How to select a MPPT Charge controller
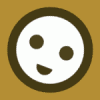
Iftikhar Hussain
Registered Users Posts: 6 ✭
Dear friends,
I am new in solar business not does not know enough to design a solar home system or any other, i am facing problem to select MPPT charge controller , inverter and batter bank, for example:
125 watt celing fan x 8 hrs run = 1000 wh/day
added system loss factor 1000 x 30%= 1300 wh/day
Sun shine hours : 1300 / 4 sunshine hours= 325 wh/day
Now how to select inverter size ?
how to select battery bank for 2 days backup
how to design mppt charge controller?
what will be equation / formula ?
I am new in solar business not does not know enough to design a solar home system or any other, i am facing problem to select MPPT charge controller , inverter and batter bank, for example:
125 watt celing fan x 8 hrs run = 1000 wh/day
added system loss factor 1000 x 30%= 1300 wh/day
Sun shine hours : 1300 / 4 sunshine hours= 325 wh/day
Now how to select inverter size ?
how to select battery bank for 2 days backup
how to design mppt charge controller?
what will be equation / formula ?
Comments
-
Re: How to select a MPPT Charge controllerIftikhar Hussain wrote: »i am facing problem to select MPPT charge controller , inverter and batter bank, for example:
125 watt celing fan x 8 hrs run = 1000 wh/day
added system loss factor 1000 x 30%= 1300 wh/day
Sun shine hours : 1300 / 4 sunshine hours= 325 wh/day
Now how to select inverter size ?
how to select battery bank for 2 days backup
how to design mppt charge controller?
Welcome to the forum,
This doesn't make sense: "Sun shine hours : 1300 / 4 sunshine hours= 325 wh/day"
I think you are calculating that you need a 325 watt solar array to provide 1300 watthours of energy every day.
You should first choose your battery bank, and then figure out what you need to charge a bank of that size. In the event of cloudy weather you should discharge your bank about 25% per day. After two days of poor charging your battery will be 50% depleted... what will you do then? At that point the batteries need to be recharged without delay. Do you have grid or generator?
Assuming you are OK with this, we need to make some assumptions about your inverter's efficiency. Lets assume 90% (including tare losses). Therefore your battery needs to supply about 1100 watthours per day (if there is no sun). Therefore your battery should store 4400 watthours.
You can probably do this with a 12 volt system: 4400 watthours ÷ 12 volts = 367 amphour battery (at 12 volts).
A couple of L-16 batteries will suffice.
Another option would be a 24 volt system with four golf cart batteries in series.
Does this all sound OK so far? If so, we can move on to the controller, array, and inverter....
--vtMaps4 X 235watt Samsung, Midnite ePanel, Outback VFX3524 FM60 & mate, 4 Interstate L16, trimetric, Honda eu2000i -
Re: How to select a MPPT Charge controller
I already told i am not only the new one in this field even a newest person, so please let me know how to design a 12V PV System with MPPT charge controller, Inverter sizing, and Battery back ????????? -
Re: How to select a MPPT Charge controller
yes this is ok, Please keep carry on -
Re: How to select a MPPT Charge controller
Ok--Lets do the math using our rule of thumbs design guidelines.
