can program a wind curve in the Classic to match electrical loading to available shaft power at any rpm I want to run the engine at. The idea is to optimize electrical efficiency. DC generators have absolutely horrible electrical efficiency on battery charging duty at high outputs - take a look at the Alten 2480 or 4850 as an example.
Our battery bank is in a utility room on the side of the house so if I want to charge the bank at full output how long do you think my wife is going to put up with a noisy Hatz diesel running only 10 feet away from the battery bank?
It's going at least 75 feet away from the house, on the other side of the shop, so we can't hear it running in the house. The total wire run length to get the power to the bank is about 85 feet by the time you make all the corners. By running that generator at 120 volts instead of 60 I cut the amps in half for the same power output, improving power efficiency in the generator head itself, the rectifier, and power transmission from the genset to the utility room.
If people want to put their DC genset right by the bank and listen to it run that's fine by me. If people want to lay 2/0 cable to get the amps from the generator to the bank from further away, that's fine by me too. But I'm not doing either. I already got a Classic, I got a place to hook the generator up by the solar array far away from the house where we won't be able to hear it running, so I'm going to use the high voltage/low amperage method "just because I can".
There's one other advantage to using the Classic on a DC genset - it provides a state-of-art charge controller that will do proper bulk/absorb and even EQ if you want - with temperature compensated charging stages.
--
Chris -
Re: 48VDC generator headChrisOlson wrote: »The idea is not to optimize a piston engine.
OK, so please forgive me as I continue to beat this silly. It was postulated that Maximum Power Tracking may be a good match for a genset. I'm still exploring that question outside of the bounds of transmission voltage. I agree your novel implementation of the Classic is intriguing.
However, I'm still on the topic of what happens to a spark-ignition engine loaded with a MPPT? So digging around, I found some gasoline engine maps on constant-throttle. The MPPT will attempt to maximize power at a given throttle position:
Attachment not found.
So assume the same 6kW engine is being used as the BSFC example in my previous post. And assume these constant-throttle maps are representative of an average engine. Lots of assumptions, but as a rule, most engines follow generic representative patterns.
If full throttle represents 6kW, these curves show the MPPT will unload the engine (reducecurrent) and find high RPM (high voltage), which will create the maximum (voltage x current), or (speed x torque) on the engine. The specific fuel consumption suffers, going from 0.45 to 0.55. This is because high RPMs, although delivering maximum power, also contribute lots of frictional losses.
So look at the half-throttle position. The MTTP will unload the engine (reduce current) to let the engine spin to high RPM until power starts to drop off again. This is at 4000 RPM. Compare this to the efficiency curves, again, the MPPT's favorite spot is not the most efficient spot.
The situation is acceptable at quarter throttle. The maximum power at quarter throttle nearly matches maximum efficiency.
So a MPPT will attempt to maximize power at a given throttle position, not maximize efficiency. The conclusion is a MPPT is not suitable for controlling the load on a spark-ignition engine. This is because the way a carburetor works by drawing fuel via Bernoulli's principle into the airstream. As the engine RPM changes, so does the mass air flow, which changes the venturi velocity, which changes the Bernoulli effect.
Some caveats: Diesel is completely different. The output of Diesel is controlled by injectors, not by Bernoulli's principle. In addition, the engine is not the only device to consider - as Chris points out, the electrical head itself also has its own family of efficiency curves. To fully solve this question, the entire system must be considered - the Diesel BSFC map multiplied by the electrical generator efficiency map - and then trace constant-power and constant-fuel curves on top of the composite map.
I'm beating on this question because I'm wondering if a MPPT can indeed maximize a genset's ultimate efficiency. The exercise thus far suggests that maximizing power is not the same as maximizing efficiency. Diesel may be different. And when the engine's efficiency is translated through the generator's electrical efficiency, it may further change the conclusions. -
Re: 48VDC generator head
swmspam - interesting topic for sure - and it's not silly.
