input voltage drop
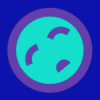
Is it possible some have degraded to this point?
The other string next to it shows an average of 65 Volts at the CC.
Both strings are series/parallel, both sets of panels are new/used and each feed 40A MPPT controllers to one set of 4 370AH Deka fld. batts.
I know I'll need to measure open circuit voltage on each panel and did so when set up, marked each one with a sharpie and the ink has disappeared! If I recall all were in the 33-37Voc. range.
Appreciate any advice!
4- 450 Watt panels with 4 Rolls 235 AH 6 volt batts./ 2-Renogy Tracer 40 Amp controllers/ Xantrex 1800W PSW Inverter.
Comments
-
If you have series/parallel strings of panels... You have a couple of quick test options:
- If you have a circuit breaker combiner box, you can turn off one string and then the other... Record the string current and voltage. Frequently, things fail one at a time, and the "weak string" can be identified and you can then do further testing (i.e., disconnect panels and check Voc/Isc numbers). If you have, for example, fuses/fuse holders, generally not a good idea to use the "fuses" as a functional quick disconnect as it is (quite) likely that you will have DC arcs which can ruin the holders or even set a holder on fire. Depending on how easy to get to the panels, you could try covering one string at a time with dark tarps/blankets to see if the "dark string" is carrying "its share" of voltage/current.
- Get an AC+DC Current Clamp meter. You need the DC function of the meter and can quickly check the current from each string--Again, double check operation of each string.
Examples of AC+DC current clamp DMMs (digital multi meters):
https://www.amazon.com/UNI-T-Digital-Handheld-Resistance-Capacitance/dp/B0188WD1NE (lower cost, "good enough")
https://www.amazon.com/Auto-Ranging-Resistance-Klein-Tools-CL800/dp/B019CY4FB4 (higher function, mid priced)
When doing your checks, crimp connections fail--You may see melting of plastic, or the wire may pull from crimp connections). Or you may see corrosion from water intrusion.
Look closely at panels... You may see streaks on cells/glass, water intrusion, corrosion, browning of cells, cracked cells, etc. I had failed panels due to j-box overheating (see some browning--"Coffee Stains"--on glass side of panel over j-boxes).
When testing panels--Try to do all checking quickly under "same sun, same direction wrt sun--With multiple panels, they should all be very close to each other (Vmp/Imp/Voc/Isc)--With in 10% or so of each other. Any panels that are 50% or greater deviation are probably "bad".
-BillNear San Francisco California: 3.5kWatt Grid Tied Solar power system+small backup genset -
Note: MC4 type solar connectors are not designed to make/break under load... Turn off "loads" (i.e., solar charge controller, combiner box breakers, etc.), cover panels with tarp, or similar when make/break connections (if under sun).
-BillNear San Francisco California: 3.5kWatt Grid Tied Solar power system+small backup genset -
BB, thanks. Time to break out the tarps again...
BTW, I have no idea how old or used the panels were when I bought them (from a solar biz but I think it was the owner or an employee.)..
Will report back. Thanks8- 235Watt panels, 2 strings in series/parallel, 4 Rolls, 235 AH FLA. batteries, 1800 W.Xantrex pure sine inverter, SRNE ML2440 40Amp Controller & 40 Amp Renogy controller, 24 Volt system.5 stand alone PV arrays; 12V gate opener, 24V Dankoff rain water pumping system, 12V Shurflo rain water garden pumping, 12V bathroom lighting and fan.
4- 450 Watt panels with 4 Rolls 235 AH 6 volt batts./ 2-Renogy Tracer 40 Amp controllers/ Xantrex 1800W PSW Inverter.Honda EU3000W generator for backup. -
235 watt, 60 cell panels are the earliest of the 60 cell format. Very likely 12-15 years old.
2.1 Kw Suntech 175 mono, Classic 200, Trace SW 4024 ( 15 years old but brand new out of sealed factory box Jan. 2015), Bogart Tri-metric, 460 Ah. 24 volt LiFePo4 battery bank. Plenty of Baja Sea of Cortez sunshine.
