Charge, Float and Cutoff Voltages for Large LiFePO4 Cells
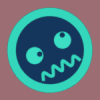
RonR
Registered Users Posts: 7 ✭✭
First, this is a great site with incredible participation by some very knowledgable folks, thanx!
I'm an electrical engineer, the first step in the design process is to collect requirements, understand the options and issues, then get to work.
Not so simple when dealing with ever shifting and conflicting data surrounding LiFePO4. I've used T105's for decades but LiFePO4 is a different kind of animal. I know that most of the folks on this site use various lead based technologies, but I have seen a few LiFePO4 posts and this is clearly the place to go for unbiased MPPT info.
My application is an RV with 2 solar panels (about 600W), an MPPT controller (not selected), about 200Ah of LiFePO4 battery at 24V (8 cells), a custom micro-controller and interface electronics (individual cell voltage, SOC calculation, over voltage and under voltage disconnect, alarms, etc, etc).
Why LiFePO4? This is a small RV (sprinter van), using LiFePO4 is about a quarter the weight and size of any lead solution I could find. In this case about 200 less pounds and 1.5 less cubic feet. Considering the relative lifetimes LiFePO4 is even cheaper, in the long run, up front costs are pretty hard to stomach. At the end of the day (with a lot of insulation and using one of the ultra efficient mini-split systems) I hope to power a small air conditioner.
This is partly an education / hobby project and partly a "get rid of the generator in the RV" project.
Considering the cost of LiFePO4 I plan to buy a little more battery than I need and restrict the operating range to roughly 95% max charge and 20% minimum charge to maximize the cycle life. Max discharge rate is about .5C / 100A and max charge about .1C / 10A so the system never has significant self heating. At room temperature (20C) it looks like the charge cutoff should be about 3.55V and the low voltage cutoff about 3V. These voltages are all over the map depending on your choice of vendor, web site or battery "guru", but my intent is to not stress the battery while still trying to get a usable 75% of net capacity. I think I will need to test to find the correct voltages. The system is intended to be automatic and available for charge or discharge at any time.
First question.
How do you guys handle "float"? The battery is charged, so I just want to maintain without damage. Apparently (based on several LiFePO4 papers) just leaving the charge voltage (even at almost no current) starts to degrade battery cycle life. Some references recommend floating at 3.3V, which seems like a good idea and is above the typical battery discharge voltage. During the day this would allow the panels to supply most of the demand power until demand drags the system voltage down to 3.2V when the battery will start to deliver energy. Great, but how and when do you decide that you need to start a charge cycle (bring the batter voltage back up to 3.5V)? Is this where SOC comes in and we arbitrarily select (let's say) 80% charge as the point to start a charge cycle?
Second Question.
Temperature is a big deal. For discharge at 0C / 32F, 75% discharge occurs at about 2.8V. 2.3V at -20C, but some sources recommend not using the battery at that temperature. It looks like the only reasonable thing to do is the heat the battery box (hot water is not a too hard to do) since this almost doubles the usable capacity at -20C and adds 30% at 0C. What has been your experience? Has anyone had any experience at cold temperatures?
Third Question.
I have had no luck in finding an MPPT controller that has either the correct LiFePO4 charging profile or easy to use hooks to use external controls. Are there any units you can recommend?
Thanx
RonR
I'm an electrical engineer, the first step in the design process is to collect requirements, understand the options and issues, then get to work.
Not so simple when dealing with ever shifting and conflicting data surrounding LiFePO4. I've used T105's for decades but LiFePO4 is a different kind of animal. I know that most of the folks on this site use various lead based technologies, but I have seen a few LiFePO4 posts and this is clearly the place to go for unbiased MPPT info.
My application is an RV with 2 solar panels (about 600W), an MPPT controller (not selected), about 200Ah of LiFePO4 battery at 24V (8 cells), a custom micro-controller and interface electronics (individual cell voltage, SOC calculation, over voltage and under voltage disconnect, alarms, etc, etc).
Why LiFePO4? This is a small RV (sprinter van), using LiFePO4 is about a quarter the weight and size of any lead solution I could find. In this case about 200 less pounds and 1.5 less cubic feet. Considering the relative lifetimes LiFePO4 is even cheaper, in the long run, up front costs are pretty hard to stomach. At the end of the day (with a lot of insulation and using one of the ultra efficient mini-split systems) I hope to power a small air conditioner.
