What size fuses do I need?
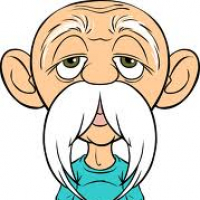
From the solar panels (Four, 100 watt 12 volt parallel) to the controller, one 30 amp.
From the controller to the batteries through a central positive terminal post, one 30 amp.
From each parallel wired battery to the common positive terminal post,100 amp on each battery. (100 AH batteries)
From the central positive terminal post to the inverter 250 amp.
Does this sound right? Too much? Too little? Any unnecessary?
Thanks
Comments
-
Assuming this is a PWM controller, and all 4 solar panels are wired in parallel, you would need to find the series fuse rating for the panels. Roughly:
- 100 Watts * 1/17.5 Volts Vmp = 5.71 Amps Imp (close guess)
- Very roughly Isc = ~1.25 x 5.71 Amps = 7.14 Amps Isc (Isc=current short circuit; guess)
- Guessing Series Fuse rating = 10 amps
- Total current from array 4x 5.71 Amps = 22.84 Amps Imp-array
The reason for the 4 fuses (typically in the positive solar panel lead) is to protect a shorted panel from being fed too much current from the other three parallel solar panels (3x7.14amps=21.42 amps short circuit)--Would blow the 10 amp fuse instead.
No 30 amp fuse needed between the combiner box and Vpanel input to the charge controller. Some folks will use a >=30 amp fuse as a handy on/off switch (or you can use a heavy 12 VDC rated switch instead).
If you have an MPPT type controller, you would have a different array configuration, and no fuses (most likely).
The fuse/breaker fromt the battery bank to the controller, I would suggest the wiring and fuse be rated at 1.25x Imp (current maximum power)... That is a NEC factor for continuous current flow derating of fuses/breakers/wiring (you will get near max Imp for a few hours per day--need NEC derating to prevent "false trips"):- 22.84 Amps Imp-array * 1.25 NEC derating = 28.55 Amps minimum = 30 amps minimum rated branch circuit fuse and wiring
A 250 Amp fuse from battery bank to AC inverter is pretty big--And would support an AC inverter size (on a 12 volt battery bus) of:- 250 Amps * 0.85 AC inverter eff * 10.5 volts cutoff = 2,205 Watt AC inverter max suggested based on fuse
Also, for a ~2,000 Watt 12 volt AC inverter, you would need around a 800 AH @ 12 volt battery bank (minimum "suggested" for a Flooded Cell Lead Acid battery bank). Any smaller battery bank, and you run the risk of collapsing the battery bus voltage by drawing so much current at full inverter load (especially as the battery bank discharges).
And this brings us back to 400 Watt of solar panels on a 12 volt battery bank--Using our rules of thumbs again, suggest around 5% minimum rate of charge (for a weekend/sunny weather system) to 10%-13%+ rate of charge for a full time off grid system.- 400 Watts of panels * 0.77 panel+controller deraring * 1/0.05 rate of charge * 1/14.5 volt charging = 425 AH @ 12 volt battery bank maximum
- 400 Watts of panels * 0.77 panel+controller deraring * 1/0.10 rate of charge * 1/14.5 volt charging = 212 AH @ 12 volt battery nominal
- 400 Watts of panels * 0.77 panel+controller deraring * 1/0.13 rate of charge * 1/14.5 volt charging = 163 AH @ 12 volts typical cost effective minimum
Your questions with the 400 Watt array, 12 volt battery bank, and 250 Amp fuse for inverter suggest an "unbalanced" system design. Too small solar array and too large AC inverter for use in a cabin/RV.
With some power needs, you can push outside the typical design rules (using Li Ion batteries, short heavy loads like power tools, etc.)...
-Bill
Near San Francisco California: 3.5kWatt Grid Tied Solar power system+small backup genset -
BB. said:If you have an MPPT type controller, you would have a different array configuration, and no fuses (most likely).
Battery wiring... Can you tell us a bit more about the battery bank design? Flooded Cell, AGM, etc., 2/4/6/12 volt battery @ XXX AH in series/parallel configuration.
And this brings us back to 400 Watt of solar panels on a 12 volt battery bank--Using our rules of thumbs again, suggest around 5% minimum rate of charge (for a weekend/sunny weather system) to 10%-13%+ rate of charge for a full time off grid system.- 400 Watts of panels * 0.77 panel+controller deraring * 1/0.10 rate of charge * 1/14.5 volt charging = 212 AH @ 12 volt battery nominal
- -Bill
Thanks for all this information. Sorry I did not provide enough details about my system. My friend has helped me set up a temporary system to get me started to see what I want and need to buy long term. Here is what I have now.
