24vdc alternator to sine wave inverter
Options
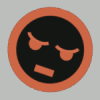
cptdondo
Solar Expert Posts: 105 ✭✭✭
I'm doing some thought experiments along the following lines:
Install a 140A, 24VDC alternator on a car engine (secondary to the engine alternator)
Run the output of the alternator to a 2500-3000W sine wave inverter
Use that to run various appliances - microwave, air conditioning, etc
There are no batteries between the alternator and the inverter.
Any thoughts on this? Is it feasible? Any potential for damage to the inverter?
The idea is to replace a 2.8kW 120VAC generator. I'm looking at 24VDC to reduce the size of the wiring; otherwise I could use 12VDC.
Install a 140A, 24VDC alternator on a car engine (secondary to the engine alternator)
Run the output of the alternator to a 2500-3000W sine wave inverter
Use that to run various appliances - microwave, air conditioning, etc
There are no batteries between the alternator and the inverter.
Any thoughts on this? Is it feasible? Any potential for damage to the inverter?
The idea is to replace a 2.8kW 120VAC generator. I'm looking at 24VDC to reduce the size of the wiring; otherwise I could use 12VDC.
Comments
-
Re: 24vdc alternator to sine wave inverter
The first fly in the ointment is: where will that alternator get the power to excite the armature windings from? Normally that comes from a battery, through a regulator.
Which brings up the next little problem; how to regulate the output of the alternator so that it maintains proper Voltage range for the inverter against varying current demands. Normally the battery fulfills this role as well: the great leveler between power production and power demand.
In essence what you're trying to do is create an inverter-generator. You can buy those already made, usually for less money than the main component parts required to build your own. -
Re: 24vdc alternator to sine wave inverterI'm doing some thought experiments along the following lines:
Install a 140A, 24VDC alternator on a car engine (secondary to the engine alternator)
Run the output of the alternator to a 2500-3000W sine wave inverter
Use that to run various appliances - microwave, air conditioning, etc
There are no batteries between the alternator and the inverter.
Any thoughts on this? Is it feasible? Any potential for damage to the inverter?
The idea is to replace a 2.8kW 120VAC generator. I'm looking at 24VDC to reduce the size of the wiring; otherwise I could use 12VDC.
Many years ago I bought a "conversion kit" for my car alternator which included a switch that both disconnected the alternator from the battery and the rest of the car electrical system and replaced the voltage regulator with one in the kit box. When you revved the engine to a high enough speed, you got 120V DC from the kit to run tools, etc. with "universal" (AC/DC) motors. It worked right up to the point where it fried the alternator diodes one day.
So most alternators can work (although not very well) without a battery attached. There will be some residual magnetism to start the alternator producing current or it will use a permanent magnet.
The regulation will certainly not be as good and I would worry about damaging the inverter too.
The regulated field current system, requiring a battery, was commonly used in auto generators which produced DC directly, back before alternators were invented.SMA SB 3000, old BP panels. -
Re: 24vdc alternator to sine wave inverter
Nit-pick: generators also produce AC, not DC. It is rectified to DC by the relation of the commutator and brushes: the positive brush always aligned with a section of armature coil that is positive and the negative brush always to negative. Since they are a series of connection points this amounts to switching on/off in relation to the coil energizing. It also means they are sometimes connected across two and tend to arc and spark and grab the full Voltage output for only part of the waveform. In other words they're inefficient and wear more compared to a modern alternator design with its constant-contact slip rings and solid-state rectifiers. -
Re: 24vdc alternator to sine wave inverterCariboocoot wrote: »Nit-pick: generators also produce AC, not DC. It is rectified to DC by the relation of the commutator and brushes: the positive brush always aligned with a section of armature coil that is positive and the negative brush always to negative. Since they are a series of connection points this amounts to switching on/off in relation to the coil energizing. It also means they are sometimes connected across two and tend to arc and spark and grab the full Voltage output for only part of the waveform. In other words they're inefficient and wear more compared to a modern alternator design with its constant-contact slip rings and solid-state rectifiers.
By the same nit, alternators either produce AC or, because the bridge rectifier pack is internal, they produce DC at their output terminals.
Just so the overall operation is understood, either labeling standard works. It is when people start mixing the two that problems develop.SMA SB 3000, old BP panels.
Categories
- All Categories
- 227 Forum & Website
- 135 Solar Forum News and Announcements
- 1.3K Solar News, Reviews, & Product Announcements
- 198 Solar Information links & sources, event announcements
- 895 Solar Product Reviews & Opinions
- 255 Solar Skeptics, Hype, & Scams Corner
- 22.4K Solar Electric Power, Wind Power & Balance of System
- 3.5K General Solar Power Topics
- 6.7K Solar Beginners Corner
- 1K PV Installers Forum - NEC, Wiring, Installation
- 2.1K Advanced Solar Electric Technical Forum
- 5.5K Off Grid Solar & Battery Systems
- 428 Caravan, Recreational Vehicle, and Marine Power Systems
- 1.1K Grid Tie and Grid Interactive Systems
- 652 Solar Water Pumping
- 815 Wind Power Generation
- 624 Energy Use & Conservation
- 617 Discussion Forums/Café
- 310 In the Weeds--Member's Choice
- 75 Construction
- 124 New Battery Technologies
- 108 Old Battery Tech Discussions
- 3.8K Solar News - Automatic Feed
- 3.8K Solar Energy News RSS Feed