-
hillside said:littleharbor2 said:235 watt, 60 cell panels are the earliest of the 60 cell format. Very likely 12-15 years old.
So expect some reduction of wattage? They've been baking in the Caribbean sun.
If I have a dead panel should I consider replacing the whole string of 4?
If you can come up with New or newer larger panels easy enough you might just run a new array.2.1 Kw Suntech 175 mono, Classic 200, Trace SW 4024 ( 15 years old but brand new out of sealed factory box Jan. 2015), Bogart Tri-metric, 460 Ah. 24 volt LiFePo4 battery bank. Plenty of Baja Sea of Cortez sunshine.
-
It is the old question... Was a panel hit by a rock, or did it delaminate and the others are just a few years from following? Or was it "external" (failed MC4 crimp, etc.)?
When panels were $10-$30 a Watt... Saving old but otherwise OK panels was more of an economic decision.
When you can purchase panels at $0.50-$1.00 per Watt (shipping is always a big question), then it becomes an issue of how much time and energy you wish to expend working around the "old" (and the mix&match Vmp/Imp issues) vs just installing new panels and (hopefully) getting 20+ years out of the new set.
-BillNear San Francisco California: 3.5kWatt Grid Tied Solar power system+small backup genset -
The panels haven't been hit with a rock but a couple of hurricanes. And a few feet of rain...Counts for something, right?.
I'm hoping I find a failed MC4 conection. I noticed one of the panel's 10ga. wires gets warm at times during peak sun...
And, the other kitchen array needs a 40 Amp fuse and I can't find one anywhere. Store here is out as is Platt Electric. I bought a 3 pk of these for lighting and would like to know what you think. Thanks
https://www.ebay.com/itm/114056620173
8- 235Watt panels, 2 strings in series/parallel, 4 Rolls, 235 AH FLA. batteries, 1800 W.Xantrex pure sine inverter, SRNE ML2440 40Amp Controller & 40 Amp Renogy controller, 24 Volt system.5 stand alone PV arrays; 12V gate opener, 24V Dankoff rain water pumping system, 12V Shurflo rain water garden pumping, 12V bathroom lighting and fan.
4- 450 Watt panels with 4 Rolls 235 AH 6 volt batts./ 2-Renogy Tracer 40 Amp controllers/ Xantrex 1800W PSW Inverter.Honda EU3000W generator for backup. -
Oh boy... What to say.
- Don't know mfg and ratings (Starpoint? No details I could find)... Typically this type of fuse is rated for "automotive" use and 32 VDC max voltage
- Fuses really don't do much for lightning which took a trip of mile(s) to reach your system. Another 1/2 inch is not doing much.
- Where are the fuses installed... Typically for series strings of panels, need one series protection fuse (typically around 10-20 amps depending on panel specs). If used for controller to battery bus connection, that is less than 32 VDC, they could work as wiring protection fuses.
- When designing for lightning--Grounding design is critical. And a good quality surge suppressor helps too (i.e., clamp voltage to ground vs just "opening a switch/fuse/breaker".
https://www.solar-electric.com/search/?q=midnite+surge+mnspd
Scroll down for Documents/Video buttons for detailed information:
https://midnitesolar.com/productPhoto.php?product_ID=283&productCat_ID=23&sortOrder=1&act=p
-BillNear San Francisco California: 3.5kWatt Grid Tied Solar power system+small backup genset -
Those fuses are for lighting, not lightning. We get plenty of lightning strikes around here but so far no damage except for a coffee maker and tower fan. Not too bad for 14 yrs. here.
But back to my voltage drop.
I could buy the clamp on multi meter but amazon will take 2-3 weeks to get here. Or I could drive around for a couple hours searching locally but if I could check the panels with my regular multi meter it would save serious time.
But, in a 4 panel string that is series/parallel (no j-box) how to go about checking each panel seperately? Tarp all 4, disconnect all wires and uncover one panel at a time?