Assuming an AC fan and a 12 volt battery bank. 1-3 days of energy storage and 50% maximum discharge of the battery for longer battery life. Usually 2 days of storage and 50% discharge is a good choice:- 125 Watts * 8 hours per day * 1/0.85 inverter eff * 1/12 volts battery bank * 2 days of storage * 1/0.50 maximum discharge = 392 AH @ 12 volt battery bank
First, sizing the array based on battery bank (a large battery bank needs a large solar array for proper charging current). 5-13% is a typical range of acceptable of solar power for charging:- 392 AH * 14.5 volts charging * 1/0.77 panel+controller derating * 0.05 rate of charge = 340 Watt array minimum
- 392 AH * 14.5 volts charging * 1/0.77 panel+controller derating * 0.10 rate of charge = 738 Watt array nominal
- 392 AH * 14.5 volts charging * 1/0.77 panel+controller derating * 0.13 rate of charge = 960 Watt array "cost effective" maximum
[h=3]Islamabad
Average Solar Insolation figures[/h] Measured in kWh/m2/day onto a solar panel set at a 56° angle from vertical:
(For best year-round performance)
Jan
Feb
Mar
Apr
May
Jun
4.81
5.06
5.69
6.35
6.63
6.56
Jul
Aug
Sep
Oct
Nov
Dec
5.77
5.52
6.25
6.76
5.91
4.79
So, on average, you would get more than 4 hours of sun per day--So very conservative (and lots of sun in your area). The array needed to support a 125 watt AC fan would be:- 125 Watts * 8 hours * 1/0.52 over all system eff * 1/4 hours of sun per day = 481 Watt array minimum
One suggestion--You do some research on Ceiling fans. A 125 fan is a pretty large fan/uses a lot of power. You may be able to find fans that are more efficient--And even get down towards 25 watts. If you could find a smaller/more efficient fan that would meet your needs, your solar power system could be 1/5th as large and 1/5th as expensive.
In general, it is almost always better to spend your time/money on conservation vs just building a larger solar power system. For a typical solar installation with average quality deep cycle batteries in a warm climate--Your batteries will probably last 3-5 years. Battery replace is one of the big/ongoing costs for a solar power system.
If you could run the fan just when the sun is up (i.e., in a school/work space)--You can find DC input fans and connect them directly to the solar array--That saves you costs of batteries/ac inverter/solar charge controller--And your system will be about 1/4 the cost and no ongoing battery maintenance.
You might want to read this thread:
Solar Electric System for a School
His system plans are a lot larger than yours--But we have talked about many of the same issues. Send a private message to "Badar"--He has located some fans that may be of use for you (low power/high efficiency). And is in Pakistan too (local sourcing of materials).
-BillNear San Francisco California: 3.5kWatt Grid Tied Solar power system+small backup genset -
Re: How to select a MPPT Charge controller
yes your calculation is exact i made a mistake in calculations -
Re: How to select a MPPT Charge controller
That's great now what is next ? -
Re: How to select a MPPT Charge controller
Iftikhar,
The first question are my assumptions correct (your fan is probably a 230 VAC 50 Hz unit)?
Next, we can go through some equipment selection... Our suggestion is always to do a few "paper" designs first before you start buying equipment. After you do the paper design, you can review the costs/capabilities of the system and decide if you want to move forward, or revisit the loads (i.e., spend more time/money on high efficiency/not cheap fan units in this example).
Also--We, in the forum, usually make the assumption that power is collected (and stored in batteries) during the day and the power is used in the evening (sun is down, all power comes from battery bank), and you want to have power for a couple of days of cloudy weather (and use a backup generator for winter/monsoon seasons).
There are many different design requirements... Running an office/school/shop during the day. That means that much of the power comes from the solar panels directly--So a battery bank could be smaller. But the array has to be larger since it has to run the loads and charge the battery bank at the same time (5% to 13% rate of charge to the battery bank+power to run the battery bank).
For fans, perhaps you only need power during sunny/hot weather (like a school room/work shop) and when the sun is not shining, weather is cooler and you really do not need the sun--So you can run without a battery bank (much cheaper system, and much less maintenance).
So--Lets go with your system as stated today (as much for learning--and we have to start somewhere). Lets say that you want to run the fan if the sun is up or not (perhaps is humid during cloudy weather)--So a battery bank is still needed. And the fan is used in the late afternoon/evening (again a reason for the battery bank).
Using the information I posted in the earlier post--That is a typical 1,000 WH per day load that is used every day during afternoons/evening (home after work/kids come home from school, etc.).