I have to point out, however, that with wind turbines and piston engine generators we do not use MPPT. It is a programmed power curve - a dyno curve that fits the unit being controlled. There are various curves for different wind turbine models on my website:
http://dairylandwindpower.us/Classic150_PowerCurves.html
The controller loads the wind turbine (or piston engine generator) identically to the way a dynamometer would load it. With a piston engine there are only two parameters that are adjustable for a given load - speed and fuel rate. Shaft power is a function of speed and torque (hp = torque x rpm / 5252). So if speed is reduced, torque has to increase to power the load. In order for torque to increase at the lower speed, the fuel rate has to be increased. This is where the brake fuel curve is established - in torque rise as speed is lost due to loading by the dyno.
So you have to forget the MPPT concept. Go to the dyno room instead. That's what we're doing here. That Classic, in conjunction with the electrical components the engine is powering (generator as the dyno, Classic as the controller, battery as the load bank) is the same thing as an eddy current dyno. And we get a torque reading from the dyno in the form of amps shown on the Classic's display, and a speed reading in the form if input volts on the Classic's display, and a hp reading in the form of real time watts. Subtract out the losses in the electrical equipment and we get brake power at the flywheel.
As you can see by the various power curves I have for wind turbines, I can make a wind turbine run any way I want with a Classic controller on it. I can do the same with a piston engine driving a generator.
Now we get the meat of the issue - and why you will not match a Classic controlled gas or diesel DC generator with a unit that is direct hooked. And why you can't match a Classic controlled wind turbine with one that is direct hooked to the bank. Ohm's Law is the determining factor. And the biggie version of Ohm's Law is I^2R power dissipation losses.
Let's consider a generator with a .5 ohm stator charging a battery bank at 60 volts. A permanent magnet generator develops a fixed amount of voltage for every rpm it turns because it has no variable field. The only thing that affects this is reactance losses in iron cores, but that's a different issue. So if this generator develops 80 open volts at 2,200 rpm, at 3,600 rpm it will develop 131 open volts. In order to get amps from this generator we have to "clamp" it to a lower (loaded) voltage.
OK, so let's try to charge our battery bank at 40 amps. With the direct hooked setup with the engine running at 3,600 rpm the generator is going to try to push 142 amps from the stator when you hook it up to the 60 volt battery. The engine won't maintain speed and it will lug down. When it lugs down we lose speed and have to increase torque. The balance will be found at 2,200 rpm - that's where you'll get 40 amps and the stator will be dissipating 800 watts. The power input requirement to that generator is 3.2 kW, 4.29 hp, or 10.24 lb-ft torque @ 2,200 rpm. The power efficiency of the generator is 75% - 25% of the shaft power being fed to it is converted directly to heat
With the Classic controlled unit, I can "clamp" the generator at a higher voltage of 120 and only require 20 amps from the generator. This requires an engine speed of 3,575 rpm. The stator is dissipating 200 watts. Shaft power requirement is 2.6 kW, 3.48 hp, or 5.11 lb-ft torque @ 3,575 rpm. The power efficiency of the IDENTICAL generator at the same power output (2.4 kW) goes to 92.3%.
Now - with the Classic I can adjust this to whatever I want to achieve the best brake fuel curve/generator efficiency combination just by pressing some buttons because it's a dynamometer. You can try to wind a generator for a direct hooked setup that's most efficient at peak output, and then you end up with too high of a engine speed requirement to get to the minimum 60 volts required for charging, meaning you'll never be able to idle the engine to provide charging current at the required 60 volts. Or you can throw massive amounts of materials at the generator and build a monstrosity that develops the required voltages with low enough resistance to get decent power efficiency - and end up with a small fortune just in the generator, not to mention an incredibly big and heavy unit.
No matter what you try to do with a direct hooked generator you can only tune it for one specific output at peak efficiency and live with a reduction in efficiency on each side of that. I will beat you with a Classic controlled one every way from Sunday with a generator that never falls below 90% power efficiency from cut-in to full rated output, and live with a very small conversion loss in the controller. Your best attempt at matching the best brake fuel curve to output with a direct hooked generator will be defeated by the increase in electrical efficiency I can get with the Classic with the same amount of fuel burned. There's a reason utilities use high voltage transmission lines stepped down to terminal voltages with transformers instead of generating 240 split phase right at the power plant.