Thanks8- 235Watt panels, 2 strings in series/parallel, 4 Rolls, 235 AH FLA. batteries, 1800 W.Xantrex pure sine inverter, SRNE ML2440 40Amp Controller & 40 Amp Renogy controller, 24 Volt system.5 stand alone PV arrays; 12V gate opener, 24V Dankoff rain water pumping system, 12V Shurflo rain water garden pumping, 12V bathroom lighting and fan.
4- 450 Watt panels with 4 Rolls 235 AH 6 volt batts./ 2-Renogy Tracer 40 Amp controllers/ Xantrex 1800W PSW Inverter.Honda EU3000W generator for backup. -
That is a problem... You have to "break" each panel out to measure its Voc/Isc numbers.
As a start, I would, in the middle of the day, with a discharged battery bank (or put, for example, and electric heater as a load on the system to ensure lots of current/power draw from the array)... Cover one panel at a time and see what the charge controller array voltage/current is.
Since all the panels are similar, then covering each panel separatly and logging the results--My guess is that a weak panel (or string) you will find (at least) one panel that "behaves" differently than the rest (most likely, that one covered panel does not drop the array power as much as any of the other panels).
You have "identical" panels, and are looking for any that do not behave the same as the rest.
Regarding the 40 amp fuses... I suggest that you "oversize" the wiring and fuses/breakers by 1.25x ... For example, in North America, fuses (breakers) are designed to no trip at 80% or less of rated current, and trip at 100%+ of rated current (may take hours, or never for 101%--They are not that accurate).
For example, if these were for the 40 Amp MPPT charge controllers, I would suggest the fusing (and wiring) be rated for:
40 amps * 1.25 NEC derating = 50 amps "branch circuit"
The idea is to avoid trips for otherwise normal operation (i.e., MPPT controller outputting rated current for several hours into a discharged battery bank).
-BillNear San Francisco California: 3.5kWatt Grid Tied Solar power system+small backup genset -
Some panels have not been lasting as long as expected due to rear backsheet failures from UV/Temperature/etc. issues:
https://www.nist.gov/news-events/news/2020/03/nist-study-uncovers-potential-driver-premature-solar-panel-failureshttps://www.dupont.com/solar-photovoltaic-materials/mast_linked_content/WHAT-TO-KNOW-ABOUT-PV-PANEL-FAILURES.htmlThe premature cracking has largely been attributed to the widespread use of certain plastics, such as polyamide, but the reason for their rapid degradation has been unclear. By closely examining cracked polyamide-based backsheets, researchers at the National Institute of Standards and Technology (NIST) and colleagues have uncovered how interactions between these plastics, environmental factors and solar panel architecture may be speeding up the degradation process. These findings could aid researchers in the development of improved durability tests and longer-lived solar panels.
Cracks in backsheets often show up first near certain features — such as the grid-shaped space in between the blue or black electricity-producing solar cells — and can eventually propagate through the entire thickness of a sheet. These defects make way for oxygen and moisture to infiltrate and damage the interior where the cells lie and also allow electrical current to escape, increasing risks of electrocution.
If left outside for long enough, any plastic-based backsheet will start to fall apart, but not all backsheets are created equal. Some plastics deteriorate much more rapidly than others.
“In the 2010 to 2012 timeframe, many modules were deployed containing polyamide-based backsheets, which presented dramatic cracking failure in as little as four years despite meeting standard requirements,” said Xiaohong Gu, NIST materials engineer and co-author of the study.
-BillPV panel failures are not uncommon, with most of these defective modules using non field-proven materials. Even more, defects are seen among systems in use less than five years.
As early as 2010, DuPont tests revealed significant weaknesses in PET, polyamide, and PVDF-based backsheet materials, which are currently used in a large volume of solar panels in the field. Single-stress and sequential stress tests were conducted, revealing PV panel failures such as yellowing/embrittlement and cracking, caused by exposure to UV, extreme temperatures and humidity over time.