This is partly an education / hobby project and partly a "get rid of the generator in the RV" project.
Considering the cost of LiFePO4 I plan to buy a little more battery than I need and restrict the operating range to roughly 95% max charge and 20% minimum charge to maximize the cycle life. Max discharge rate is about .5C / 100A and max charge about .1C / 10A so the system never has significant self heating. At room temperature (20C) it looks like the charge cutoff should be about 3.55V and the low voltage cutoff about 3V. These voltages are all over the map depending on your choice of vendor, web site or battery "guru", but my intent is to not stress the battery while still trying to get a usable 75% of net capacity. I think I will need to test to find the correct voltages. The system is intended to be automatic and available for charge or discharge at any time.
First question.
How do you guys handle "float"? The battery is charged, so I just want to maintain without damage. Apparently (based on several LiFePO4 papers) just leaving the charge voltage (even at almost no current) starts to degrade battery cycle life. Some references recommend floating at 3.3V, which seems like a good idea and is above the typical battery discharge voltage. During the day this would allow the panels to supply most of the demand power until demand drags the system voltage down to 3.2V when the battery will start to deliver energy. Great, but how and when do you decide that you need to start a charge cycle (bring the batter voltage back up to 3.5V)? Is this where SOC comes in and we arbitrarily select (let's say) 80% charge as the point to start a charge cycle?
Second Question.
Temperature is a big deal. For discharge at 0C / 32F, 75% discharge occurs at about 2.8V. 2.3V at -20C, but some sources recommend not using the battery at that temperature. It looks like the only reasonable thing to do is the heat the battery box (hot water is not a too hard to do) since this almost doubles the usable capacity at -20C and adds 30% at 0C. What has been your experience? Has anyone had any experience at cold temperatures?
Third Question.
I have had no luck in finding an MPPT controller that has either the correct LiFePO4 charging profile or easy to use hooks to use external controls. Are there any units you can recommend?
Thanx
RonR
Comments
-
Re: Charge, Float and Cutoff Voltages for Large LiFePO4 Cells
Not that I have anything worthwhile to add to what you're asking for, I'm not clear if you are going to purchase and use an existing BMS or you're looking for values to create your own custom BMS. -
Re: Charge, Float and Cutoff Voltages for Large LiFePO4 CellsNot that I have anything worthwhile to add to what you're asking for, I'm not clear if you are going to purchase and use an existing BMS or you're looking for values to create your own custom BMS.
I would prefer to purchase (it takes a lot of work to make a reliable robust product) but it may be that at this time the only solution is to build your own. -
Re: Charge, Float and Cutoff Voltages for Large LiFePO4 Cells
You may like to look at the BMS products for LiFePo systems at :
http://www.ev-power.com.au/-EV-Power-BMS-Control-Units-.html, or
http://www.ev-power.com.au/-Thundersky-Battery-Balancing-System-.html -
Re: Charge, Float and Cutoff Voltages for Large LiFePO4 CellsHow do you guys handle "float"? The battery is charged, so I just want to maintain without damage.
I don't know anything about LiFePO4, but they sound very promising.
I can give you an idea about float. Maintain the average current into the battery at zero. While you do that, the voltage will very slowly decrease from where it was at the end of charge to the resting voltage.
Stanard solar chargers do two constant-voltage stages - absorb and float. IMHO, this could be made to work with nearly any kind of batteries, but since you're EE and the system is small, it might be easier for you to make a specialized charger. -
Re: Charge, Float and Cutoff Voltages for Large LiFePO4 Cells
Midnite (boB, Robin, and Ryan "halfcrazy) has probably the most active "larger" MPPT charge controller program right now (and they are close to releasing a mid-range MPPT controller too)... And they have just added a remote reading battery shunt--So the controller can make decisions based on current into/out of the battery proper (perhaps, even AH over time too).
Rogue has a lot of on-going development in "medium" MPPT controllers--You should probably give Marc a call there.
I would highly recommend that you contact them directly (at least as a start). Midnite also has an active forum too.... Not that I want to push you away from here.
