Proper PV Extension Wire for MC4 Connectors?
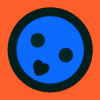
sepsolman411
Registered Users Posts: 16 ✭
I have (2) 120 watt solar panels that come with 3 foot 4mm MC4 connector cables and these cables are rated at double-insulated 12 gauge wire at 25 amps throughput. I want to connect the solar panels first in series to see what the output effect will be on a 30 amp MPPT Charge Controller connected to a single 35 amp-hour SLA/AGM 12 volt Battery. The 30 amp MPPT charge controller can regulate 12, 24, and 40 volt inputs. It can also accept up to 6mm wires (10 gauge). Both solar panels have maximum outputs of 8 amps and 22 volts each. I also want to then connect them in parallel to test the power output on the same 30 amp MPPT charge controller and 12 volt battery. The question is can I use 6mm PV Extension Cable (10 gauge) Wire to connect from the panels (12 gauge) to the 30 amp MPPT charge controller and then connect THHN 10 gauge wire from the charge controller to the 12 volt battery as well as use the same type THHN 10 gauge wire to connect to a 500/1000 pure sine wave inverter? The total distance from the solar panels to charge controller, battery, and inverter would be approximately 10 feet. I expect some voltage drop and that is why I am asking whether 10 gauge MC4 connector/pv wire can be connected to 12 MC4 connector/pv wire as well as using regular 10 gauge THHN single-insulated wires from the charge controller to the battery and loads (i.e., inverter). As we know 10 gauge wire has approximately 30 amp protection and 12 gauge wire has approximately 25 amp protection. By the way, the pure sine wave inverter is protected by a 40-amp fuse. In other words, should I basically keep all series and parallel wiring test scenarios above at 12 gauge solar PV cable (4mm)?
Comments
-
Re: Proper PV Extension Wire for MC4 Connectors?
go ahead and do it as distances that small will not usually present a problem. your comparisons may be skewed because of the different wire lengths and gauges from one to the other, but it will work in either configuration, series or parallel, fairly well. -
Re: Proper PV Extension Wire for MC4 Connectors?go ahead and do it as distances that small will not usually present a problem. your comparisons may be skewed because of the different wire lengths and gauges from one to the other, but it will work in either configuration, series or parallel, fairly well.
Using the voltage drop calculator, I could see a three-quarters to one volt drop just be adding 10 more feet and 2 more panels in parallel, I assume that the best scenario is to always keep the higher of the two gauges while not superseding the amperage rating of either gauge wire. However, this parallel configuration already puts me at 32 amps and that is clearly over the 25 amp rating of the 4mm MC4 connector (12 gauge) cables and my 30 amp MPPT charge controller. At this point, the configuration lends itself to a series connection so as not to go over these amperage ratings. The question above is more regarding expansion of the array and asking whether 12 gauge wire (PV and THHN) should be the exclusive and universal application. Your comments and recommendations are appreciated. Thanks -
Re: Proper PV Extension Wire for MC4 Connectors?
ok i was somewhat misunderstanding you as i thought you just wanted to compare 2 pvs series and parallel. i may still be misunderstanding you, but maybe i'll hit on the answer you're looking for. when adding more pvs in parallel the current is additive and so are the resistive losses unless one had individual #12 wires from each pv going back toward the cc where they would be combined there. adding 2 more pvs will not work for the mppt cc as you are exceeding the output limit of the cc with 4 of the pvs.
as for using #10 to extend the distances between the pvs and cc this would depend on the total distance of that and the cc to battery distance and what the voltage drops you experience there are. placing the pvs in series helps tremendously in overcoming v drop losses. the critical places for v drop losses are between the cc and batteries and the batteries to the inverter. between cc and batteries should be below 1% so the v drops don't mess with the proper charging of the batteries. going less than 1/2% is even more preferred. the v drop from the batteries to the inverter become a major factor because inverters usually draw high current. high currents and small wiring do not mix. use the v drop calculator to find what it is, but i would never recommend #10 for use to most inverters nowadays. the only possible time #10 may work is with a 300w or less inverter and going a very short distance. i do not gauge things on the nec max utility ac current ratings on wires as that is only a good place to start when dealing with v drop losses. the difference between 120v and 12v for the same current is a 10x difference on the percentage. that is a 1 volt drop at 120vac is 1/120=.0083%, but 12/1=.083%. that shows from under 1% to over 8% and is a huge difference for the same v drop.