A Global, Growing Concern
What was once thought to be isolated cases of failures is proving to be a more prevalent occurrence around the world, with many of those failures found in backsheets.
Globally, PV panel failures are growing.
- PA backsheets in the US, Europe, Asia, and Australia have shown cracking after just 3-5 years.
- Canada, the US, and China have experienced PVDF backsheet cracking and delamination in just 4 years.
- PET backsheets in the US, Spain, India, and China have shown yellowing / embrittlement, and delamination in just 4 years.
All of these cases have experienced backsheet failures at extremely young ages – an alarming statistic given the importance of performance and durability over the long haul.
Near San Francisco California: 3.5kWatt Grid Tied Solar power system+small backup genset -
Investing in a Midnite Solar combiner box with breakers is great for times like these. I went for years without one but now I'm so sorry I did. In my case I ran the string conductors all the way down to the combiner near the controller. It has helped me understand the limitations of my system in my heavily and oddly shaded installation. It would definitely help you here if it were at all possible to do so.
-
It is always best to test with a load, another item that you may not have on hand. I found a really cheap load are the long floodlight lamps which are 300-500W at 120V. These can be found as cheap as a pack of two for 99 cents. Newer halogen types have replaced these as many countries have outlawed the other. The stainless steel end contacts easily take solder and just put a wire on them. These are not a fixed resistance as the resistance can change X15 from hot to cold. It will give you a comparison between panels. At 12V they will start to glow. put some heat shrink on the ends and it makes a handy tester you can bring with you when buying panels.
-
Thanks Bill, I'l look for 50 amp. fuses and for the right time of mid day for checking the panels. Lots of cloud cover these days so, day by day! (this didn't post)
Edit, 2 days later.
Too much cloud cover lately and being busy have kept me from checking each panel.
But I'm wondering about my poor record keeping...
I wrote 90-92 volts at the charge controller from the one string back when I set it up.
The other string (next to it) I wrote 65V. I didn't date these numbers so they are several years old, approx. 5 +/-
Open circuit voltage I wrote under each panel and was mid 30's, maybe 33-37 avg.
However, since then I've repeatedly gotten the exact same voltage readings from both strings. Always within a few volts of each other but always peaking at 65-67V.
The panels sit next to each other, each go into their own 40A CC, both in series/parallel and both charge the 4 Deka batts.
Was that 92V reading an anomaly, something I read at equalization or what?
Because if one or two panels in the string I posted about have gone bad, then the other string of 4 has the same problem.
I don't know how to calculate what these two strings should produce at the controllers but each string is 4 235W panels and the distance to the CC is 15-16 ft.
Good info, Bill. I'll be reading about that. thanks
8- 235Watt panels, 2 strings in series/parallel, 4 Rolls, 235 AH FLA. batteries, 1800 W.Xantrex pure sine inverter, SRNE ML2440 40Amp Controller & 40 Amp Renogy controller, 24 Volt system.5 stand alone PV arrays; 12V gate opener, 24V Dankoff rain water pumping system, 12V Shurflo rain water garden pumping, 12V bathroom lighting and fan.
4- 450 Watt panels with 4 Rolls 235 AH 6 volt batts./ 2-Renogy Tracer 40 Amp controllers/ Xantrex 1800W PSW Inverter.Honda EU3000W generator for backup. -
Can you read the Vmp/Voc/Imp/Isc numbers on the panels? Or get the model number and look them up?
There is something inconsistant about your readings...
If the panels are Vmp~30 volts... And you have 4 panels in series--That should be around 4*30=120Volts...
65 volts per string / 4 series panels = 16 volts or so per panel
That could mean that each panel is Vmp~18 volts (standard test conditions), or possibly you do not have 4 series * 2 parallel strings, but 2 series * 4 parallel strings (as an example).
