System Recommendations, Improvements?
Options
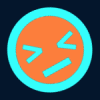
amac4all
Registered Users Posts: 6 ✭
I'm losing money on charge controllers because of newbie mistakes and cheap chinese stuff.(I think). I made a diagram of my setup below. I recently started having my PWM charge controller act up. I caught it over heating. It still acts like it works when I plug it all back in, but before long it gets too hot. Also the inverter has begun sensing an improper load and shuts off. Sometimes it says the load is insufficient and sometimes it says it's too high. I suspect my problem is the charge controller. The manual sucks and the lcd display doesn't display what the manual says it should. It has become clear to me that the PWM Charge controller is the key to the whole setup.
Judging by my diagram;
Is the PWM Controller not big enough? would a 60amp perform better?
The 10 ga wire that runs to the inverter, is it not big enough?
Is my Inverter too big for my system?
I just want to be able to depend on this system if the power fails. I want it to just sit there and be ready to provide power if needed.
Attachment not found.
Judging by my diagram;
Is the PWM Controller not big enough? would a 60amp perform better?
The 10 ga wire that runs to the inverter, is it not big enough?
Is my Inverter too big for my system?
I just want to be able to depend on this system if the power fails. I want it to just sit there and be ready to provide power if needed.
Attachment not found.
Comments
-
Re: System Recommendations, Improvements?
Welcome to the forum... First lets start with the solar array... What are the panels and how many do you have (watt/Vmp/Imp ratings).
You show the panels wired in series--But I would guess they are wired in parallel (Vmp-array should be in the 17.5 to 18.6 volt range for optimum power transfer when using a PWM controller).
Next, tell us more about your batteries... a pair of 6 volt @ ~220 AH wired in series for a 12 volt battery bank?
It would also be helpful to understand your AC loads (watts * hours per day at the very least).
-BillNear San Francisco California: 3.5kWatt Grid Tied Solar power system+small backup genset -
Re: System Recommendations, Improvements?Welcome to the forum... First lets start with the solar array... What are the panels and how many do you have (watt/Vmp/Imp ratings).
You show the panels wired in series--But I would guess they are wired in parallel (Vmp-array should be in the 17.5 to 18.6 volt range for optimum power transfer when using a PWM controller).
Next, tell us more about your batteries... a pair of 6 volt @ ~220 AH wired in series for a 12 volt battery bank?
It would also be helpful to understand your AC loads (watts * hours per day at the very least).
-Bill
5 145 watt panels, 7.75 amps each, wired just like the drawing shows. I guess that's series.
batteries. 6v trojan t105re wired in series (220 or 225 AH)
zero load most of the time. Though I want to be able to run a freezer 24/7 out there if I have to. It draws about 110watts most of the time. -
Re: System Recommendations, Improvements?
http://www.amazon.com/145w-Polycrystalline-Solar-Panel-Pack/dp/B007VPQP5Q/ref=sr_1_1?s=lawn-garden&ie=UTF8&qid=1367266555&sr=1-1&keywords=dmsolar
These are the exact solar panels
Maximum/Peak Voltage (Vmp): 18.7 V
Open Circuit Voltage (Voc): 22.3 V
Maximum/Peak Current (Imp): 7.75 A
Short Circuit Current (Isc): 8.37 A -
Re: System Recommendations, Improvements?
If there is a 110 W draw that is a constant load of 110Watts... not "Zero most of the tme"
KID #51B 4s 140W to 24V 900Ah C&D AGM
CL#29032 FW 2126/ 2073/ 2133 175A E-Panel WBjr, 3 x 4s 140W to 24V 900Ah C&D AGM
Cotek ST1500W 24V Inverter,OmniCharge 3024,
2 x Cisco WRT54GL i/c DD-WRT Rtr & Bridge,
Eu3/2/1000i Gens, 1680W & E-Panel/WBjr to come, CL #647 asleep
West Chilcotin, BC, Canada -
Re: System Recommendations, Improvements?5 145 watt panels, 7.75 amps each, wired just like the drawing shows. I guess that's series.
batteries. 6v trojan t105re wired in series (220 or 225 AH)
zero load most of the time. Though I want to be able to run a freezer 24/7 out there if I have to. It draws about 110watts most of the time.
...
Maximum/Peak Voltage (Vmp): 18.7 V
Open Circuit Voltage (Voc): 22.3 V
Maximum/Peak Current (Imp): 7.75 A
Short Circuit Current (Isc): 8.37 A
Ok... That is a good start. First, the panels should be wired in parallel (+ to +, - to -, for all panels). That will give you an array with Vmp~18.7 volts and Imp~38.75 amps for the array.
