[Part 6] Comprehensive insights into solid-state battery development
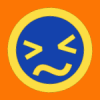
3D printing
Using ceramic materials to create electrolytes also opens up avenues for producing solid-state batteries using additive manufacturing (AM). UniMelt is a microwave-controlled plasma production system for high-volume production of solid-state batteries, using temperatures up to 6000K to generate materials in just 2 seconds instead of the 2-3 days required by traditional manufacturing methods. This technology replaces costly and wasteful traditional manufacturing methods with lower costs and a smaller footprint. UniMelt technology can be used to create materials with tight particle size distributions (PSD) for maximum energy density and engineered porosity of electrolytes, and can also be used for interface modification and passivating surface coatings. The technology can be used to create cathodes and anodes, including various NMC variants, NCA, LMO, high-voltage spinel, LTO, silicon anodes, and other unique chemistries. UniMelt technology has been used to develop products such as NMC cathodes, LFPs, silicon-dominated cathodes, lithium, solid ceramic electrolytes and regenerated cathode materials. One such material is lithium lanthanum zirconium oxide, which is currently being studied for use in solid-state electrolytes. Plasma methods offer significant advantages. For example, converting a traditional 16 GWh battery cathode production plant to the UniMelt platform can reduce CO2 emissions by 70% per year, reduce water use by 90% from 6.3 million barrels per year, and completely cut wastewater production by 7 million barrels per year, while requiring The factory is half the size of the existing facility. In addition, 3D printers have been developed to print different material layers for solid-state batteries. This could cut the amount of material used in half, double the energy density of batteries, and allow batteries to be produced near where cars are made rather than in distant gigafactories. However, this requires the development of new solid-state battery materials and AM process equipment. The process combines powder bed and jet material deposition using materials including ceramic electrolytes and metal electrodes, as well as a proprietary support material called PoraLyte. It avoids the constraints of suspended parts in different layers, enabling faster fabrication of devices with internal channels and cavities, and even adding active components such as sensors inside the battery.
Using the powder process also makes it easier to recycle ceramics and metals through traditional methods. This production technology can produce two generations of solid-state batteries. The first generation of solid-state batteries, similar to today's pouch batteries, used materials from existing factories to achieve a battery capacity of 600 Wh/L in 400 charge cycles. This is due to the use of 30 layers of materials in the battery, which increases the battery capacity from 2.3 mAh to 3 amps. By comparison, the solid-state SCiB cells in production have a capacity of 5 Ah, while the cells now starting to ship have a capacity of 20 Ah. The first-generation batteries were initially used in two- and three-seat electric vehicles. A pilot plant with an annual output of 2.5 MWh will be commissioned by the end of this year. The second-generation battery is manufactured using AM technology. It has an energy density of 1200 Wh/L, a life cycle of several thousand cycles, and a depth of discharge of 100%, rather than having to maintain 80% to 20% of charge like current batteries. This will increase the battery pack's endurance by 40%. The second-generation battery requires a professional 3D printer and some other auxiliary equipment, but its biggest advantage is that the required capital equipment and processing steps are reduced by 30-40% compared with existing processes. One AM machine can produce the equivalent of 180,000 1860 cells per month, so 30 to 40 machines is equivalent to a factory producing 1 GWh of cells per year. The use of 3D printing technology can also produce solid-state batteries in different shapes to become part of the car structure. This battery does not require a mechanical casing and can be sealed on the outside with a 50-micron electrolyte layer, giving the battery a much higher proportion of active material than other methods, again increasing battery capacity. A third-generation battery is currently under development with a high-voltage cathode voltage of 9 V instead of 4.2 V. The product will undergo sample testing at the end of 2023 and be put into production in 2024.
Categories
- All Categories
- 228 Forum & Website
- 136 Solar Forum News and Announcements
- 1.4K Solar News, Reviews, & Product Announcements
- 199 Solar Information links & sources, event announcements
- 898 Solar Product Reviews & Opinions
- 256 Solar Skeptics, Hype, & Scams Corner
- 22.5K Solar Electric Power, Wind Power & Balance of System
- 3.5K General Solar Power Topics
- 6.7K Solar Beginners Corner
- 1K PV Installers Forum - NEC, Wiring, Installation
- 2.1K Advanced Solar Electric Technical Forum
- 5.6K Off Grid Solar & Battery Systems
- 428 Caravan, Recreational Vehicle, and Marine Power Systems
- 1.1K Grid Tie and Grid Interactive Systems
- 654 Solar Water Pumping
- 816 Wind Power Generation
- 624 Energy Use & Conservation
- 619 Discussion Forums/Café
- 312 In the Weeds--Member's Choice
- 75 Construction
- 124 New Battery Technologies
- 108 Old Battery Tech Discussions
- 3.8K Solar News - Automatic Feed
- 3.8K Solar Energy News RSS Feed