4, 12 volt, 100 watt panels in parallel, rated 5.70 amps. I was told not to do them in series in any way because I get a little bit of shade from a neighbors tree on two panels for a couple of hours every afternoon. When that happens it looks like the controller drops from sending 14 amps to the battery down to 9 amps and 17.1 volts which I assume is still charging the batteries.
Running #10 wire from panels to a box where they combine and join to a #8 wire that goes 25 feet to an MPPT 40 amp controller. I wonder if this wire is too small? The panels are rated for a total of 22.8 amps but the most the controller sends to the battery bank when 50% discharged is 14 amps. Would small wire or old weak batteries maybe cause this?
Running #10 wire from the controller, 2 feet to a temporary battery bank made up of 6, used but good, 35 amp hour AGM batteries wired in parallel for a total of 210 amp hours. I plan to use two 110 AH Mighty Max AGM batteries if possible.
Using #2 wire, equal length, from all 6 batteries to central + and -terminal posts.
Running #2 wire from the central terminal posts to a 900 watt pure sine wave inverter. Is this size inverter too big for a 220 AH battery bank? I think I need one about this size to run the freezer. What size fuse do I need with this if a 250 is too big?
This will be used to run a large TV for about 4 hours per night on a daily basis, but is really for emergency use just to power a small 5 cu ft chest freezer in an emergency. Rated 3.5 amps. The TV works fine with this temporary system but I have not tested the freezer yet.
Based on what you said would my system be more balanced if I go with 2, 110AH new AGM batteries for 220 total AH, based on your calculation of 400 Watts of panels * 0.77 panel+controller deraring * 1/0.10 rate of charge * 1/14.5 volt charging = 212 AH @ 12 volt battery nominal?
If I’m using an MPPT controller and not a PWM, do I need fuses from each panel to the combiner box or just one 40 amp from the box to the charge controller?
-
Judging from my use, with 4 100w 12v panels, to a 40a PWM Controller, to 2 Battery banks totaling 650ah, 1000w Pure Sine Wave Inverter.
400w harvest isn't enough to keep a 5.0cu/ft, 218kw/h Annual Freezer running. I have to Top Off my Bank at night with my Gen Set and 30A Charger for 2-3 hours. Even with the Top Up, I see 12.5v in the morning, after a sunny days harvest. I have never tried to go without a top up to see if it will go below that.
That said, I run 2 wires (12awg) from my panels, with 20a fuse in each, 100a Shunt between the Controller and Batteries (but thinking of adding a 50a Maxi), and the Inverter is Fused on it's own.
-
Sage,
No problem on not having "all the information"--We like to have it so we can help with the "balanced" system design rather than just answering "the one question" and leave everything else assumed.
Shading on panels pretty much kills the solar harvest. They need full sun/no shade or partial shade for good operation. Any shading (nearby chimney, vent pipe, power lines shadows, etc. can easily cut output by 1/2 or more.
Since you have an MPPT type charge controller, configuring your panels for 2x series by 2x parallel would usually be better (note: the 2x series panel pairs--Each pair should be in "same sun"... For example, if you have one set that gives you 9am to noon sun, that would be one 2x series pair, and if the others where in noon-3pm sun, that would be the other pair. You do not want to mix panel series strings with different orientation or one panel in partial shade--ideally).
The whole shade vs parallel vs series connections for arrays--Shade is just bad. Since you have an MPPT controller, you will get better harvest with 2s x 2p when all panels are in sun, and probably better harvest if one of the 2s strings is in sun while the other is in partial shade. The probably with trees--They are usually growing--And 2 years down the road, your array may be shaded most of the day--And if neighbor's trees, you have nothing you can do other than ask nicely for a trim.
If you do a 2s x 2p array--You do not need any fuses in each panel string (generally, you should have fuse per string if you have 3 or more parallel strings). And you do not need any fuse in the cable from the array to the charge controller (40 amps or whatever). You have designed the array cabling to carry more current than the array can every produce--So no fuse needed.
Also, with the higher voltage array, you don't need near as heavy copper wiring back to the charge controller.
For example, if you had 10 AWG, 2x5.7 amps (2x series strings in 2z= parallel), 30 feet, and 35 Vmp-array:
https://www.calculator.net/voltage-drop-calculator.html?material=copper&wiresize=3.277&voltage=35&phase=dc&noofconductor=1&distance=30&distanceunit=feet&eres=11.4&x=0&y=0Result
Voltage drop: 0.68
You would lose about 2% of the array output--You get very good voltage at the Vpanel input for the MPPT controller (we aim for 3% to 1% drop).
