maths
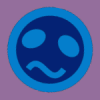
sailingjohn
Registered Users Posts: 1 ✭
I am struggling with the maths (this is an age thing) I need 1.5amps for 6 hours. A 72AH lead acid battery is said to give 30% which is about 21.5 Ah Is this correct?
1.5 amps x 6 hours is 9AH Is this correct?
If the controller gives the battery 13.5 volts and the solar panel is 200 watts (watts divided by volts ) = 14.8 amps this would suggest I need a 20amp controller. Is this correct?
would appreciate help
1.5 amps x 6 hours is 9AH Is this correct?
If the controller gives the battery 13.5 volts and the solar panel is 200 watts (watts divided by volts ) = 14.8 amps this would suggest I need a 20amp controller. Is this correct?
would appreciate help
Comments
-
Welcome to the forum SailingJohn,
You have the basic math correct... I like to write out the equations sort of like an English sentence and show the steps... For example:- AH = Amps * Hours
- AH = 1.5 Amps * 6 hours = 9 AH
- Sizing battery for 30% discharge:
- AH of load / Depth of discharge = 9 AH / 0.30 DoD = 30 AH minimum battery capacity
- AH of Battery Capacity * percentage used = AH of planned capacity
- AH of capacity used = 72 AH battery * 0.30 planned usage = 21.6 AH of battery planned usage
And the MPPT type (maximum power point tracking) which is a more complex controller and can do some very interesting things with Current and Voltage. Depending on how you like analogies...
The PWM controller is like a one speed bicycle. If you are going the right speed on level ground the bicycle is very cheap and does what you want,.
The MPPT controller is like a 10 speed bike. You can change "grears" to meet your needs at that moment. Use one gear to peddle up hill. And use another to peddle on straight and level road.
Math wise:- PWM Amps out = Solar Array Amps available.
- MPPT Amps out:
- Volts * Amps (current) = Power
- PWM Power In = Power Out.
- Volts array * Amps Out = Vbatt voltage * Ibatt charging current (ignoring controller efficiency and such)
PWM:- Power = Voltage * Current
- Amps = Power / Voltage
- 125 Watt array / 18 Volts = 6.94 Amps Imp
- Max battery charging current will be 6.94 Amps
- Max battery charging power with varying voltage:
- Power = Voltage * Current = 12 volt charging * 6.94 Amps charging current = 83 Watts into battery (discharged battery)
- Power = 14.75 volts charging * 6.94 Amps = 102 Watts charging
MPPT:
Note that Vmp (voltage maximum power) falls at solar panel temperature rises. The "name plate" panel wattage is as "room temperature". But as you know, anything left in full sun can get very hot (put your hand on the hood of a black car in full sun, and burn yourself). So, more or less, Vmp is less on a hot day in full sun because the solar panels get hot. More or less, the typical "best case" for solar array power is around 77% of Name Plate Wattage.
For an MPPT controller under the same conditions as the PWM system above:- Power of solar array * panel+controller derating = 125 Watts * 0.77 derating = 96.25 Watt typical best case array Wattage in "real life"
- P=V*I
- I=P/I
- Ibatt current = Parray / Vbatt voltage
- Ibatt charging current = 96.25 Watts from array / 12.0 volts Vbatt charging = 8.0 Amps charging a discharged battery
- Ibatt = 96.25 Watts Array / 14.75 Vbatt charging = 6.5 Amps charging a near full battery
So, you have a 200 Watt panel/array. Because of the design of PWM charge controllers, you need to "oversize" the PWM controller to avoid too much current in controller under certain conditions (reflections from snow, water, sand, certain cloud conditions). The typical derating is 85%...
PWM:- 200 Watt array / 18 Volts Vmp = 11.11 Amps from array
- 11.11 amps from array (best case typical) / 0.85 percent derating = 13.07 Amps minimum PWM controller derating
MPPT controllers can control the maximum rated output current to their name plate rating--Safely and efficiently. So the minimum MPPT controller output rating would be:- P = V*I; I=P/V
- Pcontroller output = 200 Watts * 0.77 typical array+controller deratings = 154 Watts typical "best case" peak charging power
- Icontroller output = 154 Amps / 14.75 volts charging = 10.44 Amps minimum MPPT controller suggested
Yes, in cold weather (typically sub freezing), you can get more power from your array (close to 100% or better) with an MPPT controller... But you do not really "over size" your controller as Winter Sun is already pretty weak (weather, less hours of sun per day, slant sun through atmosphere, etc.).
Another issue to watch with MPPT controllers is that the Vmp of an array needs to be higher than the battery voltage by larger amount for the MPPT circuits to operate optimally... Typically 1.3x greater than battery charging voltage.- Vbatt charging * MPPT voltage factor = 14.75 volts * 1.3 MPPT Factor = 19.75 volts Vmp-array minimum for optimal MPPT performance.
A major advantage is you can mount the solar panels/array farther away (longer wire runs) and use smaller diameter (and cheaper) copper cables to carry the power back to your MPPT controller/battery shed. Typical Vmp-array with MPPT can be from 30-100+ VDC or even as high as 600 VDC for larger/more expensive charge controllers.
For PWM controllers, you have to "match" the Vamp-array to the battery bank voltage for optimum operate. A PWM controller cannot "down convert" a high voltage/low current array to a low voltage/high current battery.
So for a PWM controller you could be looking for a 200 Watt panel/array with Vmp~18 volts.
And for a MPPT controller you would be looking for a >20 Vmp volt solar panel (typically 30-36 volts) or use 2x 100 Watt 18 Vmp panels in series for a 200 Watt 36 Vmp array.
Simple question--Not so simple answers.
-BillNear San Francisco California: 3.5kWatt Grid Tied Solar power system+small backup genset
Categories
- All Categories
- 228 Forum & Website
- 136 Solar Forum News and Announcements
- 1.4K Solar News, Reviews, & Product Announcements
- 199 Solar Information links & sources, event announcements
- 898 Solar Product Reviews & Opinions
- 256 Solar Skeptics, Hype, & Scams Corner
- 22.5K Solar Electric Power, Wind Power & Balance of System
- 3.5K General Solar Power Topics
- 6.7K Solar Beginners Corner
- 1K PV Installers Forum - NEC, Wiring, Installation
- 2.1K Advanced Solar Electric Technical Forum
- 5.6K Off Grid Solar & Battery Systems
- 428 Caravan, Recreational Vehicle, and Marine Power Systems
- 1.1K Grid Tie and Grid Interactive Systems
- 654 Solar Water Pumping
- 816 Wind Power Generation
- 624 Energy Use & Conservation
- 619 Discussion Forums/Café
- 312 In the Weeds--Member's Choice
- 75 Construction
- 124 New Battery Technologies
- 108 Old Battery Tech Discussions
- 3.8K Solar News - Automatic Feed
- 3.8K Solar Energy News RSS Feed