We use rules of thumbs to make system designs easier and more cook book. Note, I am carrying 3-4 digits for calculations. This is so you can repeat my math (and catch my mistakes--very little of my posting is cut and paste replies and I do make mistakes sometimes), and to avoid cumulative errors. Solar design, to a large degree, is based on assumptions, "fudge factors", and experiences from lots of people in the forum. We try to be conservative, but if we get too conservative, the systems can become overly complex and expensive. Nothing we write here is "written in stone"--Ask questions and, if needed, change the factors/calculations to meet your needs.
The rules size a system to, hopefully, keep the battery bank "happy" and support your loads. Assuming your loads are accurate (we use a Kill-a-Watt type meter to do this--Here is a 230 VAC version).
Note that AC power is actually quite complex (math). You need to know about your loads when designing your system. First, there is a difference between Watts and "VA" (volt amps or Volts*Amps). Induction motors like yours may use 125 Watts but have a poor "power factor" -- Basically the current sine wave "lags" the voltage sine wave--It causes the motor to draw more current (amps) than would be guessed from the simple math. For example a 125 Watt Induction Motor (fan) with a 0.60 Power Factor:- Power = Volts * Amps (simple DC and AC math)
- Power = 125 Watts / 230 VAC = 0.54 amps AC
- Power = Volts * Amps * Cos (phase angle) = Volts * Amps * Power Factor (the real AC math)
What does that mean for you--Depends on how much you "oversize" your AC inverter (for example). If you get a 125 watt rated AC inverter, it will not run a 125 Watt Fan. Because the VA or Apparent Power of the fan is not 125 Watts but something larger. Using typical numbers:- VA = Power / PF = 125 Watts / 0.6 PF = 208 Watt AC inverter
And yet, more design rules... "Good" AC inverter can typically supply around 2x their rated power as surge current. And an AC induction motor may have ~5x rated current as starting surge... So the "apparent current" of 0.54 amps would surge:- 0.54 Amps running * 5 time surge = 2.7 amps surge current (starting current)
- 2.7 Amps surge * 230 VAC rated inverter = 621 VA surge rated inverter (where inverter VA=Watts rating)
- 621 VA / 2 surge rated inverter = 310.5 VA (Watt) minimum nominal rated inverter
The detailed engineering paper review has already said you need wiring/AC inverter that is ~2.5x larger than your fan Watt Rating. That is some of the details that we need to know when designing a system--A Kill-a-Watt type power meter will give you those measurements (PF, apparent amps, Watts, and Watt*Hours of energy usage).
Since the "heart" of any off grid power system is the battery bank, you need to learn all you can about batteries:
Working FAQ (all sorts of posts about basic solar/conservation information):
http://www.windsun.com/Batteries/Battery_FAQ.htm
http://www.batteryfaq.org/
http://batteryuniversity.com/
To select a battery bank--We have some rules of thumbs. For flooded cell batteries--We look at their Amp*Hour rating at the "20 Hour Rate" (i.e., a battery that will supply 2 amps for 20 hours until "dead" is a 20 HA rated battery bank) and use those numbers for a typical rules of thumbs (i.e., 20 hours works out to ~5 hours of usage for 2 nights, to 50% maximum discharge--A typical evening home power usage). Note that battery capacity appears to drop as you draw more current (a 100 AH battery bank at 20Hr may look like an 80 AH battery at 10 hour discharge rate).
A 392 AH flooded cell 12 volt battery can supply AC loads at these rates (typical rules of thumbs for true deep cycle batteries):- 392 AH * 12 volts * 0.85 inverter eff * 1/20 hour rate = 200 Watt average AC load
- 392 AH * 12 volts * 0.85 inverter eff * 1/8 hour rate = 500 Watt "typical maximum" continuous load
- 392 AH * 12 volts * 0.85 inverter eff * 1/5 hour rate = 800 Watt "maximum" continuous load
- 392 AH * 12 volts * 0.85 inverter eff * 1/2.5 hour rate = 1,599 Watt "maximum surge" 0load
And if you assume a maximum of 2x inverter surge support:- 1,599 Watt max surge / 2 times inverter surge rating = 800 Watt maximum "useful" AC inverter
I am going to stop here--Read and ask questions. We have talked about batteries and AC inverters. When designing for loads--That is really all you need to think about first. Charging system (solar, generator, etc.) are (for the most part) a separate set of design rules/goals and wiring.
