12volt verses 24 volt
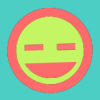
Comments
-
The rule of thumb I suggest is:
- 1,200 to 1,800 Watts maximum for 12 VDC systems
- 2,400 to 3,600 Watts maximum for 24 VDC systems
- Over 2,400 to 3,600 Watts for 48 VDC systems
- Current = Power / Voltage
- "12 volt" current = 1,800 Watts * 1/0.85 inverter eff * 1/10.5 low voltage cutoff = 202 Amps
- "12 volt" current = 3,600 Watts * 1/0.85 inverter eff * 1/10.5 low voltage cutoff = 403 Amps
- "12 volt" current = 4,800 Watts * 1/0.85 inverter eff * 1/10.5 low voltage cutoff = 538 Amps
https://lugsdirect.com/WireCurrentAmpacitiesNEC-Table-301-16.htm
4/0 Copper is good for approximately 230 amps (using NEC)... Diameter of cable (excluding insulation):AWG # Diameter
(inch)Diameter
(mm)Area
(kcmil)Area
(mm2)0000 (4/0) 0.4600 11.6840 211.6000 107.2193
Another reason for higher voltage, is that can send higher voltage and power longer distances on much smaller diameter cables... For example, how far can you send 1,200 Watts on 4/0 AWG cable with a maximum of 0.5 volt (suggested) drop:- 1,200 Watts / 11.5 volts = 104 amps
- 0.5 volt drop, 4/0 cable, 11.5 volts 104 amps
Result for 40 feet of 4/0 copper cable @ 12 volts
Voltage drop: 0.5
Voltage drop percentage: 4.48%
Voltage at the end: 10.99What diameter of cable is needed for 48 volt system:
- 1,200 Watts / 46 volts at load = 26 Amps
- max drop 2 volts, pick 40 feet (same as 12 volt example)
Result using 3 AWG cable (yes, 3 AWG is not commonly available in USA)
Voltage drop: 2.08
Voltage drop percentage: 18.08%
Voltage at the end: 9.423 AWG cable is not even a 1/4" thick.
Another suggested rule of thumb... More or less, there are fewer (and more expensive) solar charge controllers that have >80 Amp charging output... If you want at least 10% rate of charge for solar (10% is my minimum suggested charging current for an off grid Lead Acid battery bank)... That means that for a single charge controller, you would look at a jump of battery bank voltage if looking at >800 AH (i.e., 800 AH @ 12 volts => 400 AH @ 24 volts => 200 AH @ 48 volts battery bank).
Also, your typical MPPT (Maximum Power Point Tracking) charge controller will charge "any" standard battery bank voltage... 12/24/48 volts... However, look at the "supported solar array" (typical "max cost effective"):
- 80 Amps * 0.77 panel+controller deratings * 14.5 volts battery charging = 893 Watt array "max cost effective" @ 12 volt bank
- 80 Amps * 0.77 panel+controller deratings * 29.0 volts battery charging = 1,786 Watt array @ 24 volt bank
- 80 Amps * 0.77 panel+controller deratings * 58.0 volts battery charging = 3,573 Watt array @ 48 volt bank
- 400 AH @ 12 volts per 1,000 Watt AC inverter (400 AH @ 12 volt bank will support a maximum of 1,000 Watt inverter)
- 200 AH @ 24 volts per 1,000 Watt AC inverter
- 100 AH @ 48 volts per 1,000 Watt AC inverter
One reason to "avoid" going with High(er) voltage battery banks... Fewer cells to check water on (6 cells for a single 12 volt string, 12 cells for a 24 volt bank, and 24 cells to check on a 48 volt battery bank).
And using larger AH batteries (i.e., 2x 200 AH @ 6 volt series batteries (6 caps) vs 2x 12 volt @ 100 AH parallel batteries with 12 caps), vs a bunch of smaller AH batteries in lots of parallel strings.
There are always "configuration issues" to understand too... There are two types of solar charge controllers.. PWM (Pulse Width Modulated)--Cheap and require you to "match" Vmp/Imp to your battery bank voltage. Usually only "make sense" for small solar power systems.
