Install Different battery Types to A 400W 24V Wind Turbine System and other recomended specification
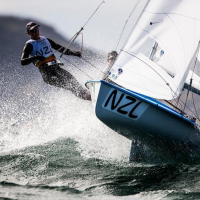
Hi to all! Just looking for a little guidance as I’m in a remote Off-grid DIY environment trying to install a Wind Turbine. No experience with a WT bought a cheap Chinese REAL 400W 24V with a manufacturer supplied small controller similar to this https://www.aliexpress.com/item/32958450500.html
I am on the beachfront with good wind.
I have 2 battery types
1 nos (New) 24V 110ah LIFEPO4 battery deep cycle solar battery. Up to 2.6kw (comes with breaker AI bms system make each cell equalizer well) https://www.trademe.co.nz/a/motors/caravans-motorhomes/parts-accessories/solar-panels-accessories/listing/3398535937
2 nos (3.5years old) 12V Sealed LEAD ACID Battery 240 ah connected in Series to make 24V
a. My question is can I connect these 2 batteries in Parallel to the Charge Controller or do I have to put some sort of isolater/switch in between the controller and each of the batteries because of their different types? Is there another option like split cables or 2 controllers or some auto switches?
b. Also what thickness of cable would be recommended for this 24V 400W turbine and is a thicker cable better or worse?
c. Please feel free to also recommend any other (Must Have) switches / meters between the turbine to past the Inverter like Knife switches etc.
Thanks in advance (its truly appreciated) and apologies for being confused looking at articles on the web 😊
Comments
-
Welcome to the forum ZedK,
Just be aware--Personally, I am not a fan of small wind turbines. It if works for you--great.
1. Suggest you place the turbine on a 10 meter tall pole/tower, or taller. You need to get the turbine into "non-turbulent" airflow. Too low, upwind obstructions (buildings, trees, etc.) create turbulent airflow--And there is very little energy in turbulent air (no matter what wind turbine mfgs. say).
2. The two starting points for wiring... First is the peak continuous current you expect. The second is the distance you want to send the power.
Charge controllers should be very close to the battery bank (for a 24 volt battery bank, you only want ~0.1 to 0.2 VDC max voltage drop--short/relatively heavy cables).
I will do the stuff in US Standards--Just because I don't have handy charts/websites for metric stuff...
How much current will a 400 Watt turbine output @ 24 volts- 400 Watts / 24 volts = 16.7 Amps
- 16.7 amps * 1.25 NEC derating for continuous current (aka battery charging) = 20.9 amps derated branch circuit
12 AWG (depending in insulation rating)--12 AWG is one of those thou shall use 20 Amp max @ 12 AWG wiring... So, technically 10 AWG (which is 30 amp max by NEC) would also be suggested.
Next is voltage drop... For "unregulated" voltage from solar panels and wind turbines, 1% to 3% is a good range to aim for as total voltage drop... Say 16.7 amps @ 30 meters or 99 Feet with 1% to 3% drop (one way wire run for this voltage drop calculator--That is total run from top of tower to base to "battery shed":
If we want to aim for ~3% max drop at 30 meter run and 16.7 amps:
https://www.calculator.net/voltage-drop-calculator.html?necmaterial=copper&necwiresize=5&necconduit=pvc&necpf=1&material=copper&wiresize=0.4066&resistance=1.2&resistanceunit=okm&voltage=29.0&phase=dc&noofconductor=1&distance=99&distanceunit=feet&eres=16.7&x=49&y=20&ctype=nec- Using 4 AWG copper wire @ 16.7 amps @ 99 feet
- Voltage drop: 1.03
- Voltage drop percentage: 3.54%
- Voltage at the end: 27.97
https://technick.net/guides/electronics/awg_to_metric/Since I know nothing about your site, the wind turbine, prevailing wind conditions, obstructions, etc... All I can give you is the above math.AWG Number Ø [Inch] Ø [mm] Ø [mm²] 6⁄0 = 000000 0.580 14.73 170.30 5⁄0 = 00000 0.517 13.12 135.10 4⁄0 = 0000 0.460 11.7 107 3⁄0 = 000 0.410 10.4 85.0 2⁄0 = 00 0.365 9.26 67.4 1⁄0 = 0 0.325 8.25 53.5 1 0.289 7.35 42.4 2 0.258 6.54 33.6 3 0.229 5.83 26.7 4 0.204 5.19 21.1 5 0.182 4.62 16.8 6 0.162 4.11 13.3 7 0.144 3.66 10.5 8 0.128 3.26 8.36 9 0.114 2.91 6.63 10 0.102 2.59 5.26 11 0.0907 2.30 4.17 12 0.0808 2.05 3.31 13 0.0720 1.83 2.62 14 0.0641 1.63 2.08
Personally (I don't trust small wind turbine mfgs in general)--If you saw more than 5 amps at any time--You are probably doing well.