If the panels are connected in series (+ from one panel to - to the next, and so on for the rest of the panels) that would give you a Vmp-array ~ 93.5 Volts and Imp-array~7.75 amps.
If these panels are series connected (like stacking D Cell batteries in a flash light), that is not going to make either your PWM controller or you very happy. PWM controllers (pulse width modulation) are just "fancy" On/Off switches. When current is needed, the controller turns on, and when less/zero current is needed, the switch (PWM controller) just turns off (do this 10's to 1,000's of times a second, more "on time" is higher average current, less "on time" is less average current--or Pulse Width Modulation).
Depending on the PWM controller, the maximum Voc-array votlage (open circuit voltage) will be >130 VDC pretty easily. Not many small/less expensive PWM controllers can manage that sort of voltage level (most can manage ~30 to 40 volts for a 12 volt controller).
And you won't be happy, because the most current you can get out of that array is ~7.75 amps--Or the current of one solar panel.
So--Your first step is to check if your panels are parallel or series connected.
And, you will need to decide if you want to rewire to parallel connected solar panels (you should have a fused/breaker equipped combiner box to protect solar panels against internal shorts) and a new PWM controller (same brand or different). You would need to check the specifications and ensure that it can manage near 40 amp Imp solar array (many controllers have safety margins built in, others need to be derated--depends on the controller mfg.).
Or, you can get an MPPT type charge controller. These are very nice devices, can have a lot more options (logging, remote battery temperature sensing, some have Internet web servers built in, etc.). But, you are looking at $500 to $600+ for such a controller. The MPPT controller can take the high voltage / low current from the solar array and efficiently "down convert" to low voltage / high current to charge the battery bank. A useful reason to use "higher Vmp-array" setups is you can put the solar array much farther away from the Battery bank+charge controller and use smaller gauge copper wire (save money on copper).
In general, if this were a smaller system with a closely mounted solar array, less than 400 watts, a PWM controller may work just fine. And for over 800 watt array and/or a more than a few 10's of feet of distance from array to battery bank, you probably should look closely at a MPPT type charge controller.
We have more to discuss--But lets get the "front end" right first. You need to get those batteries on charge so they do not get damaged (do you have a hydrometer to check that they are getting >90% charged a couple times a week and don't sit below ~75% state of charge for more than a few hours/days at a time?).
-BillNear San Francisco California: 3.5kWatt Grid Tied Solar power system+small backup genset -
Re: System Recommendations, Improvements?Also the inverter has begun sensing an improper load and shuts off. Sometimes it says the load is insufficient and sometimes it says it's too high.
The 10 ga wire that runs to the inverter, is it not big enough?
Is my Inverter too big for my system?
I suspect that if you checked the Inverter manual, you'd find that the minimum recommended wire size is much larger than 10ga. What size fuse are you using? The manual probably also has a recommended size that matches the wire size.
Is your Inverter too big? Most folks will say that 1000W is the biggest that you'd want to use with a 12V system. Having said that, what is the maximum load that you'd want to run - taking into account portential surge?
Just another Newb
-
Re: System Recommendations, Improvements?
The fuse should be a 40amp fuse. I'm not sure why I used 10ga wire. Probably was what I had available at the time. I have 6 ga I think, so I'll replace that.
The only load I plan to use on this system is a 7 cubit ft freezer. My kilowatt tool says it runs at about 110 watts most of the time. I'm not sure what the surge level would be, but I'm sure it would be far less than the 1000 watt inverter (continuous, 2000k surge) can handle. -
Re: System Recommendations, Improvements?
That's a lot of good help Bill.Ok... That is a good start. First, the panels should be wired in parallel (+ to +, - to -, for all panels). That will give you an array with Vmp~18.7 volts and Imp~38.75 amps for the array.
If the panels are connected in series (+ from one panel to - to the next, and so on for the rest of the panels) that would give you a Vmp-array ~ 93.5 Volts and Imp-array~7.75 amps.
If these panels are series connected (like stacking D Cell batteries in a flash light), that is not going to make either your PWM controller or you very happy. PWM controllers (pulse width modulation) are just "fancy" On/Off switches. When current is needed, the controller turns on, and when less/zero current is needed, the switch (PWM controller) just turns off (do this 10's to 1,000's of times a second, more "on time" is higher average current, less "on time" is less average current--or Pulse Width Modulation).