And there are the MPPT type controllers. More expensive, but they can take High voltage/Low current from the array and efficiently down convert to low voltage/high(er) current to charge the battery bank. Usually best/optimum pick for any medium to large solar power system.
For an MPPT controller, you put the solar panels in series (and then parallel more strings of panels) and connect to the MPPT controller (think of an MPPT controller like an automatic transmission--Matches array voltage/current to battery bank voltage/current).
There are still "configuration rules"... More or less, the Vmp-array needs to be at least 2x the battery bank charging voltage.
For a 12 volt battery bank charging at 15.0 volts, that means Vmp-array needs to be at least 30 volts for an MPPT solar charge controller... You would take 2 of your standard "12 volt" solar panels (Vmp~18 volts) in series for Vmp-array ~ 36 volts...
The maximum Vmp/Voc voltage is based is based MPPT solar charge controller specifications (typical Max Input values of 100, 150, and even >400 Volts).
There are a lot of "pieces to juggle"... If this is a new system--You need to do a complete "paper" design with the brands/models of components you want to purchase.
If this is an upgrade from an older system... The panels may be able to be "rewired" from parallel to series (or series+parallel). If you have an MPPT controller, it may already support your new battery bank voltage. And of course--You need to look at your battery back capacity (larger system?) and pick the optimum battery configuration.
For folks with RVs, there may be reasons to "stick with 12 VDC"... The existing DC appliances are DC. Vehicle chassis electrical may be 12 VDC.
For systems that may expand in the future (cabins, small homes, etc.)--Your loads and power requirements typically grow over time. Starting with 24 VDC (and bypassing 12 VDC initial system) may be the way to start (or even 48 VDC for "starter system").
Also, for any "medium to large" solar power system... These days AC equipment (lights, TV, pumps, washers, etc.) are almost as efficient at 120/240 VAC as their 12/24 VDC cousins. It almost always makes sense to only plan and install AC loads/appliances. And for cabins+homes--120/240 VAC is easier to get by inspectors and probably safer/cheaper to wire vs trying to run 12 VDC appliances.
Note the above are rules of thumbs to make initial paper designs simpler (you got to start somewhere). Yes, lots of RVs are running with 3,000 Watt @ 12 VDC inverters... But unless you are space/weight/DC load dependent, it is usually better to design with a higher voltage battery ban of 24 or 48 VDC from the beginning. None of the "rules of thumbs" are written in stone. They are just guide posts. And if you will be "violating" one of the rules of thumbs--Just make sure you have good reasons to do it.
All this is done with paper designs first... It is much easier and cheaper to do lots of paper designs/iterations vs buying hardware and working yourself into a corner.
Your thoughts?
-BillNear San Francisco California: 3.5kWatt Grid Tied Solar power system+small backup genset -
BillThank you for this info. I all ways have to print these answers out so I can read them until I have a complete understanding as I am a little slow.I bought this with the idea of upgrading the system to run in my shop.Right now the system consists of the Renogy 400 watt PV kit with a Renogy 3000 watt 12V inverter and a Epever 100 amp mppt CC.I am looking at ordering 6 255 panels and wanted to go to 24V on the system if it really gives you twice the usable watt's.I also want to order 2 more 200 AH batterys to get the system to run long enough [a couple of days] in a power outage.I was thinking this would be cheaper then buying and installing a separate Generac for the shop as I have one for the house.There seems to be a steep learning curve to all this that I wasn't expecting but I guess it will give me something to do.Greg
-
Greg,
By itself, 24V or 48V does not give you more power/energy... It just lets you keep the wiring much smaller gauge (cheaper) and less issues with voltage. Drop. The old P=V*I ... 2x higher voltage and 1/2 the current for the same power "flow".
12 volt systems just become a real wiring nightmare when you get >~1,200 - 1,800+ Watt loads (i.e., 100-150+ amp loads).
In the olden days, there where no "small" AC inverters in 24 or 48 volts (sub 1,000 Watts)... Today there some good small inverters out there for even 24 and 48 volt systems.