as to comparing the outputs from the cc it is theoretically the same if the v drops from the wires are the same percentage-wise for both series and parallel. this can be confusing to you, but for the same wire used for the same distances, the higher voltage series connection will yield a bit more power for the cc to output. -
Re: Proper PV Extension Wire for MC4 Connectors?ok i was somewhat misunderstanding you as i thought you just wanted to compare 2 pvs series and parallel. i may still be misunderstanding you, but maybe i'll hit on the answer you're looking for. when adding more pvs in parallel the current is additive and so are the resistive losses unless one had individual #12 wires from each pv going back toward the cc where they would be combined there. adding 2 more pvs will not work for the mppt cc as you are exceeding the output limit of the cc with 4 of the pvs.
as for using #10 to extend the distances between the pvs and cc this would depend on the total distance of that and the cc to battery distance and what the voltage drops you experience there are. placing the pvs in series helps tremendously in overcoming v drop losses. the critical places for v drop losses are between the cc and batteries and the batteries to the inverter. between cc and batteries should be below 1% so the v drops don't mess with the proper charging of the batteries. going less than 1/2% is even more preferred. the v drop from the batteries to the inverter become a major factor because inverters usually draw high current. high currents and small wiring do not mix. use the v drop calculator to find what it is, but i would never recommend #10 for use to most inverters nowadays. the only possible time #10 may work is with a 300w or less inverter and going a very short distance. i do not gauge things on the nec max utility ac current ratings on wires as that is only a good place to start when dealing with v drop losses. the difference between 120v and 12v for the same current is a 10x difference on the percentage. that is a 1 volt drop at 120vac is 1/120=.0083%, but 12/1=.083%. that shows from under 1% to over 8% and is a huge difference for the same v drop.
as to comparing the outputs from the cc it is theoretically the same if the v drops from the wires are the same percentage-wise for both series and parallel. this can be confusing to you, but for the same wire used for the same distances, the higher voltage series connection will yield a bit more power for the cc to output.
I think I have the answer that I am looking for here: In either testing of (2) 120 watt PV's (series or parallel), it seems like the best PV gauge wire to connect to the 4mm (12 gauge) MC4 connectors is 10 gauge (6mm) seeing that voltage drop at 10 feet is very minimal. When expanding the array with an additional 2 pv panels (total of 32 amps) and 10 feet, it still seems valid to be using 10 gauge (6mm) pv wire with an upgrade of an MPPT charge controller from 30 amps to 40, 50, or even 60 amps. I would still use 10 gauge THHN wire from the MPPT charge controller to the battery seeing as the distance would be about 6 feet and that is the maximum guage available at the terminals. I have a higher gauge wire between 4 and 8 that goes from the battery to the 500/1000 watt pure sine wave inverter. We can forego the THHN 10 gauge wire coming straight off the pos. and neg. load ports from the MPPT charge controller to this inverter because that is a unstable load input. I assume that no more than 30 amps can go directly from those pos/neg load ports on a 30 amp MPPT charge controller as DC current to powering some DC appliances, tools, devices, lights, etc. in effect cancelling out the need for a DC to AC inverter. I cant wait to re-read my PV: Design and Installation Manual again. Thanks for your patience. -
Re: Proper PV Extension Wire for MC4 Connectors?
I'm just going to add something because I think you might be confused about the wiring. Inverters do not run off charge controllers, they run off batteries. The inverter draws from the batteries as it needs to and the panels & controller replenish the batteries as they are able. The batteries are the power reserve.
PANELS --> CHARGE CONTROLLER --> BATTERIES --> INVERTER
This is the standard wiring, and allows a quite large inverter to draw from the batteries (say a 1kW continuous with current draw up to 100 Amps @ 12 VDC) with appropriate wiring (0 AWG or better) while the charge controller feeds whatever current the panels can supply through smaller wiring even if this is less than the inverter needs at the moment. A difference between the immediate needs of the loads and the production ability of the panels.
Further I will hazard a guess that with short and appropriate array to battery wiring you will not notice much performance difference between two 120 Watt panels in parallel and two in series as there would not be much line loss to overcome either way. If the distance between array and controller were great then the series panel arrangement would have a definite advantage.
Curiously, if you were to try this same experiment with panels in parallel and PWM vs. MPPT controller you would see a small advantage to the MPPT at best, due to the difference in "ideal" Vmp of the array for the two controller types under varying light conditions. As the array size increases, so does the advantage of the MPPT (all other factors being equal, which they never are). -
Re: Proper PV Extension Wire for MC4 Connectors?Cariboocoot wrote: »I'm just going to add something because I think you might be confused about the wiring. Inverters do not run off charge controllers, they run off batteries. The inverter draws from the batteries as it needs to and the panels & controller replenish the batteries as they are able. The batteries are the power reserve.
PANELS --> CHARGE CONTROLLER --> BATTERIES --> INVERTER
This is the standard wiring, and allows a quite large inverter to draw from the batteries (say a 1kW continuous with current draw up to 100 Amps @ 12 VDC) with appropriate wiring (0 AWG or better) while the charge controller feeds whatever current the panels can supply through smaller wiring even if this is less than the inverter needs at the moment. A difference between the immediate needs of the loads and the production ability of the panels.
