Impact testing for obtaining natural frequency
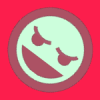
SH Yang
Registered Users Posts: 9 ✭
Hello,
I am planning to conduct impact testing wth a hammer to gain natural frequecy on a spare blade and then compare the FFT data from the wind turbine.
I am just wondering that if natural frequency is obtained, could I judge which vibration is normal or not after comparing the FFT data from the spare blade with the FFT data from the wind turbine??
If so, would u please let me know how to compare that??
I am planning to conduct impact testing wth a hammer to gain natural frequecy on a spare blade and then compare the FFT data from the wind turbine.
I am just wondering that if natural frequency is obtained, could I judge which vibration is normal or not after comparing the FFT data from the spare blade with the FFT data from the wind turbine??
If so, would u please let me know how to compare that??
Comments
-
Re: Impact testing for obtaining natural frequency
How I would approach it...
The frequencies that you find resonating in the blade(s) would be ones that I would not want the turbine to produce (and harmonics there of). Gear box design, hub, even shaft designs should avoid blade harmonics.
Basically, if the turbine outputs 100 Hz, and the blade resonated at 130 Hz--In theory, there is no issue.
If the blade resonated at 100 Hz and the turbine produce a 100 Hz frequency--Then you have a chance of the blade "amplifying" the input frequency and either failing immediately or over time (fatigue).
So, you have the option of redesigning the blade/mounting (I would suggest that you test the blade response when mounted to the hub/shaft--A piece of metal will have a difference response if one end is fixed vs just hanging from some light weight supports/cables--even where the cables are connected can affect response). If this is a variable pitch type blade/hub--I would test several pitch settings to see if the spectral response changes, etc.).
Or you can work at reducing input energy that "match" various resonances.
If this is a fixed speed turbine (synchronous alternator), you could change the gearing/shaft/hub design a bit to operate the blades at a different speed/avoid problem resonances.
If this is a "wild frequency" turbine (rectified output or wild AC to Fixed AC via an inverter), you could program the control software to avoid certain operating speeds.
Obviously, you can also modify the blade design (shorten/lengthen/adjust width/material/heat treatment/etc.). There are also various "stabs" or winglets that can be added to adjust aerodynamics--these could be adjusted for position/weight to move resonances to different frequencies/break up major resonance points. But this may not be possible at this point in the design/purchasing process.
-BillNear San Francisco California: 3.5kWatt Grid Tied Solar power system+small backup genset
Categories
- All Categories
- 229 Forum & Website
- 137 Solar Forum News and Announcements
- 1.4K Solar News, Reviews, & Product Announcements
- 199 Solar Information links & sources, event announcements
- 898 Solar Product Reviews & Opinions
- 256 Solar Skeptics, Hype, & Scams Corner
- 22.5K Solar Electric Power, Wind Power & Balance of System
- 3.5K General Solar Power Topics
- 6.7K Solar Beginners Corner
- 1K PV Installers Forum - NEC, Wiring, Installation
- 2.1K Advanced Solar Electric Technical Forum
- 5.6K Off Grid Solar & Battery Systems
- 428 Caravan, Recreational Vehicle, and Marine Power Systems
- 1.1K Grid Tie and Grid Interactive Systems
- 654 Solar Water Pumping
- 816 Wind Power Generation
- 624 Energy Use & Conservation
- 619 Discussion Forums/Café
- 312 In the Weeds--Member's Choice
- 75 Construction
- 124 New Battery Technologies
- 108 Old Battery Tech Discussions
- 3.8K Solar News - Automatic Feed
- 3.8K Solar Energy News RSS Feed