Battery dual cable.
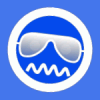
robert5208
Registered Users, Users Awaiting Email Confirmation Posts: 2 ✭
I got a simple question. Can you use thhn 8awg wire for batteries and 4000 watt 12v inverter. And what is the reason for dual 8awg wires going into on terminal. The inverter I bought came with this type of cable's.
Comments
-
Welcome to the forum Robert.
There can be several reasons for 2x 8AWG cables... One is that two 8AWG cables are more flexible than one 5 or 4 AWG cable. Second, if you need 2x 8AWG cables, then that is equavalent to 1x ~5AWG cable--And "odd cable" AWG sizes are rare in the USA. The next standard with be 4 AWG and would have "more copper" than "needed" (roughly, the cross sectional wire area "doubles" for every 3 AWG increase in wire AWG).
NEC does allow parallel cable connections--But only for larger AWG cables (as I recall???). The rest of the typical requirements (same cable lengths, same termination, same insulation, same cable tray/conduit/etc.):
https://www.electricallicenserenewal.com/Electrical-Continuing-Education-Courses/NEC-Content.php?sectionID=297.0
Going with the basics calculations... If you run the inverter at 4,000 Watts (max rated continuous load), then the max continuous current would be (assuming 10.5 volts inverter cutoff voltage):- 4,000 Watts * 1/0.85 AC inverter eff * 1/10.5 volts DC cutoff = 448 Amps max continous
https://usawire-cable.com/wp-content/uploads/nec-ampacities.pdf
THHN 8 AWG is rated at 90C for 55 Amps (each) inside of conduit... So 2x would be 110 Amps--Way less than 448 amps max continuous...
Now, there are other specifications... For example ABYA ISOMarine ratings are:
https://www.boatus.com/expert-advice/expert-advice-archive/2020/february/choose-the-correct-wire-size
Between 39 and 60 Amperes each cable (depending on location temperatures/usage, insulation ratings, etc.)...
Each chart has fudge factors (open air, conduit, cable bundle sizes, etc.)... As you can see, the 8 AWG cables pairs would need to be rated for 224 Amps each to carry the full rated load for the AC inverter... And none of the copper wiring/codes above really support that high of current flow... What to do is up to you--Following the manual and accepting that you probably will only be using (typically) 25-50% of AC inverter output/loading, you can "hand wave" that you will not pull 448 amps in "normal operation".
Don't forget the question voltage drop... Typically we assume a "near dead" 12 volt battery working Voltage is ~11.5 volts and that the inverter cutoff voltage is 10.5 volts--Giving you 1.0 volt "useful" wiring drop.
Usually that means I suggest using 0.5 VDC (for 12 volt wiring) voltage drop... And that allows for 2x current flow for surge current (starting a saw or other larger motor--Most AC inverters are rated at 2x Rated Wattage for a few seconds of starting load--I.E., ~1.0 volt worst case design drop for heavy starting current on a well discharged battery).
And that voltage drop is dependent on wire length... I.e., how long is the 12 VDC harness from battery bus to AC inverter... A typical calculator (using 2x 8 AWG parallel), 448 Amperes, 12 volt bus, 3 feet length)
https://www.calculator.net/voltage-drop-calculator.html
You can see that 448 amps on 3 feet of 2x 8AWG cable is already nearly 1.05 VDC.... Note that this wire drop calculator assumes "one way run" length entered... But assumes real life 2x for round trip length.
Also--Do not forget that a Fuse or Circuit Breaker is required to protect the wiring against short circuit in wiring or AC inverter/loads. Of course, you could assume that the 4,000 Watt inverter will only power a maximum of 2,000 Watt AC loads for your needs--And the harness current/over current protection would be 1/2 too.
This gets back to defining your loads and then designing the battery/wiring/etc. system to support those loads... And why, for example, I suggest that for loads that are 1,200-1,800 Watts can work with a 12 volt bus--But larger loads (2,400 to 3,600 Watts for 24 volt bus, and over that use a 48 VDC bus).
Low voltage DC (such as 12 VDC buses), just need a huge amount of copper to send "significant amounts of current" any appreciable distances... A 4,000 Watt AC inverter @ 12 VDC battery bus is both limiting and expensive if you really want to send 4,000 Watts from the battery bank to the AC inverter "reliably" over any distance.
The starting point for any system design (such as the AC inverter) is to start with the user manual... But it is not unusual to read some pretty "optimistic" design recommendation for this large Wattage 12 VDC inverters when you start adding "engineering fudge factors" such as low battery state of charge, longer cable runs, environmental temperatures, and such... A design that works when the system is charging (I.e., battery bus running at 14.0 VDC or higher, the inverter runs "reliably". But with low battery state of charge at 11.5 volts, the inverter no longer outputs "rated" wattage but may shut down instead because of voltage drop, etc.
Lots of stuff here... Please feel free to ask questions, make any correction in my guesses.
-Bill
Near San Francisco California: 3.5kWatt Grid Tied Solar power system+small backup genset -
Alright thank you. That was a lot of info.
Categories
- All Categories
- 229 Forum & Website
- 137 Solar Forum News and Announcements
- 1.4K Solar News, Reviews, & Product Announcements
- 199 Solar Information links & sources, event announcements
- 898 Solar Product Reviews & Opinions
- 256 Solar Skeptics, Hype, & Scams Corner
- 22.5K Solar Electric Power, Wind Power & Balance of System
- 3.5K General Solar Power Topics
- 6.7K Solar Beginners Corner
- 1K PV Installers Forum - NEC, Wiring, Installation
- 2.1K Advanced Solar Electric Technical Forum
- 5.6K Off Grid Solar & Battery Systems
- 428 Caravan, Recreational Vehicle, and Marine Power Systems
- 1.1K Grid Tie and Grid Interactive Systems
- 654 Solar Water Pumping
- 816 Wind Power Generation
- 624 Energy Use & Conservation
- 619 Discussion Forums/Café
- 312 In the Weeds--Member's Choice
- 75 Construction
- 124 New Battery Technologies
- 108 Old Battery Tech Discussions
- 3.8K Solar News - Automatic Feed
- 3.8K Solar Energy News RSS Feed