Depending on the PWM controller, the maximum Voc-array votlage (open circuit voltage) will be >130 VDC pretty easily. Not many small/less expensive PWM controllers can manage that sort of voltage level (most can manage ~30 to 40 volts for a 12 volt controller).
And you won't be happy, because the most current you can get out of that array is ~7.75 amps--Or the current of one solar panel.
So--Your first step is to check if your panels are parallel or series connected.
And, you will need to decide if you want to rewire to parallel connected solar panels (you should have a fused/breaker equipped combiner box to protect solar panels against internal shorts) and a new PWM controller (same brand or different). You would need to check the specifications and ensure that it can manage near 40 amp Imp solar array (many controllers have safety margins built in, others need to be derated--depends on the controller mfg.).
Or, you can get an MPPT type charge controller. These are very nice devices, can have a lot more options (logging, remote battery temperature sensing, some have Internet web servers built in, etc.). But, you are looking at $500 to $600+ for such a controller. The MPPT controller can take the high voltage / low current from the solar array and efficiently "down convert" to low voltage / high current to charge the battery bank. A useful reason to use "higher Vmp-array" setups is you can put the solar array much farther away from the Battery bank+charge controller and use smaller gauge copper wire (save money on copper).
In general, if this were a smaller system with a closely mounted solar array, less than 400 watts, a PWM controller may work just fine. And for over 800 watt array and/or a more than a few 10's of feet of distance from array to battery bank, you probably should look closely at a MPPT type charge controller.
We have more to discuss--But lets get the "front end" right first. You need to get those batteries on charge so they do not get damaged (do you have a hydrometer to check that they are getting >90% charged a couple times a week and don't sit below ~75% state of charge for more than a few hours/days at a time?).
-Bill -
Re: System Recommendations, Improvements?The fuse should be a 40amp fuse. I'm not sure why I used 10ga wire. Probably was what I had available at the time. I have 6 ga I think, so I'll replace that.
The only load I plan to use on this system is a 7 cubit ft freezer. My kilowatt tool says it runs at about 110 watts most of the time. I'm not sure what the surge level would be, but I'm sure it would be far less than the 1000 watt inverter (continuous, 2000k surge) can handle.
Actually, don't be so sure of that... Small fridge/freezers typically use the same pumps as the larger units. And a 1,200 to 1,500 watt inverter is a good minimum size inverter for a fridge+a few lights, cell charger, laptop computer...
Having short/heavy wiring between the inverter and battery bank will be a big help too to ensure the inverter has all of the energy needed to support the starting surge. Just to give you a good idea on the wiring requirements:
1,000 watts * 1/0.85 inverter eff * 1/10.5 battery cutoff voltage * 1.25 NEC derating = 140 Amp minimum DC branch circuit+fusing
Of course, if you do not plan on running 1,000 watts (other than starting surge), then a 150 Amp rated wiring+breaker is on the over kill side. But you still need to make sure you have heavy enough wiring that you do not have more than ~0.5 to 1.0 maximum voltage drop with high surge current (a good inverter can supply upwards of 2x rated watts for surge current).
-BillNear San Francisco California: 3.5kWatt Grid Tied Solar power system+small backup genset -
Re: System Recommendations, Improvements?
Was there more information you wanted to tell me about the back end?
Categories
- All Categories
- 227 Forum & Website
- 135 Solar Forum News and Announcements
- 1.3K Solar News, Reviews, & Product Announcements
- 198 Solar Information links & sources, event announcements
- 895 Solar Product Reviews & Opinions
- 255 Solar Skeptics, Hype, & Scams Corner
- 22.4K Solar Electric Power, Wind Power & Balance of System
- 3.5K General Solar Power Topics
- 6.7K Solar Beginners Corner
- 1K PV Installers Forum - NEC, Wiring, Installation
- 2.1K Advanced Solar Electric Technical Forum
- 5.5K Off Grid Solar & Battery Systems
- 428 Caravan, Recreational Vehicle, and Marine Power Systems
- 1.1K Grid Tie and Grid Interactive Systems
- 652 Solar Water Pumping
- 815 Wind Power Generation
- 624 Energy Use & Conservation
- 618 Discussion Forums/Café
- 311 In the Weeds--Member's Choice
- 75 Construction
- 124 New Battery Technologies
- 108 Old Battery Tech Discussions
- 3.8K Solar News - Automatic Feed
- 3.8K Solar Energy News RSS Feed