Voltage drop percentage: 1.95%
Voltage at the end: 34.32
It is very difficult to measure the system "best case" output current/power into a battery bank. If the battery bank is near full or full, the charge controller will limit the harvest current anyway. I.e., if your controller sees ~14.4 volts at the battery bank (typical set point for AGM charging in Absorb), the battery starts to limit charging current naturally. Also, the charge controller can decide that the battery is full and drop to Float mode (around 13.6 volts or so)--And the controller will hold that voltage.
Now, if you had a large DC Bus load, the controller will let more current through to try and hold 13.6 volts on the battery bus. Up to what is available from the solar array. (the Vmp-array~17.1 volts is probably what the MPPT controller decided is Vmp-array optimum operation point (for a cool/clear day).
The other thing to look at is the charge controller to battery wiring... Need to keep that short and heavy. Looking at voltage drop for 10 AWG cable with a 400 Watt array:- 400 Watts * 0.77 panel+controller derating * 1/14.4 volts charging = 21.4 Amps "best case charging current @ 14.4 V battery bus"
https://www.calculator.net/voltage-drop-calculator.html?material=copper&wiresize=3.277&voltage=14.4&phase=dc&noofconductor=1&distance=2&distanceunit=feet&eres=21.4&x=65&y=21Result
Voltage drop: 0.085
Normally suggest 0.05 to 0.10 volt drop from controller to battery bank--So that looks OK.
Voltage drop percentage: 0.59%
Voltage at the end: 14.315
You need to monitor the voltage at the battery bank terminals. You want to see the battery bank voltage rise from whatever it is resting voltage (usually below 12.8 volts) to ~14.4 volts as the sun rises, and the batteries get charged. And hold 14.4 volts for something like 2-6 hours (for "full charge"). In practice, you may not get 6 hours (as sun sets, you have loads you want to run,etc.).
To wire parallel batteries, this website does a good job of explaining how to do the wiring optimally:
http://www.smartgauge.co.uk/batt_con.html
250 Amp fuse and wiring for a 900 Watt inverter is overkill... Closer to:- 900 Watt inverter * 1/0.85 AC inverter eff * 1/10.5 volt battery cutoff = 101 Amps max draw at 900 Watts
- 101 Amps * 1.25 NEC derating = 126 Amp rated fuse/wiring suggested (if you run near 900 Amps for a period of time to prevent false trips of your fuse)
https://lugsdirect.com/WireCurrentAmpacitiesNEC-Table-301-16.htm
A 900 Watt AC inverter on a flooded cell lead acid battery bank would need around (400 AH per 1,000 Watt AC inverter rating on a 12 volt bank) ~ 360 Amp minimum (at 12 volts).
The reality is that AGM batteries do have higher surge current support--So you could probably get away with ~200 AH AGM Battery bank (with heavy enough wiring to keep voltage drop down). Say 101 amps @ 12 volts @ 3 feet @ 2 AWG wiring, the voltage drop would be:
https://www.calculator.net/voltage-drop-calculator.html?material=copper&wiresize=0.5127&voltage=12&phase=dc&noofconductor=1&distance=3&distanceunit=feet&eres=101&x=69&y=23Result
Voltage drop: 0.095
Suggest a maximum voltage drop of 0.5 volts (12 volt battery bank) for load wiring... A short length of 2 AWG is very good here.
Voltage drop percentage: 0.79%
Voltage at the end: 11.905
For the AGM batteries, I would prefer that you get 2x 6 Volt @ 220 AH vs the 12 volt @ 110 AH. Same energy storage (2x voltage vs 2x AH capacity P=V*I) for a couple reasons (easier to monitor each battery voltage/health, a bit less issue with parallel wiring). But if the 12 volt batteries are easier to get/cheaper--It is not a huge issue.
The other issue to look is your loads... If you can get a Kill-a-Watt type power meter:
https://www.amazon.com/s?k=kill-a-watt+meter&ref=nb_sb_noss_2
This will allow you to measure your AC loads and figure out how much energy/time you have available for use from your solar system.