Further I will hazard a guess that with short and appropriate array to battery wiring you will not notice much performance difference between two 120 Watt panels in parallel and two in series as there would not be much line loss to overcome either way. If the distance between array and controller were great then the series panel arrangement would have a definite advantage.
Curiously, if you were to try this same experiment with panels in parallel and PWM vs. MPPT controller you would see a small advantage to the MPPT at best, due to the difference in "ideal" Vmp of the array for the two controller types under varying light conditions. As the array size increases, so does the advantage of the MPPT (all other factors being equal, which they never are).
You bring up very interesting points regarding the PWM and MPPT differences between series and parallel configurations because in a typical winter, the solar gain coefficient is higher than in the summer and that makes sense as the hotter the panels, the less efficient the output. These new panels although rated at 120 watts were outputting open circuit 8 amps and 21.5 volts for about 140 watts, if the math were done it would be over 160 watts. Regardless of the season, I am sure that the panel's efficiency will decline ever so slowly over the next 25 years. All these factors taken into consideration and the array wiring up to approximately 10-25 feet, I am settling on 10 gauge PV wire connecting these 2 panels as well as adding 2 more in series in the future, then 2 more and so on up to a total of 10 or 12 (1.2 Kw/1.4 Kw total), foregoing the parallel circuit scheme altogether, utilizing between a 30 and 60 amp pwm charge controller because of the wire diameter access terminals, increasing the battery size from 12 to 24 volt using (4) 6 volt 210 amp-hour SLA/AGM batteries, increasing inverter size to modified sine wave at 5000/10000 watts to get partially or completely off-grid or even grid-tied in. Thanks for the informative dialogue. -
Re: Proper PV Extension Wire for MC4 Connectors?
I have to pick nits again. You do not have any current in an open circuit because there is no circuit for current to flow through. That the Voltage open circuit would read 22.5 is in-line with what should be expected from a "12 Volt" panel. That the short-circuit current (measured with an Ammeter only between the + and - leads) would be around 8 Amps is also in-line with what would be expected. But this does not mean the panel puts out 22.5 Volts @ 8 Amps. Trying to measure the Voltage at maximum power and current at maximum power is extremely difficult to do "at home". For a 120 Watt panel we would expect the peaks here to be Vmp 17.7 and Imp 6.8 or so.
Aside from the "cold weather advantage" found with MPPT controllers, there is a small amount of gain to be had under normal conditions. This is due to the MPPT's ability to "pick" an Vmp other than what the panel might settle at under the load conditions. For example, a panel Vmp might be 17.5 (typical) but the "ideal" Voltage point when charging the battery might call for the panel Voltage to be 16.75 or such; ever-so-slightly different than the panel's output. The MPPT can make this adjustment and turn the "extra" 0.75 Volts into more charge current instead of waste heat. As I mention, the larger the array is the greater the gain from this. On top of that you have the ability of higher Voltage/lower current to overcome line loss and the potential increase from even higher cold panel Voltages.
Since you are clearly planning on expanding your system in the future I urge you to plan ahead carefully. For instance you mention using MSW inverter and then possibly going grid-tie - these two are not compatible goals. Off-grid is always more expensive than using the utility power and/or going grid-tie, and a non-battery-based GT inverter does not require a charge controller but can require quite different wiring than an off-grid system. Regrettably solar electric power systems are not mix-and-match compatible.
Categories
- All Categories
- 229 Forum & Website
- 137 Solar Forum News and Announcements
- 1.4K Solar News, Reviews, & Product Announcements
- 199 Solar Information links & sources, event announcements
- 898 Solar Product Reviews & Opinions
- 256 Solar Skeptics, Hype, & Scams Corner
- 22.5K Solar Electric Power, Wind Power & Balance of System
- 3.5K General Solar Power Topics
- 6.7K Solar Beginners Corner
- 1K PV Installers Forum - NEC, Wiring, Installation
- 2.1K Advanced Solar Electric Technical Forum
- 5.6K Off Grid Solar & Battery Systems
- 428 Caravan, Recreational Vehicle, and Marine Power Systems
- 1.1K Grid Tie and Grid Interactive Systems
- 654 Solar Water Pumping
- 816 Wind Power Generation
- 624 Energy Use & Conservation
- 619 Discussion Forums/Café
- 312 In the Weeds--Member's Choice
- 75 Construction
- 124 New Battery Technologies
- 108 Old Battery Tech Discussions
- 3.8K Solar News - Automatic Feed
- 3.8K Solar Energy News RSS Feed