-BillNear San Francisco California: 3.5kWatt Grid Tied Solar power system+small backup genset -
Re: Charge, Float and Cutoff Voltages for Large LiFePO4 Cells
here is an active MN thread on Li batteries http://midniteforum.com/index.php?topic=1492.new#new
KID #51B 4s 140W to 24V 900Ah C&D AGM
CL#29032 FW 2126/ 2073/ 2133 175A E-Panel WBjr, 3 x 4s 140W to 24V 900Ah C&D AGM
Cotek ST1500W 24V Inverter,OmniCharge 3024,
2 x Cisco WRT54GL i/c DD-WRT Rtr & Bridge,
Eu3/2/1000i Gens, 1680W & E-Panel/WBjr to come, CL #647 asleep
West Chilcotin, BC, Canada -
Re: Charge, Float and Cutoff Voltages for Large LiFePO4 Cellswestbranch wrote: »here is an active MN thread on Li batteries http://midniteforum.com/index.php?topic=1492.new#new
Thanx guys, great info.
Looks like both Rogue and Midnight can be tweaked to work with LiFePO4 without over charging. I need to spend some time digesting the info on both of those great sites. Rogue seems to have more options and does appeal to the geek in me.
Has anyone had any experience with either product in a high vibration environment like an RV or truck?
Thanx -
Re: Charge, Float and Cutoff Voltages for Large LiFePO4 Cells
I have been running an off grid 24V system with 360AH of LiFePO4 batteries, 1.2kW of panels and my own MPPT controller with similar max charge rate of .1C and discharge of .5C for about six months now.
With this low charge rate i reckon 3.45 volts is a high enough maximum cell voltage to get above 95% charge. I currently have my controller programmed to limit charge voltage to 3.45 volts/cell and to go to float when current going into the battery gets below C/20. I have set the float voltage to the no load full voltage of the batteries which seems to be around 3.32 volts/cell. System will go back to full charge at the start of the next day or if the no load voltage goes below ~3.27 volts/cell which is around 60-70% SOC. I am fortunate that the temperature where we live is in the range 45C-0C (~110F-32F) and spends most of its time between 30C-10C so i don't have to worry too much about voltage temperature compensation.
I am surprised by the temperature specs you have quoted, the temperature graphs for the Winston batteries i am using show a voltage of 2.7v/cell for 80%DOD at -25C, they even give a graph for -45C!
From what i have read about the LiFePO4 cells, i think the best way to maximise the life of the batteries is to try and keep them centred around 50% SOC. This is obviously not practical if you need to store as much charge as possible for a rainy day.
With this in mind when i get around to it i will be modifying my controller to charge to around 80%SOC, and once a week or so to 3.45-3.50 v/cell to reset the AH meter with a manual override to get to >95%SOC if i see bad weather ahead.Off-Grid with LFP (LiFePO4) battery, battery Installed April 2013
32x90Ah Winston cells 2p16s (48V), MPP Solar PIP5048MS 5kW Inverter/80A MPPT controller/60A charger, 1900W of Solar Panels
modified BMS based on TI bq769x0 cell monitors.
Homemade overall system monitoring and power management https://github.com/simat/BatteryMonitor
-
Re: Charge, Float and Cutoff Voltages for Large LiFePO4 CellsFrom what i have read about the LiFePO4 cells, i think the best way to maximise the life of the batteries is to try and keep them centred around 50% SOC. This is obviously not practical if you need to store as much charge as possible for a rainy day.
I've read if you keep them between 20 and 80% there's no destructive forces that would shorten their lives. This gives you an ample room for cycling and very suitable for off-grid applications.
How do you go about cell balancing? -
Re: Charge, Float and Cutoff Voltages for Large LiFePO4 CellsI've read if you keep them between 20 and 80% there's no destructive forces that would shorten their lives. This gives you an ample room for cycling and very suitable for off-grid applications.
I am not sure if it is voltage or SOC that is the major factor that degrades the battery capacity. This web page has some interesting information http://batteryuniversity.com/learn/article/how_to_prolong_lithium_based_batteries
It is about Li-ion batteries, but i would think this may applicable to LiFePO4 based batteries. The interesting section is about the effect of temperature and SOC on the life of the batteries, the question i have is, is it the SOC with temperature that is directly degrading the battery or the higher voltage that a higher SOC implies?
If possible, I would be interested in a link to the articles that give the 20 to 80% info.How do you go about cell balancing?Off-Grid with LFP (LiFePO4) battery, battery Installed April 2013
32x90Ah Winston cells 2p16s (48V), MPP Solar PIP5048MS 5kW Inverter/80A MPPT controller/60A charger, 1900W of Solar Panels
modified BMS based on TI bq769x0 cell monitors.