Do you want to try the turbine first with "light" gauge copper wiring first??? Maybe. Depends on the cost of copper cable in your area (Auckland New Zealand?).
My first suggestion is to design and build out your system using solar panels... In general, they are much more reliable (both mechanically, and just month to month energy harvest) than wind turbines. Use your turbine in winter/poor weather conditions to "assist" when there is not much sun... To give you an idea how to figure your "hours of sun" per day by month--Here is a simple calculator that does that:
http://www.solarelectricityhandbook.com/solar-irradiance.htmlAuckland
Measured in kWh/m2/day onto a solar panel set at a 53° angle:
Average Solar Insolation figures
(For best year-round performance)
More or less, 3 hours or more per day is a "good" amount of sun... Below that, solar becomes a bit more "iffy" economically speaking.Jan Feb Mar Apr May Jun 5.80
5.54
5.10
4.27
3.47
3.14
Jul Aug Sep Oct Nov Dec 3.39
3.82
4.63
4.92
5.41
5.57
In your case, if my guess to your location is somewhat accurate--You could have pretty decient sunlight (no trees/buildings casting shadows on solar array--Any shadows can easily cut production "with any shade on any panel" by 50% or more (i.e., during winter with lots of tall trees/hills, morning/evening sun may be shaded).
Mixing batteries is usually a pretty good "no"... But practically speaking, the min/max/charging range of your Li Ion battery with BMS is not much different that that of AGM type batteries (typically 14.4 Max voltage @ 77F). AGM/Lead Acid batteries do like/require higher charging voltage for "optimum" results during cold weather (especially if bank goes sub freezing). Li Ion batteries are generally run with 0 temerature compensation for charging.
Typically Li Ion batteries "stop charging" when 100% full and reaching 28.8 VDC. AGM (lead acid) batteries 'need' 2-6 hours of "absorb charging' (held at 28.8 VDC) (2 hours for 75% light discharge--6 hours suggested for 50% SoC or greater discharge).
Is it "ideal" to share batteries. No. If you have an old set and they help you for the next few years (decent AGM batteries typically have around 5-7 years of life if not "run hot" or over discharged, badly treated, etc.)--Why not.
I have to go cook dinner right now--But this is a start.
Do you know your daily loads (AH @ 24 VDC, or WH per day, by season)--Full time off grid or sunny weekend weather? Backup generator for bad weather? Are power needs for "nice to have stuff" (lighting, laptop computer, cell phone charging) or for some 24x7 "base line loads" such as refrigerator that needs power "every day"?
-Bill
Near San Francisco California: 3.5kWatt Grid Tied Solar power system+small backup genset
Categories
- All Categories
- 228 Forum & Website
- 136 Solar Forum News and Announcements
- 1.4K Solar News, Reviews, & Product Announcements
- 199 Solar Information links & sources, event announcements
- 898 Solar Product Reviews & Opinions
- 256 Solar Skeptics, Hype, & Scams Corner
- 22.5K Solar Electric Power, Wind Power & Balance of System
- 3.5K General Solar Power Topics
- 6.7K Solar Beginners Corner
- 1K PV Installers Forum - NEC, Wiring, Installation
- 2.1K Advanced Solar Electric Technical Forum
- 5.6K Off Grid Solar & Battery Systems
- 428 Caravan, Recreational Vehicle, and Marine Power Systems
- 1.1K Grid Tie and Grid Interactive Systems
- 654 Solar Water Pumping
- 816 Wind Power Generation
- 624 Energy Use & Conservation
- 619 Discussion Forums/Café
- 312 In the Weeds--Member's Choice
- 75 Construction
- 124 New Battery Technologies
- 108 Old Battery Tech Discussions
- 3.8K Solar News - Automatic Feed
- 3.8K Solar Energy News RSS Feed