I'm ALWAYS up for challenges. I'll build mine, you build yours, and we'll get together and run 'em with some test equipment and see who wins. We'd have to establish some baseline rules:
- that we both have to use the same engine - I'd propose a Honda GX200 because they're cheap and readily available
- use the same wire run from the generator to the battery bank - I'd set it at 20 feet to give the direct hooked unit a decent chance
- use a 24 volt battery bank (although I'd like to point out I can switch my setup to 48 volts by pressing some buttons on the Classic and loading a different curve for it)
- we can each use whatever generator we feel is necessary to do the job
The challenge is to simulate an off-grid cabin - we're going to charge a 232ah 24 volt battery bank (4 Trojan T105's) that starts out at 50% SOC, with a constant 1,000 watt load on the bank, to float, and see who can do it on the least amount of fuel. And once the generator is started you can't touch it - it has to do the job from start to float, and shut itself down (I'm just using the Classic's AUX 1 ON in Float to shut the generator down), without any intervention from a human. And all thru this the DC genset will be required to maintain PRECISE temperature compensated charging parameters to insure longest bank life and battery care possible in the long term.
That $650 for a Classic is starting to look pretty cheap when you want a REAL DC genset, huh?
And in the end we both end up with a DC genset for our homes, have a lot of fun, and have an excuse to drink beer.
I'd LOVE doing that. Wanna do it?
--
Chris -
Re: 48VDC generator headChrisOlson wrote: »I'd LOVE doing that. Wanna do it?
OK, so this is about the most fun I've had all day.
I agree the MPPT is a bad idea. I wanted to drive my conclusion with data that a power tracker is unsuitable for engine control. DTO (Data Trumps Opinion). It was fun exercise. I love BSFC maps. I based my dissertation on BSFC maps. I need to buy a Diesel, so I can start learning more. Most of what I know is spark-ignition. There's a dyne down the street that I can easily access, and it's starting to call my name.
I called Advanced DC this morning and talked to an applications engineer. He recommended the #A00-4009 6.7" series-wound motor, 80A/6hp continuous, 350A/28hp peak. It runs $850 from a DIY electric vehicle shop. Although some juice is lost in the field coil, some is recovered by optimizing the torque:speed map of the motor. For example, the field coils can be cranked up to get more voltage at a lower RPM. So absorption and float stages are operating at a low RPM instead of revving the engine like would be required with a PM head. The key is to keep RPMs low and torque high to live on the high-efficiency island of the BSFC map. If RPMs are tied to battery voltage, fuel economy will suffer badly during absorption and float stages.
Now if you have some programmable power electronics (as your Classic), it decouples the output voltage from the generator head. So you can use a PM motor with a fixed Voltage:RPM relationship. When the RPMs fall, the output voltage falls, but the power electronics upconverts it to float voltage.
So far, I'm pretending the voltages are the same. I haven't even started to consider your higher transmission voltage.
If the voltages are the same, the losses represented by each solution is either power losses in the field coils (series-wound) or switching losses in the power electronics (PM). With both methods, the fundamental RPM:Voltage relationship is being altered. The series-wound method uses the physical magnetic field to alter the RPM:Voltage relationship, the other uses post-processing power electronics. The power electronics are probably more flexible, able to modulate much larger voltage swings than the field coil could do.
But your proposed solution uses a higher generation voltage, which radically alters the situation. The power electronics only downconvert, the i2R losses in the generator head are reduced, and transmission losses are reduced.I agree your novel implementation of the Classic is intriguing.
Don't get me wrong here. I agree with your Classic implementation. You're using the Classic with a DC system the same way inverter generators work: decoupling the final output from the actual generator head. The winner depends on who dissipates the most power: the field coils of the series-wound, or switching losses in the power electronics. If the voltages were equal, the power electronics probably win. But with your higher voltage, it's a no-brainer. -
Re: 48VDC generator head
The only thing is - I've never seen a wound field generator of reasonable size, cost and weight that can match a PM one for flux in the air gap. So that means higher resistance in the stator winding no matter what you do with a wound field. This is evidenced by Vestas, even though they use gearing in their wind turbines, have gone to permanent magnet generators with power electronics in lieu of the old wound field.
One of the "bad" things about PM designs is that the conventional iron core, or laminated electrical steel cores, that are used in traditional wound field generators tend to have some serious reactance issues with the extreme flux from a PM rotor. Those cores become saturated very easily with the powerful flux from neo magnets.