An "issue" with off grid solar power systems is that the charge controller and the battery bank + loads "decide" how much current/power the system will draw from the solar array. So while your array may be capable of outputting (typical max is 8 * 235 Watts * 0.77 solar derating factors = ) 1,448 Watts on a cool clear day--A relatively charged battery bank with no much in the way of loads could draw much less power (1% float charge current * 370 AH battery bank * 27.2 volts float charge on battery bank = ) 101 Watts float charging or (101 Watts / 27.2 volts charging = ) 3.7 Amps into your battery bank--A perfectly working system (which does not tell you much about the 'health" of the solar array.
Your 65 Volt array reading--An MPPT controller will search (or track) for the optimum Vmp of the array (solve the Pmp=Vmp*Imp equation)... For example
65 Volt Vmp-array / 2 panels in series = 32.5 Volts Vmp-array (actual) -- Which is pretty close to a normal value for many panels.
-Bill
Near San Francisco California: 3.5kWatt Grid Tied Solar power system+small backup genset -
These panels are wired series/parallel. I got numbers from 3 of 4 (one string) and the 4th has the label gone/faded.
And each string has MPPT CC's (altho lower end), one is Renogy the other SRNE 40A. The Renogy is the one we're discussing although like I said, both strings show near duplicate voltage at peak sun.
!) Boviet - Vmp 30.7 & Voc 38.0 (260W)
2 & 3) Hanwha, Vmp 30.1 & Voc 36.8 on both (235W)
4) Likely a Sonali or Trina, #'s are gone (235W likely)8- 235Watt panels, 2 strings in series/parallel, 4 Rolls, 235 AH FLA. batteries, 1800 W.Xantrex pure sine inverter, SRNE ML2440 40Amp Controller & 40 Amp Renogy controller, 24 Volt system.5 stand alone PV arrays; 12V gate opener, 24V Dankoff rain water pumping system, 12V Shurflo rain water garden pumping, 12V bathroom lighting and fan.
4- 450 Watt panels with 4 Rolls 235 AH 6 volt batts./ 2-Renogy Tracer 40 Amp controllers/ Xantrex 1800W PSW Inverter.Honda EU3000W generator for backup. -
These 2 strings are only at about 10-15 degree angles and some hold rain at the corners. They don't seem to leak as I watch the water evaporate (in a day or so) but there could be water intrusion. I estimate at least 400" inches of rain in the last 6 years.8- 235Watt panels, 2 strings in series/parallel, 4 Rolls, 235 AH FLA. batteries, 1800 W.Xantrex pure sine inverter, SRNE ML2440 40Amp Controller & 40 Amp Renogy controller, 24 Volt system.5 stand alone PV arrays; 12V gate opener, 24V Dankoff rain water pumping system, 12V Shurflo rain water garden pumping, 12V bathroom lighting and fan.
4- 450 Watt panels with 4 Rolls 235 AH 6 volt batts./ 2-Renogy Tracer 40 Amp controllers/ Xantrex 1800W PSW Inverter.Honda EU3000W generator for backup. -
If a pro was involved, (hourly cost) you would be well beyond the cost of replacing the array.
Just past the equinox now, if you depend on this power source, it is best now before winter. Module defects usually get worse and are absolutely not fun to troubleshoot."we go where power lines don't" Sierra Nevada mountain area
htps://offgridsolar1.com/
E-mail offgridsolar@sti.net -
Have you measured the Voc-array (voltage open circuit of each string/full array)?
You have a 24 volt battery bank (?) and seeing ~60+ volts at the array/MPPT controller input... So it appears the MPPT controller is functional and the "measured by MPPT" is simply way below what would be expected--Roughly:- 4 panels in series * 30.7 volts Vmp * 0.81 (Vmp temperature derating on hot/sunny day) = 99.5 volts nominal minimum expected array Vmp voltage.
- 235 Watt panel / 30.7 volts Vmp = 7.65 Imp approximate per panel/per string max current (what are you seeing)?
If your max current is 1/2 or less of Imp, that would also suggest problems with panels or wiring.