Then we will continue.
-BillNear San Francisco California: 3.5kWatt Grid Tied Solar power system+small backup genset -
Re: How to select a MPPT Charge controller
Mr. Bill , I think i could not get exactly the battery sizing i send you a web there is a 12V system designing and i understood it exactly, it is not i am not understanding what you are saying but because of my poor english i am not understanding by a good way, Please check, there is written in simple english with equation , also advise me is this correct, i think this is system designing with PWM charge conroller, waiting for your reply. http://www.leonics.com/support/article2_12j/articles2_12j_en.php -
Re: How to select a MPPT Charge controller
Your link is similar to "our" design recommendations... For example, I suggest to discharge a battery by 50% maximum, they chose to discharge to 40% state of charge (a bit deeper discharge as "standard").
In general, their methods may be a bit less conservative--But not that different on average.
One thing missing from their calculation (that I did not see) is that a large battery bank may need a larger solar array.
In general, if you use the mid-range rules of thumbs (like 2 days of storage and 50% or 40% maximum discharge), most of the time you do not need to do a separate battery capacity calculation. However--We have seen many people "throw" batteries at an off grid system, and then have battery charging/life issues (too large of battery bank for installed solar array).
We try to give "ranges" and reasons for selection of actual values--A little bit less cook book and more understanding/customizing for "your" needs.
Anyway--Back to the rest of the system design issues/rules.
-BillNear San Francisco California: 3.5kWatt Grid Tied Solar power system+small backup genset -
Re: How to select a MPPT Charge controller
OK--The first set of equations I used to "size" your power system was "pure math". Now we get into some limitations that help us make some design choices going forward.
First is choosing the battery bank voltage... 12/24/48 volts are typical. There are some (mostly industrial) battery systems that can be 100-200 VDC--But we usually stay away from those. Safety issues go up with voltage and bank AH capacity (ability to surge very large amounts of current). Typically ~48 volt battery bank is about the highest voltage I would suggest for people that do not have specialized safety/engineering training. And usually, 48 volts is a "large enough" battery system for most homes.
To pick a battery bank voltage... I like to suggest around 100 Amps as the maximum nominal current for the AC inverter/DC loads etc...
So, a 12 volt battery bank at 100 amps would be a 1,200 watt load. 24 volt would be 2,400 watt load limit, and above that, look for a 48 volt battery bank. You will find a 2,000 watt 12 volt AC inverter--And they will work OK--You just need very heavy/short cables to run the inverter at rated load (and remember 2x rated load for a few seconds--cannot have too much voltage drop or inverter will shutdown).
The issues with 12 volt systems is that you discharge the battery bank to ~11.5 volts and have 10.5 volts for AC inverter cutoff... That gives you 0.5 - 1.0 volt maximum voltage drop. Takes very short cables and heavy copper to support those currents.
A 24 volt system would have a ~2 volt maximum drop and a 48 volt system would have a maximum of 4 volt drop.
And when you add the engineering/code "deratings", the wiring requirements can get even higher. Remember that AC inverters are "constant power" devices... Basically if you have a 100 watt load, you need 100 Watts (plus losses) for input power:- Power = Voltage * Current -- As battery voltage falls, the input current must rise to support the fixed AC load.
For example (using US Electrical Code), the branch circuit with NEC 1.25 derating (the wiring, circuit breakers, fuses, etc. need to be 1.25x larger than the expected load):- 1,200 Watt AC load * 1/0.85 inverter eff * 1/10.5 volts inverter cutoff * 1.25 NEC Derating = 168 Amp rated branch circuit.
Or round up to next standard size (175 amp breaker and wiring rating).
Another choice of Battery Bank voltage is your charging current. For example, typical MPPT controllers in the US range from ~15 amps to 45/60/80+ amps...
In your 1,000 WH per day example, I suggested a nominal ~300 Watt AC inverter--So a 12 volt battery bank is "OK" here.