Homemade overall system monitoring and power management https://github.com/simat/BatteryMonitor
-
Re: Charge, Float and Cutoff Voltages for Large LiFePO4 CellsIf possible, I would be interested in a link to the articles that give the 20 to 80% info.
I don't have a link, but I've read it in several places. These were mostly discussions of laptop and cell-phone batteries. There are numerous on the Web. For example, the article that you're quotes talks about upper limit.
I was reading this stuff because I was going to use Li batteries for my 2W micro solar system, but looks like they don't work when it's below freezing, so I switched to lead-acid.For my system i do it manually.
How do you do it manually? Do you measure individual cells with a voltmeter? What do you do if you find a deviating cell? -
Re: Charge, Float and Cutoff Voltages for Large LiFePO4 CellsI was reading this stuff because I was going to use Li batteries for my 2W micro solar system, but looks like they don't work when it's below freezing, so I switched to lead-acid.
2W is very micro!
I think the low temperature characteristics of the LiFePO4 batteries has improved in recent years. I do remember reading somewhere that the addition of Yttrium to the Winston (Thundersky) batteries has enhanced low temperature operation. If Winston's performance graphs for their batteries can be believed the performance at -25C looks quite respectable. I am not sure what it does to the life of the batteries running them at these temperatures, it is not really relevant to my situation.How do you do it manually? Do you measure individual cells with a voltmeter? What do you do if you find a deviating cell?
I use a gadget called a Cellog8 to display the voltage of the 8 block of cells i have in series. The Cellog8 also provides an alarm if any of the blocks of cells get too low or high. The cell voltages only start to diverge when they are nearly empty or full, so i keep an eye on the individual voltages when there are only a few AH to go until they are full, or until the cells voltages are over 3.4 volts.
Any cells that are 20 or so mV above the others i put a 1 ohm resistor across. I disconnect the resistor when the high cell voltage has dropped down to the others. With cells that are low i use my current limited adjustable power supply that runs off the inverter to inject extra current into the cell that is low. I ramp the current down as the low voltage cell rises to the others.
It is not too hard to do and does not have to be done very often. A word of warning, don't get distracted while you are doing the balancing as you could overcharge and damage the cells you are balancing or flatten them.
When i get around to it, automatic cell balancing will get integrated into the next iteration of my MPPT controller.Off-Grid with LFP (LiFePO4) battery, battery Installed April 2013
32x90Ah Winston cells 2p16s (48V), MPP Solar PIP5048MS 5kW Inverter/80A MPPT controller/60A charger, 1900W of Solar Panels
modified BMS based on TI bq769x0 cell monitors.
Homemade overall system monitoring and power management https://github.com/simat/BatteryMonitor
-
Re: Charge, Float and Cutoff Voltages for Large LiFePO4 CellsAny cells that are 20 or so mV above the others i put a 1 ohm resistor across. I disconnect the resistor when the high cell voltage has dropped down to the others. With cells that are low i use my current limited adjustable power supply that runs off the inverter to inject extra current into the cell that is low. I ramp the current down as the low voltage cell rises to the others.
Thank you for the explanation.
Is it always the same "bad" cells that need adjustments? Or is it pretty much random? -
Re: Charge, Float and Cutoff Voltages for Large LiFePO4 CellsIs it always the same "bad" cells that need adjustments? Or is it pretty much random?
The imbalance i had dates back from when the cells were new. When i bought them i paid extra to have them fully charged and balanced. Unfortunately i assumed this had been done correctly and installed the batteries without checking them, a mistake i won't be making again!
In future i will always balance any new batteries by connecting them in parallel and charging them to 3.6 volts until the current drops to around C/100 before i use them.
I haven't had the batteries for long enough to really know how much they go out of balance by themselves. From what i have read and my experience to date , i don't think it will be a big problem.Off-Grid with LFP (LiFePO4) battery, battery Installed April 2013
32x90Ah Winston cells 2p16s (48V), MPP Solar PIP5048MS 5kW Inverter/80A MPPT controller/60A charger, 1900W of Solar Panels
modified BMS based on TI bq769x0 cell monitors.
Homemade overall system monitoring and power management https://github.com/simat/BatteryMonitor
-
Re: Charge, Float and Cutoff Voltages for Large LiFePO4 CellsIn future i will always balance any new batteries by connecting them in parallel and charging them to 3.6 volts until the current drops to around C/100 before i use them.
It would make 9000AH bank. Not that easy to chargeI haven't had the batteries for long enough to really know how much they go out of balance by themselves. From what i have read and my experience to date , i don't think it will be a big problem.