Gone through this before:
http://www.solarelectricityhandbook.com/solar-irradiance.htmlChesterfield MO
Measured in kWh/m2/day onto a solar panel set at a 51° angle:
Average Solar Insolation figures
(For best year-round performance)
The freezer may take 1,000 WH per day (guess), and a "large TV"--Can run from 35 to 200 Watts--Need a power meter to measure.Jan Feb Mar Apr May Jun 3.29
3.73
4.46
4.94
5.03
5.27
Jul Aug Sep Oct Nov Dec 5.46
5.35
5.30
4.63
3.38
3.03
Your AGM battery bank (220 AH @ 12 volts) would supply for your TV (assuming 2 days of storage and 50% maximum discharge) around (guessing 100 Watt TV):- 220 AH * 12 volts * 0.85 AC inverter eff * 1/2 days storage * 0.50 max planned discharge = 561 WH per day (no sun, 2x days)
- 561 WH per day / 100 Watt TV load = 5.61 hours per day
Based on hours of sun. Using 3.73 hours of sun (February break even):- 400 Watts * 0.61 AGM off grid AC system eff * 3.73 Hours of sun per day = 1,268 Hours of sun (average Feb day harvest)
I will stop here... Post is getting way long. Questions?
-Bill
Near San Francisco California: 3.5kWatt Grid Tied Solar power system+small backup genset -
BB. said:Sage,
Shading on panels pretty much kills the solar harvest. They need full sun/no shade or partial shade for good operation. Any shading (nearby chimney, vent pipe, power lines shadows, etc. can easily cut output by 1/2 or more.
-BillBill I'm beginning to think I'm screwed with solar. Shade is my enemy! But I'll ask these questions anyway since you offered to answer them and maybe I can do a compromise setup.
Unfortunately, I can’t do a series/parallel solar panel array. I watched every 10 minutes as the sun moved and it always seem to just slightly shade 1 and sometimes 2 of the panels on and off, different panels at different times, for about 2 hours right at Noon to 2 PM. I can get great sun with my panels facing south east from sunrise to noon with good amperage to my controller, but after that power production is more or less cut in half. By 4 PM I’m in all shade. If I face them due South production is lower in the morning but I get a bit more in the Afternoon up to 5 PM. There is no way I can see to do a series array connection. So, with only a parallel array do I need any fuses between the panels and the charge controller?
For my battery bank I will be using method 3 with a central terminal post for + and -. That seems like the best way to do a parallel set up. The 12-volt batteries are simply a better buy for me right now. Maybe next time around I’ll switch to 6 volts.
Even though the 250-amp fuse is overkill from the battery bank to the inverter can I still use it since I already have it or does code require I match more closely to my actual amperage?
My deep freeze runs at 1.5 amps and draws 5 amps at compressor start up, which if I’m calculating correctly means it runs at 180 watts and 600 watts at startup. I’m getting a Kill A Watt meter tomorrow to confirm these numbers. Will the 900-watt inverter handle this with a 220-amp AGM battery bank with 18” of #2 AWG from the battery banks to the inverter? I calculate my voltage drop percentage is only 0.53%.
I’m not sure what you meant when you said … “If your freezer uses 1,000 WH per day, that would be around 1/2 day of freezer runtime (per day), or 1 day of stored energy for freezer (no sun).” The freezer doesn’t run continuously but did you mean ½ day being equal to running continuously for 12 hours? What does 1 day of stored energy (no sun) mean?
So be straight with me Bill. With the shading issue and my application needs is solar a lost cause for me? Could I just use the solar for the TV and be better off using a generator with a lot of gas stored up for a long term power failure to run the deep freezer, or just forget about solar all together and stick with a generator for emergency use?
What would you do in my shoes?
Thanks for all the great links. I find them very helpful. My wife says you are an exceptional human being for helping less knowledgeable people like me with all your knowledge and years of experience so we don’t screw up as badly as we would without you, and all for free. She thanks you most sincerely as do I.
Categories
- All Categories
- 228 Forum & Website
- 136 Solar Forum News and Announcements
- 1.4K Solar News, Reviews, & Product Announcements
- 199 Solar Information links & sources, event announcements
- 898 Solar Product Reviews & Opinions
- 256 Solar Skeptics, Hype, & Scams Corner
- 22.5K Solar Electric Power, Wind Power & Balance of System
- 3.5K General Solar Power Topics
- 6.7K Solar Beginners Corner
- 1K PV Installers Forum - NEC, Wiring, Installation
- 2.1K Advanced Solar Electric Technical Forum
- 5.6K Off Grid Solar & Battery Systems
- 428 Caravan, Recreational Vehicle, and Marine Power Systems
- 1.1K Grid Tie and Grid Interactive Systems
- 654 Solar Water Pumping
- 816 Wind Power Generation
- 624 Energy Use & Conservation
- 619 Discussion Forums/Café
- 312 In the Weeds--Member's Choice
- 75 Construction
- 124 New Battery Technologies
- 108 Old Battery Tech Discussions
- 3.8K Solar News - Automatic Feed
- 3.8K Solar Energy News RSS Feed