Now look at the charging current. Say we choose 738 Watts (nominal 10% rate of charge for battery bank). Using MPPT Charge controller math:- 738 Watt array * 0.77 panel+controller derating * 1/14.5 volt charging = 39 amp controller @ 12 volt bank
- 738 Watt array * 0.77 panel+controller derating * 1/29.0 volt charging = 19.6 amp controller @ 24 volt bank
- 738 Watt array * 0.77 panel+controller derating * 1/58.0 volt charging = 9.8 amp controller 48 volt bank
Now... We also look at choosing the batteries. You have brand/type of batteries. Some are designed for deep cycle solar power systems, others are deigned for other use (like forklifts). Some batteries take higher charging voltages (i.e., your battery may need 15.5 to 16.0 volts to fully/quickly charge, but the AC inverter may have a 15.0 volt shut down).
Also, you can place batteries (cells) in series to add voltage. And place strings in parallel to add AH capacity. You can also find larger AH rated cells/batteries to reduce placing batteries in parallel (I like a single string with 2-3 strings in parallel maximum--Others do OK with more parallel strings, but that does require more battery maintenance).
392 AH @ 12 volt battery bank for this design... You can get 2x 6 volt @ 225 AH "golf cart batteries" in series x 2 parallel strings (4 batteries total) for a 12 volt @ 450 AH string:
Trojan T-105 6 Volt, 225 AH Deep Cycle Battery
Or you can pick larger battery. Just two of these in series:
Trojan L16H 6 Volt, 435 AH Deep Cycle Battery
Crown Industrial Battery - 12 Volts, 530 Amp-hours (forklift battery)
PVX-5340T 2 volt AGM cells, ~500 AH (6 AGM cells in series)
There is no "correct choice" here... What is available and "cost effective" for you. Flooded cell batteries are cheaper and tend to be more forgiving... Unless nobody checks the electrolyte levels.
AGMs--No electrolyte to check, much cleaner (no acid fumes/spills), very high surge current support. 2x as expensive, possibly a bit shorter life for similar class battery.
Forklift batteries--Very rugged. Tend to use more distilled water. Can have higher self discharge... Can last 15+ years.
Flooded cell batteries using a hydrometer and thermometer for logging (weekly/monthly) temperature corrected specific gravity is really helpful to understand how your system is performing. Sealed batteries like AGM are more difficult to "see" what is happening.
A Battery Monitor (Victron is another very good brand) is very helpful for non-technical people to understand power usage/battery charging/etc.
What questions do you have, and where to go next... There are a lot of suggestions/questions about specific hardware. As well as details about how batteries perform (different discharge rates, temperature, etc.)--But that will be dependent on what is available in your market.
-BillNear San Francisco California: 3.5kWatt Grid Tied Solar power system+small backup genset
Categories
- All Categories
- 229 Forum & Website
- 137 Solar Forum News and Announcements
- 1.4K Solar News, Reviews, & Product Announcements
- 199 Solar Information links & sources, event announcements
- 898 Solar Product Reviews & Opinions
- 256 Solar Skeptics, Hype, & Scams Corner
- 22.5K Solar Electric Power, Wind Power & Balance of System
- 3.5K General Solar Power Topics
- 6.7K Solar Beginners Corner
- 1K PV Installers Forum - NEC, Wiring, Installation
- 2.1K Advanced Solar Electric Technical Forum
- 5.6K Off Grid Solar & Battery Systems
- 428 Caravan, Recreational Vehicle, and Marine Power Systems
- 1.1K Grid Tie and Grid Interactive Systems
- 654 Solar Water Pumping
- 816 Wind Power Generation
- 624 Energy Use & Conservation
- 619 Discussion Forums/Café
- 312 In the Weeds--Member's Choice
- 75 Construction
- 124 New Battery Technologies
- 108 Old Battery Tech Discussions
- 3.8K Solar News - Automatic Feed
- 3.8K Solar Energy News RSS Feed