You may not only wish to replace the array, but do something about your single (?) 40 amp MPPT controller... The "optimum" max array for your controller would be around:- 40 amps * 29 volts battery charging * 1/0.77 panel+controller deratings = 1,506 Watt array "optimum" suggested maximum
- 1,506 Watts array / 235 watt panels = 6.4 panels @ 235 Watts
- 235 Watt array * 8 panels = 1,880 Watt rated array
A good quality MPPT controller should be able to manage the over-sized array just fine--No damage to controller or array would be expected (assuming good cooling airflow to charge controller).
-Bill
Near San Francisco California: 3.5kWatt Grid Tied Solar power system+small backup genset -
Each string of 4 panels has it's own controller. I mentioned that up a ways. Yesterday we had good sun and the 4 batts. reached Float stage by about 3PM.
First thing I'll do is a specific gravity check on the batts later today.
Voltage at the CC's is in the 62-65V range.
"Have you measured the Voc-array (voltage open circuit of each string/full array)?" (Bill)
Sorry for my ignorance, but is the reading at the CC's (panel icon) the correct way or is there another?8- 235Watt panels, 2 strings in series/parallel, 4 Rolls, 235 AH FLA. batteries, 1800 W.Xantrex pure sine inverter, SRNE ML2440 40Amp Controller & 40 Amp Renogy controller, 24 Volt system.5 stand alone PV arrays; 12V gate opener, 24V Dankoff rain water pumping system, 12V Shurflo rain water garden pumping, 12V bathroom lighting and fan.
4- 450 Watt panels with 4 Rolls 235 AH 6 volt batts./ 2-Renogy Tracer 40 Amp controllers/ Xantrex 1800W PSW Inverter.Honda EU3000W generator for backup. -
I was suggesting with the charge controller is disconnected from the array, to read the Voc-array (with an off grid system, there is no way to "guarantee" that the MPPT controller is not drawing some current from the array)... I am wondering what the voltage of 4 panels in series with zero load is (just using a separate volt meter which draws very little current)... Do the array strings get anywhere near 120+ Volts?
I don't understand how the array produces 62 volts or so with 4 panels in series unless you have one or two "dead" panels (or shorted bypass diodes in the J-Box).
I am a bit confused about the configuration... Do you have a 4s x 2p array connected to one charge controller, or have 4s x 1p array connected to one controller and 4s x 1p array string connected to a second 40 amp MPPT controller?
You don't have the 4s x 2p array connected to the Vpanel input of both controllers inputs--Correct?
-Bill
Near San Francisco California: 3.5kWatt Grid Tied Solar power system+small backup genset -
hillside said:Those fuses are for lighting, not lightning. We get plenty of lightning strikes around here but so far no damage except for a coffee maker and tower fan. Not too bad for 14 yrs. here.
But back to my voltage drop.
I could buy the clamp on multi meter but amazon will take 2-3 weeks to get here. Or I could drive around for a couple hours searching locally but if I could check the panels with my regular multi meter it would save serious time.
But, in a 4 panel string that is series/parallel (no j-box) how to go about checking each panel seperately? Tarp all 4, disconnect all wires and uncover one panel at a time?
Thanks2.1 Kw Suntech 175 mono, Classic 200, Trace SW 4024 ( 15 years old but brand new out of sealed factory box Jan. 2015), Bogart Tri-metric, 460 Ah. 24 volt LiFePo4 battery bank. Plenty of Baja Sea of Cortez sunshine.
-
That's is my confusion, i read 8 panels in 2 strings with 4 panels in series connected to a single controller.You have 4 panels in 2s x 2p connected to a single controller. And s second controller with another array 2s x 2p.Let me reread the thread before i say more.-BillNear San Francisco California: 3.5kWatt Grid Tied Solar power system+small backup genset
-
A few years back I think it was Photowit that suggested the series/parallel configuration and I think he posted a diagram of it. I've looked for it but no luck. on
I'll look some more and find something., (edit.): Image in forum posts of 2019 w/ diagram of series/parallel is not available.)