Try a few different "paper designs" first... And see what works out best for you.
I know that this is a solar forum... But for $1,000 or less, you can get from a 3 kWatt to 9 kWatt genset that runs from gasoline or even propane (a bit more rare--especially for smaller gensets). I.e., small inverter for lighting, charging battery tools. A larger inverter to fire up when running larger tools.
Costco can have a few choices (not bothering with links--Things change):
Depends on how often and long your outages are. Propane is great for storage--If fuel storage is possible for your place...
Just store the genset empty (if using gasoline--Use preservative) and a teaspoon of oil in the spark plug hole, crank, pull to begining of compression stroke--And the genset will usually store for years just fine... (have done this with a few gensets--And no issues).
Of course, if there is a battery--You may have to float charge/charge once energy few months to keep the battery fresh (for a least a few years). Need a good quality float charger for batteries... The "cheap" trickle chargers can "boil" the battery dry in a few months.
Not a bad solution if your outages are once every few years (for a few days)....
Like solar, "matching" your genset to your load is important too... An "efficiently matched" genset will cost around $1 per kWH for fuel (running geset at 50% loading, or an inverter-generator at 25%+ load). (assuming $4 per gallon gasoline and 4kWH/Gallon rough estimates)
Runing a few LED lights on a 10 kWatt genset--That will cost you a lot just to keep the genset spinning.
I like 2-3kWatt inverter generators. They are relatively fuel efficient for smaller loads (like 1/4 to 1/8 GPH)... Vs larger gensets that can drink a 1/2+ per hour without any loads. And many of the inverter generators are pretty quiet without needing to build sound deadening enclosures around them.
I can store some gasoline and have no propane handy other than BBQ tanks (natural gas in our area)... Can use stored gasoline for car too in emergency.... Recycle fuel to car once a year and refill using gasoline preservative.
Only issue with propane is in very cold/snow bound climates, can be issues of "chilling" the propane tank so much that the pressure drops o near zero PSI (whole bunch of other questions to ask/answer for propane in cold weather).
-Bill
Near San Francisco California: 3.5kWatt Grid Tied Solar power system+small backup genset -
I was wondering what the reason was for running 24V verses 12V. Thanks for clearing that up for me.On the generator I have a 14 KW natural gas Generac for my house and really like it. I was just going to add another one for my shop but hearing the hype for solar I decided to give it a try. One reason is because of the noise of the gen set.We have lost power here up to 28 day's. In 2011 all the power poles and tree's were destroyed from a ice storm.Since then I got rid of my gas gen set because during the time with no power I was having to make a 75 mile trip to the only gas station that was working.We have an ice storm and the power is gone and we have a lot of them.I have been out 7 day's, 11 day's, 17 day's and a lot of 2 or 3 day's without power when we have the spring storm's.Just have to figure this solar stuff out, only been in it for a little over a month.Greg
Categories
- All Categories
- 229 Forum & Website
- 137 Solar Forum News and Announcements
- 1.4K Solar News, Reviews, & Product Announcements
- 199 Solar Information links & sources, event announcements
- 898 Solar Product Reviews & Opinions
- 256 Solar Skeptics, Hype, & Scams Corner
- 22.5K Solar Electric Power, Wind Power & Balance of System
- 3.5K General Solar Power Topics
- 6.7K Solar Beginners Corner
- 1K PV Installers Forum - NEC, Wiring, Installation
- 2.1K Advanced Solar Electric Technical Forum
- 5.6K Off Grid Solar & Battery Systems
- 428 Caravan, Recreational Vehicle, and Marine Power Systems
- 1.1K Grid Tie and Grid Interactive Systems
- 654 Solar Water Pumping
- 816 Wind Power Generation
- 624 Energy Use & Conservation
- 619 Discussion Forums/Café
- 312 In the Weeds--Member's Choice
- 75 Construction
- 124 New Battery Technologies
- 108 Old Battery Tech Discussions
- 3.8K Solar News - Automatic Feed
- 3.8K Solar Energy News RSS Feed