That is good. I thought you would need to re-balance it every week. If it hardly ever happens then this is not a big deal. -
Re: Charge, Float and Cutoff Voltages for Large LiFePO4 CellsIt would make 9000AH bank. Not that easy to chargeThat is good. I thought you would need to re-balance it every week. If it hardly ever happens then this is not a big deal.Off-Grid with LFP (LiFePO4) battery, battery Installed April 2013
32x90Ah Winston cells 2p16s (48V), MPP Solar PIP5048MS 5kW Inverter/80A MPPT controller/60A charger, 1900W of Solar Panels
modified BMS based on TI bq769x0 cell monitors.
Homemade overall system monitoring and power management https://github.com/simat/BatteryMonitor
-
It's been a while, but I have come to some conclusions that I would like to share.
1 Each vendors Li cells are slightly different and over time batteries from the same vendor will also be different. The chemistry and technology are still evolving.
2 If you buy a commercial system, you are done, your vendor takes the responsibility. If you don't, you need to understand what you are doing to avoid costly mistakes and potential damage.
3 Over time all vendors have been reducing the recommended max charge voltage with no changes to the battery. This makes sense since early max charge voltages provided little additional capacity and reduced the battery life. It makes sense to buy more battery and operate at 90 to 95% max capacity to maximize battery life.
4 Most BMS systems are made for vehicle / high load applications. Voltage set points are based on multiple C charge (braking) and discharge (acceleration), numbers in the 100s of amps for a low voltage system. My system occasionally would draw 100A but usually about 10A and could never charge at more than 75A. At these low rates you are "off the chart" on all the data sheets I have seen.
5 I made up a low current (10A) charge and discharge test rig to find the best voltage points at my operating currents. You will have trouble duplicating the "pretty" commercial curves since you really don't know the max capacity so it is very hard to create a %capacity scale for the horizontal axis. I simply changed it to amp-hrs. Now as you plot cell V against amp-hrs you will clearly see the change in slope as you reach full charge and full discharge. Your call on how far away from the straight line section you want to set your upper and lower limits.
6 The limits do change over temperature. I have no way to measure this so I took my data from above and conservatively scaled it using the many commercial curves that are online.
7 I purchased the cheap HousePowerBMS as a fail safe backup. Still coding a more appropriate controller using a integrated LCD system from 4D systems. I think the HousePower voltage set points are both too high, and too low.
8 Many folks don't use a BMS. I think this works given a good initial balance and general attended usage. I expect to have my system operate autonomously for weeks at a time and don't see how I could not have a BMS.
9 While the HousePowerBMS does do top balancing, it occurs at what I think is too high a voltage. My charging system is set to just barely reach that voltage. The main function of the BMS is to trigger relays to disconnect loads and sources if the battery voltage is too high or too low.
10 Any system should be designed to "fail safe" if the controller lose power. I was able to do this by using a mix of normally open of closed relays along with the correct flavor power FETS.
This is not a difficult problem but it seems that a lot of good information from one area (let's say lithium laptop batteries) is being applied to other areas (let's say a battery bank for an RV) with poor or confusing results. Each application is different and each lithium battery is unique. You need to be careful to understand the application any online data is coming from.
Good luck.
Ron
Categories
- All Categories
- 229 Forum & Website
- 137 Solar Forum News and Announcements
- 1.4K Solar News, Reviews, & Product Announcements
- 199 Solar Information links & sources, event announcements
- 898 Solar Product Reviews & Opinions
- 256 Solar Skeptics, Hype, & Scams Corner
- 22.5K Solar Electric Power, Wind Power & Balance of System
- 3.5K General Solar Power Topics
- 6.7K Solar Beginners Corner
- 1K PV Installers Forum - NEC, Wiring, Installation
- 2.1K Advanced Solar Electric Technical Forum
- 5.6K Off Grid Solar & Battery Systems
- 428 Caravan, Recreational Vehicle, and Marine Power Systems
- 1.1K Grid Tie and Grid Interactive Systems
- 654 Solar Water Pumping
- 816 Wind Power Generation
- 624 Energy Use & Conservation
- 619 Discussion Forums/Café
- 312 In the Weeds--Member's Choice
- 75 Construction
- 124 New Battery Technologies
- 108 Old Battery Tech Discussions
- 3.8K Solar News - Automatic Feed
- 3.8K Solar Energy News RSS Feed