No junction boxes. Each is it's own separate set-up. 4 panels into it's own CC, and the other 4 into it's own CC, both go into the 4 batts.
And the readings I get from each controller, are in the ranges I mentioned, 55-62Volts so double that is going to the 4 batts. Panels and CC sit side by side
And IIRC, someone here also said with a nominal system like this no J box is necessary.
8- 235Watt panels, 2 strings in series/parallel, 4 Rolls, 235 AH FLA. batteries, 1800 W.Xantrex pure sine inverter, SRNE ML2440 40Amp Controller & 40 Amp Renogy controller, 24 Volt system.5 stand alone PV arrays; 12V gate opener, 24V Dankoff rain water pumping system, 12V Shurflo rain water garden pumping, 12V bathroom lighting and fan.
4- 450 Watt panels with 4 Rolls 235 AH 6 volt batts./ 2-Renogy Tracer 40 Amp controllers/ Xantrex 1800W PSW Inverter.Honda EU3000W generator for backup. -
If each controller has 2 series * 2 parallel--Then no "Combiner Box" (from panels to charge controller with fuses/breakers per strong) is needed.
The J-Box I was typing about was in regards to the boxes on the rear of the solar panels. Sometimes there is a cover that you can unscrew... Many of the newer panels are simply sealed boxes (no service access) with the two +/- pigtails coming out of the box.
So seeing 62 some odd volts on the array when the sun is up and the MPPT controller is running is perfectly OK operation (at least from the 2x2 array voltage side).
Do you have a range of current that you have seen from the array? With Imp~7.65 volts--A well working 2x2 array should be, at best, have a maximum output current of 7.65 to (2x) 15.3 Amps (depending on sunlight conditions, battery state of charge, loading). As an example for the math:- 7.65 Amps (1/2 the max array current) * 62 volts = 474 Watts (not clear day, battery bank mostly charged, not too much DC loads)
- 474 Watts * 0.95 (typical MPPT controller eff) * 1/28 volts battery charging = 16.1 amps (nominal, OK functioning) out of charge controller
After several years of trouble free use my downstairs system is showing a marked drop in input voltage from the panels. And it may have happened further back than I realized. Early on one string of 4 235W panels would show up to 90 volts at the controller--now it shows in the low-mid 60's, to 67V. Panels are mixed, purchased new and used (very limited supplies here on the island at the time)The 90 Volts at the controller does not make a lot of sense for a 2s x 2p array... The 60-67 volt range would be in the normal range (all things considered).
Is it possible some have degraded to this point?
The other string next to it shows an average of 65 Volts at the CC.
Both strings are series/parallel, both sets of panels are new/used and each feed 40A MPPT controllers to one set of 4 370AH Deka fld. batts.
I know I'll need to measure open circuit voltage on each panel and did so when set up, marked each one with a sharpie and the ink has disappeared! If I recall all were in the 33-37Voc. range.
Appreciate any advice!
What we need to know is the Wattage (and or Volts * Amperes) from each array and the battery state of charge (battery bank below 80% SoC will draw much of the power the array can provide). A full battery bank and not much DC bus loading, the controller will draw only the power from the array to hold the battery bank at charging voltage (~29.0 VDC) or float charging (~27.6 volts or so).
With solar power systems, and especially off grid systems, it is "difficult" to figure out how well the array is working... You could have solar panel issues, wiring issues, or simply a "full battery bank and zero loads"...
As a first guess--Look at the array current... If you are seeing between 50% and 100% of array rated Imp current (7.65 to 15.3 amps)--Everything is usually find (with Vmp-array voltage in your 6X volt range).
If you want to do some quick and dirty tests... Log the controller vmp-array and Imp-array. Then quickly cover one panel in a 2 x 2 string. Log the Vmp-array and Imp-array... If all is working OK, then your Imp-array should drop by about 1/2 (i.e., one parallel string is shaded, and not producing power). Then repeat by covering another panel on the other string and Log. Again, Vmp-array should be roughly the same, and Imp-array should be roughly 1/2 again.