Even the most powerful wound field generators only have less than half of the airgap flux that modern PM neo magnet rotors can provide.
--
Chris -
Re: 48VDC generator headOK, so this is about the most fun I've had all day.
I agree the MTTP is a bad idea. .....
Don't get me wrong here. I agree with your Classic implementation. You're using the Classic with a DC system the same way inverter generators work: decoupling the final output from the actual generator head. The winner depends on who dissipates the most power: the field coils of the series-wound, or switching losses in the power electronics. I bet the power electronics win.
And that's on top of your higher transmission voltage, which will have lower transmission losses.
This will be FUN thread to watch, guys!
(BTW, thats MPPT not MTTP) :-)
I think that a consideration here is just what you mean by MPPT. A basic MPPT system on the input of a CC or GTI will be configured to optimize (maximize) the power drawn assuming that the current versus voltage curve of the source is fixed in shape, not variable.
As such it will not do what it is intended to do when the source is also actively changing its characteristics (throttle at minimum, field strength if controllable in the generator case) in response to the load.
The solution is to change the algorithm by which the MPPT process works, making use of your secret (from the CC anyway) knowledge of the characteristics of the source. I believe that is what Chris is talking about, since apparently the Classic lets you assign weights to given voltage/current pairs instead of just trying to maximize their product. If this is a correct interpretation and the Classic lets you do that, then the exercise for the experimenter is indeed to find the right tables to load into the controller, based on knowledge of the power source.
The I/V curve of a PV array has a constant shape but varies in scale on one axis with varying insolation. The insolation is (over the short term) a constant and both unpredictable and uncontrollable.
The I/V curve of a wind turbine with varying wind speed is also constant, but with a possible time lag to stabilize at the new RPM. (I love the turbine vendor who measured rated power output for a given wind speed by throwing a sudden load onto a spinning turbine and if pressed commented that the peak load could not be sustained very long because the turbine would slow down!!) How does an MPPT (or power curve to be more general) device deal with that?
The wind speed is not constant in the short term and is also not controllable.
The I/V curve of a generator will vary with both shaft speed (very short term constant), field strength (very rapidly controlled) and with throttle setting (more of a lag). The end result is that for a particular fixed load resistance the output will be fixed and the fuel use will be constant. But any changes made by the intelligent load which has been set to simply sweep and maximize I x V will interact in a very complex (and probably unfortunate) way with the generator controls.
Like I said, I look forward to learning a lot from this thread and getting entertained to boot.
Thank you both. :-)
PS: Please state your acronyms which are outside the general realm of RE at least once for our benefit. (BSFC maps, for example) :-)SMA SB 3000, old BP panels. -
Re: 48VDC generator head(BSFC maps, for example) :-)
Brake Specific Fuel Consumption (in the old days when I got my mech engineering degree - lbs/hp/hr - these days the metrics are used). It's used on the dyno to predict and map engine fuel consumption vs power output. It is basically a function of the torque rise curve and thermal and volumetric efficiency of the design.
--
Chris
Categories
- All Categories
- 229 Forum & Website
- 137 Solar Forum News and Announcements
- 1.4K Solar News, Reviews, & Product Announcements
- 199 Solar Information links & sources, event announcements
- 898 Solar Product Reviews & Opinions
- 256 Solar Skeptics, Hype, & Scams Corner
- 22.5K Solar Electric Power, Wind Power & Balance of System
- 3.5K General Solar Power Topics
- 6.7K Solar Beginners Corner
- 1K PV Installers Forum - NEC, Wiring, Installation
- 2.1K Advanced Solar Electric Technical Forum
- 5.6K Off Grid Solar & Battery Systems
- 428 Caravan, Recreational Vehicle, and Marine Power Systems
- 1.1K Grid Tie and Grid Interactive Systems
- 654 Solar Water Pumping
- 816 Wind Power Generation
- 624 Energy Use & Conservation
- 620 Discussion Forums/Café
- 313 In the Weeds--Member's Choice
- 75 Construction
- 124 New Battery Technologies
- 108 Old Battery Tech Discussions
- 3.8K Solar News - Automatic Feed
- 3.8K Solar Energy News RSS Feed