You can repeat for the second controller too... Ideally, both controllers should be reading the same input and output voltages/currents.... HOWEVER, charge controllers have a "memory" and slightly different calibrations--So it is possible that one controller will "supply more current" than the other in some conditions (one controller is in float while the other is still in bulk charging). Or you could be near 29.0 volt set point, and one controller is reading "29.2 volts" and cutting back on the current, etc....
At this point, I don't see anything wrong with your systems... But it will take the tarp testing, and logging Vmp-array and Imp-array values (with a discharged battery bank and/or high DC Bus current loading) to see if your system is performing at "peak" efficiency.
In general, solar panels don't all fail at once in the same way at the same time. The idea here is to test each one (drop one from system at a time) and see how much the output (current/power) falls. Ideally, they should all fall within the same amount (on the same array) withing 10% or so (i.e., 7 amps vs 7.7 amps).
-BillNear San Francisco California: 3.5kWatt Grid Tied Solar power system+small backup genset -
Thanks, Bill. I'm going to see if I can get a knowledgeable guy to help with that testing.
Here is the wiring set-up
8- 235Watt panels, 2 strings in series/parallel, 4 Rolls, 235 AH FLA. batteries, 1800 W.Xantrex pure sine inverter, SRNE ML2440 40Amp Controller & 40 Amp Renogy controller, 24 Volt system.5 stand alone PV arrays; 12V gate opener, 24V Dankoff rain water pumping system, 12V Shurflo rain water garden pumping, 12V bathroom lighting and fan.
4- 450 Watt panels with 4 Rolls 235 AH 6 volt batts./ 2-Renogy Tracer 40 Amp controllers/ Xantrex 1800W PSW Inverter.Honda EU3000W generator for backup. -
2S/2P there you go, that explains the 60.xx voltage you are seeing.
2.1 Kw Suntech 175 mono, Classic 200, Trace SW 4024 ( 15 years old but brand new out of sealed factory box Jan. 2015), Bogart Tri-metric, 460 Ah. 24 volt LiFePo4 battery bank. Plenty of Baja Sea of Cortez sunshine.
-
Bill, Harbor, thanks so much.
Will still do the tests but appreciate your help.8- 235Watt panels, 2 strings in series/parallel, 4 Rolls, 235 AH FLA. batteries, 1800 W.Xantrex pure sine inverter, SRNE ML2440 40Amp Controller & 40 Amp Renogy controller, 24 Volt system.5 stand alone PV arrays; 12V gate opener, 24V Dankoff rain water pumping system, 12V Shurflo rain water garden pumping, 12V bathroom lighting and fan.
4- 450 Watt panels with 4 Rolls 235 AH 6 volt batts./ 2-Renogy Tracer 40 Amp controllers/ Xantrex 1800W PSW Inverter.Honda EU3000W generator for backup.
Categories
- All Categories
- 228 Forum & Website
- 136 Solar Forum News and Announcements
- 1.4K Solar News, Reviews, & Product Announcements
- 199 Solar Information links & sources, event announcements
- 898 Solar Product Reviews & Opinions
- 256 Solar Skeptics, Hype, & Scams Corner
- 22.5K Solar Electric Power, Wind Power & Balance of System
- 3.5K General Solar Power Topics
- 6.7K Solar Beginners Corner
- 1K PV Installers Forum - NEC, Wiring, Installation
- 2.1K Advanced Solar Electric Technical Forum
- 5.6K Off Grid Solar & Battery Systems
- 428 Caravan, Recreational Vehicle, and Marine Power Systems
- 1.1K Grid Tie and Grid Interactive Systems
- 654 Solar Water Pumping
- 816 Wind Power Generation
- 624 Energy Use & Conservation
- 619 Discussion Forums/Café
- 312 In the Weeds--Member's Choice
- 75 Construction
- 124 New Battery Technologies
- 108 Old Battery Tech Discussions
- 3.8K Solar News - Automatic Feed
- 3.8K Solar Energy News RSS Feed